The world’s top watch manufactures are a secretive bunch. They will say nothing – absolutely nothing – that might identify even one of their clients. That’s as it should be, I suppose.
Still, I wanted to understand how a top-end Swiss company restores a badly damaged watch to its original condition. I’m not talking about a cracked crystal or a scratched lug. I’m talking catastrophic damage that bends metal and subjects the piece to physical forces never imagined by those who created it.
So I compiled my questions and contacted five of the planet’s greatest watch manufacturers.
“Talk to me,” I pleaded. “Tell me what happened. Show me how you restored a treasured watch whose owner thought it was a total loss and would never run again.”
“No,” four said.
“No?”
“This is confidential,” each said. Or something equivalent.
“I’m not interested in who the client was,” I tried reasoning. “Just the story behind such catastrophic accidents and the resulting restoration.”
“No.”
I threw my hail Mary, “The underlying message will be: if your service department can restore such a catastrophe, imagine what you can do with a consumer’s watch.”
You guessed it. “No.”
One manufacturer had the audacity to claim that its pieces are so valuable and well cared for that it has never had anything close to a catastrophic accident requiring such extensive repair as I described.
We’re all human. Accidents happen.
In the course of my research, I discovered one owner of a six-figure watch who liked to wear it while gardening. Gardening. The inevitable happened, placing the piece in that manufacturer’s watch “emergency room.”
Still, the four wouldn’t speak with me.
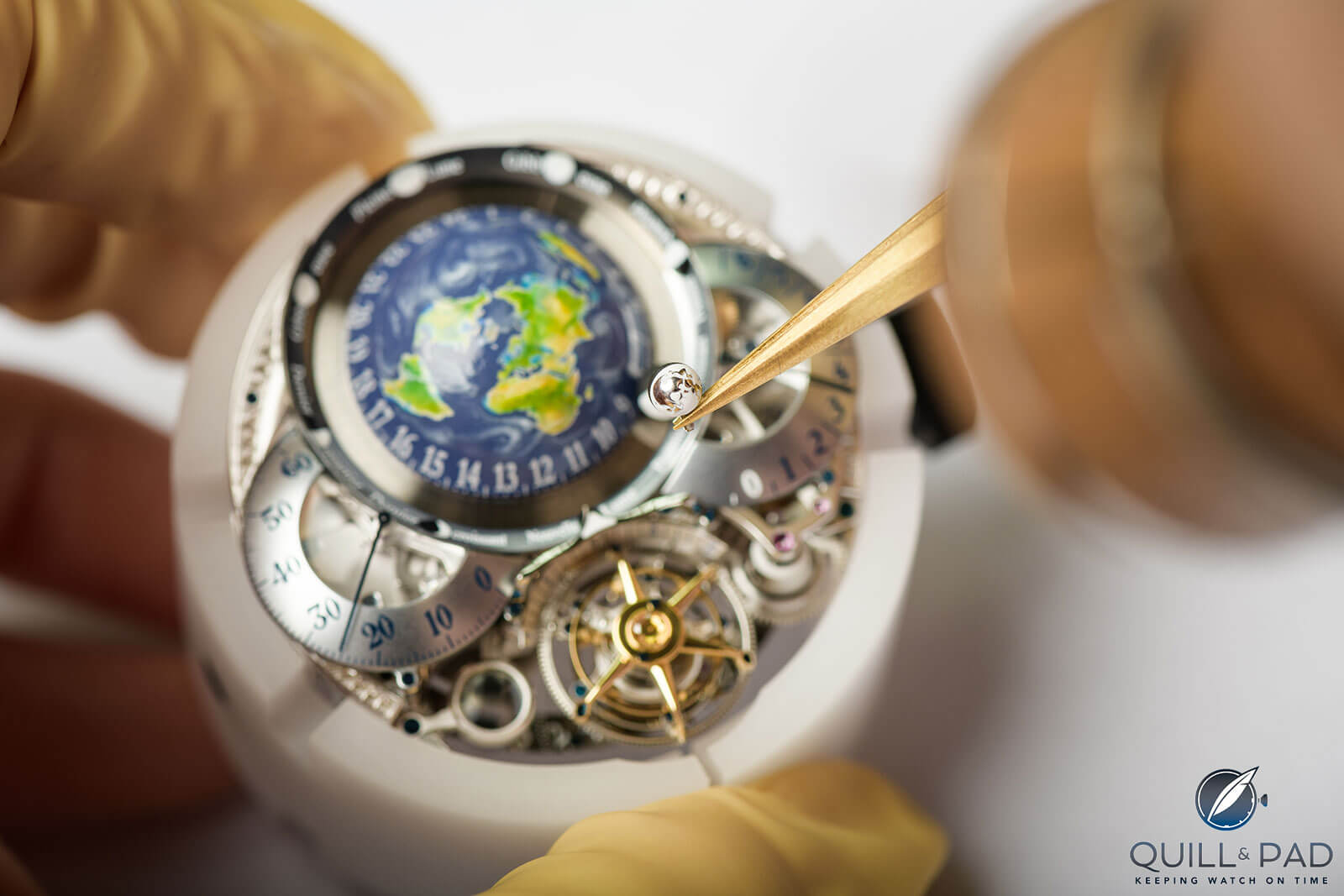
A Bovet watchmaker carefully assembling a Récital 22 Grand Récital
But one manufacture did: Bovet. Indeed, my request traveled up the chain of command to Pascal Raffy himself, president, CEO, and sole owner.
I found Raffy to be charming, forthright, and intensely proud of the company he has rebuilt. Yet, he too was a wall of stone so far as giving away anything that could possibly identify his clients. No problem. I don’t care.
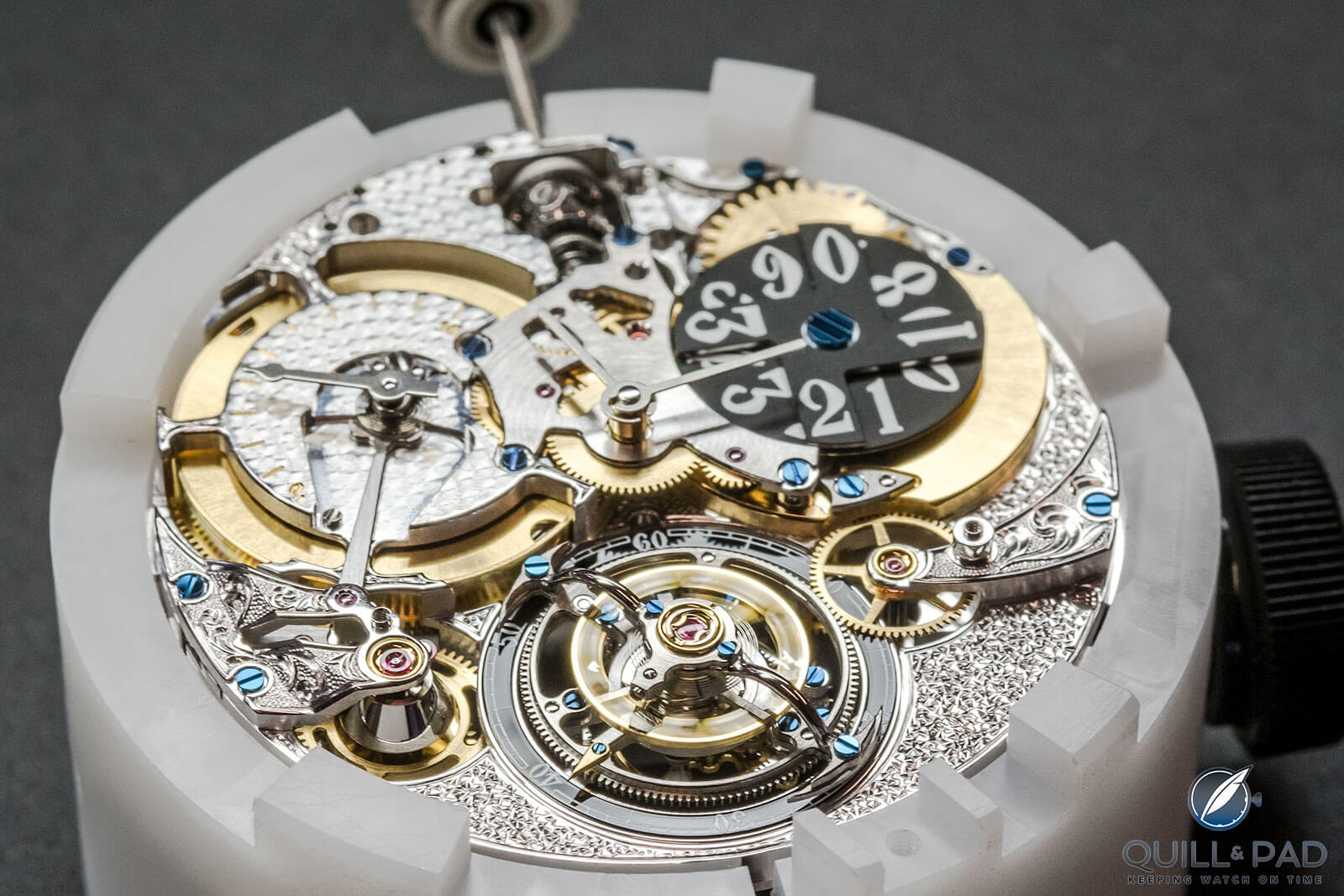
Assembling the Bovet Virtuoso VIII movement
More than just saving a treasured watch
Raffy’s story revealed more insight into the company than I expected. Within the context of a single catastrophic accident that befell one of Bovet’s more valuable pieces we spoke of old-world craftsmanship and how preserving client relationships takes precedence over everything – especially something so secondary in importance as payment for repair services rendered.
Therein lay the larger lesson Raffy wanted to convey about his company. He schooled me on what it took to rebuild the maison de Bovet’s reputation once he acquired the company in 2001.
The devastating accident and the restoration he used as an example is probably just one of many that have occurred over Bovet’s 197-year history. But the underlying lesson in what it takes to service and maintain Bovet’s reputation is enduring.
Bovet’s approach to service
The company routinely deals with two types of repairs: good-faith repairs and misuse of the timepiece, unintentional or otherwise. Good-faith repairs occur during the normal course of use. Bovet is well equipped to deal with these, having 25 watchmakers and 102 artists at the ready.
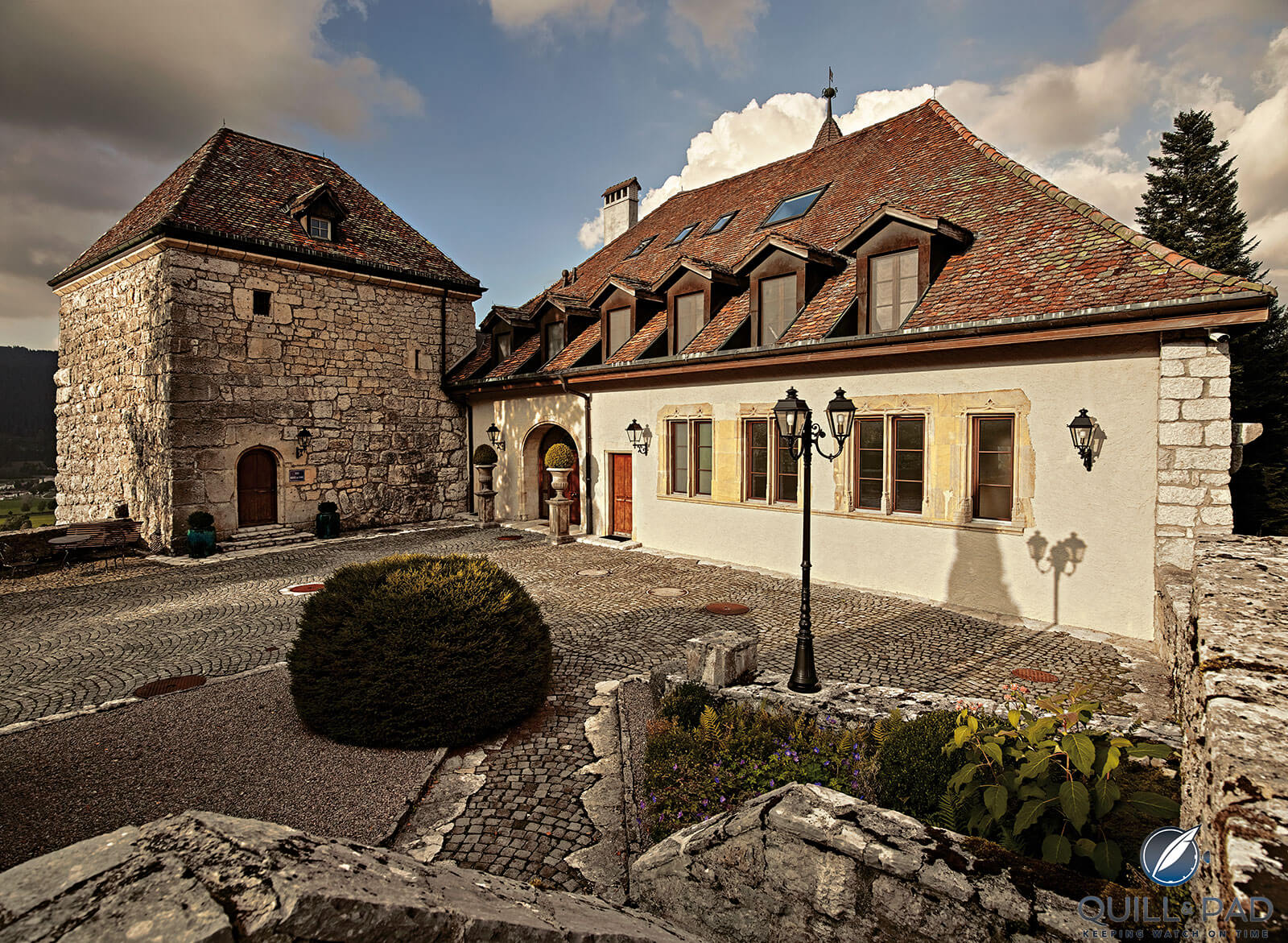
Bovet HQ at the Château de Môtiers, Switzerland
Just five years after acquiring Bovet, Raffy added what is now known as Bovet 1822 Manufacture de Cadrans et Sertissage and Dimier 1738 Manufacture de Haute Horlogerie in addition to the Château de Môtiers.
These acquisitions completed the plan for vertical integration of most of the company’s manufacturing processes and guaranteed independence from most outside providers. Along with this strategy came total quality control.
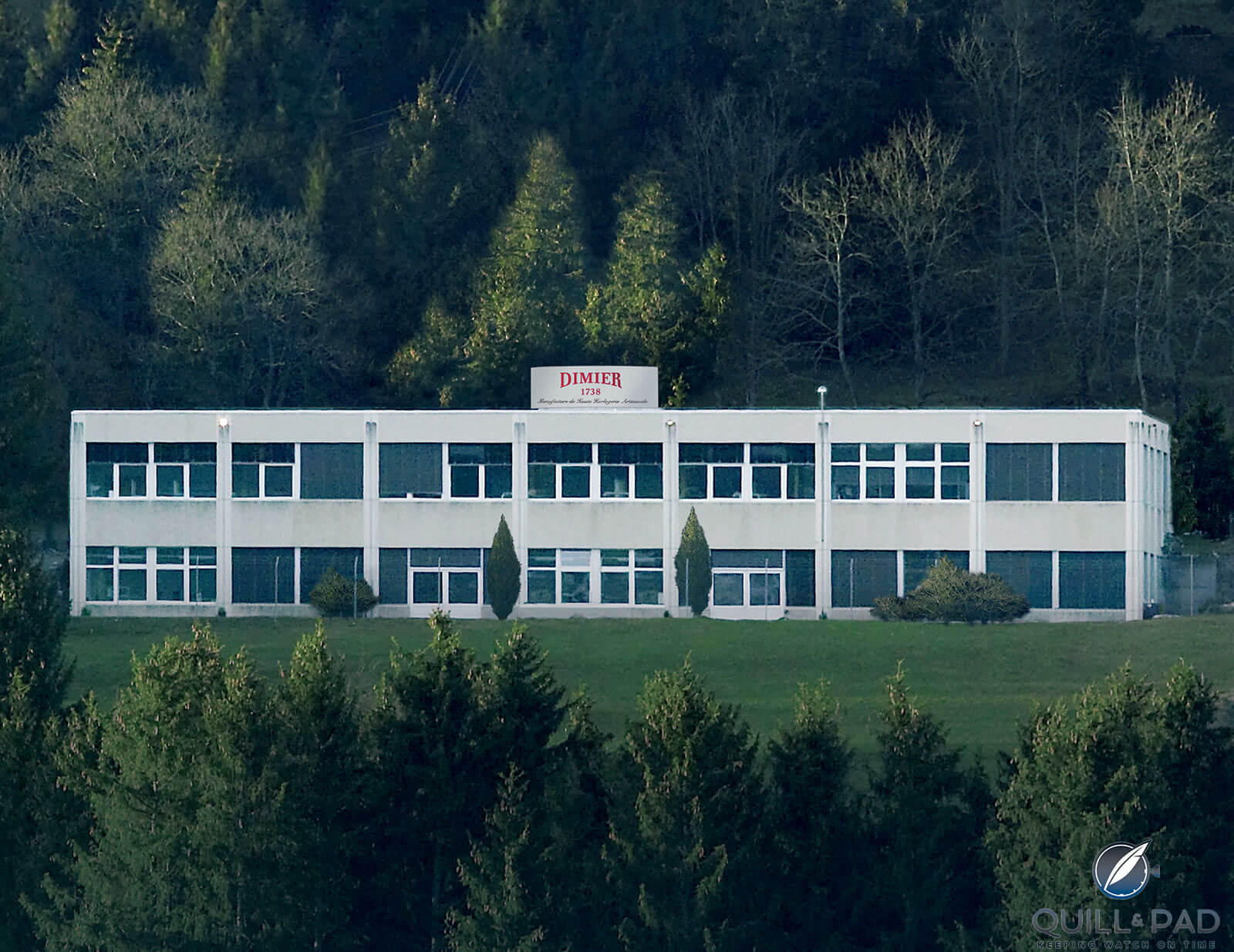
Bovet’s Dimier 1738 Manufacture de Haute Horlogerie in Tramelan, Switzerland
Raffy’s insistence on vertical integration is the reason most repairs usually occur very quickly and in a cost-effective manner (unlike some of the other manufacturers).
Those are the good-faith repairs. Then there are the others – repairs necessitated by unforeseen misuse of the timepiece. Raffy identified such things as immersing a watch in deep water when it was never intended for such use.
Another cause sited was blunt force trauma to the watch far beyond any shock the timepiece was designed to withstand. Both occurred in the example we discussed.
According to Raffy, such extensive repairs have happened. They are rare, and so the company treats them as one-off incidents.
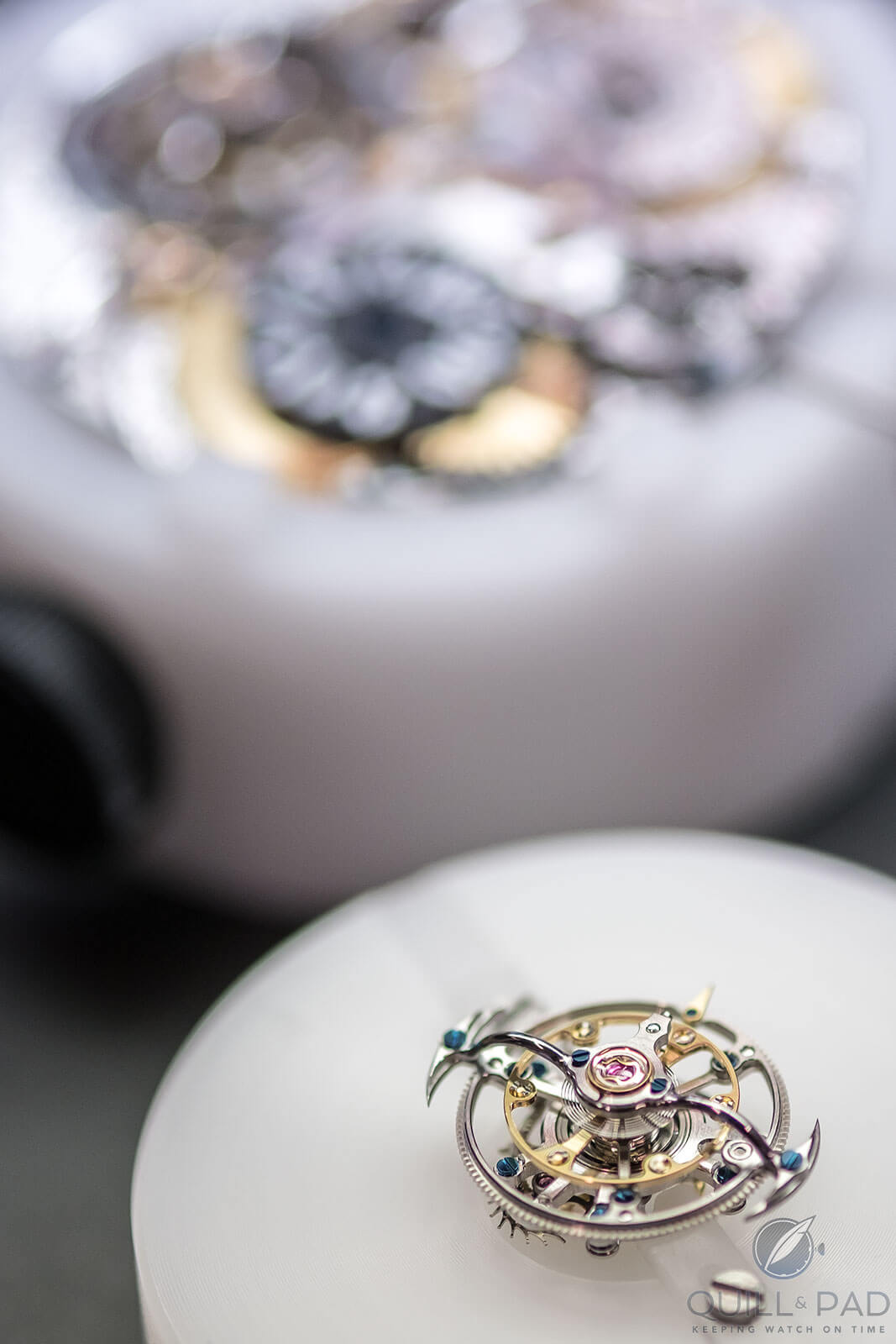
Bovet tourbillon assembly
Here’s when the unthinkable happened with Bovet
Bovet counts many loyal collectors as frequent clients. These individuals are unlikely to misuse one of their treasured watches.
Yet one day the unthinkable happened: a Bovet collector suddenly found himself shoved into a swimming pool while wearing his treasured watch. That wouldn’t have been so bad. However, in falling the watch somehow crashed against the pool’s hard coping.
This blunt-force trauma not only broke the crystal, it smashed and bent the case, completely compromising its designed water-resistant integrity. The watch flooded.
The owner was rightly upset. This watch was a treasured piece in his collection. Though Raffy didn’t comment on any particular customization for the crushed timepiece, I would speculate it was likely significant. If for no other reason than that, simply replacing the watch with another production model was not a consideration. The owner wanted that particular watch restored.
Raffy became involved, as I imagine he frequently does with as many clients of the company as possible. His mission was to save and restore all possible movement components. Bovet maintains an inventory of spare components for at least six complete watches of all models going back 10-15 years.
For movements, the inventory includes ten years of all components. The same with dials.
That is why there would never be a point where the cost of repairing the damage exceeds the value of the watch, causing them to declare it a total loss. The only component that cannot be repaired is a badly bent, crushed, and smashed case. Then the technicians will replace it with a new one from inventory.
So Bovet had the replacement parts on hand even for this catastrophic repair.
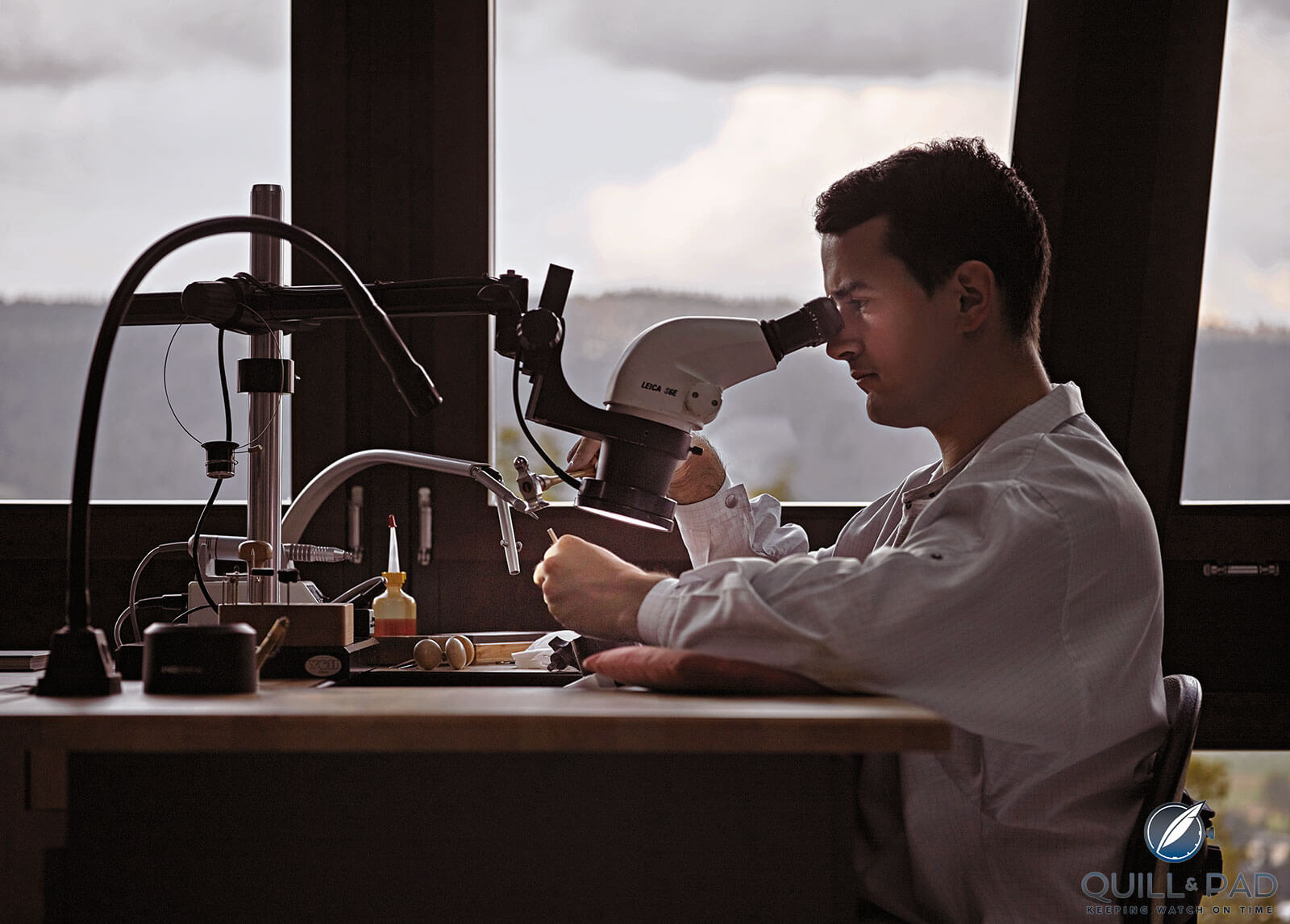
A Bovet engraver at work in the brand’s atelier at the Château de Môtiers, Switzerland
The repair process
For most manufacturers there’s a definite process to restore watches involved in catastrophic accidents. They usually involve assessment of the project, cost estimates, time estimates, assembling the artisans with the requisite specialties required, scheduling the work, actually doing the repair, and testing the result.
As Raffy related to me, Bovet’s process is a little more genteel. Raffy himself wanted to speak with the collector.
What happened?
How did it happen?
How was the timepiece normally used?
There was a shock to the watch – that much was obvious – but what kind of a shock?
Raffy wanted the whole picture. I think as much to discover what lessons Bovet might learn from this accident.
Then Bovet took the piece into the shop. “The facility is 18 years old,” Raffy says. “It houses 25 watchmakers and 102 artists. All are extraordinarily competent.”
Given the discipline and demanding precision of the owner, I wouldn’t doubt that statement. “There is both the spirit as well as the essence of quality among the team. All watchmakers are there to service the collectors/owners.”
Now that the professionals are involved, the first task is to assess and give their opinion of the damage.
In this case it was, well, extensive.
Like most businesses, along with the work assessment comes an estimate of the cost. If it was a fault on Bovet’s part, there would be no charge. Not the case here.
Yet, cost of this extensive repair is not an issue.
However, what is important at this point is time is that the owner wants his treasured piece back in his collection, and Raffy wants to give it to him. So a time/cost estimate is provided.
In this case, owing to the extensive damage, it will take about six months to restore the piece to its original condition using as many original components as possible.
From Raffy, I understood this to be a long time for a Bovet piece to be on life support inside the repair shop. “Due to our vertical integration and our inventory of original parts, most repairs are surprisingly fast.”
So the team set to work. Task one was to restore the movement. Then the power reserve. About 70 percent of the original parts were salvaged and restored. Those that could not be reused were replaced with new parts from inventory.
Not what the owner preferred, but there’s only so much even Bovet’s watchmakers can do.
Unfortunately, the smashed case was irretrievable. The team plucked a case from inventory. Though Raffy wouldn’t say, my guess is that if there were any special engraving or inscriptions on the original case, it was faithfully recreated on the replacement.
Next, the technicians assembled the entire piece, conducted quality control tests, made any necessary adjustments, and tested again. Then they released the recovered timepiece back to the owner. I imagine it was in at least as good condition as it was before that fateful day. Probably better.
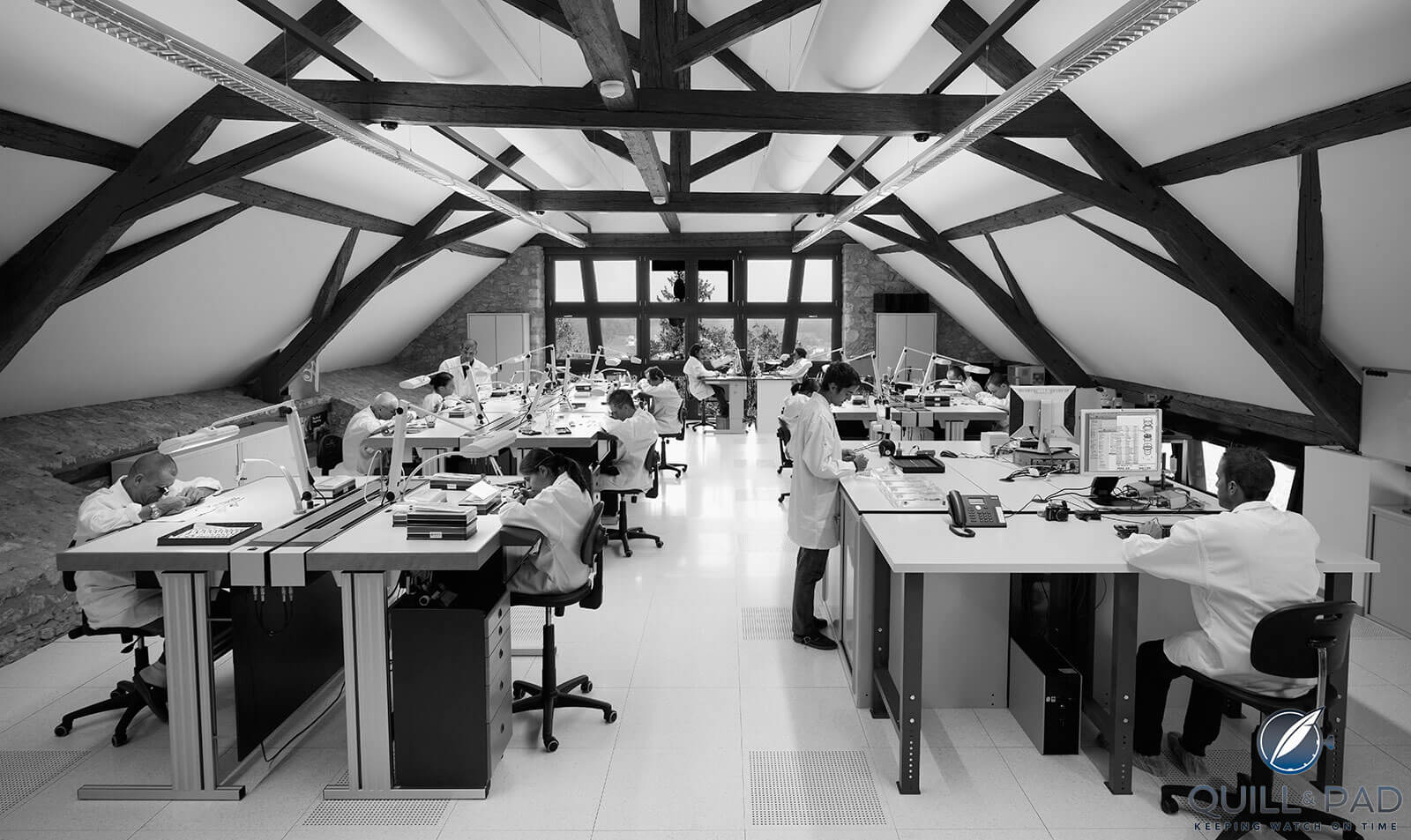
Bovet’s watchmaker and engraver workshop at the Château de Môtiers, Switzerland
What was the cost?
“Cost estimates” are where Bovet’s art meets its business imperatives. Unlike other manufacturers, the cost of such a catastrophic repair doesn’t use a bill of materials and price list. Instead, it depends on several factors:
Who caused the issue?
What was the challenge to Bovet and what did the technicians learn from the incident that they can use to make their watches that much better?
What is the house’s relationship with this particular client?
Bovet wants to retain client relationships, that is clear from speaking with the brand’s owner. For this repair, cost was never an issue. Instead, it was how can Bovet help restore the piece to someone whose goodwill and relationship the brand values and wishes to keep?
For Raffy, it was the joy and happiness of returning an important part of a friend’s collection. At the end of the day, there was no cost to the owner.
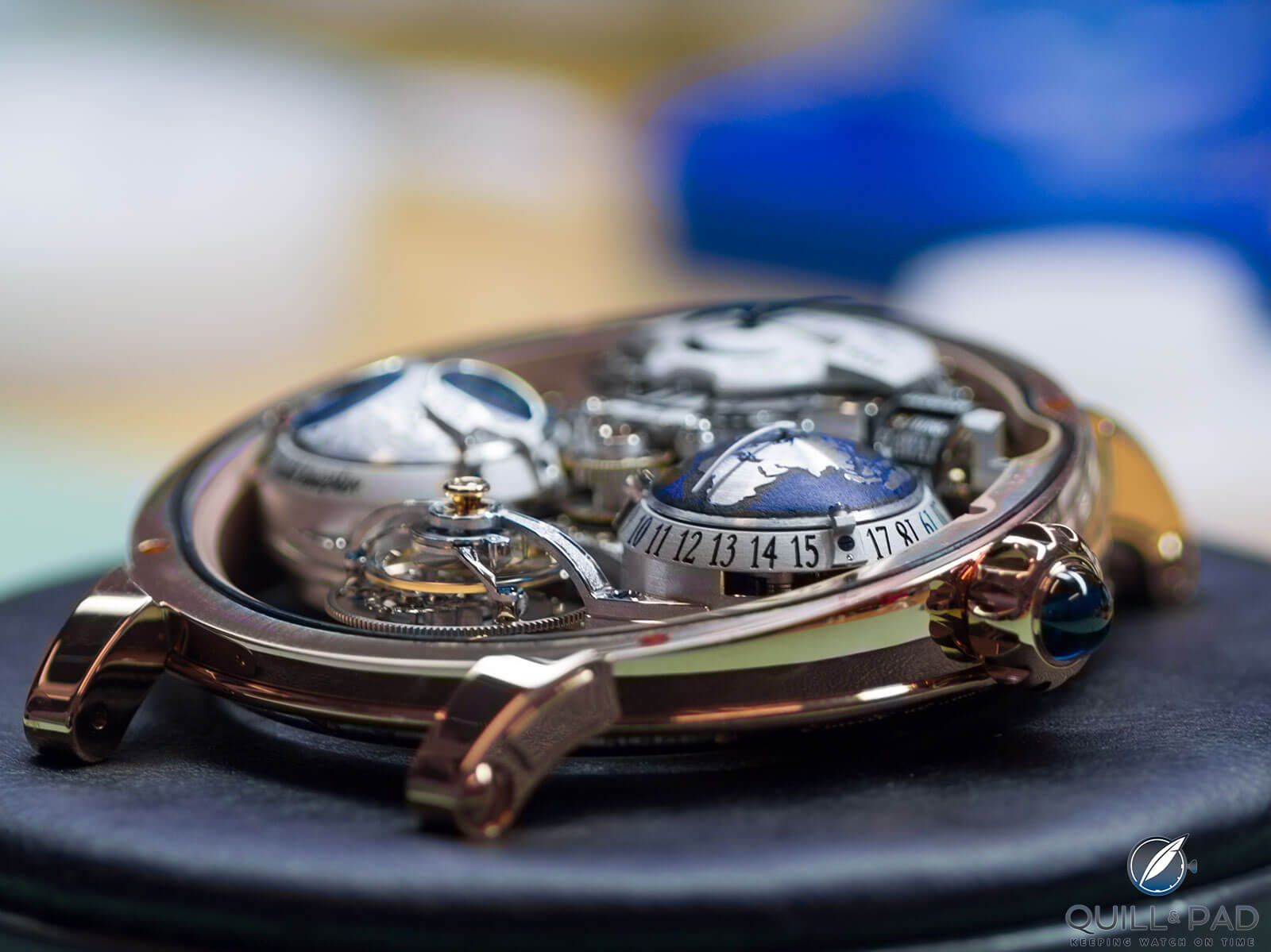
Bovet Récital 22 Grand Récital being assembled
Relationship building
Bovet’s philosophy places service over everything else, continually searching for ways to strengthen the loyalty of its clients. The brand seems more relationship-based rather than strictly financially oriented.
After having spoken with Pascal Raffy I can see some of the reason for his success. People want to do business with Bovet because of the personal relationships the company fosters with its clients.
Watchmaking at Bovet is not just mechanical engineering. Some of the pieces are often so customized they may as well be bespoke. The resulting client relationships are based on emotion and service.
According to Raffy, “This is what makes a house. Our collectors are like an extended family. They never forget courtesy and what you did for them.”
Quick Facts Bovet Récital 22 Grand Récital
Case: 46.3 x 19.6 mm, red gold or platinum
Functions: hours (24), retrograde minutes, seconds (on tourbillon); precision moon phase, date, power reserve indication, perpetual calendar (on back) with hour, day, month, and leap year
Movement: manually wound Bovet Caliber 17DM03-TEL with one-minute flying tourbillon, variable inertia balance, nine-day power reserve
Limitation: 60 pieces across all variations, including customized pieces
Price: $469,800 (red gold), $502,200 (platinum)
Remark: five-year warranty
For more information, please visit www.bovet.com.
Chris Malburg is the author of many books, including his “Enforcement Division” series, which you can learn more about at www.enforcementdivision.com.
You may also enjoy:
Bovet Récital 26 Brainstorm Chapter One: Design Intent Uncompromised
Watch Customization: The Top Of The Pyramid
The Astronomical Grandeur Of The Bovet Récital 22 Grand Récital
Leave a Reply
Want to join the discussion?Feel free to contribute!
Now that sounds like service – sadly of the sort that us mere mortals will never receive from run-of-the-mill watchmakers. When my boat comes in, Bovet will be high on my list of to-buys.
Reliving the pool incident made me cringe inwardly. But all’s well that ends well. When my ship comes in…well, my ship will probably be more like a canoe, but if anyone ever asks my opinion on which timepiece they should invest in, Bovet must spring to mind. Unless they want to be inconspicuous.