I’ve always been fascinated with the concept of rigorous discussion, followed by making predictions, and finally waiting to see if the predictions come true. This describes many people’s entire careers and areas of expertise.
Scientists and savvy business folks have been playing this game for centuries, and with the invention of the modern economic system, for markets it’s generally been refined into a science. Although whether or not that type of science actually helped any economies is a story for another day.
To have the responsibility for actively making predictions based on something outside of your own control must be a rather tenuous position to hold. I make predictions all the time about how something is going to work (or not), or whether or not I can complete a project by a stated deadline.
The difference here is that I am a part of the process and have some control of variables, so I can affect the result. As such, I rarely make any claims about what is or will be if I have no say in it.
So imagine my surprise when, in one of my rare predictions about the future of 3D printing in watchmaking, I got one right: the Panerai Lo Scienziato Luminor 1950 Tourbillon GMT Titanium says it all.
The prediction
In a two part series focusing on 3D printing and the technological applications for watchmaking (see Focus On Technology: 3D Printing, What Is It Really? and Focus On Technology: 3D Printing, What Is It Really? Part Deux), I discussed the variety of processes and their best-use scenarios, including where they might be applicable in the watchmaking industry. That led to a prediction about where we might see 3D printing technology first appear in the world of watches.
My prediction was deliberately vague, but generally stated that the technology had a way to go and the most likely appearance would be in an expensive, limited edition watch by a smaller brand, where the 3D printing aspect would be in a non-moving component in the dial or case construction, and probably utilizing SLS or DMLS technology (we’ll get back to that in a bit).
With the release of Panerai’s Lo Scienziato Luminor 1950 Tourbillon GMT Titanium, we see a limited edition watch using 3D-printed components in the case construction. Okay, the smaller brand part didn’t pan out, but I’ll take it.
My accurate predictions were that the 3D-printed component is the watch case, it is for a watch limited to 150 pieces, and it was printed using the DMLS (Direct Metal Laser Sintering) process.
When I first saw this watch at the 2016 edition of SIHH I didn’t even remember that I had made the prediction; all I knew was that I was incredibly interested to hear more.
The first of its kind
The PAM00578 (as I will call it from now on since its name fills a paragraph by itself), as far as I know, is the first production watch to utilize 3D printing for the case construction – and specifically to use direct metal laser sintering (DMLS).
The case is made from titanium for extra lightness, but that’s not the only, or even the main, reason for using DMLS titanium.
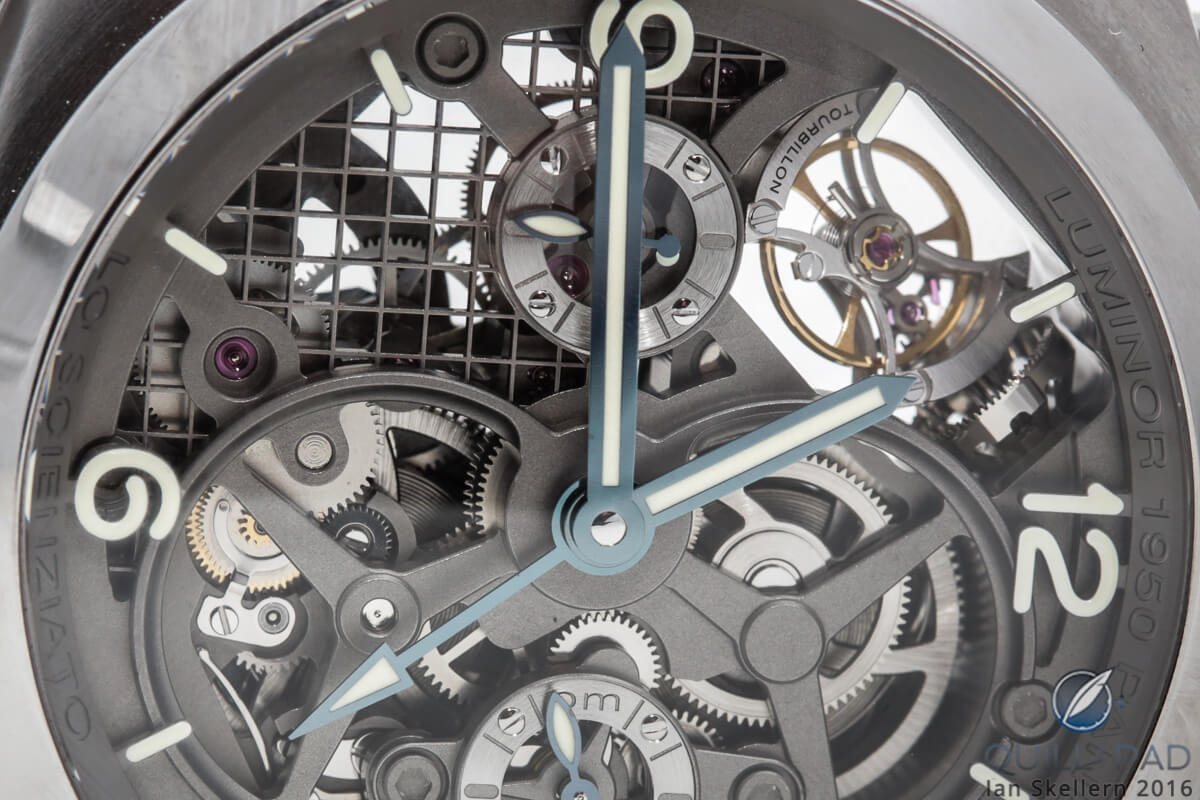
Close look at the rolling tourbillon (top right) of the Panerai Lo Scienziato Luminor 1950 Tourbillon GMT Titanium
This is where a bit of a refresher will come in handy. Direct metal laser sintering (DMLS) is a form of 3D printing in metal that is created when powdered metal is spread across a build platform that can move up and down. The layer of metal powder can vary in thickness, but the depth used for the PAM00578’s titanium case is 0.02 mm.
After the powdered metal is added, the build platform is ready to be sintered with a high-power Ytterbium fiber laser that heats the powder to a temperature just below melting point.
At this point, the powder fuses together to form a sintered solid, though not a homogenous crystal due to the fact it does not completely melt the material and allow for flow. If the watch case were to be seeing dynamic loads, then a different type of 3D printing called selective laser melting would have been employed.
The DMLS process is perfect for this application (creating a watch case) as it’s easier to control (easier being a relative word here) and produces better finish with the current technology.
The main advantages to utilizing DMLS titanium printing for a watch case come in the special considerations the process affords. Panerai could have very easily machined a case from solid titanium and made sure it was rigid and beautifully finished. But depending on the shape of the case, machining would create a huge amount of waste with up to 90 percent of the material being removed (and discarded) during machining.
The removal of that material is also very hard on tools – and compared to stainless steels, yields fewer components per tool due to the difficulty of machining. The DMLS process is a net-shape process, meaning that what material is utilized for the process in powder form goes directly to the final shape.
Only a very small amount of material is removed for the finishing processes so there is very little waste.
It’s what’s inside that counts
Material waste is a huge consideration when making a small amount of pieces – like the 150 pieces to which this model is limited. If the material used for making 150 cases weighs around 25 kilograms (55 pounds) from a solid bar of titanium, it means that somewhere around 20 kilograms (45 to 50 pounds) of material could be lost to chips in the shaping process.
Imagine the benefit of only using the material needed and minimizing the cost in forging, stocking, transporting, tooling, and machine time, just to make chips of titanium.
But the real secret of the DMLS process is that it can do something that no other process is capable of. A machined titanium case is internally solid, even though the material in the center of the case section is doing very little for the overall strength of the case.
When 3D printing a case, hollow sections may be included inside the case structure to eliminate weight where material isn’t necessary for strength. This is something that no other process can do and it is where the DMLS process earns its weight in gold . . . um, titanium.
The DMLS process therefore further reduces the weight of the titanium case, making it lighter than any similar titanium case made using traditional methods. This makes for an extremely light yet rigid structure with minimal fabrication waste and only minor need for secondary operations.
Considering the limitations of DMLS for miniaturized mechanical parts (basically they are not really feasible at this stage), using direct metal laser sintering to make a titanium case the lightest it can be is exactly what this technology should be used for right now.
Double measures
So if you are going to all the trouble to create a super light and technologically advanced titanium case from 3D printing, it would be a waste to throw a simple, heavy movement inside the case. And Panerai understood this.
Inside the PAM00578 is a movement made of titanium (machined using traditional methods, of course) and completely skeletonized. This makes the movement ridiculously light and very strong.
All of the movement plates and bridges are titanium, so the majority of a typical movement’s mass in relatively heavy steel and brass just isn’t there. The wheels are also skeletonized for further weight reduction, and the dial has been removed allowing the main plate to act as a surrogate dial.
The main plate is skeletonized in a square mesh pattern, providing rigidity to the plate but removing an extremely large amount of the material in the process. But this isn’t where the movement packs up and goes home after a good day’s work. No, the P.2005/T, as its name would suggest, includes Panerai’s awesome rolling tourbillon rotating perpendicular to the axis of the balance wheel,
This high-tech tourbillon is an excellent addition for such a material science adventure piece like the PAM00578.
Adding to the advanced case, the skeletonized titanium movement, and the rolling tourbillon, Caliber P.2005/T also boasts some other super functional complications. On the front of the dial we see a second time zone/GMT indicator and a day/night indicator to help keep some sanity during travel.
On the rear of the movement we find the ever important power reserve to keep track of the very stout six days’ worth of power reserve provided by the triple spring barrels operating in series.
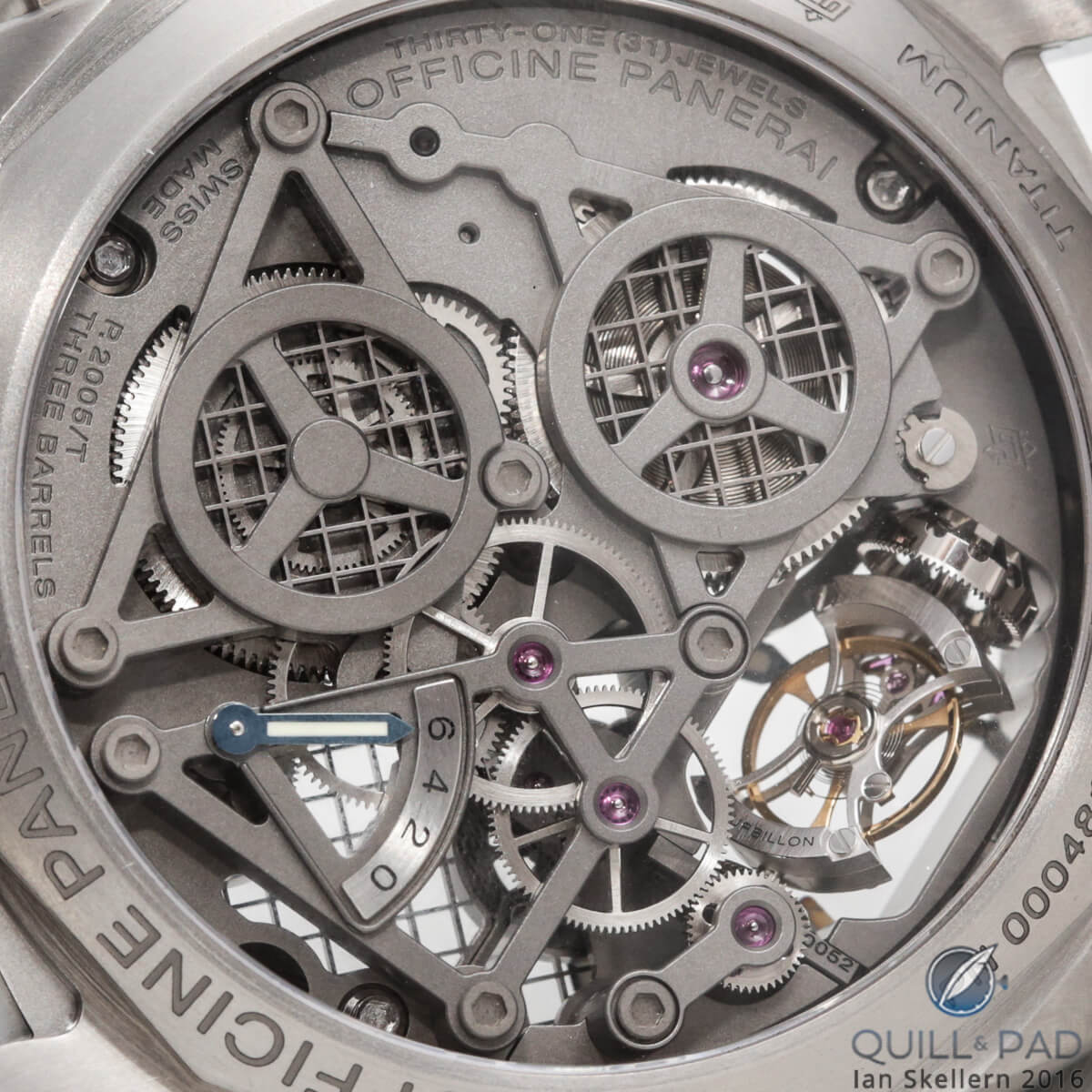
View through the display back of the Panerai Lo Scienziato Luminor 1950 Tourbillon GMT Titanium: note the power reserve indicator expressed in days
When all of these features are combined, the result is nothing short of increditastic. The desire to push the limits of production technology and actually utilize DMLS for the case is great, and knowing that I totally called that is even better.
The rolling tourbillon is always a joy to see, and the unique skeletonization of the movement really goes well with the intentions for this timepiece. I’m excited to see where the future takes us with regard to 3D printing and how it can be utilized for watchmaking. Many things are still far off, but it seems the days of 3D-printed cases could be here to stay.
So let’s get to it . . . the breakdown!
- Wowza Factor * 9.75 DMLS titanium case, fully skeletonized movement with a rolling tourbillon, this has wowza written all over it.
- Late Night Lust Appeal * 89.65 » 879.166 m/s2 Heavy, lustful forces act upon you even though the watch is super light thanks to all the titanium!
- M.G.R. * 68.1 I love a rolling tourbillon, and this movement features a ton of other useful features and awesome skeletonization.
- Added-Functionitis * Severe With the second time zone/GMT, the day/night indicator and the power reserve, it looks as though this watch has a pretty severe case of added-functionitis with a touch of the rolling tourbillons. Looks like prescription strength Gotta-HAVE-That cream is what you will need for the surprisingly light swelling.
- Ouch Outline * 11.1 – Getting all your arm hair ripped off from an accidental application of epoxy resin! Some people might know what that is like. You don’t really want to know, it’s a weirdly ominous feeling. Still, I would do it again for this watch!
- Mermaid Moment * DMLS, you say?! Just knowing that the case was made layer by layer, is completely hollow, and is super-light titanium would make anyone call the reverend to set a date!
- Awesome Total * 980 Multiply the water resistance in bars (10) by the total weight of the watch (98 grams) for an absolutely feather-light awesome total!
For more information, please visit www.panerai.com/lo-scienziato—luminor-1950-tourbillon-gmt-titanio.
And for further reading on 3D printing, you may enjoy Focus On Technology: 3D Printing, What Is It Really? and Focus On Technology: 3D Printing, What Is It Really? Part Deux.
Quick Facts Panerai Lo Scienziato Luminor 1950 Tourbillon GMT Titanium
Case: 47 mm, DMLS 3D-printed titanium
Movement: manually winding Caliber P.2005/T with one-minute rolling tourbillon
Functions: hours, minutes, seconds; GMT/second time zone, day/night indicator, power reserve indicator
Limitation: 150 pieces
Price: $143,000
Trackbacks & Pingbacks
-
[…] requirement of producing highly functional precision instruments for the toughest situations (see Prediction Comes True: Panerai Lo Scienziato Luminor 1950 Tourbillon GMT Titanium With DMLS 3D-Print… and The Panerai Lab-ID Luminor 1950 Carbotech 3 Days With 50-Year […]
-
[…] Along the same lines… http://quillandpad.com/2016/02/29/pr…titanium-case/ […]
Leave a Reply
Want to join the discussion?Feel free to contribute!
Panerai is trying to pull rabbits out of a hat because it is running out of GOOD design ideas. This wouldn’t be an issue if Panerai focused on advancing the technical aspects of the movement, or traditional high end case finishing.
This watch look like it has been finished by a machine. And that does not appeal to me.
Master then improve the traditional ways. Don’t jump to a new technology for the wrong reasons.
Tshark