Design Thinking: Schofield Blacklamp With Black Badger Lume
Details. Incredibly important and often overlooked, details are what makes everything real.
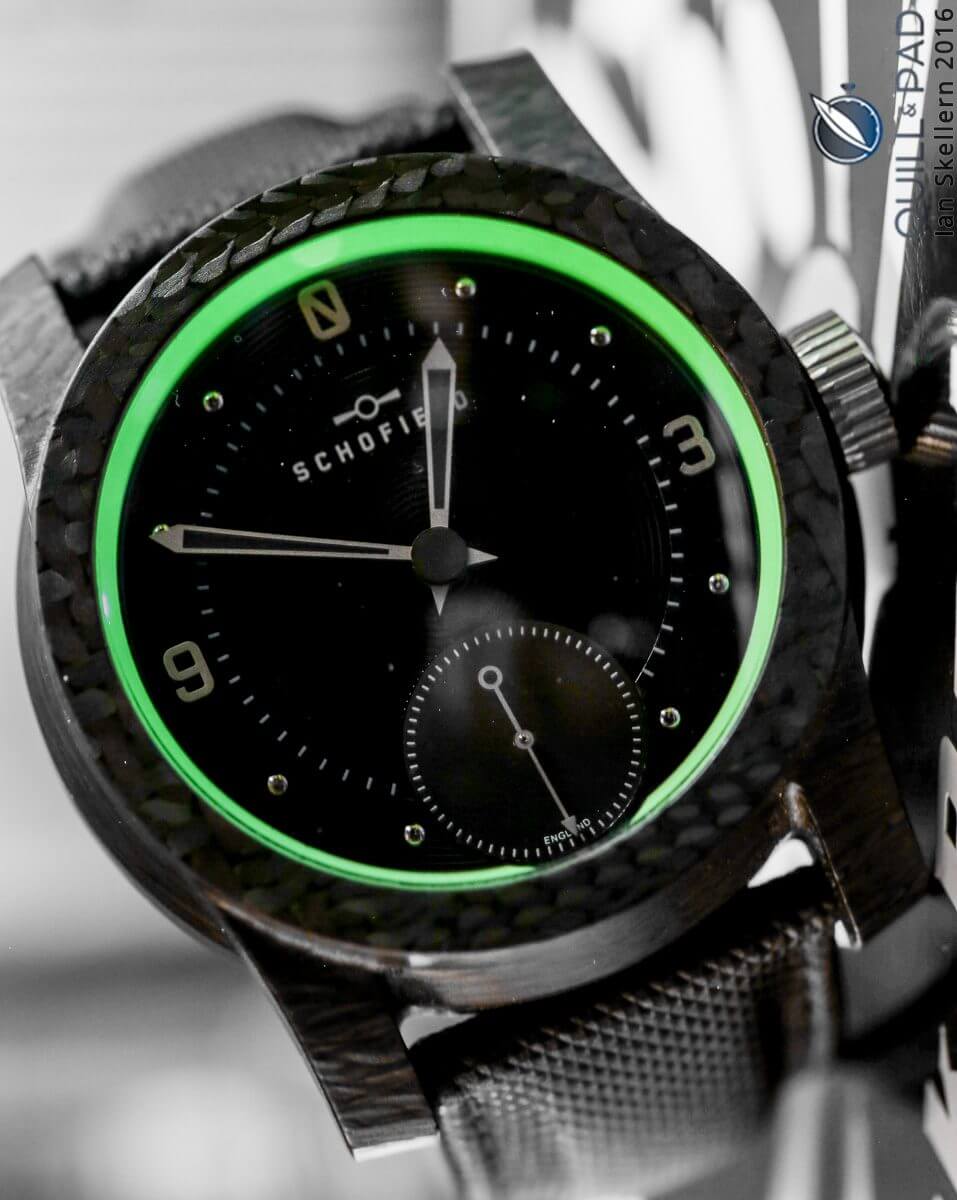
Schofield Blacklamp Moonglow with lume by Black Badger
When special effects and 3D graphics were first making their way into films and TV, they generally lacked any significant amount of realism to the point that they hardly fooled anyone.
The reason? The details.
It turns out that even if a person is not consciously aware of minute details, the brain notices their absence regardless. The real world is full of details; every object has hundreds, thousands, or millions of tiny little details that combine to create an understanding of that object through the senses.
Even something as simple as a pencil on a desk has a multitude of colors, reflections, shadows, highlights, textures, angles, shapes, and parts that are in relative scale to each other that the brain recognizes and, if enough are missing, notices when they are gone.
Your brain can account for variation, sure, but when too many little details are missing, perception is broken and any illusion becomes apparent. That is what happened for animations and CG effects attempting to replace real things: they lacked enough of the little details to make something appear real.
It has taken more than four decades of CG effects development to reach the point where properly implemented digital effects go largely unnoticed. This change, while partly due to an increase in computing power, comes largely from animators and designers paying attention to every detail, no matter how small. And it has made all the difference.
The same attention to detail must be observed in other disciplines, not the least of which is industrial design and product development. Designs that lack the appropriate amount of design thinking in the details are the products that look cheap, old, boring, plain, or simply unfinished.
The truly great products, whether they be expensive or affordable, usually share one thing: thoroughly considered details.
Giles Ellis, the man behind Schofield Watches, is first and foremost a man of details. An industrial designer by training, his passion is paying attention to the minutia that combine to create an object.
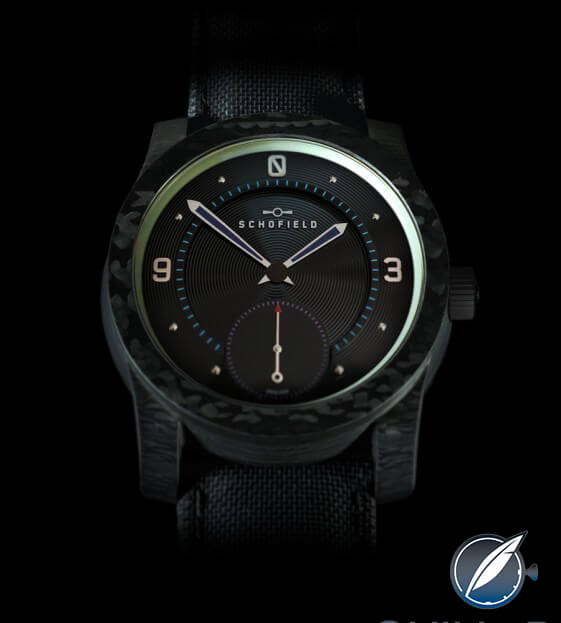
Schofield Blacklamp with Black Badger lume
The result is very often an honestly cool creation, and chief among these is the Blacklamp. This watch breaks conventions, not only for Schofield, but for watchmakers developing a product that is completely and utterly reasoned.
But to understand why all the details matter, you first need to be aware of what they are.
The development of the Blacklamp largely centers around the development of the carbon fiber material dubbed Morta, which was used for the case. It turns out that the impetus to develop the material comes down to a disagreement over the feasibility of creating such a material.
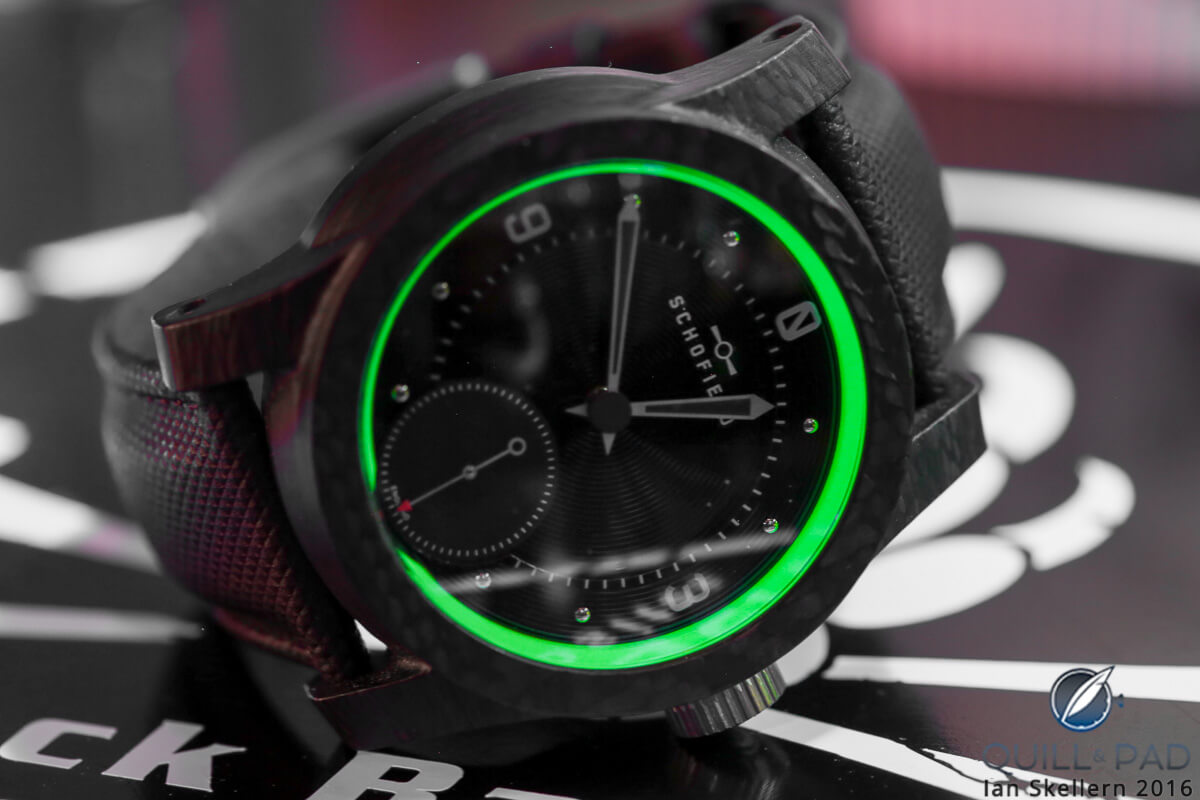
Schofield Blacklamp Moonglow with lume by Black Badge
Ellis had a meeting with a carbon fiber manufacturer specializing in Formula 1 components and high-grade military applications like those used in the Ocelot Foxhound by Force Protection. During this meeting, an unofficial challenge was posed to the CEO of the company when Ellis mentioned he didn’t believe that the manufacturer could make a case that was beautiful, functional, and strong enough for the design of a Schofield case (based on the Signalman style).
The CEO disagreed and proceeded to prove Ellis wrong. Using this project as a springboard for a new research and development facility within the company led by the UK’s leading composite specialist, 18 months of trial and error went into designing a new carbon fiber material.
First off, it was imperative that it didn’t look like carbon fiber (Ellis dislikes the now ubiquitous woven carbon pattern). It also needed to resist delamination and discoloration (a UV blocking agent was added to the resin), be completely non-porous (or close to it), and provide a good finish all while fitting with the look for which Schofield is known.
Testing all types of resins, woven sheets, and forming tools (as well as abandoned attempts at molding), lead to the material dubbed Morta.
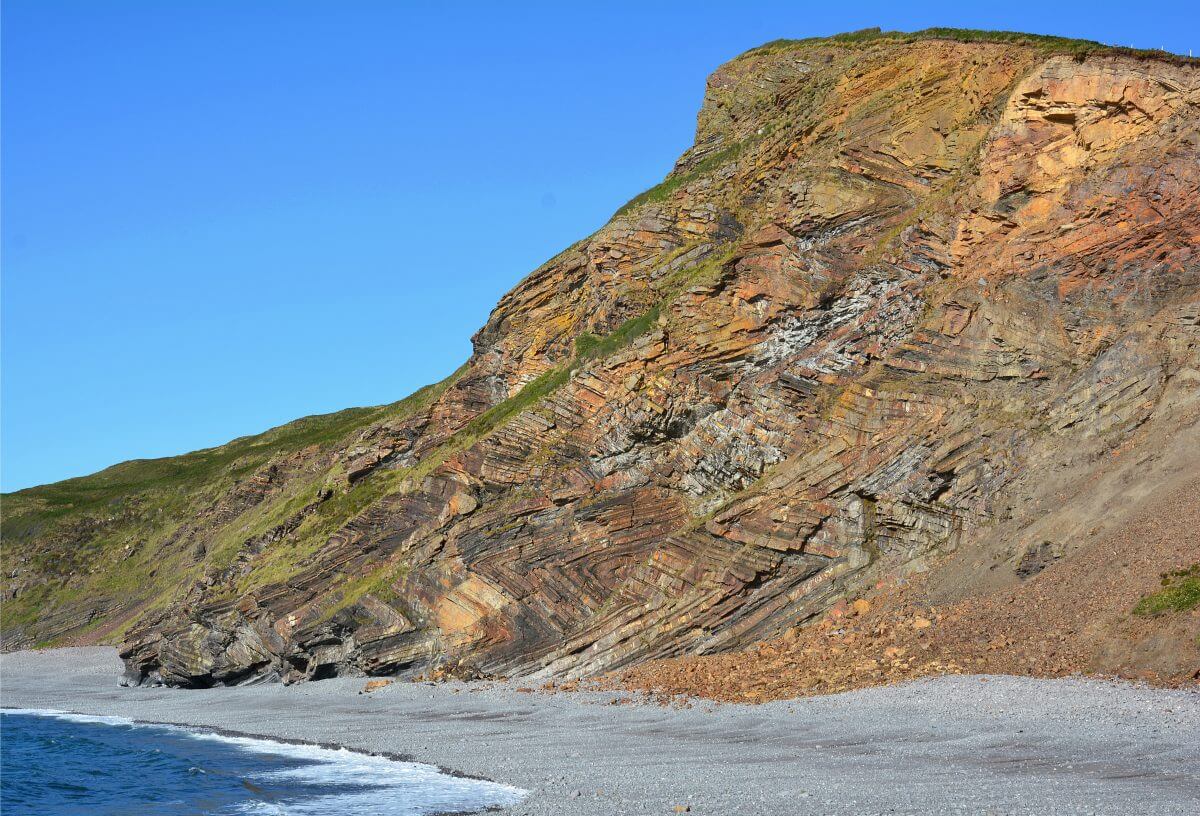
Chevron Folding at Millook Haven in Cornwall, England (photo courtesy Edmund Shaw/Wikipedia)
The inspiration for the wavy stratigraphy of the layers came from the cliffs and killas in Millook Haven, North Cornwall, where rock zigged and zagged upon itself to create beautiful patterns that begged recreation.
An early case sample nearly recreated the figures found in the cliffs, but proved overly complicated and expensive, and a new solution was found. Unlike standard carbon fiber layup techniques, which would see this case made from about 17 layers, the Morta billets that were created featured more than 90 layers compressed with approximately 15 tons of pressure in a state-of-the-art autoclave.
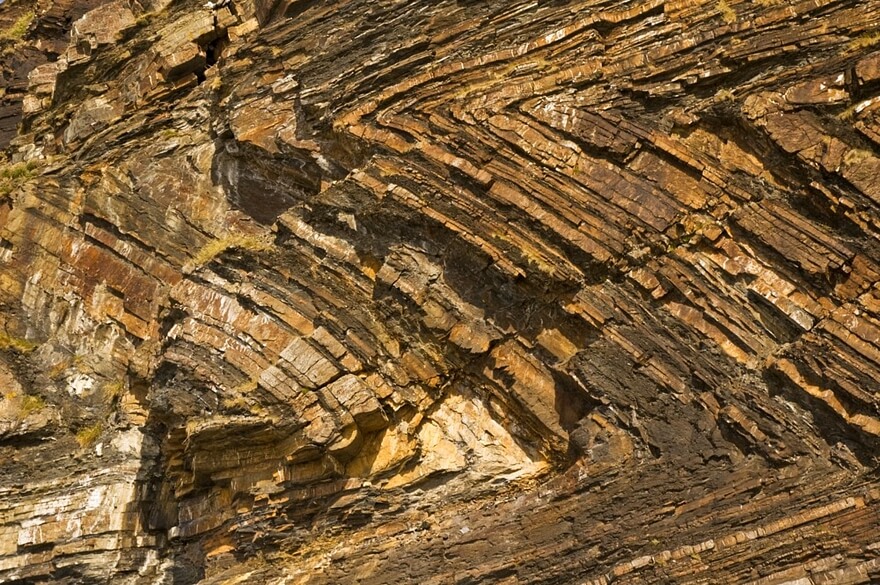
Contorted strata in the cliffs at Millook, North Cornwall (photo courtesy Smalljim/Wikipedia)
Geology nerd side note: “killas” is a Cornish mining term for metamorphic rock strata of sedimentary origin that were altered by heat from the intruded granites in the English counties of Devon and Cornwall.
The carbon fiber was bundled in six layer groups, where the direction of the carbon alternated between 0, 90, 45, -45, 90, and then 0 degrees. These groups were compressed and then stacked for the final assembly and compression to form the billet that would be machined into a solid carbon case.
The compression of so many layers and the use of specific resins resulted in a dense, pore-free material that was much more homogeneous than normal carbon fiber layups. Since lightness was not a concern, most of the unappealing qualities of carbon fiber (when used for watch cases) could be solved.
The last big constraints – eliminating the appearance of the woven pattern and making sure the lugs weren’t vulnerable to breakage – were solved by using a former during compression.
Making it beautifully better
This former slightly curved the layers to nearly follow the curve of the lugs, allowing them to be much more rigid and minimizing the machine-through of the layers during the shaping of the case.
Thanks to the fact that the curve didn’t match perfectly, however, it allowed the topmost layer to be machined enough to eliminate the standard woven pattern from the surface. This even worked on the bezel face, which is completely flat, so the slightly curved layer of carbon would be machined away just enough to disrupt the pattern and make for a more random and beautiful metamorphic pattern.
Of course, the process of machining the carbon fiber billet wasn’t a cakewalk after all that development of the material. The goal for the case was to closely replicate the dimensions and look of the Signalman case, which is famous for its sharp internal corners thanks to its three-part construction.
Since the Blacklamp would be a single-piece case, a tool with a very small diameter was used to slowly cut the profile of the entire case, stepping down very little after each circumnavigation. This process ate through tools with ease, usually breaking between three and five tools per case, as compared to getting five to ten cases when working with titanium or dozens of steel cases from a tool.
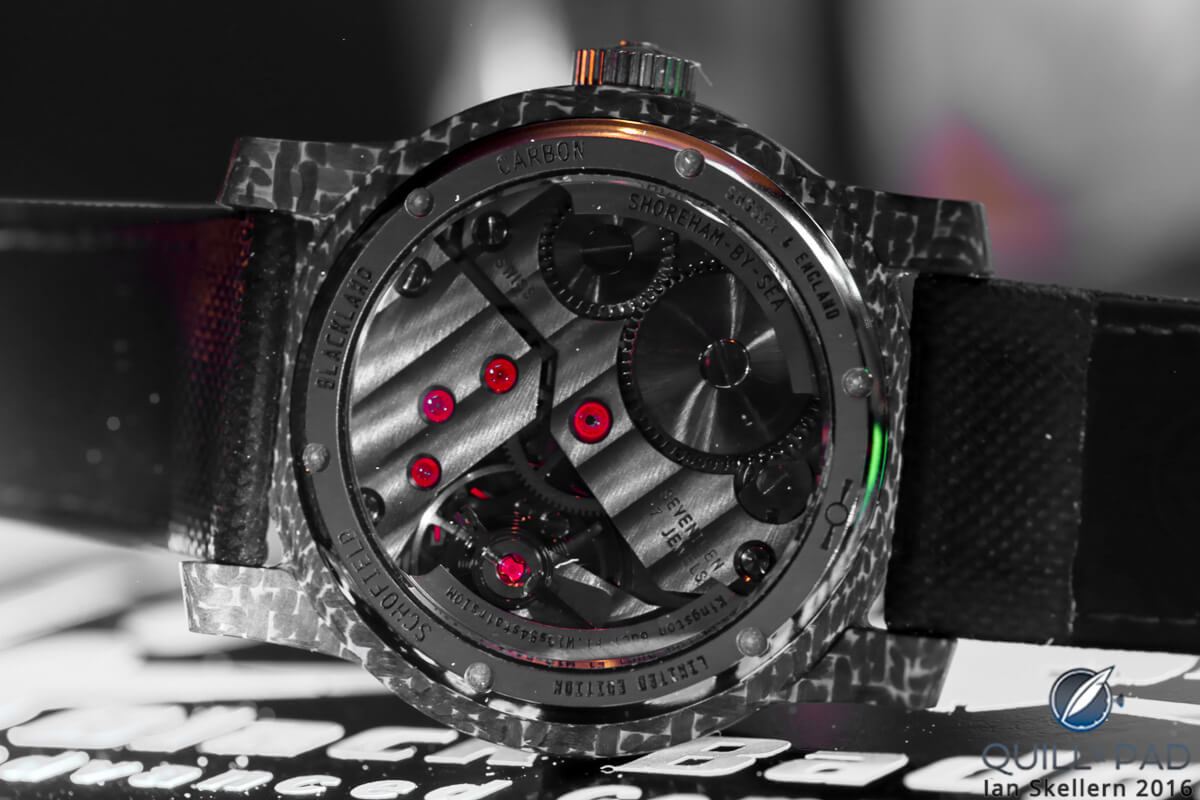
View through the display back of the Schofield Blacklamp
When considering how difficult it is to make and transform Morta into a case, the payoff for how it looks and how it performs is that much sweeter. The first tests for durability occurred in a meeting with the manufacturer where Ellis put a strap on the case and proceeded with an attempt to twist, yank, and stretch it into failure before simply slamming it down against the table multiple times – and watching the case just bounce off as if nothing had happened, looking like it was fresh off the machine.
The case was in the bag, but a mountain of details were left
After a satisfying conclusion to the carbon fiber creation adventure, there were still a thousand details to hone in an attempt to make an object worthy of being impressive in the creator’s eyes.
Every tiny aspect of the watch was scrutinized and tweaked in an attempt at aesthetic perfection.
The secondary driving factor in the design of the Blacklamp was the inclusion of a Moonglow ring made by Black Badger, and this feature drove a multitude of decisions including the size, shape, position, and material of the hobnail hour markers, the redesign of the hands to better utilize the glow from the ring (a bit of a reversal over Schofield’s regular hands), and the inclusion of tiny pointers on the opposite end of the hands to eliminate a floating effect that added visual confusion.
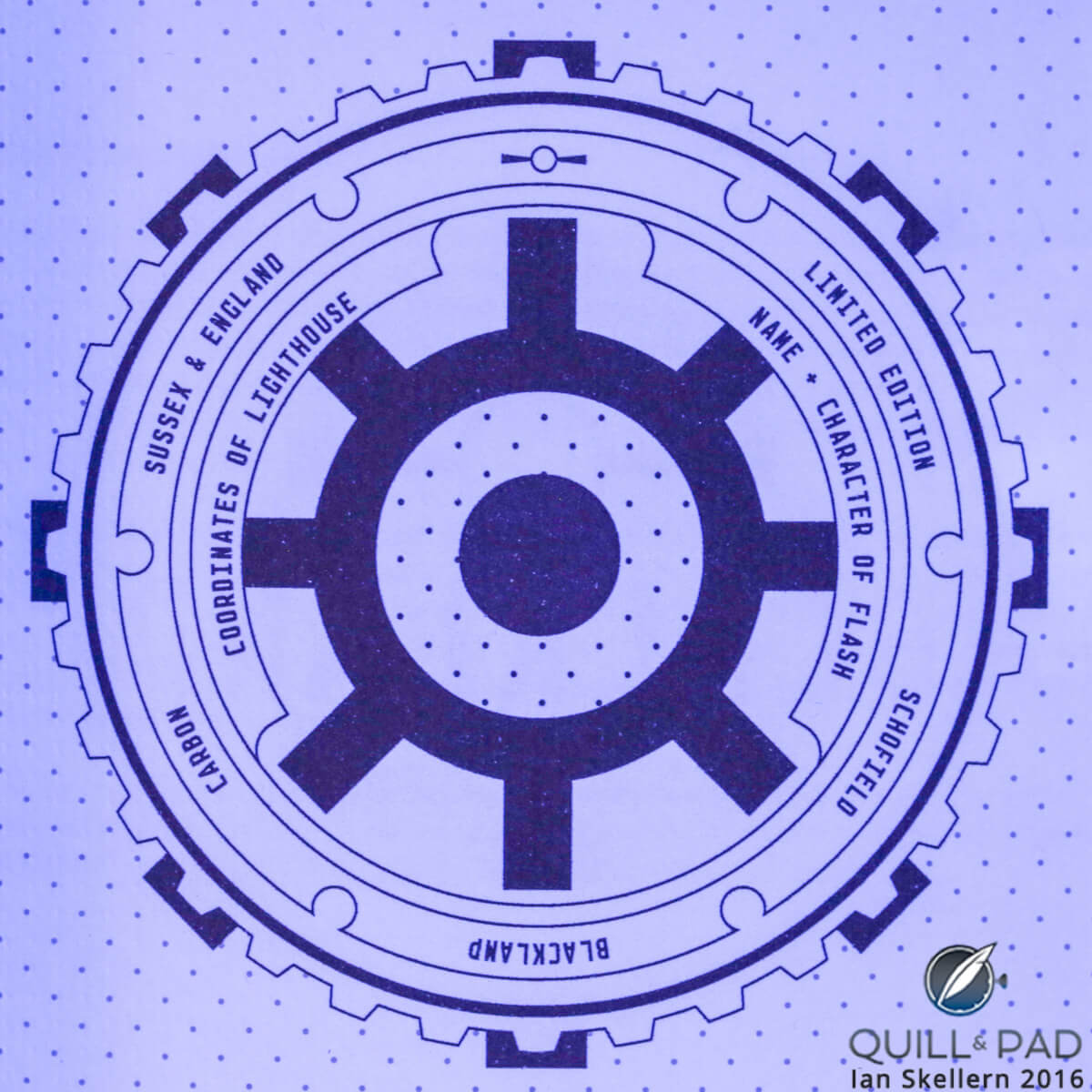
Schofield Blacklamp
Even the eventual complex colors of the second and minute markers to mimic the fluorescence color of UV-emitting materials (the subtle blues and purples) were painstakingly tested and vetted by Ellis before settling on what you see.
And once those details were decided upon, everything was tweaked again after seeing some production pieces so as to adjust spatial relationships on the dial, increase the amount of visible glow from the ring, better the finish of the engraved rings on the dial, and change the seconds subdial to a matte finish.
And still the details don’t stop there. The crown features an inset tritium gas tube at the center of a Unicode symbol for a lighthouse, which is featured on all the Schofield crowns. This symbol’s center dot is replaced with an actual light, something that almost seems obvious given the lighthouse imagery used to build the brand. But the detail of the light wasn’t easy either.
The tritium insert is supplied by MB-Microtec because otherwise Schofield would need to obtain special licensing to work with raw tritium and capsules; the purchased tritium tube came mounted in a sealed insert. Different inserts have different specs and materials, and after careful consideration of the available options, the specific insert chosen ended up coming in a nickel silver shell. One size up would have been steel, one size down would have also been nickel silver, but both of those would have changed the relationship of the symbol elements. So in this respect, choices were made to preserve one element while adding another.
Radioactivity side note: the tritium in the tubes has a half-life of 11 years, at which time it is only half as bright as it is new. By using an insert, Schofield can easily replace the tritium tube for a lasting glow.
Romanticism
In making these choices, a narrative develops that creates a history for the object – the watch – and a reason for its existence. This story is made of decisions, choices, and opinions about a direction and an intended result. And the result is a “romantic story of tactility,” as Ellis calls it, which allows a wearer to understand why it exists in the first place.
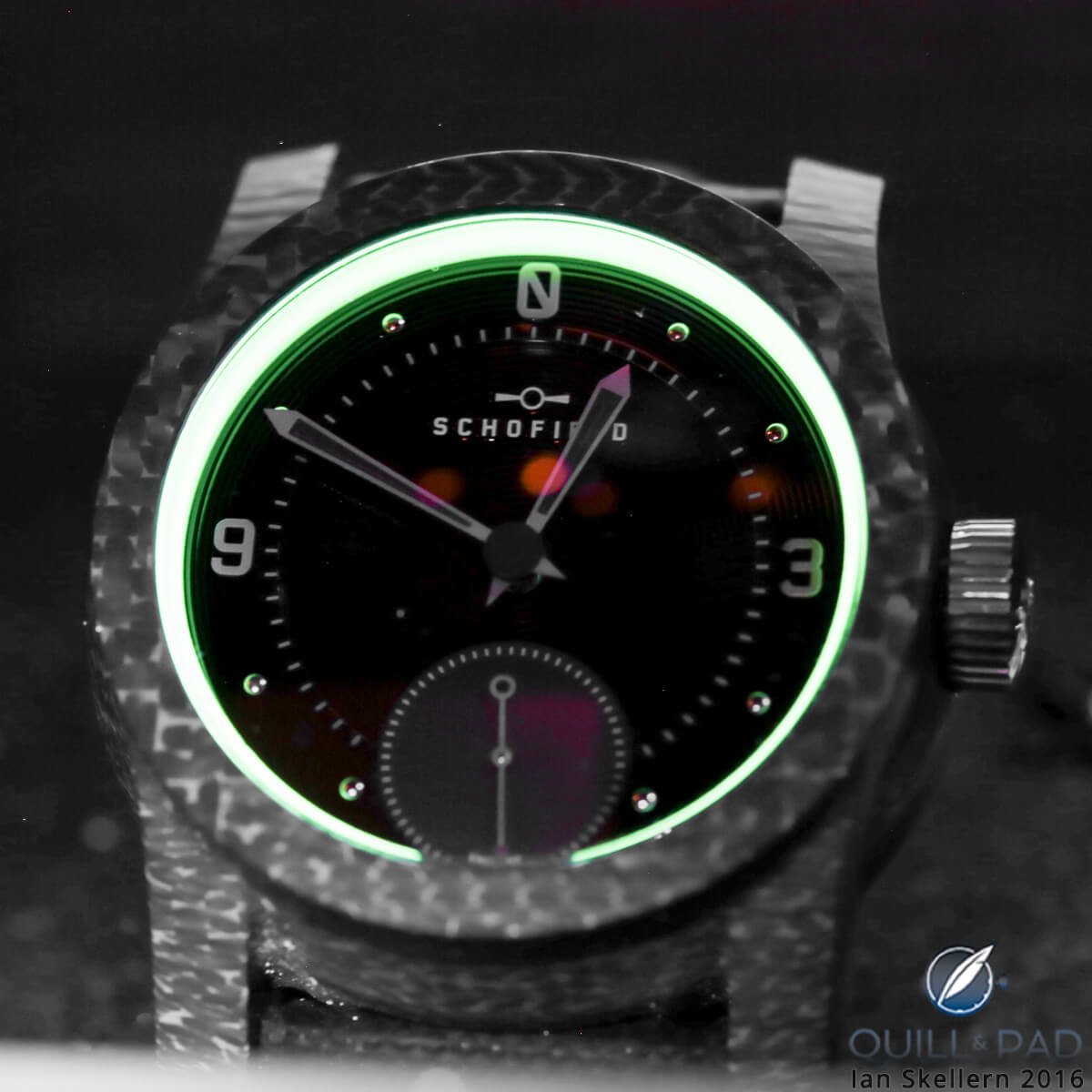
Schofield Blacklamp Moonglow with lume by Black Badger
And this is what drives the design process for Giles Ellis: the why. Every decision and every choice must, as much as possible, have a reason for being so. The process of creating the Blacklamp, and every object by Schofield, hinges on thinking.
This sounds obvious, but every designer has a personal line after whose crossing he or she will justify a decision with, “Well, I just like it.” This is not wrong, and in many cases in fashion and art, it is encouraged to provide differentiation and inspiration.
Ellis’ line of justification stretches to the horizon, and he personally feels that every choice must have a considered reason, at least in relation to another possible choice that could have been made. This proves a design’s honesty and makes the object’s history cohesive. The addition of accessories further builds on this history.
The Blacklamp comes with a miniature LED flashlight used for charging the Moonglow ring. The design thinking and development that went into that object was comparable to the Blacklamp itself. Months of prototyping and design refinement went into that little torch, and details from the Blacklamp carry over into its body, including the angled bevels matching the bevel on the case.
Keeping the flashlight’s barrel in raw aluminum helped matched the realness of the Blacklamp materials, but provided challenges for making the torch even work properly.
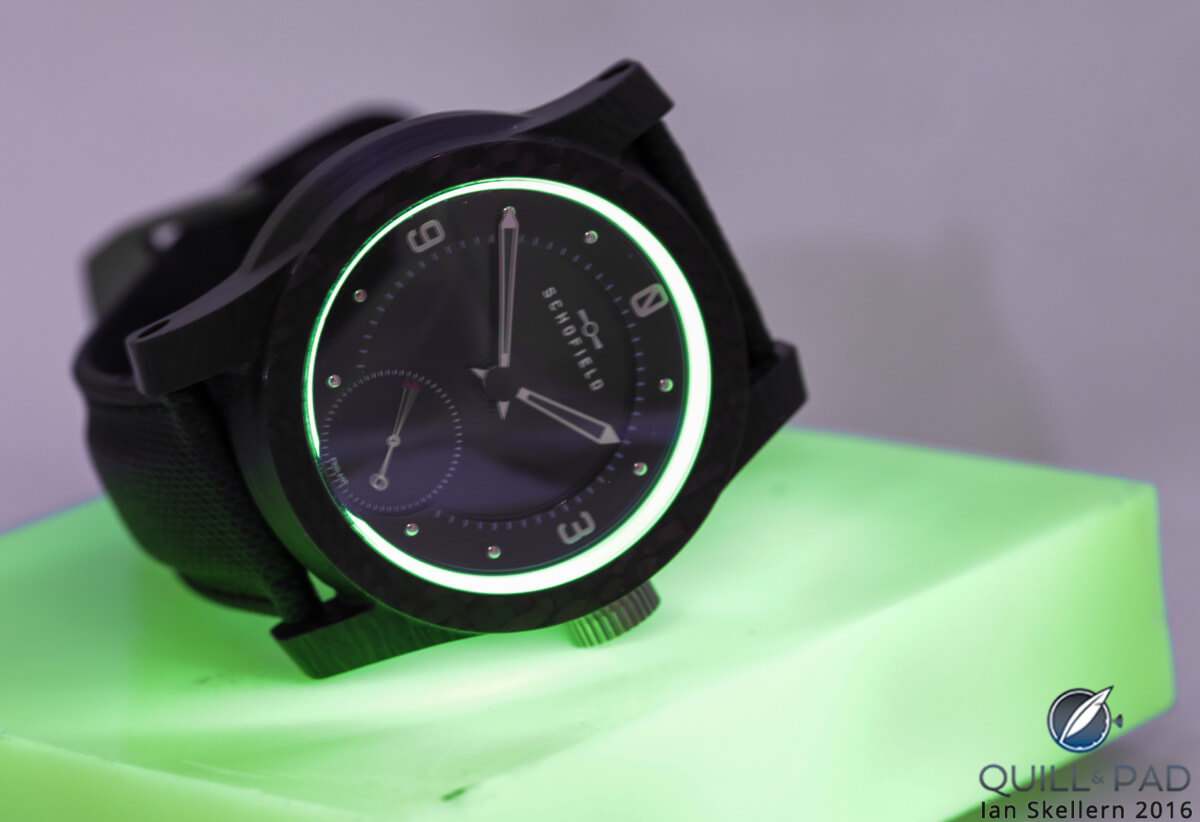
Schofield Blacklamp in carbon with Black Badger lume
All of these details add a richness to the product, something that Ellis is more than happy to discuss as it is an essential part of the Blacklamp and Schofield. Schofield is a watch company, but even more than that, it is a design-driven house of creation. Knowing the details behind every aspect of a watch, its accessories, and the entire brand are what drives Schofield forward.
This is also what allows you to be into the brand. I absolutely love the major watch brands, but they usually fall short of independents when it comes to a real, tangible connection to the product and the people behind it.
There is a raw sincerity that exists among independents, and Schofield focuses on the narrative behind why it creates what it creates. The people that buy a Schofield want to be a part of that narrative; they are intensely engaged in the story of its creation. The more you understand of an object’s creation, the easier it is to personally subscribe to it.
Obviously, I am one of those that subscribes to the Schofield narrative: from the sheer coolness factor of the watches all the way to the technical details that followed this type of object.
Heck, Schofield even inspired me to make my own tweed watchstraps and it keeps me interested in the industrialized luxury that is unfailingly honest in what it is. There is no pretentiousness in a Schofield watch, simply a desire to make awesomely cool things that are unique and real. It might not be your thing, or it may just be.
But that was never really the point anyway.
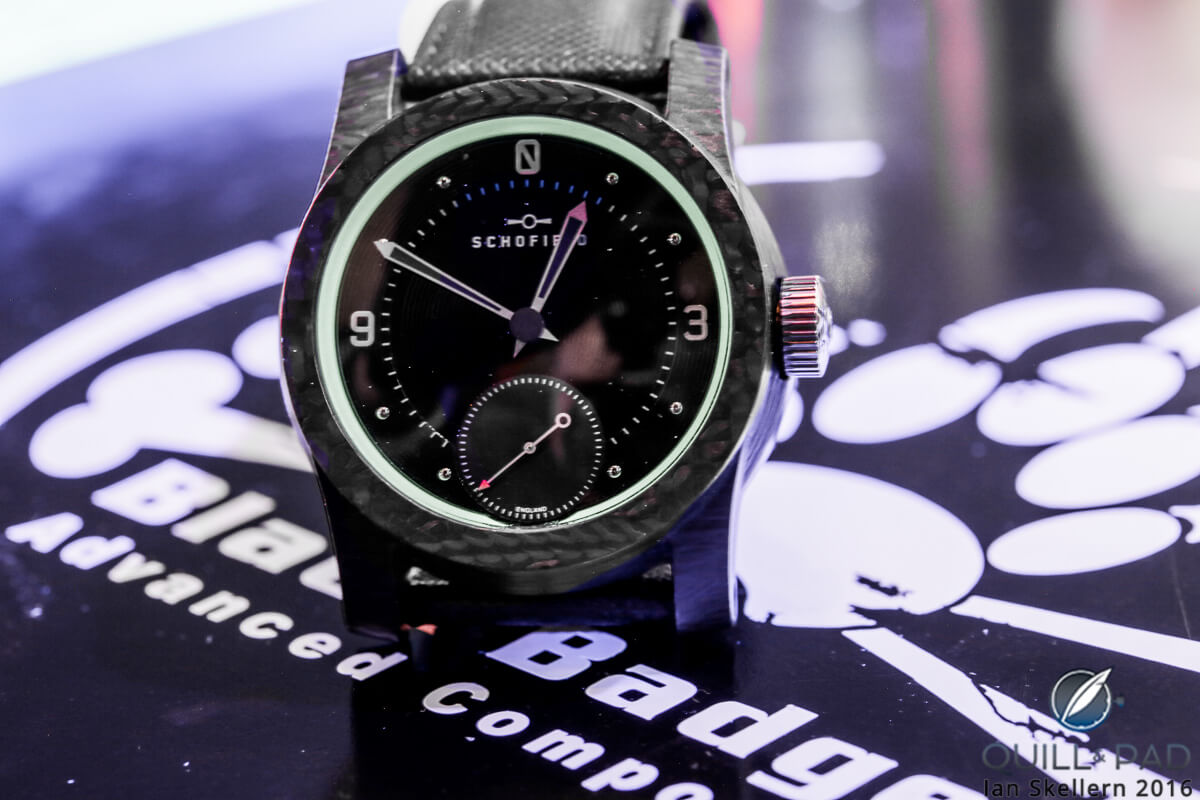
Schofield Blacklamp in carbon with Black Badger lume
And fitting with Schofield’s example, how about a detailed breakdown!
- Wowza Factor * 9.1 The wow this watch creates comes from the uniquely cool carbon case and the incredible glow from the ring on the dial!
- Late Night Lust Appeal * 102.85 » 1,008.613 m/s2 This watch makes me lust over 100 Gs, keeping me in my seat for hours of drool-inducing gazing. I need to go into the light!
- M.G.R. * 45.1 Some might say the use of a Unitas 6498-1 movement in a watch of this price point is underwhelming. I would say that a hacking seconds 6498 is pretty awesome if you are into old-school reliability. And let’s be honest, the movement is hardly the reason we are here with the Blacklamp!
- Added-Functionitis * N/A Alas, yet another time only watch that is hella cool regardless of the lack of complications. I’ll take that Moonglow and Morta any day, though, and skip the Gotta-HAVE-That cream.
- Ouch Outline * 11.3 Aluminum shaving in your eye. Sometimes you forget that you don’t have your safety glasses on when you blow out a part on the mill. And then you pay for it. But I’d pay that price many times over for a chance to get the Blacklamp on my wrist!
- Mermaid Moment * The glow is mesmerizing! Sometimes I feel like an insect, drawn uncontrollably to a beautiful glow that I can’t escape. Oh well, maybe I should just put a ring on it!
- Awesome Total * 870 Multiply the number of layers of carbon in the case (96) to the water resistance in bar (10), and subtract the weight of the watch in grams (90) for a glowingly awesome total!
For more information, please visit www.schofieldwatchcompany.com/shop/schofield-blacklamp.
Quick Facts Schofield Blacklamp
Case: 44 x 16.5 mm, Morta carbon fiber
Movement: manual winding Caliber Unitas 6498-1 with seconds modified to hack
Functions: hours, minutes, seconds
Limitation: 101 pieces customized with personal lighthouse details or custom text
Price: £9,900
Remark: comes with aluminum LED flashlight for charging the Black Badger ring of luminous material around the flange
Trackbacks & Pingbacks
-
[…] Joshua wrote a detailed review of this watch as well; find it at Design Thinking: Schofield Blacklamp With Black Badger Lume. […]
Leave a Reply
Want to join the discussion?Feel free to contribute!
Despite a lengthy article I’m none the wiser as to what a ‘moonglow ring’ actually is.
Hi Jeffrey,
Sorry that my article didn’t focus on the moonglow material enough. It is a non-radioactive photoluminescent polymer (plastic) that stores light energy and releases it over time, just like the lume on the hands. The Blacklamp comes with an LED torch to charge the ring, or it can be charged with sunlight. The moonglow ring was made by James Thompson of Black Badger and is a circular piece of the material embedded into the sides of the case just above the dial to provide a different style of dial illumination. The material is easily machinable and can be made in a variety of colors. The “Moonglow” material was originally developed by NASA and has been produced by a variety of companies more recently. If you want more information you can check out SchofieldWatchCompany.com or BlackBadger.se. Thanks for reading!