As the tenth anniversary of the InnoVision approaches, now is a great time to take a look back at Ulysse Nardin’s pioneering technologies as they led to the creation of the concept watch introduced in 2007.
Though it might seem anachronistic that a 163-year-old company famed for its marine chronometers would be the one to start a revolution in mechanical watchmaking, that is just what Ulysse Nardin did by leading the search for the perfect materials and advanced geometery to aid in cutting lubrication and improving watch efficiency.
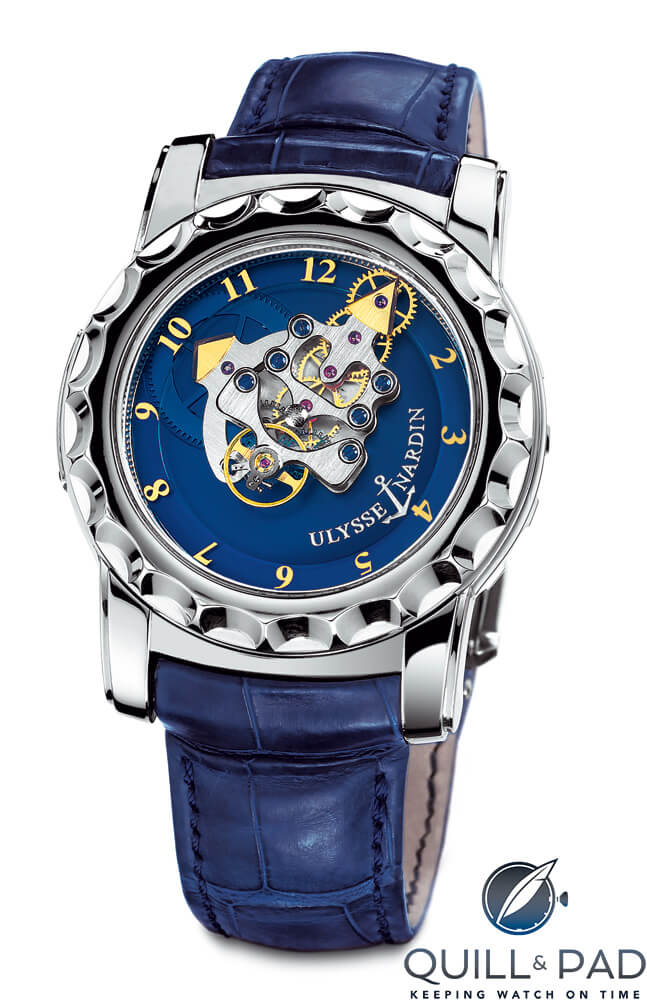
The first Ulysse Nardin Freak (2001)
This began with the Freak, a watch that broke every convention in watchmaking history.
Ticking within the original Freak of 2001 was a new escapement called the Dual Direct Escapement, the industry’s first successful promise of lubrication-free regulation. The wheels of this escapement were made of silicon since they could not be machined using traditional processes.
A short three years later, Ulysse Nardin was already experimenting with polycrystalline diamond components, another industry first, introducing a balance spring made of the material in the 2003’s Sonata.
Two years after that, a revised version of the Freak called Freak 28,800 V/h was presented at Baselworld 2005; it ran on a new and improved version of the Dual Direct escapement called the Dual Ulysse.
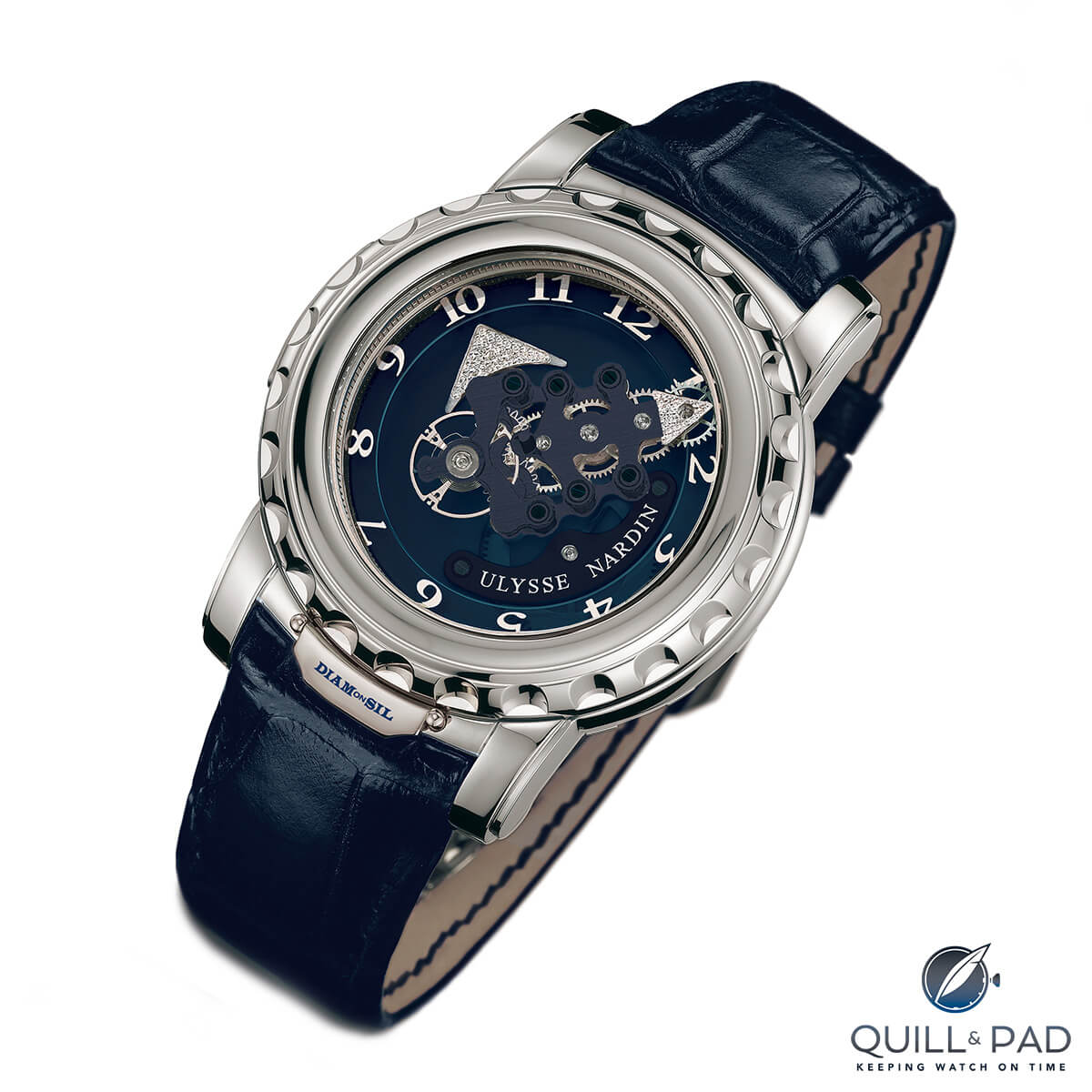
Ulysse Nardin Freak DIAMonSIL with diamond-coated silicon escapement and “hands” from 2007
Diamond micro components were also to be found in a version of this same watch called the Freak Diamond Heart. These components were manufactured by Diamaze Microtechnology SA, a joint venture between Ulysse Nardin, Sigatec, and the GfD Institute (a producer of diamond components for tools and the medical industry). This company’s raison d’être was to create diamond-coated silicon and “grow” synthetic diamond as perhaps best exhibited in 2007’s Freak DIAMonSil.
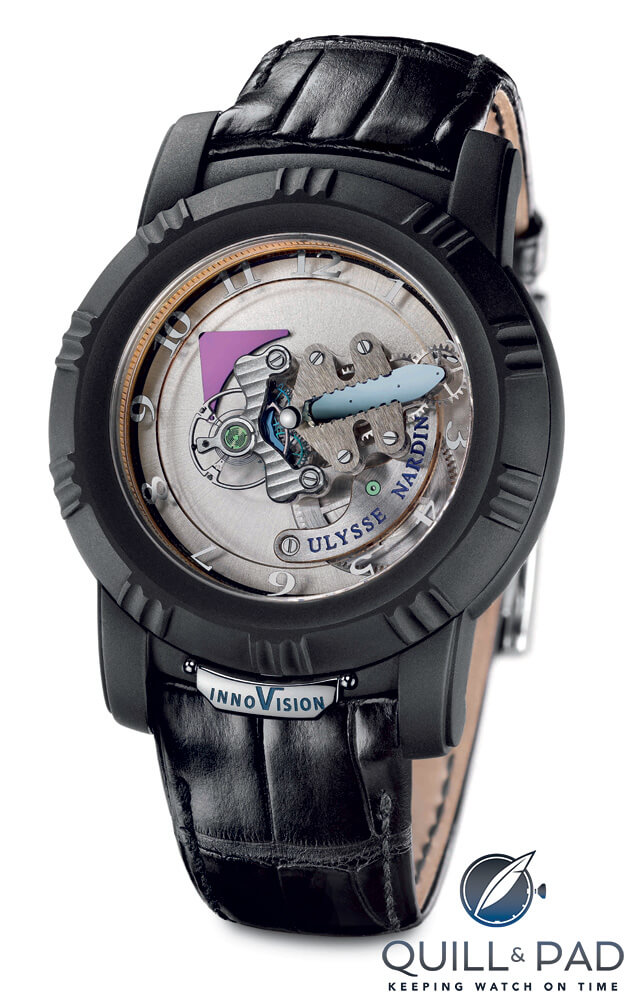
Ulysse Nardin’s InnoVision from 2007 was a concept watch designed to showcase Sigatec’s combined LIGA/silicon technology
And while the era of this new material began for most experts with the advent of the Freak back in 2001, a forward-thinking watch most experts agree functions as something of a laboratory on the wrist, it was the 2007 appearance of a Freak variation called InnoVision that truly heralded the future of what watchmaking could be.
Silicon
But before I head into what made this watch instrumental in Ulysse Nardin’s technical progression, I’d like to review the ten key technologies pioneered by the Le Locle-based brand that were instrumental in the InnoVision.
Silicon (silicium in French and Latin) is an element that has been used in other high-tech industries for decades. It is the eighth most common element in the universe by mass and the second most abundant element on earth after oxygen, making up 25.7 percent of the earth’s crust.
First identified in 1787 by Antoine Lavoisier, today silicon can be found in glass, cements, and ceramics – though the largest application of metallurgical-grade silicon, representing something like 55 percent of the world’s consumption, is found in the manufacture of aluminum-silicon alloys to produce cast parts generally utilized in the automotive industry.
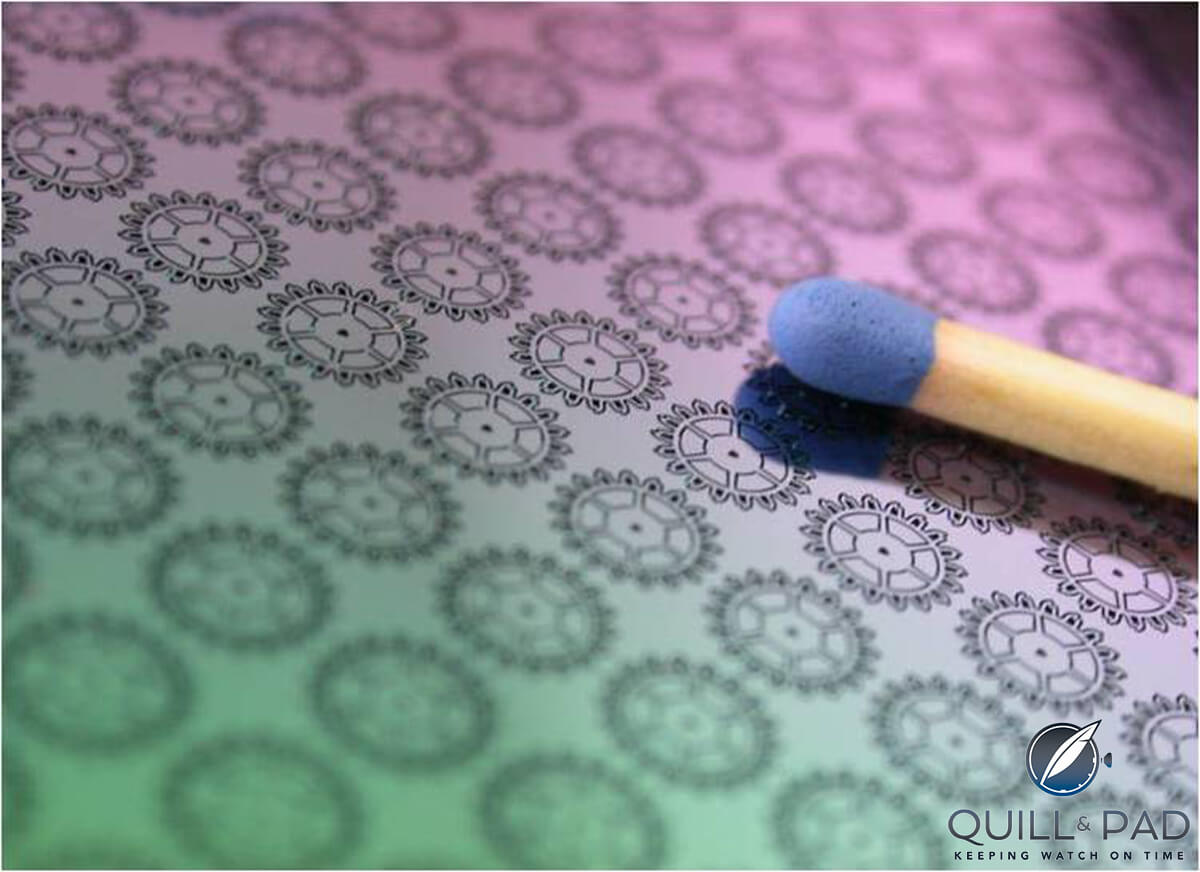
Silicon escape wheel wafer made by Sigatec for Ulysse Nardin
As a pure silicon wafer, is used for electronics and other high-tech applications, now including watchmaking.
Silicon originally made a splash in the watch industry thanks to CSEM (Centre Suisse d’Electronique et de Microtechnique S.A), a private company jointly owned by the Swatch Group, Rolex, Patek Philippe, the Richemont Group, and the Federation of the Swiss Watch Industry (FH).
CSEM, which at the time shared a research lab with the Institute for Microtechnology of the University of Neuchâtel, a non-commercial supplier, has been working with silicon since 1992 with the intent of selling its ideas to watch brands willing to sponsor research.
This is the same institute that Ulysse Nardin first commissioned to aid in manufacturing the first watch components resulting from the company’s research. However, it was Ulysse Nardin’s continued exploration of the LIGA process, which was made most accessible by Mimotec from 1998, that put the company’s extensive research into real motion.
Mimotec’s products not only enabled Ulysse Nardin to have perfectly smooth, friction-free parts in nickel and nickel-phosphorus alloys that were ideal for prototyping, but also joined Ulysse Nardin in the quest for further research into silicon. In 2006, the two companies entered into a joint venture to explore the combination of LIGA and silicon.
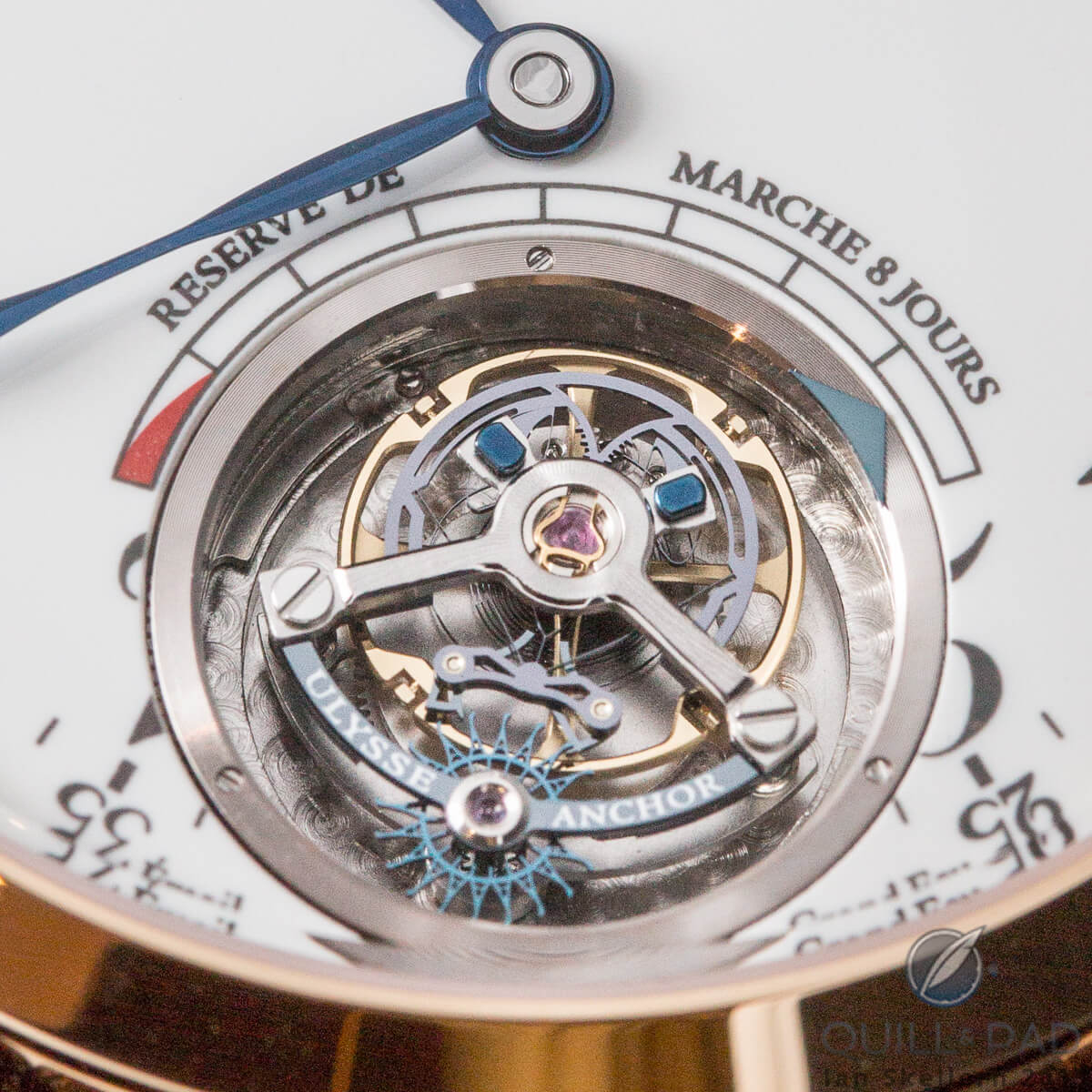
A close look at the tourbillon and escapement of the Ulysse Nardin Anchor Tourbillon
The culmination of this joint venture was the Ulysse Anchor Escapement of 2015, a timepiece proving that the historical anchor escapement could be made viable for wristwatches thanks to new technologies. For full details on this watch, see The Ulysse Anchor Tourbillon By Ulysse Nardin.
Using silicon for watchmaking has many advantages, among them flexibility, durability, hardness, elasticity, accuracy, low density, and no need for lubrication. LIGA offers many of the same advantages.
LIGA
Sigatec is a commercial supplier essentially applying the direct LIGA process with the addition of DRIE (deep reactive ion etching) to silicon. Components manufactured with this process are not only flat, but can be produced on two levels and in a variety of interestingly shimmering colors.
But to understand this process, we need to first understand what LIGA is – and where Sigatec came from.
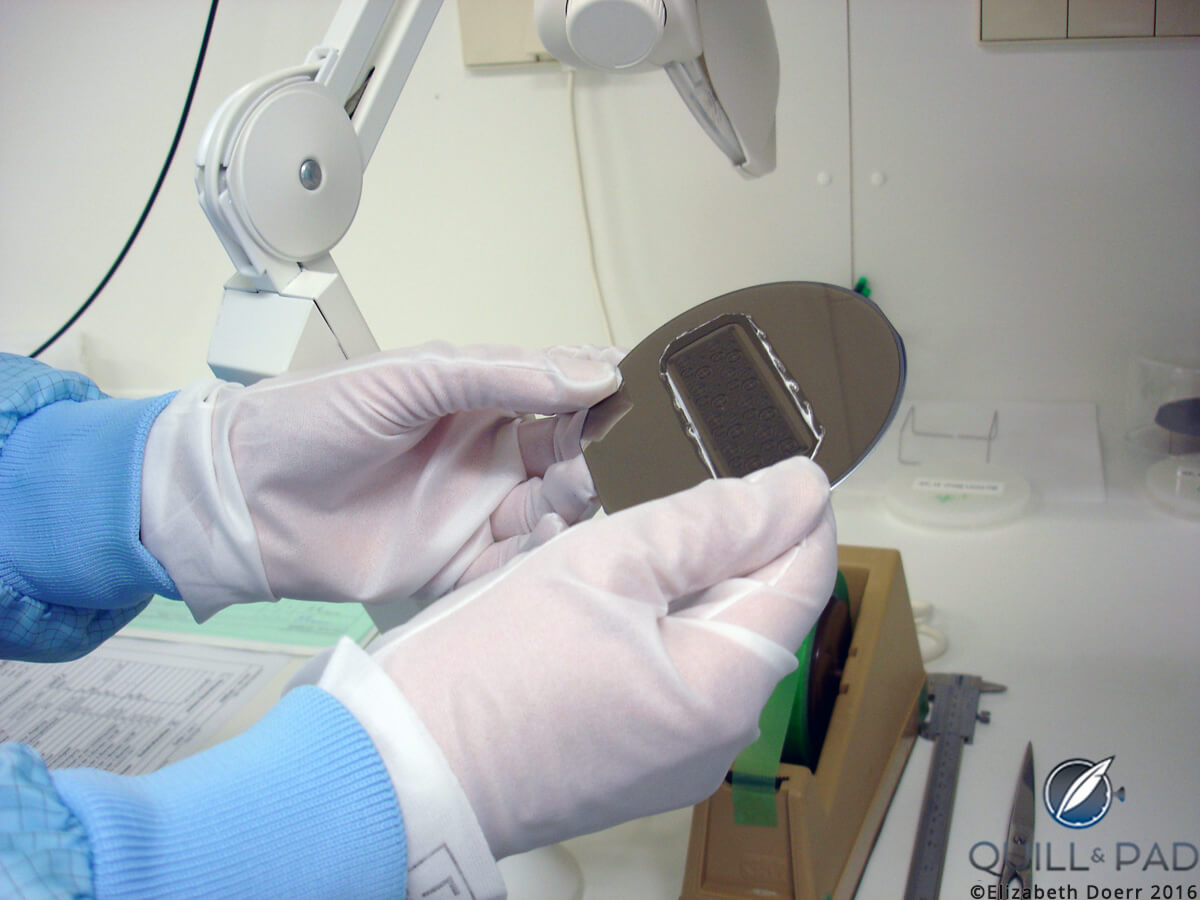
A LIGA wafer at the Karlsruhe, Germany KIT/IMT institute created with the help of X-ray light
The word LIGA is a German acronym standing for lithography (Lithografie), galvanic (Galvanisierung), and plastic molding (Abformung).
The lithographic process is probably one that is more familiar to the layperson as an artistic medium used for copying, printing, and transferring something such as text or art onto a smooth surface. The modern photographic litho process is used, for example, on credit cards.
LIGA uses light for stabilization, and its founding research institute – IMT/KIT in Karlsruhe, Germany (the commercial arm was recently privatized to become Microworks) – uses a very expensive X-ray light.
Used to manufacture micro components for watchmaking and other industries, LIGA components begin life with an X-ray mask containing precise computer-generated shapes of the parts to be manufactured. The X-ray light “exposes” the structural information onto a layer of polymer. Then a solvent is introduced, leaving behind the non-irradiated plastic as the primary structure.
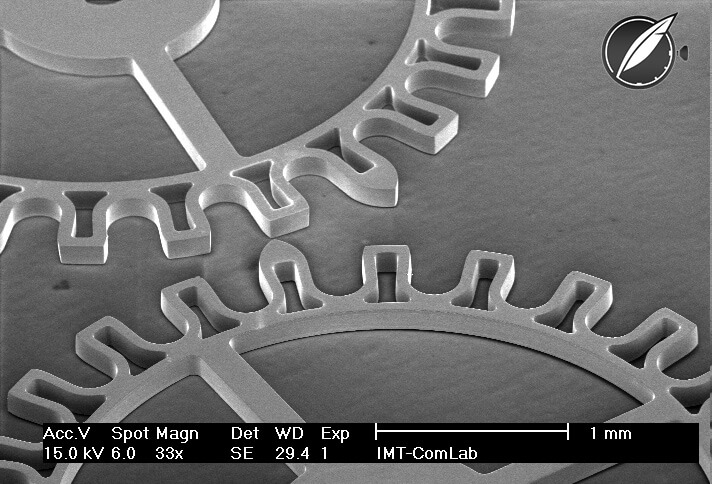
Ulysse Nardin escape wheels in LIGA nickel-phosphorus from the first version of the Freak
The galvanic part of the acronym can be better described as electroforming, which “grows” a component in a plating bath atom by atom until it reaches the desired thickness.
The spaces generated by the removal of the irradiated plastic material are then filled with an electroformed metal. Due to its thickness, the variety of metals and alloys is somewhat restricted, with a main focus on nickel, copper, gold, nickel-cobalt, nickel-phosphorus, and nickel-iron.
Today, LIGA is used to manufacture micro components for many industries, though for metal watch component production the molding step is not used. LIGA, or direct LIGA, as the shortened process is known, is perfect for creating horological micro components of very high quality.
In stark contrast to wire spark erosion technology, LIGA components are perfect every time and require no finishing. There are no burrs, since they are not cut, and therefore do not need to be trimmed or polished.
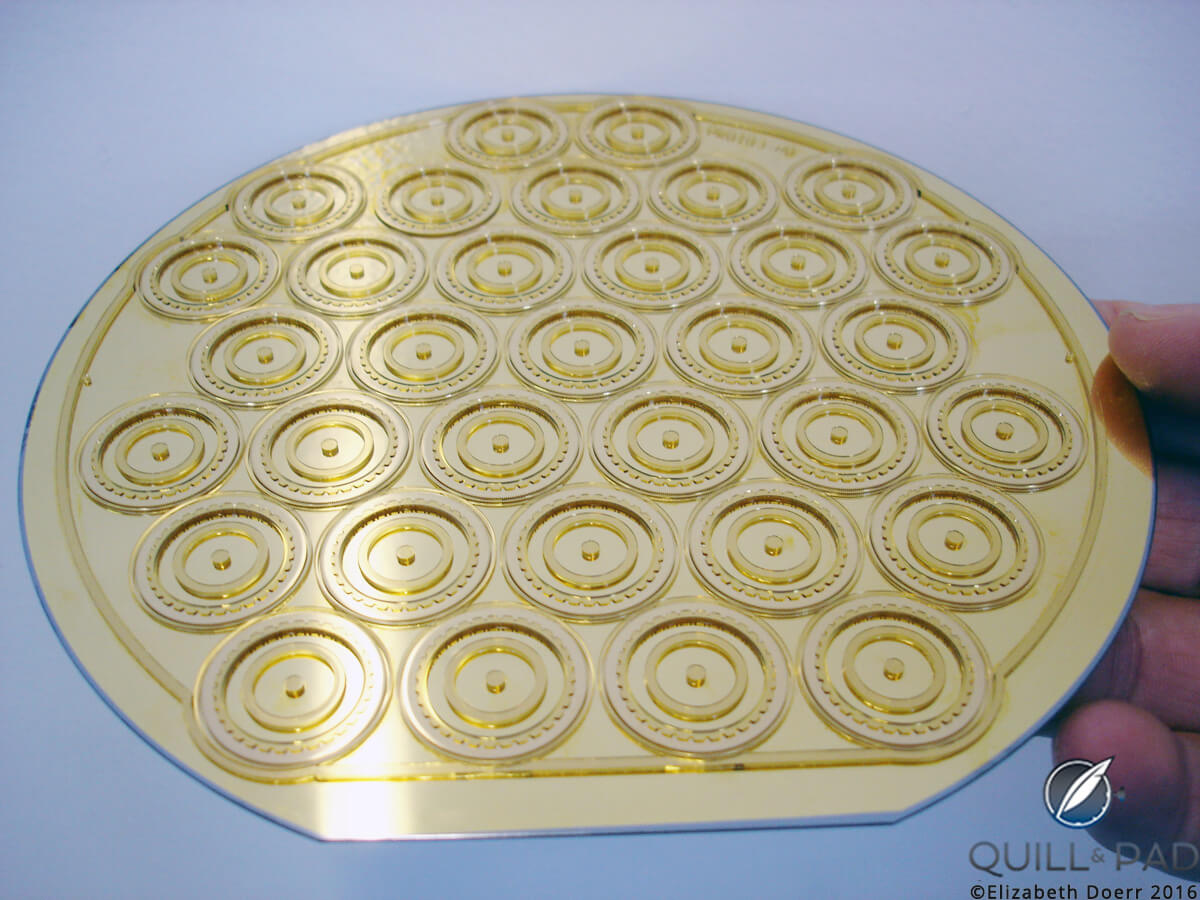
A LIGA wafer at Mimotec created with the help of ultraviolet light
The first commercial firm to use the LIGA process for extended watch industry purposes was Mimotec, founded by Dr. Hubert Lorenz and Nicolas Fahrni in 1998. Lorenz’s idea was groundbreaking for watchmaking: using a recipe for an SU-8-based photo sensitive epoxy developed by IBM, he conceived a much more cost-effective system of direct LIGA. Mimotec also uses a less expensive ultraviolet light source for the exposure process instead of X-ray light, making it more viable as a solution for watch companies.
Mimotec’s first step in the direct LIGA production process is to design the photo mask, which then undergoes ultraviolet lithography to produce wafers with the parts’ negative in SU-8 epoxy. Then follows the electroplating step: the SU-8 and wafer are dissolved, leaving behind the desired micro components, which are ground to get the exact thickness desired. The final step comprises only inspection and quality control; no finishing is necessary.
DRIE and silicon
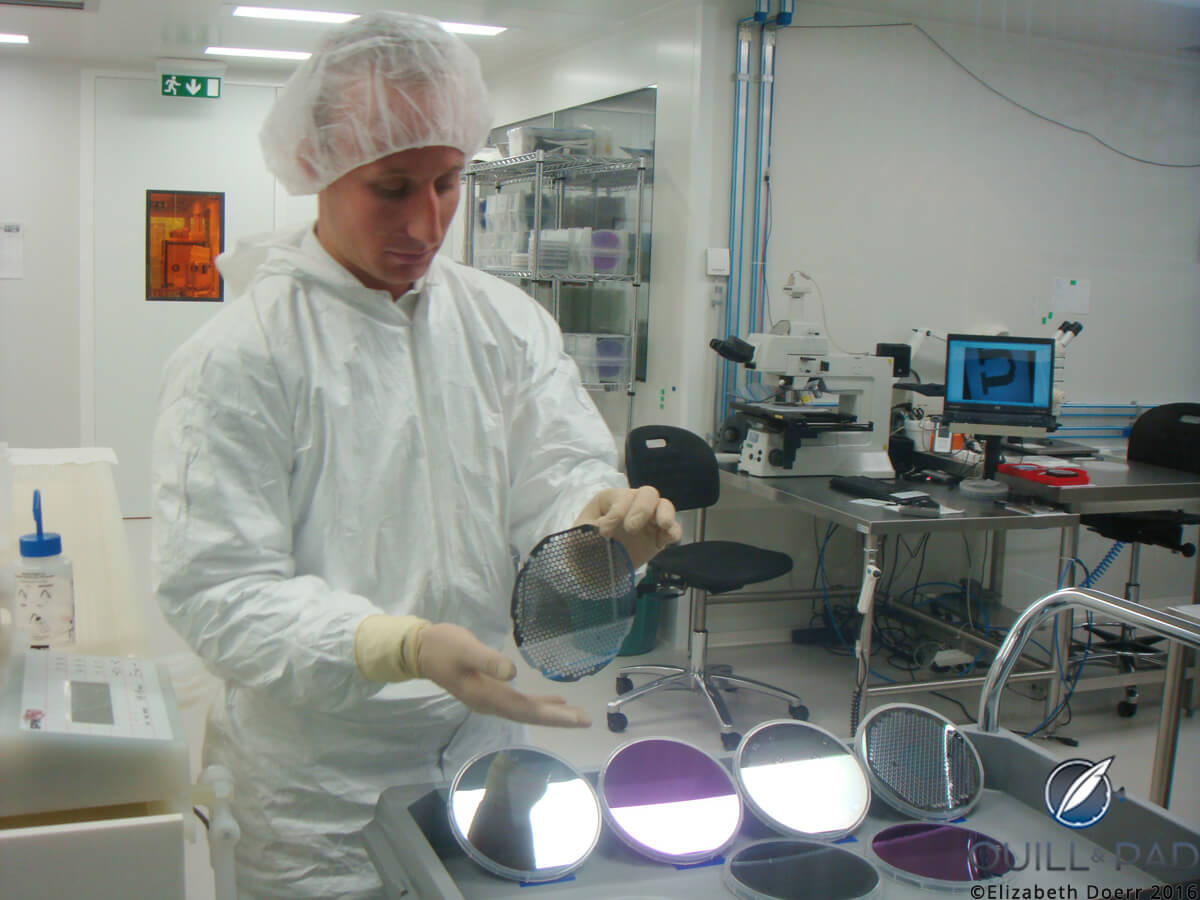
Producing a silicon wafer at Sigatec
Sigatec is a joint venture company between Mimotec and Ulysse Nardin created to harness much of the same ease in manufacturing already in use on LIGA micro parts to apply them to silicon. The silicon process developed isn’t too terribly different except for the materials used and heat applied.
DRIE (deep reactive ion etching) is a plasma etching process attacking the wafer now made of silicon instead of polymer and electroformed metal, tracing the outlines of the figures supplied by a thin chromium mask and simultaneously protecting the walls of the micro components.
After having received a photo resistant layer and UV radiation, the wafers are oxidized in an oven at 1,100°C for six to seven hours.
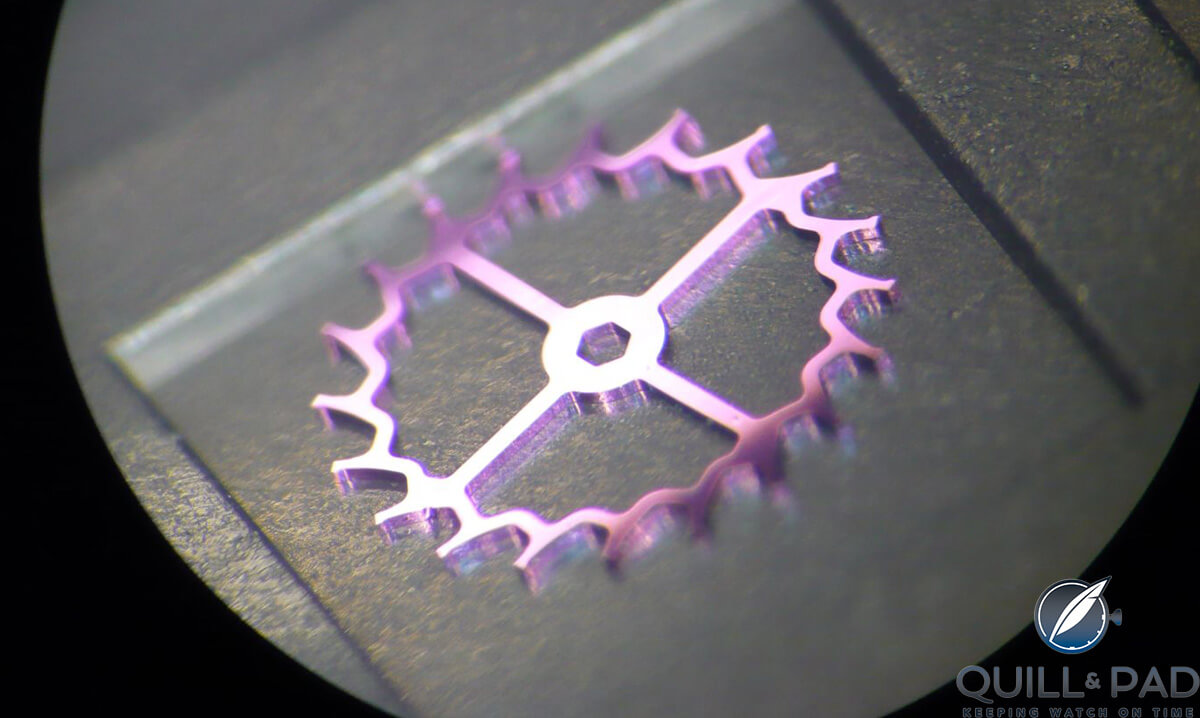
An iridescent silicon escape wheel at Sigatec
At this point in the process, the wafer can also take on a desired color by adding a vapor to the oxidation. These colors – which are very visible on Ulysse Nardin’s InnoVision movement – iridescently shimmer and shine. Then the parts are chemically released from the wafer, after which they undergo visual quality control.
InnoVision 2007
Back in the mid-2000s, these seemed like quasi futuristic technologies. Today, in 2016, we take these technologies so for granted that they are hardly talked about anymore. I sometimes wonder whether it is because the watch writers du jour use less space to mention them for whatever reason or if it is that the watch-interested public is less interested in hearing about them anymore. Something to ponder and discuss, at any rate.
Ulysse Nardin’s InnoVision showcased a number of innovative components including smooth silicon bearings that can be manufactured directly as one piece together with silicon bridges that are easily added to plates made of other materials, eliminating the need for jewel bearings and lubrication.
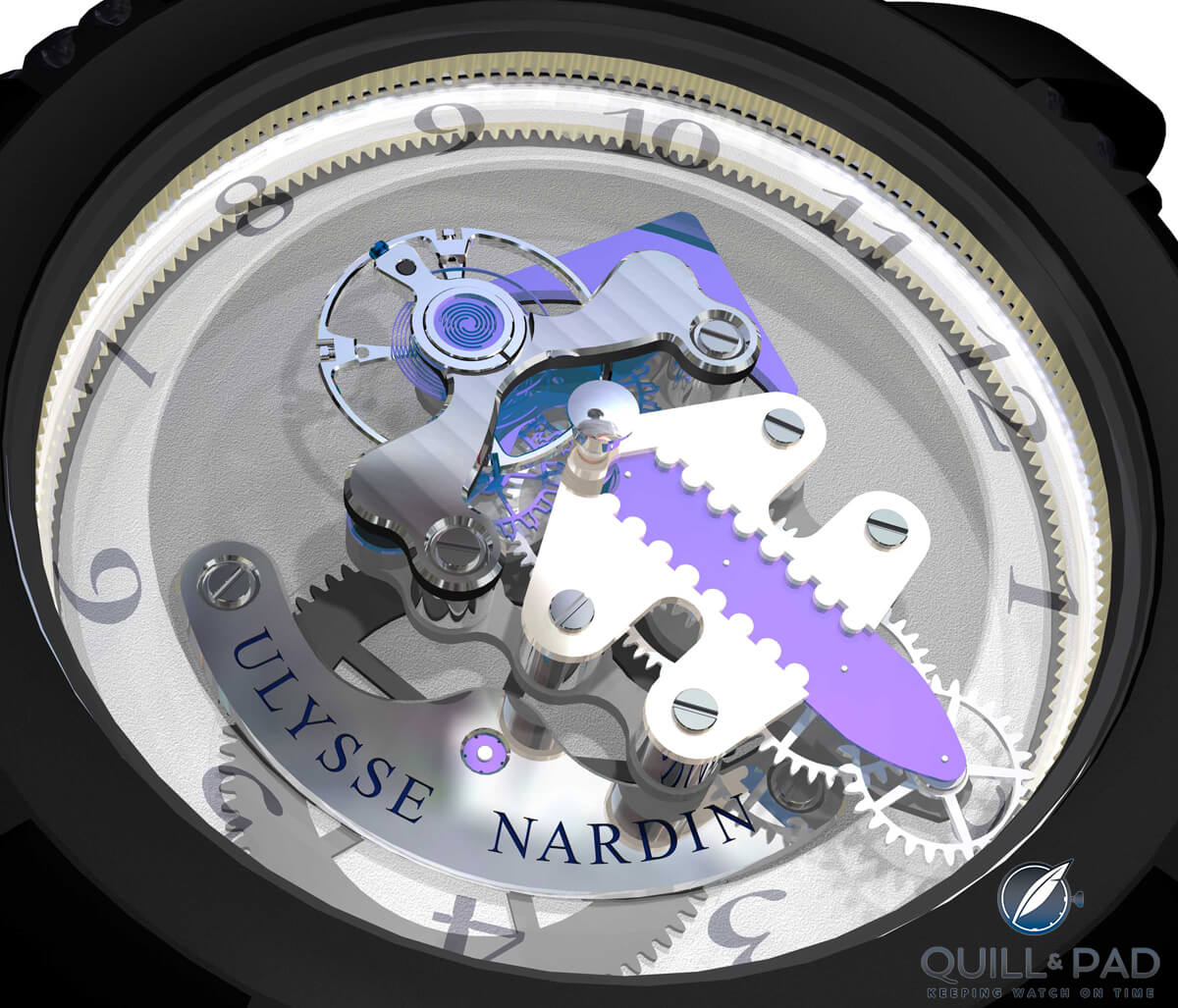
A close-up rendering of the 2007 Ulysse Nardin InnoVision
InnoVision’s escapement bridge could be manufactured in two different versions: in solid silicon or in a combination of the LIGA and DRIE technologies. The solid silicon bridge benefits highly from the precision of the production process, allowing the movement designer extreme freedom because he or she could design bearings closer to the edge of the bridge than would normally be the case since there no actual jewels were involved. The precision of their positioning was five times as accurate as that of a conventional ruby bearing.
Ulysse Nardin also introduced a reinforced silicon bridge in the movement combining LIGA with DRIE by using both Mimotec and Sigatec technology. Ulysse Nardin’s technical director Pierre Gygax explained its practicality at the time, “The bi-material bridge performs extremely well. This exclusive process is precise, with the silicon guaranteeing low friction and the LIGA nickel providing mechanical toughness.”
Gygax, who was instrumental to the brand’s technical ascension, retired in 2015. Read more about him in Ulysse Nardin’s R-Evolutionary Pierry Gygax.
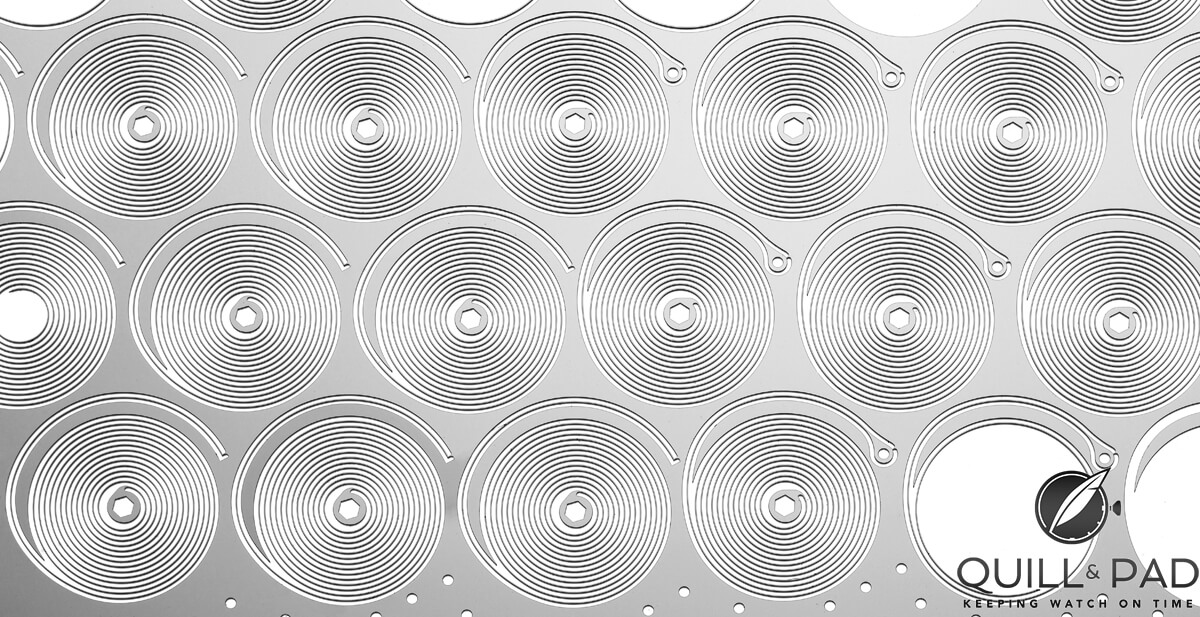
Silicon balance springs by Sigatec for Ulysse Nardin
One of silicon’s big advantages is that it is elastic. Ulysse Nardin exploited this characteristic by developing a shock protection bearing directly on the balance wheel shaft that pivots in the center of an elastic, spiral-shaped silicon disk.
In a shock situation, the disk changes shape, deforming as necessary to absorb the shock, immediately returning to its original position afterward. This same elasticity is used in the silicon balance spring located underneath the innovative shock absorber.
In 2007, as demonstrated by InnoVision, a new dimension to the DRIE process was that two-level components could be made using it. Thus, Ulysse Nardin combined the stopper and security pin of the Dual Ulysse escapement. Similar to the pallet system of the Swiss lever escapement, this version of the Dual Ulysse Escapement included a security pin perfectly aligned to the parts around it. And it is precisely this element that often caused trouble if tolerances were off.
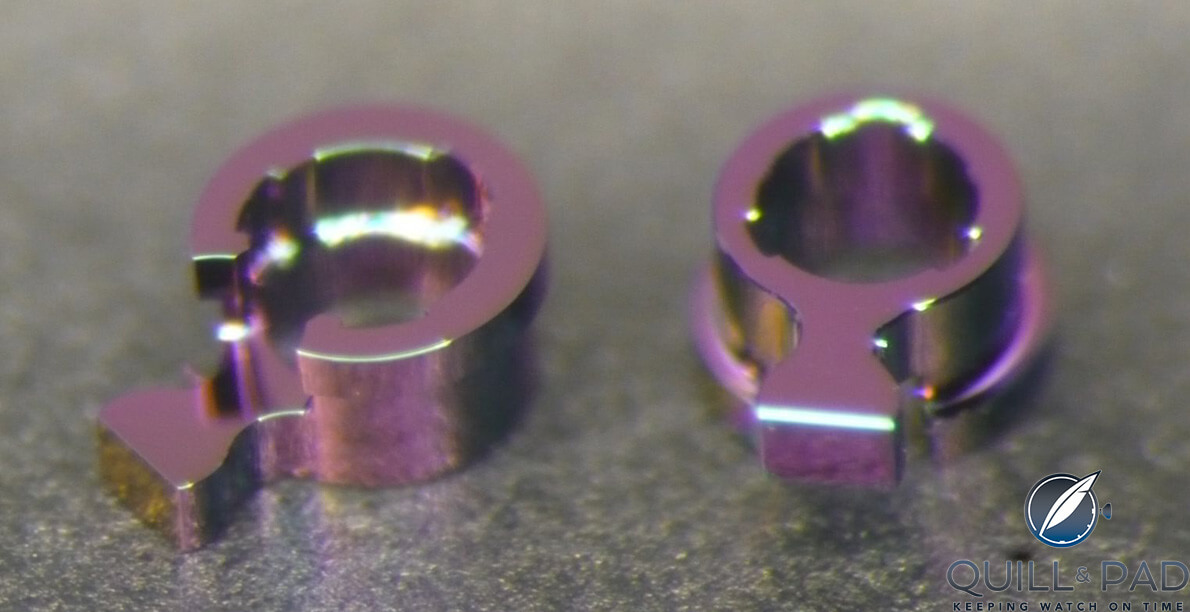
An iridescent multi-level roller and pin made at Sigatec for the Ulysse Nardin InnoVision
Thanks to the two-level etching process of DRIE that Sigatec created, these two components can be manufactured together. In other words: what used to be a subgroup is now a single component requiring neither assembly nor finishing. The same is true of the escape wheel and its pinion as well as the roller (plateau) and impulse pin, which were single components before the InnoVision.
InnoVision 2007: the 10 technical innovations
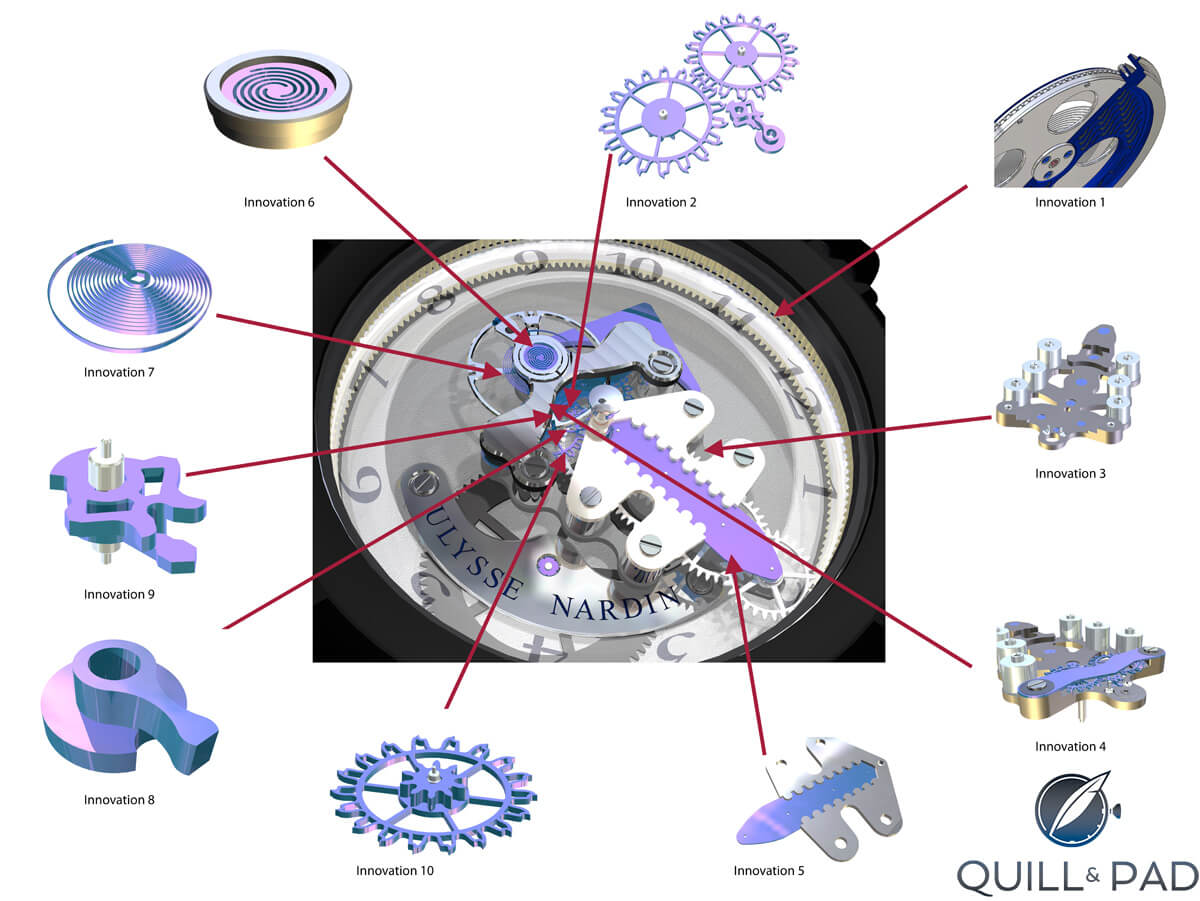
The 10 innovative elements of Ulysse Nardin’s InnoVision explained
Here is a clear visual listing of the ten technical innovations included in 2007’s InnoVision.
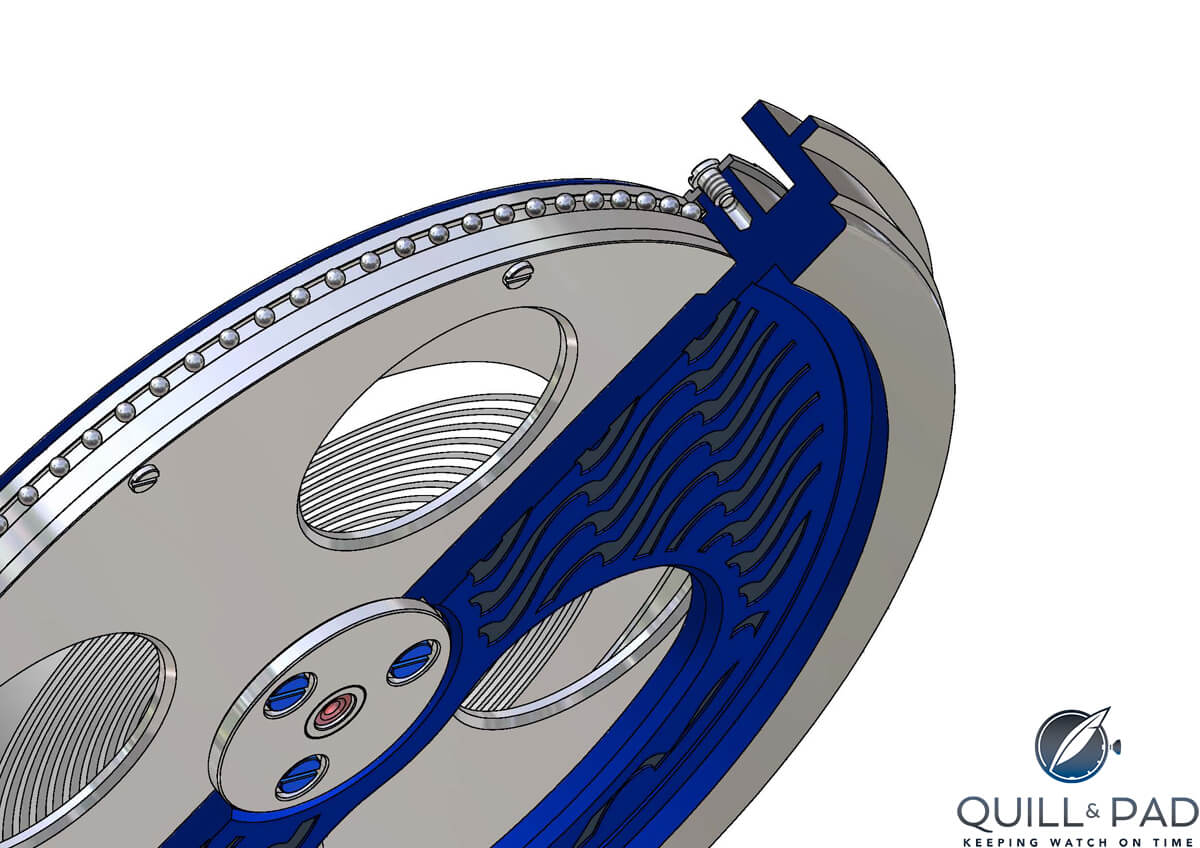
1. A non-lubricated spring barrel with 96 ball bearings in silicon
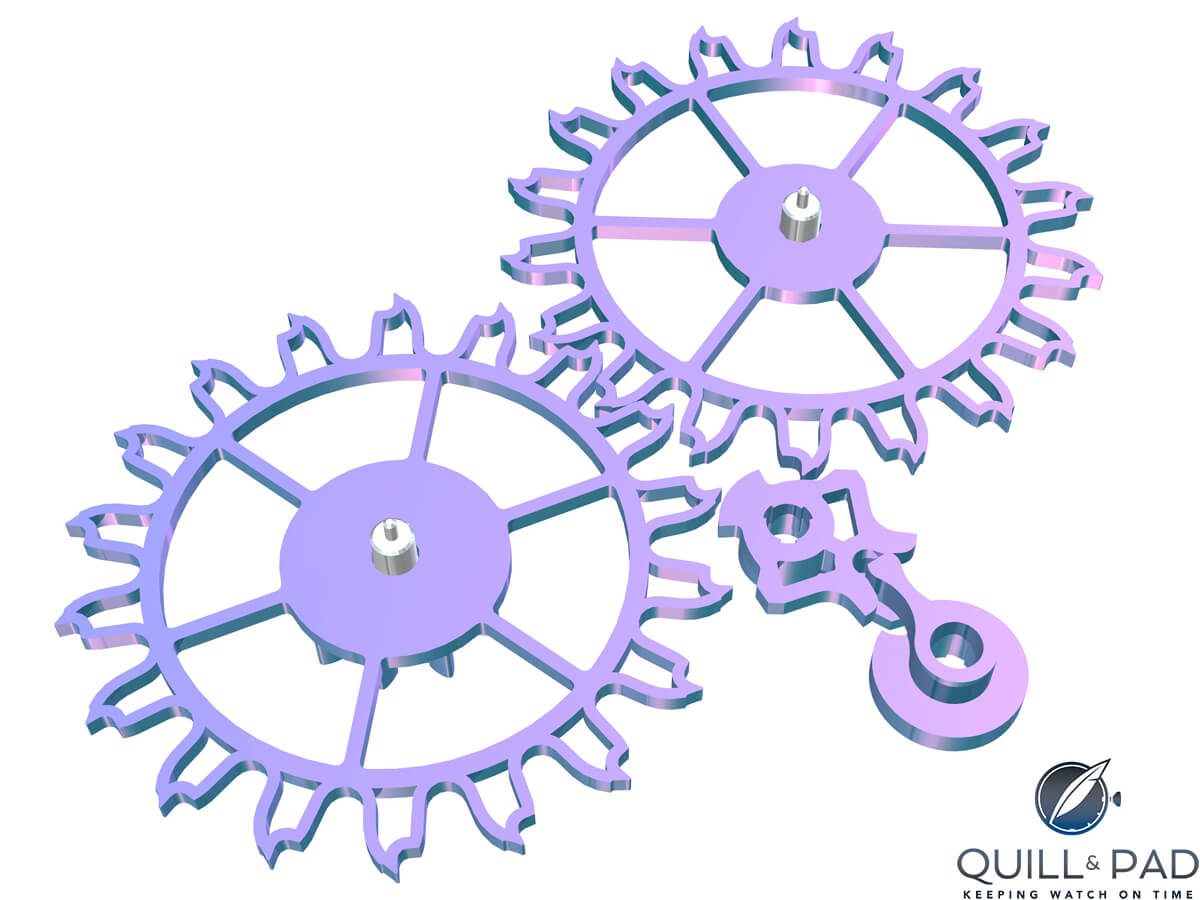
2. The Dual Ulysse Escapement, manufactured completely in silicon, needs no lubrication.

3. The brass base plate is fitted with lubrication-free silicon bearings, meaning there is no need for oil recesses.
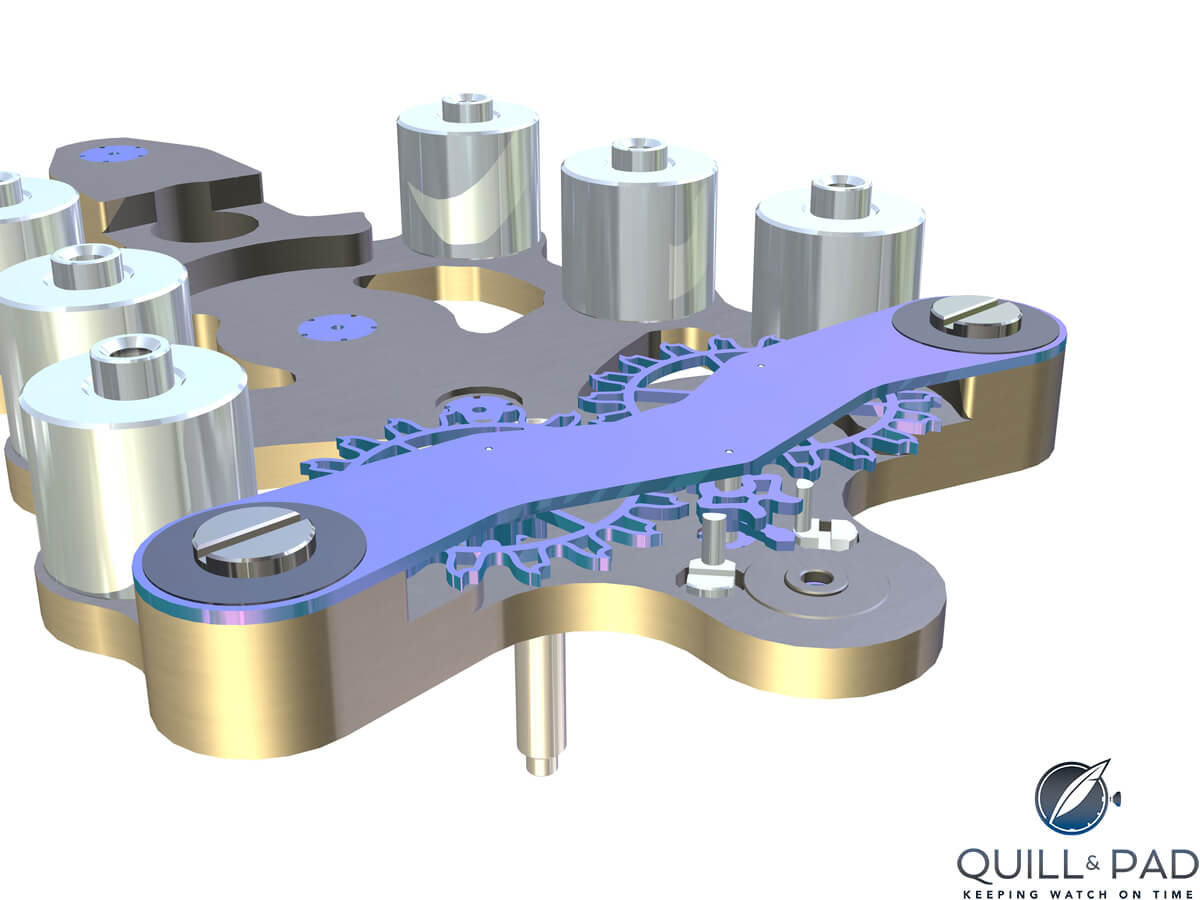
4. The movement designer has more freedom in designing a solid silicon escapement bridge – whose design is of course proprietary to Ulysse Nardin – since taking jewel position into account is no longer necessary.
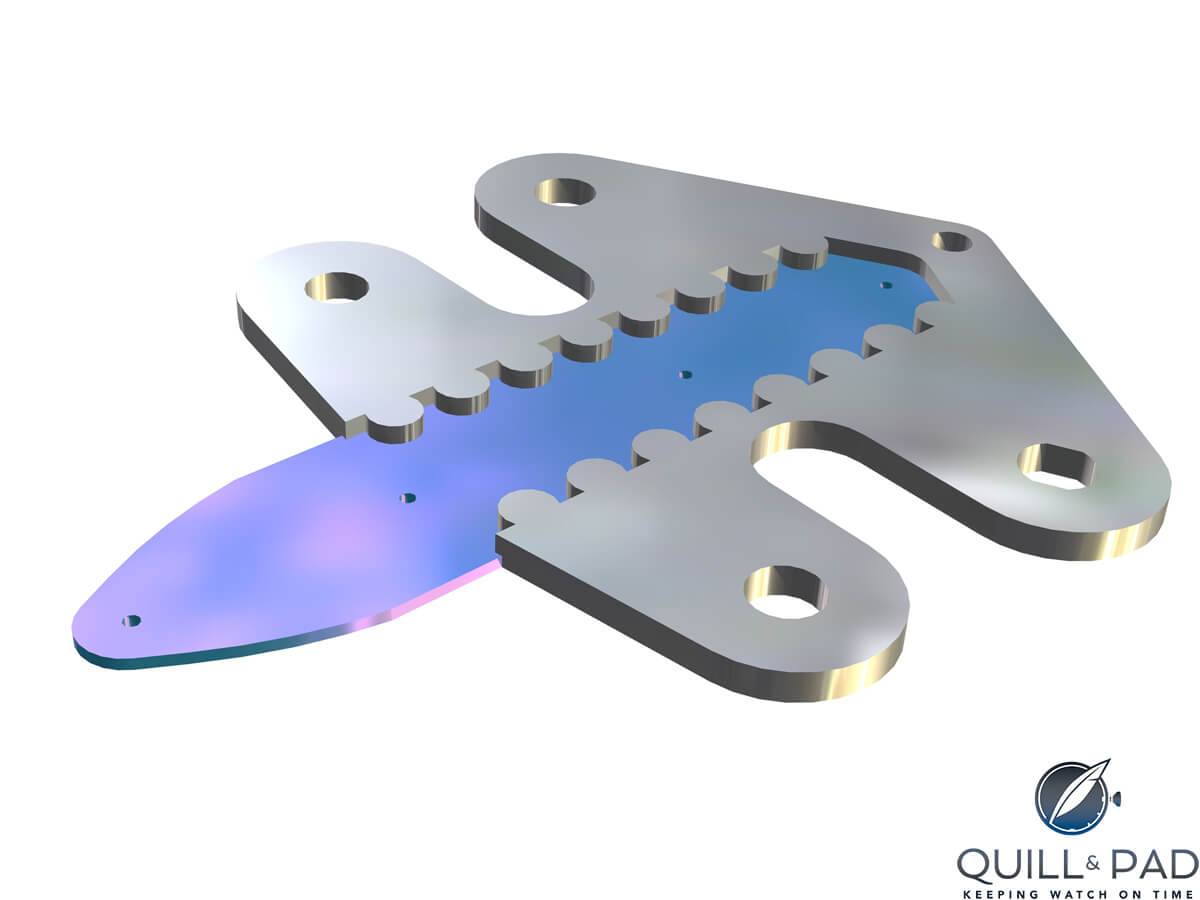
5. Thanks to combined use of LIGA and DRIE silicon, Sigatec, Mimotec, and Ulysse Nardin were able to produce a two-material bridge. The advantage of this is the ability to take advantage of the best elements of both materials resulting in low friction and mechanical grit.
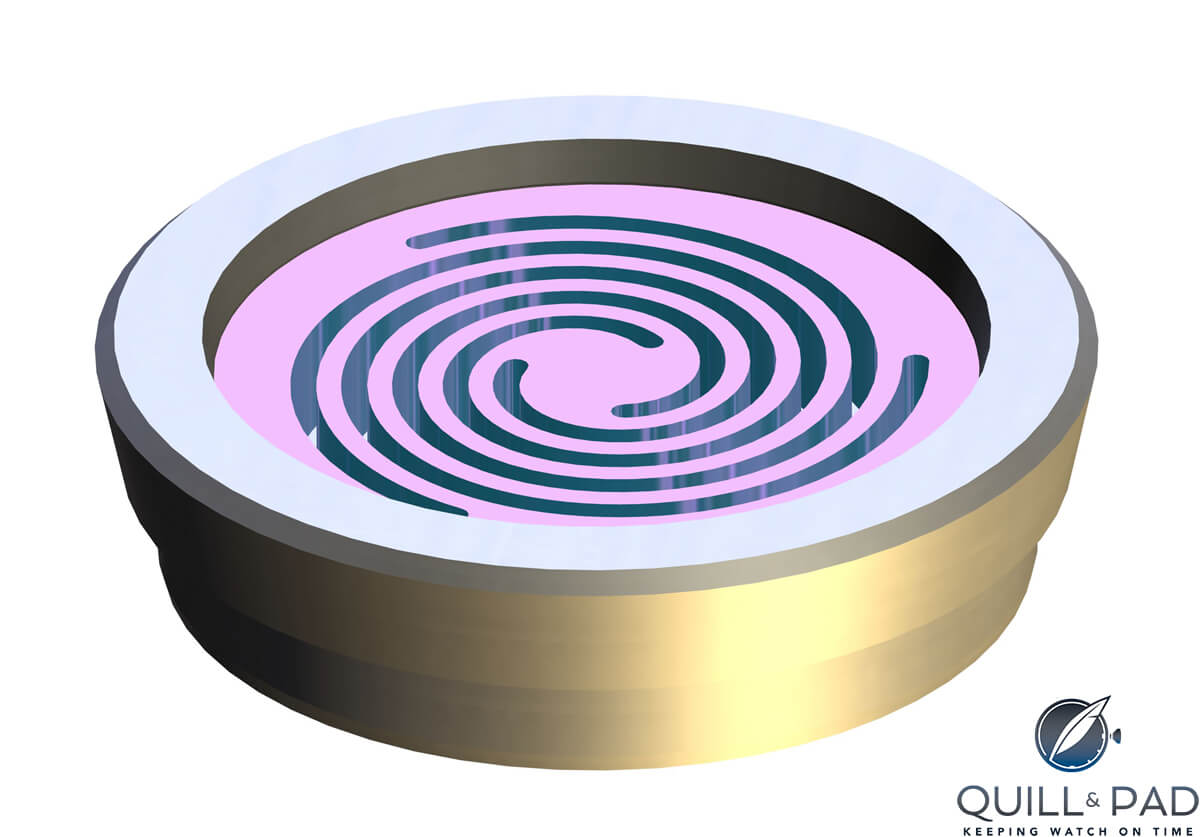
6. The elasticity of silicon allows for a shock absorber bearing integrated into the balance wheel shaft, which pivots in the middle of a silicon disk. The elasticity of the disk allows the necessary deformation when shocks arise, after which it returns to its original shape immediately.
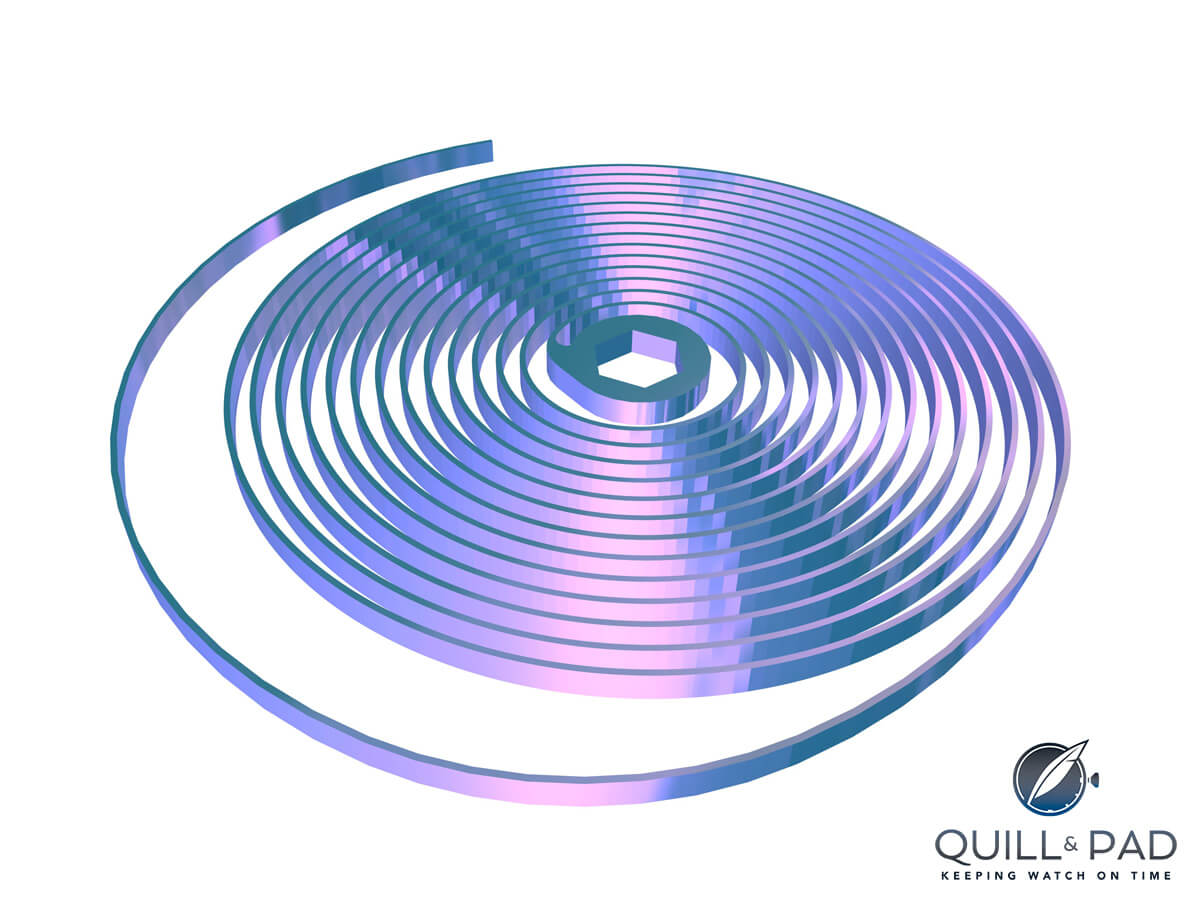
7. Ulysse Nardin’s iridescent silicon balance spring.
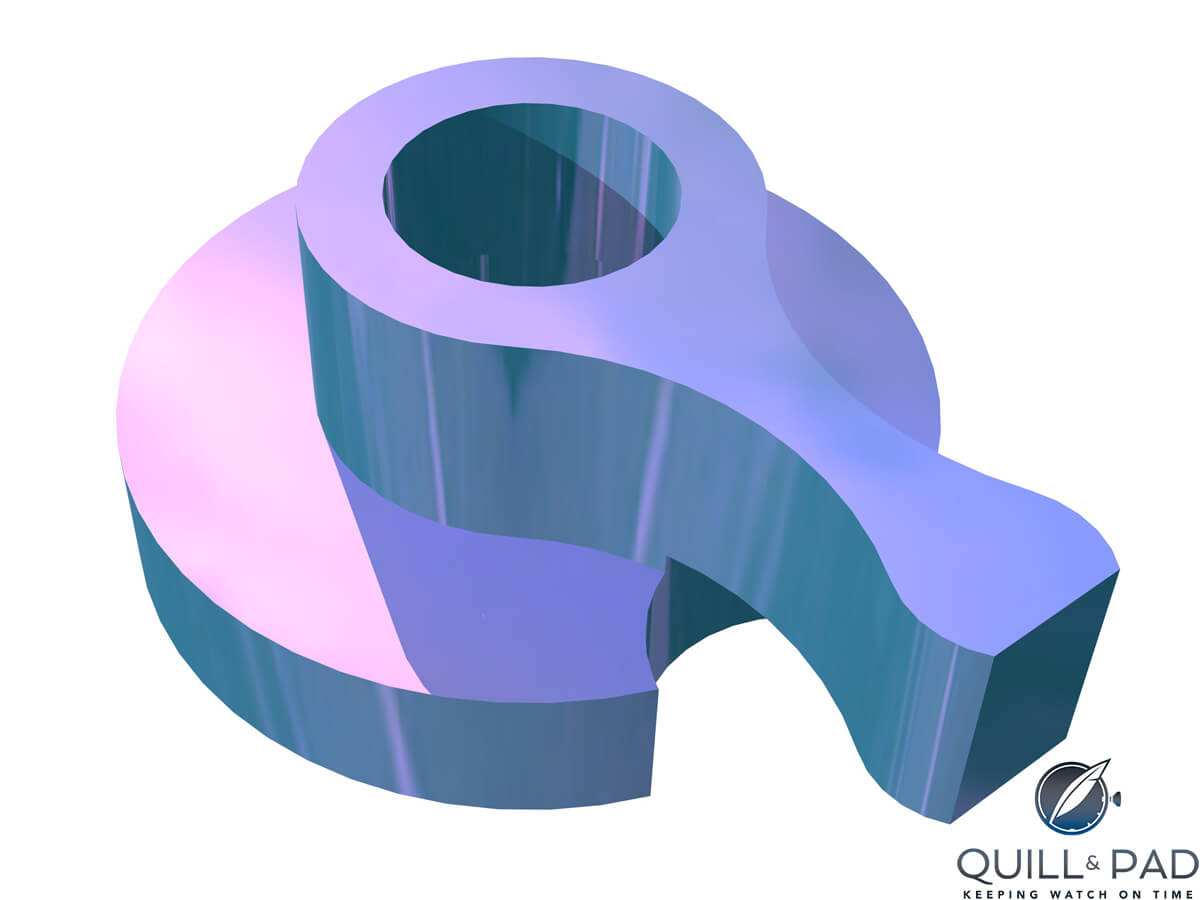
8. A truly innovative side effect of the Sigatec DRIE silicon process is that two-level parts can be manufactured. This roller (plateau) and impulse pin combination is a prime example.
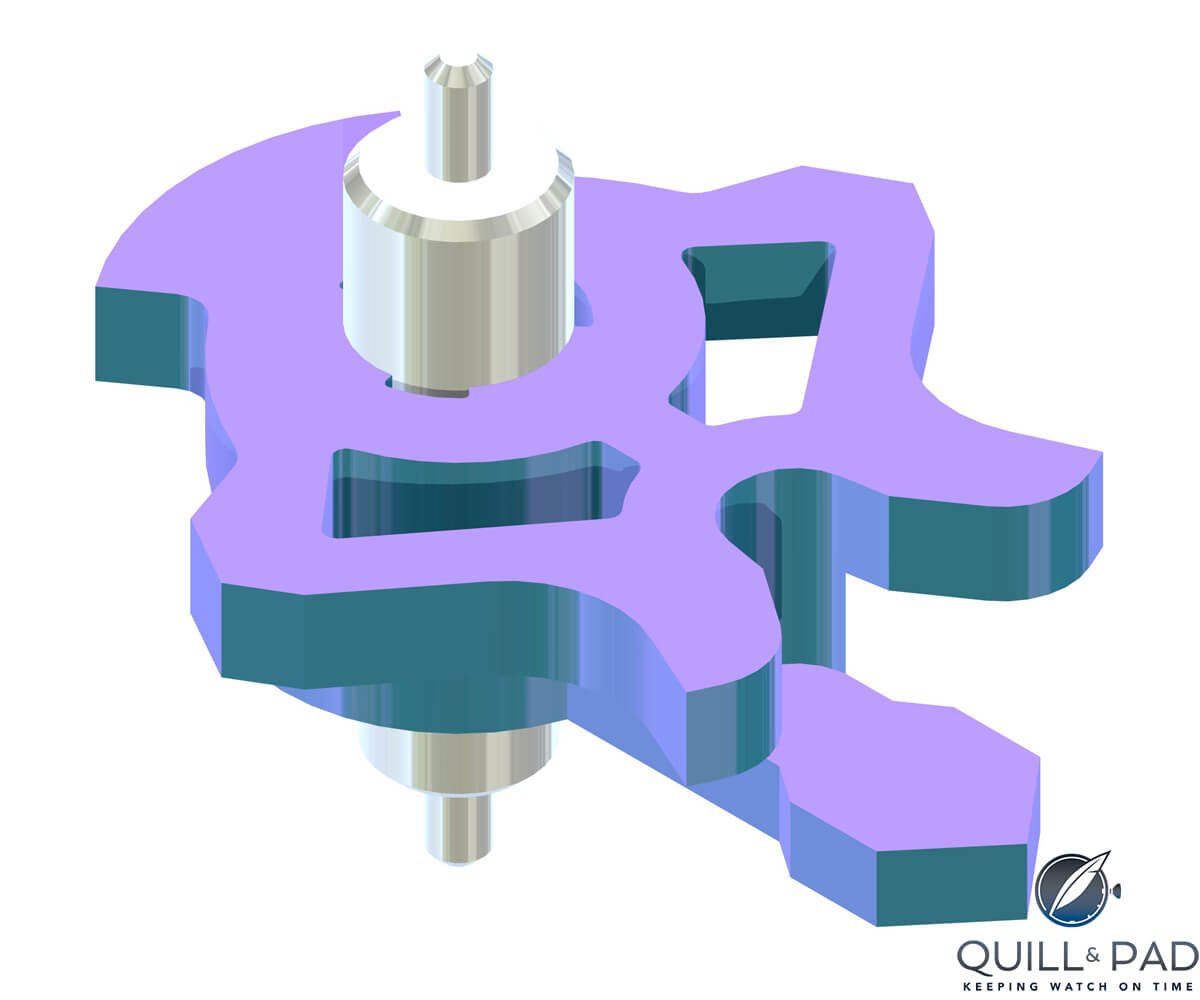
9. The stopper and security pin of the Dual Ulysse Escapement can be manufactured as one unit, requiring no assembly and no finishing.
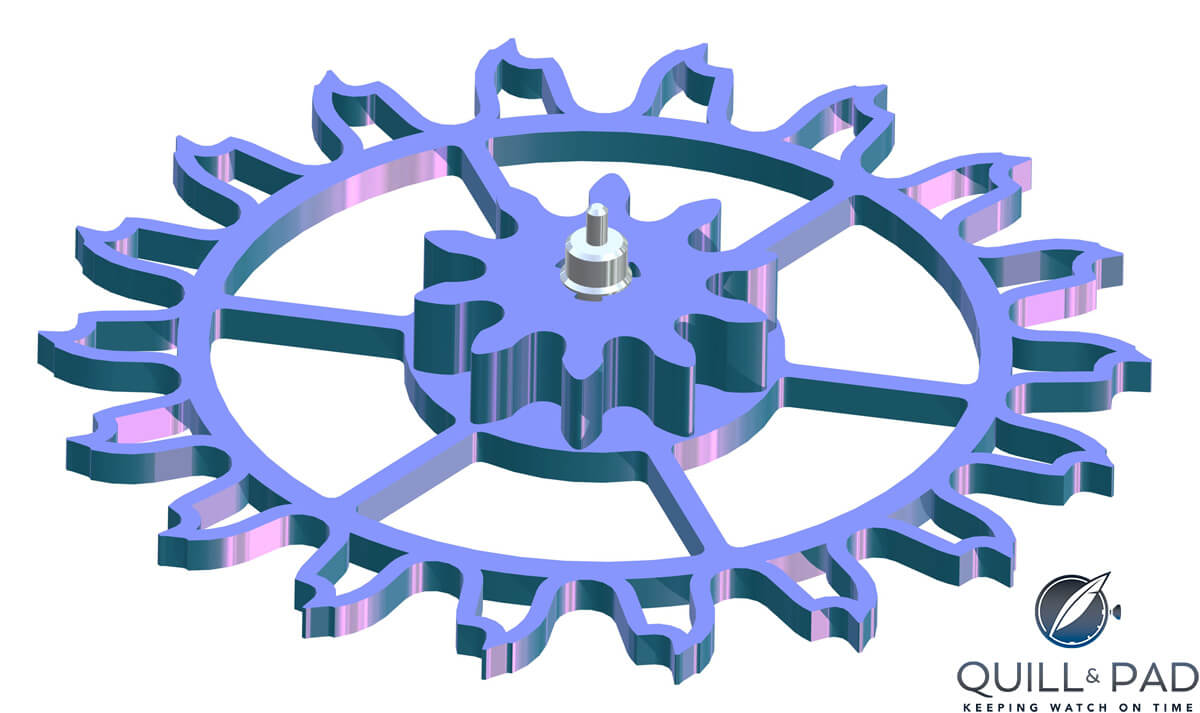
10. The escape wheel and pinion as a unit thanks to the dual-level DRIE process. It too requires no assembly and no finishing.
Ulysse Nardin’s progressive direction was spearheaded by former CEO and owner, Rolf Schnyder, who passed away in 2011. It was always his vision to ensure that his brand’s technical future was based on sustainable technologies and the best partnerships. Therefore, it is only fitting to end this look back on the InnoVision with something he said to me in 2007.
“Without a doubt, our industry will continue to progress, and probably in very different directions, but it seems important to us to include new materials and technologies in our concept that promise improvements or advantages,” he explained the profound justification of these processes and materials.
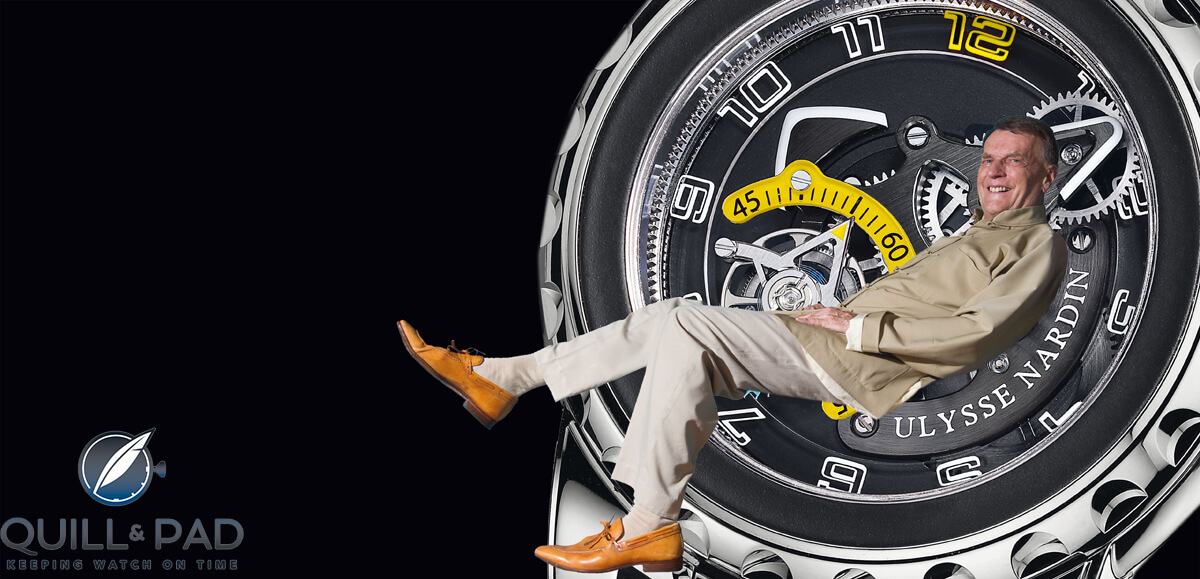
The Ulysse Nardin Freak version created in honor of deceased CEO Rolf Schnyder on the occasion of his 75th birthday in 2010
His goal – and that of Pierre Gygax and even Ludwig Oechslin, another important collaborator in the Ulysse Nardin universe – was to make lubrication a thing of the past and production more precise and simple.
“We are of the opinion that mechanical watchmaking is a living thing,” Schnyder continued. “Perhaps Ulysse Nardin, in some modest way, has contributed to a new collective imagination to which there is no boundary.”
Trackbacks & Pingbacks
-
[…] Silicon hairsprings have been around a lot longer than 2014: Ulysse Nardin was the first to introduce this amazing feat more than ten years before (see Looking Back On 10 Years Of Ulysse Nardin’s Pioneering InnoVision Technology). […]
-
[…] in 2017 came the InnoVision 2, the successor to the feature-packed InnoVision 1, a watch that pulled together just about everything that Ulysse Nardin’s research-and-development […]
-
[…] For the Lab-ID Luminor 1950 Carbotech 3 Days, a high percentage of carbon was added to the ceramic composite, which turned it into a carbide, making for an extremely low-friction material. Since this substance makes up the movement’s plates and bridges, the pivot jewels can be eliminated and the holes resized to accept wheel pivots. This is something we’ve already seen a version of in Ulysse Nardin’s InnoVision I. […]
-
[…] In 2007 Ulysse Nardin introduced a watch whose sole purpose was to be a vehicle for innovation (see Looking Back On 10 Years Of Ulysse Nardin’s Pioneering InnoVision Technology). […]
-
[…] 2 is where science meets horology as it contains ten new innovations for watchmaking. The previous InnoVision 1 did the same and resulted in a majority of those innovations being incorporated into regular […]
-
[…] For details on the specific ten innovations of InnoVision 1 and full explanations of the LIGA and DRIE technologies, see Looking Back On 10 Years Of Ulysse Nardin’s Pioneering InnoVision Technology. […]
Leave a Reply
Want to join the discussion?Feel free to contribute!
Thank you for this well researched article.
A great summary of UN’s innovations.
I’ve often felt UN doesn’t get enough credit in starting the “silicon revolution” in the watchmaking industry.
Thank you so much for reading and taking the time to respond. I’m glad you enjoyed it.