Do you remember high school, sitting in art class, being instructed on how to make your mother an ashtray out of clay (those were different times) and realizing that you were completely hopeless when it came to ceramics? I sure do, and my lumpy, heart-ish shaped ashtray finally found its way into the garbage years later when we were going through old boxes. Shudder . . .
Luckily, those ceramics are not the topic of today’s discussion, but rather advanced ceramics and how they are used. There have been a lot of talk and promises made by the watch industry about ceramics and their use in timepieces, so it would seem that a primer in ceramics might make us much more informed consumers.
My goal here is to give you a basic understanding of what ceramics are, why they are used for certain aspects of watchmaking, and why they may never be used for others. I’ll also touch on some fabrication techniques as it may relate to our favorite subject, horology.
And, of course, this will be a rather nerdy (and wordy) discussion, so get ready to discover some awesome knowledge!
Wide world of ceramics
Ceramics is a bit of a dual subject as most people, rightly so, think of pottery and porcelain when they hear the word ceramics. Having a “ceramics course” in high school or college doesn’t help that, either.
But there is an entire world of ceramics beyond clay and a potter’s wheel, and that world is referred to as advanced ceramics. This covers almost every ceramic discovery beyond the “traditional” ceramics that have been in use for hundreds or thousands of years such as the clay material called kaolinite.
But this might be putting the cart before the horse, so the real issue is what constitutes a ceramic material in the first place? Well, I’m glad you asked, dear fictional follower of my fantastical fables!
Ceramics are inorganic, non-metallic materials made from compounds comprising a metal and a non-metal. They also can be crystalline or partly crystalline. Already that makes it a little confusing.
Basically, a ceramic is a compound material that cannot be defined as a metal even though it has some metal components in it. The rest of the mixture comprises complimentary non-metallic materials that, when combined, form a distinct class of materials with properties different from others.
A ceramic tends to be strong and stiff, rigid really. And with this rigidity comes brittleness. This is a very different story than metals. Imagine, if you will, that you have a bunch of rubber bands all tied together into a ball. The ball feels firm but can bounce because the rubber deforms.
This is somewhat analogous to a metal, though greatly exaggerated. The type of bonds in metals allow for movement of the atoms under stress, which is why metals can be hammered and shaped.
A different story
Not so with ceramics. Ceramics are like a block made of rigid, interlocked sticks (very figuratively). This is a much sturdier structure that doesn’t deform when force is applied. But because ceramics do not deform, they will continue to withstand greater and greater forces until those forces out measure the strength of the interlocking sticks . . . and then the entire structure fails catastrophically. In other terms, it shatters, just like ceramics.
The bonds (and in the larger sense, the crystals) of ceramics are locked in position very strongly, thanks to a combination of ionic and covalent bonds (seriously, just know they are pretty strong and stable) and the shape and distribution of the crystals. These strong bonds have very little ability to shift under force, so huge amounts of pressure can be applied and the material will hold strong.
However, this only holds true in compression. Under shearing, tension, or high-speed shock the bonds fail at much lower forces (and the ceramic shatters).
This is due to the fact that the inherent strength of the bonds and the formation of the crystals create a direction to the material on a micro level. The grain (as the micro-crystals are referred to) has a shape resembling overlapping stones in a stone wall. The grain is stacked and packed tightly together with somewhat random orientation.
Depending on grain size, the stacks will, at a very small level, have grain boundaries that happen to line up with each other creating a continuous grain boundary where an aggregate slip could occur.
This requires a lot of force, but when the positions are disturbed, they move away from the complimentary grain boundary and cannot find a new position (random grain size and orientation) which causes the material to continue this slippage outward and shattering begins.
Why that matters
The reason this is a critical function of ceramics is that it creates a very specific set of strengths. The force required to cause a slippage of a grain boundary is fairly high, so in most cases, the material will resist “intrusion” from whatever is imposing force on it.
This means that ceramics are very hard to break, mark, or change in any way.
When you want an object to withstand a high amount of forces without showing signs of the force, ceramics are your best bet. The bonds create a super-strong material that can maintain its shape very well. But the shearing forces that occur when high force is concentrated on a small area create a slippage in the grain boundary and the material fails.
This is why you can hit a rock with a sledge hammer and only have it crush the very smallest amount of material on the surface, while hitting it with a pointed pick can cause the entire rock to shatter or crack completely through as a slippage moves through the material.
With advanced ceramics, the size, shape, and general distribution of grain can be controlled to a certain extent, creating different types of ceramics with enhanced properties in different ways. Some are made to allow a small amount of plastic deformation (bending and moving like metal can), while some are created to withstand enormous compression force when there is little risk of impact or shearing.
This all has to have an application, right? Sure! Watch cases, bezels, and other external components are designed with ceramics that can handle bumps and dings without problem, creating virtually scratch-proof components. These components are actually pretty sizable, though, compared to internal components. They have enough mass and grain variation that they will be able to withstand a lot of abuse.
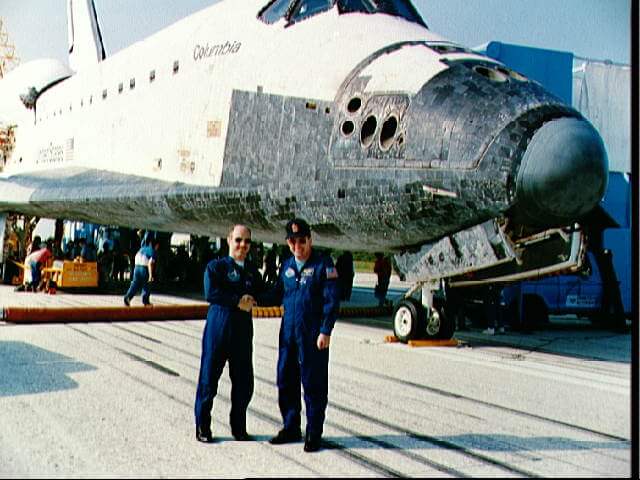
The nose and underbelly of space shuttles have ceramic tiles to insulate from the blast-furnace heat of re-entry
The shoe on the other foot
The larger the ceramic part, the more robust it is. This is not anything miraculous, really; almost every material gets stronger as it gets bigger. But there is a certain threshold for size going smaller, where the number of grains is so few that the entire structure is made of proportionately large grain boundaries.
And we all know what happens when a shearing force is applied along a grain boundary, right? You guessed it: catastrophic failure, shattering, and disintegration.
This is not exactly the case with other materials. With a ceramic, if the method of construction can create a minuscule shape, the strength of the bonds can help hold that shape permanently, while in many other materials there is a threshold under which shapes simply are not self-supporting.
But that also hinders ceramic in other ways. Those other materials, if they can be formed, will usually not completely shatter under force, instead bending out of the way or simply momentarily deforming and then returning to shape.
This is the benefit and a disadvantage of ceramic materials. Once a ceramic receives too much force and deformation occurs, it is usually permanent.
This is why when a jewel in a movement breaks, it shatters and sends bits of material all over the movement, but when a staff or wheel tooth “breaks” they tend to simply bend or squish under the force.
If separation occurs, it usually is a single piece of material and not a total structural failure. This is why ceramic materials have less use inside a movement: they are much more sensitive to shocks unless they are fully supported.
Bridges and plates could be made from ceramic since they are larger and not moving components, but wheels, staffs, pinions, and other small things are better left to different materials.
In the real world
The applications that ceramic technology are used for and why actually constitutes an interesting part of it. Heat shielding, bulletproof materials, wear-resistant surfaces, precision gauge materials, and electrical insulators make up a large variety of the ceramic market.
There are even specific ceramics that, at very certain extremely low temperatures, switch from being insulators to superconductors. These engineering ceramics are tapped in thousands of ways, and the ways in which they are fabricated vary as well.
Since ceramics are very strong and resistant to deformation and abrasion, normal manufacturing techniques are not adequate. The main ways that ceramics are made is either with molding and machining followed by heat-treating (sintering) to the appropriate density (which results in shrink, more on that in a bit) or with grinding and abrasion.
Now I know that I said ceramics were resistant to abrasion, and they are, but (like all materials, really) only to things that aren’t as hard as they are. Granted, this is still almost everything. But there are still some things on the very, very hard end of the scale that can be used to damage ceramics, like diamond. Actually, diamond tooling and diamond abrasives are used in many instances of ceramic formation simply because the material needs something much harder to be worn away in any meaningful manner.
In an example of a multi-step ceramic production process, which happens to be the same way that most watch cases and bezels are made, a rough shape is born by creating a slurry of ceramic and then drying it. The dry powder is then molded into a rough shape called a green body, meaning that it is unsintered. This shape is fairly close to what the final part will look like, only larger.
Secondary features not able to be molded are then usually machined into the green body using (you guessed it again) diamond tooling. The part is then sintered (with heat and/or pressure) to compact the ceramic material into its final shape and density.
During the sintering process there are three stages of shrinkage with the highest amount of shrink coming in the middle of the process.
The amount of shrink is different for each specific material, and this must be carefully factored in during the molding and machining stage. If done correctly, the pre-sintered part can shrink to a desired size that is then accurate within microns.
A rather difficult process
The next main fabrication technique is taking a fully sintered material and grinding, lapping, and polishing it to a final shape. Those processes utilize diamond abrasives to shape the either the green body or fully hardened ceramic. This is usually done when the shape is less complicated or when working with a carefully pre-made piece of specialized ceramic from a supplier.
Some companies will not produce their own ceramic but instead work with stock produced for them. Granted, this material can usually come close to net shape if the part is made from a molded and machined green body process.
Sapphire crystal, which is an aluminum oxide material and therefore a ceramic, is usually shaped from the fully hard condition by means of grinding and lapping with diamond tooling and abrasives. Some of the more complicated three-dimensional crystals are slowly machined with diamond-coated tools under great care to produce some very complicated and hard shapes.
The diamond tooling used to create these green body parts can also be ceramic themselves, as tungsten carbide milling tools can be coated with diamond for a very strong, rigid, and capable cutting edge. As the ability to create more dynamic and advanced ceramics continues, the tooling to work with them must also advance, usually into the same territory.
As you can see, the world of ceramics is big, hard, and complicated. The very tiny amount that I touched on here is only a fraction of the information out there describing the material, how it is manufactured and fabricated, and what exactly different kinds can do.
The properties of ceramics shine when it comes to strength and durability, which places them among the best materials for watch cases, bezels, crystals, and exterior components. The material falls flat if you need strong and tiny shapes due to the brittleness of ceramic and its propensity to shatter if not fully supported.
The bottom line is ceramics are awesome. Usually. They have their drawbacks, but then again, so does every other material. Knowing why things are made with ceramics, and how the process of fabrication works (including how difficult it can be) can help you understand why price increases for ceramic parts is not without reason, and in many cases makes a much better timepiece.
But hopefully you can also see through some hype and understand how appropriate material choices are made.
I encourage you to read more on this vast subject if you are interested. It might be one of the least understood manufacturing subjects, and it really shouldn’t be. Ceramics have been with us as a species for millennia, and I hope this article made you want to reconnect with ceramic technology.
Oh, and be careful with the ceramic mug your coffee is in right now. If you drop that sucker, all the kings horses and all the kings men couldn’t put that thing back together again without at least a little superglue!
Trackbacks & Pingbacks
-
[…] Check out more on Quill & Pad […]
-
[…] on a watch site. Well, the engineer in me is not done this weekend, so I wanted to point out Quill & Pad’s article on the rise and use of ceramics in our lives, and specifically in ou…. They do a good job of explaining the benefits and limitations of the material, so you can decide […]
Leave a Reply
Want to join the discussion?Feel free to contribute!
I was hoping for a discussion on how a ceramic bezel is made. Start to finish.