Diving Deep Into The Technology Of The Ulysse Nardin InnoVision 2
Tradition versus innovation – that is the main battle waged daily across the watchmaking industry.
Every proponent of tradition has numerous valid points justifying an attempt to retain and protect the status quo above all else. Tradition is where watchmaking came from: it is its past and its home.
Observing tradition shows respect to the great minds and incredible artisans that came before; tradition can’t and shouldn’t be ignored, lest we lose the knowledge that was gained through hard work and inspiration.
I don’t know anyone in the industry that doesn’t outwardly respect tradition.
Yet there are many who view innovation as the best way to respect tradition, since it was innovation in pursuit of excellence and accuracy in watchmaking that paved the way for much of modern science and engineering.
The need for accurate timekeeping devices was and remains crucial to the continued progress of scientific discovery. And with the development of better and more accurate timepieces came new materials, tools, and processes to enable the formation of some of the most incredible mechanical creations that humans have ever made.
Obviously, I lean more toward the latter category in that innovation should be encouraged in all aspects of watchmaking development. That is why some of my favorite pieces are what might be called the “crazy” avant-garde: the watches that break many, if not most, of the conventions of watchmaking in search of something new, interesting, and entirely exploratory.
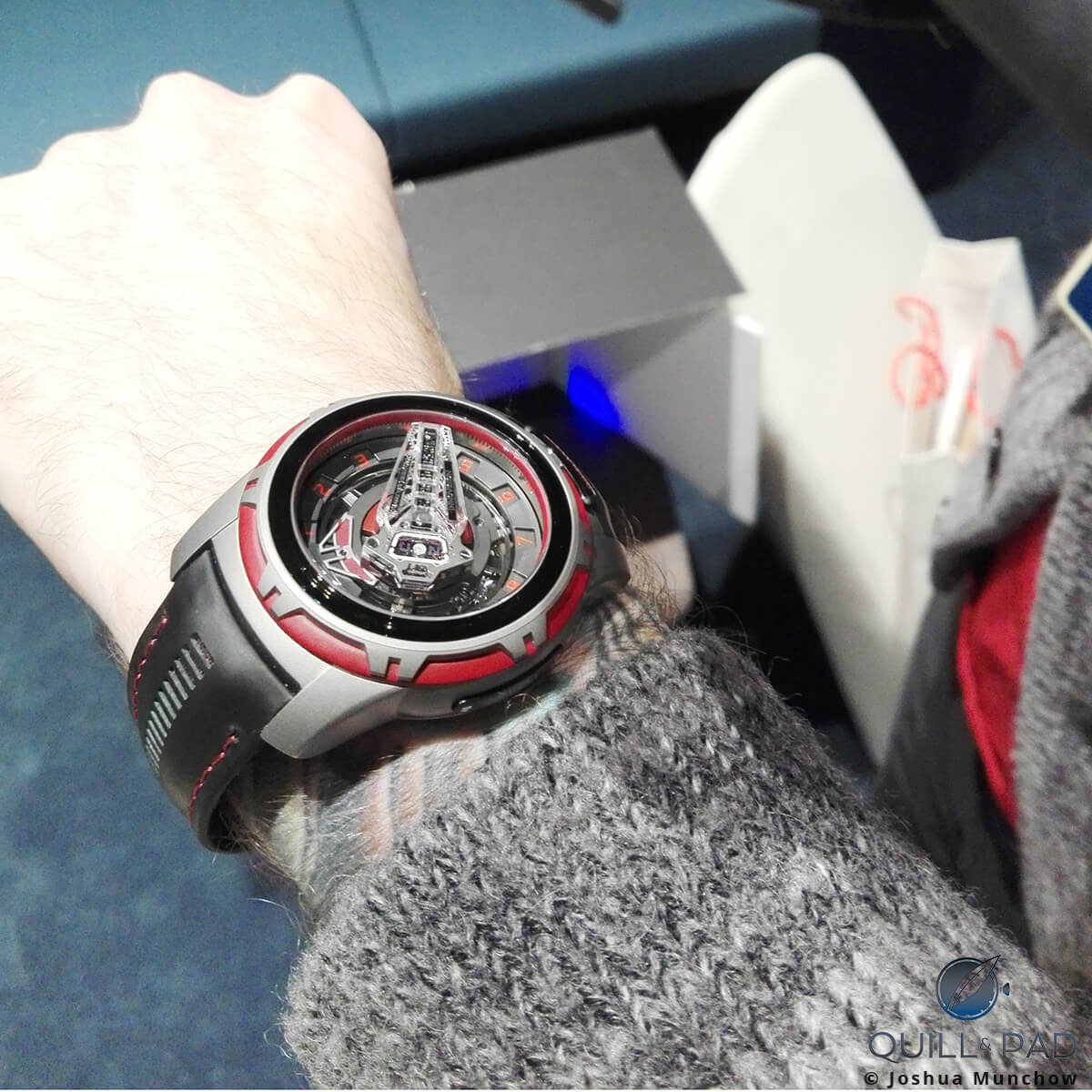
The Ulysse Nardin InnoVision 2 concept watch on the wrist
The category is filled with intensely complicated and scientifically advanced creations, and chief among them is the new Ulysse Nardin InnoVision 2.
A tradition of innovation
Ulysse Nardin has been around a very long time and has a tradition of innovation dating back decades. In recent years, engineers and watchmakers at Ulysse Nardin have gone to great lengths to push the boundaries of avant-garde watchmaking to create mechanical marvels that hurl the entire industry forward.
Ulysse Nardin was the first to use silicon in a wristwatch, which, along with a surprising mechanical design, ushered the entire industry into the age of hyper watches.
In 2007 Ulysse Nardin introduced a watch whose sole purpose was to be a vehicle for innovation (see Looking Back On 10 Years Of Ulysse Nardin’s Pioneering InnoVision Technology).
The InnoVision featured ten innovations never before seen in watchmaking that set Ulysse Nardin to drive down a path of continued exploration. Many of those innovations have since found their way into production models, proving the effort was directly tied to making better watches for the customer.

Ulysse Nardin InnovVsion 2
A decade later, in 2017, we finally see InnoVision 2, filled with ten more innovations that have a good chance of finding their way into future Ulysse Nardin models.
I could wax poetically about how amazing and interesting the InnoVision 2 is, however I think a detailed breakdown of just what exactly is inside the InnoVision 2, how it is all made, and what it might mean for the future of Ulysse Nardin is better.
So let’s get into it.
It begins with silicon
Out of the ten innovations in the InnoVision 2, four are specifically related to silicon and its use. This should come as no surprise given the history Ulysse Nardin has with the material.
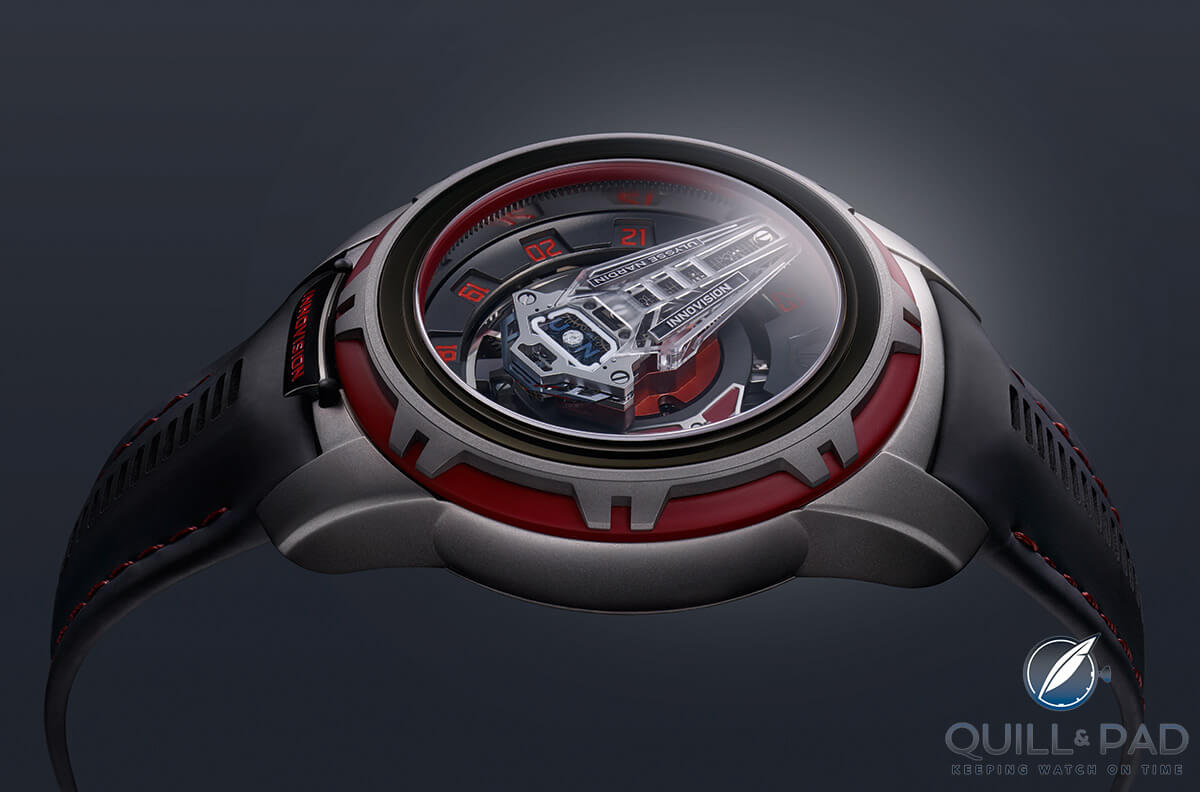
Ulysse Nardin InnoVision 2
Still, it is awesome to see that Ulysse Nardin isn’t resting on its laurels and continues to explore the boundaries of this modern material. In InnoVision 2, the use of silicon ranges from the bridges and balance wheel to the escapement, highlighting the variety of ways the material is changing how things can be manufactured.
Silicon bridge coated with sapphire
The first innovation relates to coatings on silicon, namely sapphire. InnoVision 2 is built in the Freak format with a minute hand assembly housing most of the gear train. Therefore, the parts used in the assembly need to be as light as possible.
The going train wheels all pivot in a line underneath a single silicon bridge to maintain lightness and reduce the part count and complexity. This bridge presented a perfect opportunity to experiment with coatings as a way to eliminate the need for jewels.
Using a process known as Chemical Vapor Deposition (CVD), synthetic sapphire (polycrystalline Al2O3) is added to a gas and injected into a chamber containing the part to be coated. In this case the silicon bridge is heated to a high temperature (somewhere between 300 and 1,000 degrees Celsius), which allows the surface to chemically react with the gas/sapphire mix to form a thin film.
The process can take a few hours and achieves a film thickness between 0.5 and 2.0 microns.
The main advantage of this process is the ability to create jewel-free bridges in any shape needed. This will allow greater design freedom in the future for unique and highly complicated geometry that would normally require pressed in jewels, but can now be coated and act as a bridge and jewel in one.
As a bonus, the silicon component is harder and more dimensionally stable as a result of the coating.
The process was developed and patented in collaboration with Sigatec and the École Polytechnique Fédérale de Lausanne, echoing how Ulysse Nardin, Sigatec, and Diamaze Microparts SA/GfD developed a way to coat silicon with nanocrystalline diamond prior to 2007.
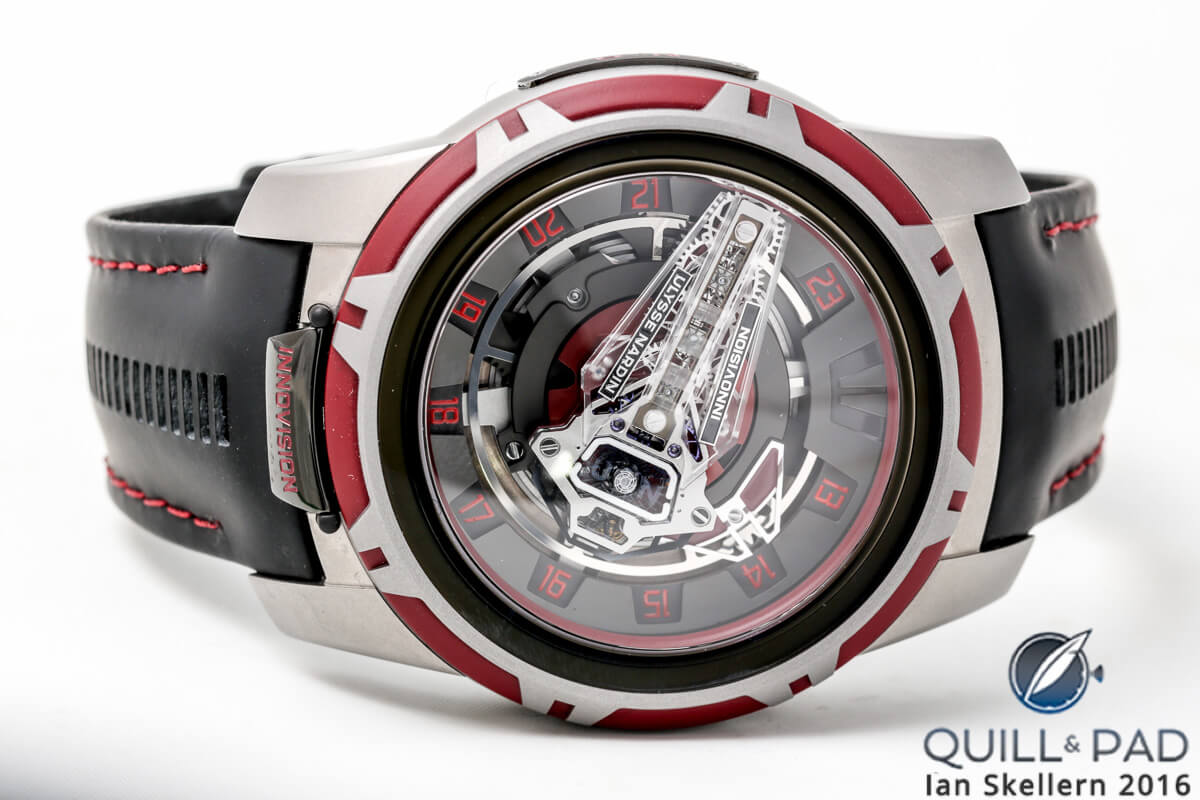
Ulysse Nardin InnoVision 2
Direct silicon bonding
The next innovation relates to the ability to directly bond two different silicon components together to create one nearly homogeneous three-dimensional shape. Normally, silicon parts comprise single layers of silicon with only a profile defined. More advanced multi-level parts are possible, like those seen in the first InnoVision, but these are harder to produce so the majority of silicon components tend to be flat.
Direct silicon bonding fills the gap between the two.
Direct silicon bonding was first successfully demonstrated around 1986 and has been in use for larger silicon wafer assemblies in other industries for years. Ulysse Nardin worked to develop the process to bond single layers of silicon together to create multi-level parts at a much smaller scale than ever before.
The process is utilized in the InnoVision 2 in the escapement: a very small silicon plate is added on top of the pallet lever in the Dual Constant Escapement (which I’ll discuss next). The small plate is much smaller than the overall escapement part, so direct silicon bonding made practical sense when compared to a multi-level DRIE (deep reactive ion etching) part.
The bonding process is technically quite complicated, though rather straightforward.
The two silicon components must be clean and free of oxides. Based on the chemical structure of the silicon, the hydrophobic surface attracts a layer of hydrogen atoms. The two components are compressed together and oxygen is added.
The temperature is then elevated to the annealing level above 1,000 degrees Celsius, and as the temperature increases the hydrogen first creates bonds with the silicon before being desorbed (leaving the surface) and allowing silicon oxide bonds to form until finally silicon atoms also bond directly.
This creates stable silicon oxide joints and parts that are fundamentally a single piece of silicon. The process allows much more complicated multi-layer parts to be created faster and still be as accurate as single-layer processes.
Dual Constant Escapement
The resulting multi-layer part is the heart of InnoVision 2: the Dual Constant Escapement.
This part is basically a conglomeration of the Dual Ulysse Escapement, the Ulysse Anchor Escapement (see Anchors Away: Ulysse Nardin Makes The Anchor Escapement Viable For The Wristwatch), and a constant force escapement all rolled into one new escapement.
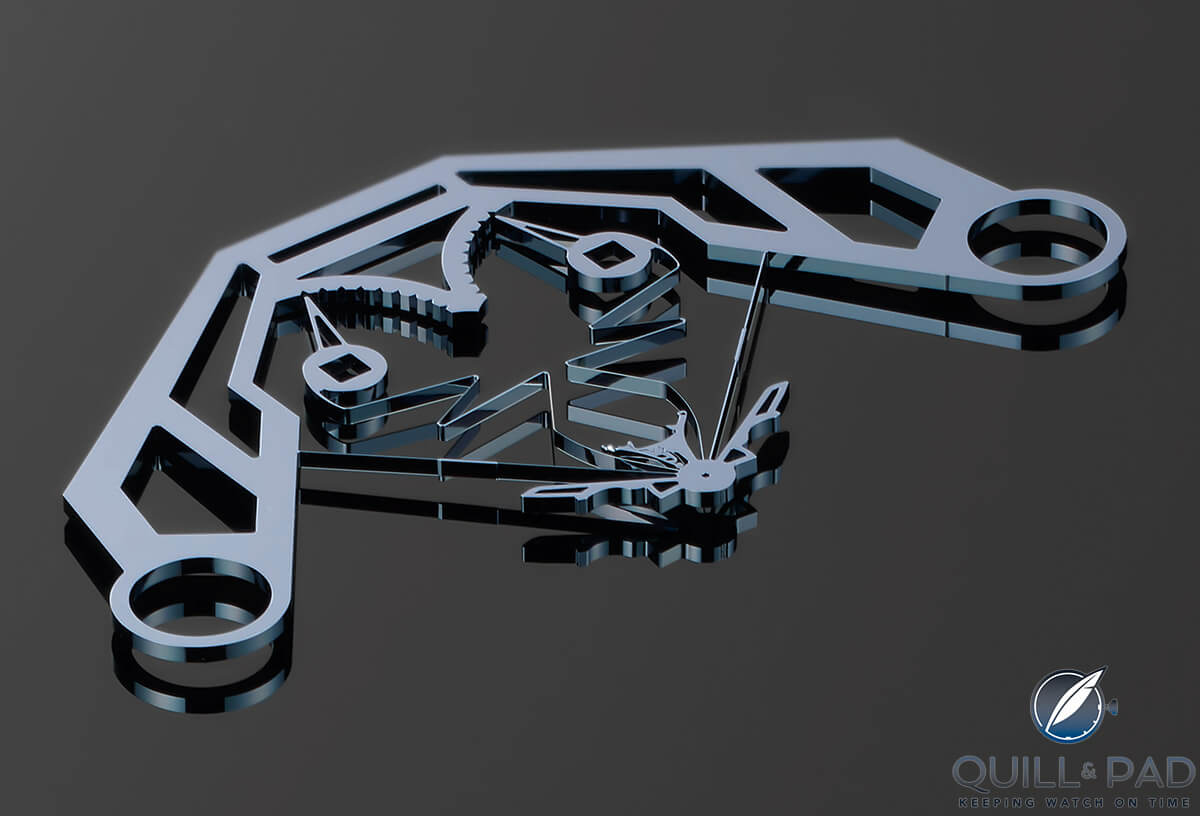
Ulysse Nardin InnoVision 2 Dual Constant Escapement
It starts with the Anchor Escapement and the idea that the floating pallet, which is suspended by extremely thin silicon blades, could be pre-loaded to apply a force when the pallet changes position. This is nearly the same thinking that saw the invention of the Girard-Perregaux Constant Escapement.
However, unlike that escapement, the Dual Constant Escapement eliminates levers, physical pivots, and about half a dozen components in favor of a virtual pivot as part of a single component. It also adds the ability to fine tune the load on each of the blades so that the force from the buckling silicon is consistent for each direction of impulse on the balance wheel.
The pallet that releases both of the interlocked escape wheels has the small plate attached as I mentioned earlier, which locks the escapement and keeps it from changing positions during each half-rotation of the balance wheel.
When the balance swings back through to unlock the escapement, the pallet and blades absorb around 150 nanojoules from the gear train, but only release 60 nanojoules into the balance wheel. This maintains consistent amplitude of the balance regardless of the power left in the mainspring.
As long as there is enough energy to reset the pallet from one stable state to its opposite, the watch will continue to keep consistent and accurate time.
Even more, since the entire escapement is made from silicon, and some pivots have been eliminated, the need for lubrication has disappeared for certain parts; wear is greatly reduced throughout the mechanism.
Overall, the Dual Constant Escapement showcases a direction for mechanical horology that could very well become the norm for progressive brands.
Silicon balance wheel with stabilizing micro paddles and variable inertia gold mass
Speaking of progressive brands, many companies have begun to utilize silicon hairsprings in mechanical movements due to their non-magnetic properties and ability to be made in a precisely calculated configuration.
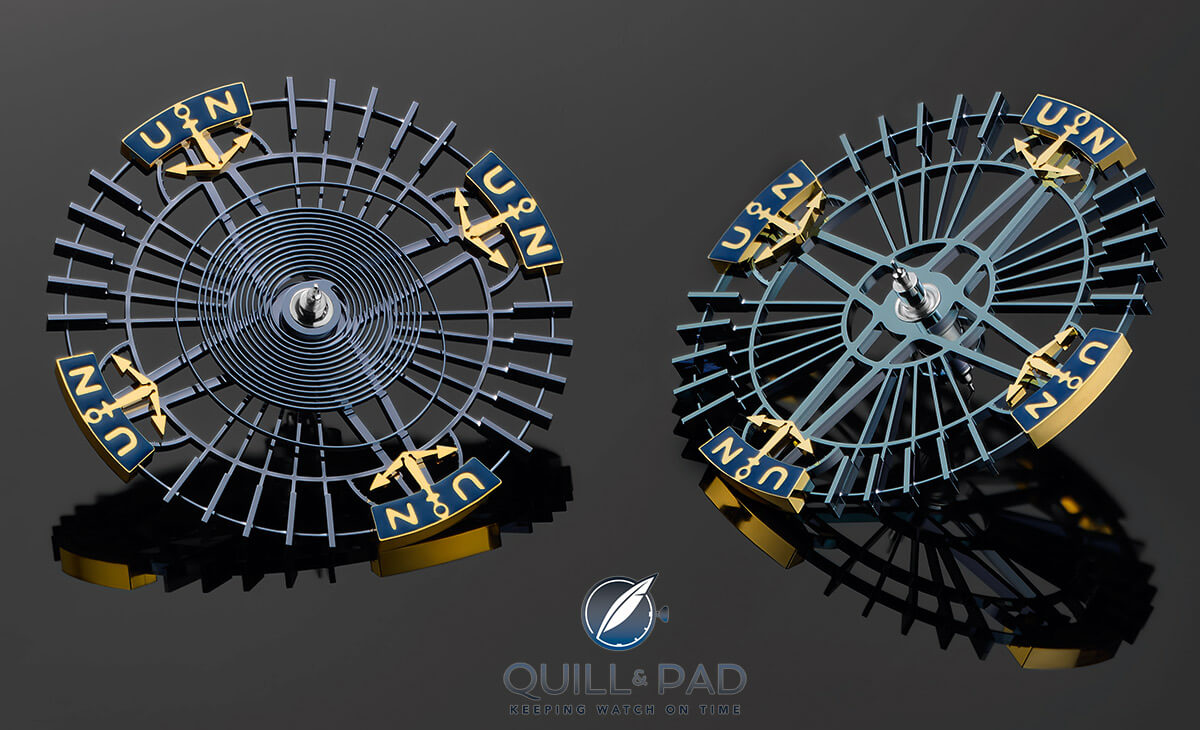
Ulysse Nardin InnoVision 2 silicon balance wheels with (left) and without a mounted silicon balance spring
But to take it one step further, Ulysse Nardin has created the entire balance wheel as well as the spring out of silicon, and in a very new form: the silicon balance wheel looks like a river boat paddle wheel – and for a uniquely good reason.
Silicon is actually a pretty perfect material for a balance wheel because the material is nearly perfectly homogeneous.
This means that the balance wheel will have its mass distributed very evenly and won’t have many density/mass irregularities that would make poising more difficult. It is also very light, 3.6 times lighter than the industry standard Glucydur, which is a beryllium bronze.
A perfect balance wheel would have zero weight at its center and all of its weight around the perimeter for a maximum moment of inertia. So making a balance wheel out of ultra-light silicon allows the central mass to be kept very low with the mass added only at the perimeter.
The InnoVision’s silicon balance wheel has four gold mass elements that are adjustable along a line extending out from the pivot; these comprise a majority of the mass of the balance assembly.
The silicon balance wheel itself only weighs seven milligrams, about the same as a dozen grains of sugar. The high moment of inertia does have its downsides, but that is compensated for by those paddles is a very clever way.
The balance wheel always receives a constant force, but depending on position and the resulting friction from the pivots, the amplitude can still vary.
The paddles actually create small air turbulences around the balance during the higher amplitude moments when the balance is in a flat position that act as a brake to keep the amplitudes more consistent.
The effect is small but important in maintaining accuracy and consistency as a primary goal. A smooth balance would have benefits of reduced energy usage, but would in fact create more inconsistency due to variable amplitudes.
The paddles end up acting as a passive check valve for an overrunning balance wheel.
Glass like you have never seen it before
The next set of innovations surround the use of glass for critical components, which are made possible by a very interesting technology called FEMTOPrint. Before discussing the innovations in the InnoVision 2, a breakdown of what exactly FEMTOPrint is will provide a basis for understanding just how spectacular the results are.
Firstly, FEMTOPrint is a misnomer. The process does not involve printing in any way familiar to the additive manufacturing camp, but instead uses some concepts from 3D printing to create amazingly detailed glass structures (see Focus On Technology: 3D Printing, What Is It Really?).
FEMTOPrint is a subtractive process in which a solid block of glass or other transparent material is prepared with a femtosecond laser before being etched to create three-dimensional structures.
In the case of the Ulysse Nardin innovations, the glass material is fused quartz, an extremely pure amorphous silica with excellent mechanical, thermal, and optical properties.
The creation of fused quartz begins with high-purity silica sand, which is – simply put – quartz crystals. The quartz itself consists of only silicon and oxygen, meaning that fused quartz is technically another form of silicon.
Ulysse Nardin really puts that stuff everywhere!
The pure silica sand is electrically heated to create an amorphous solid that is brilliantly transparent and has ultra-high purity.
The FEMTOPrint process begins with a block of this material that is exposed and then etched.
The process sees a femtosecond laser (meaning ultra-short pulse 1/1,000,000,000,000,000 of a second) directed and focused through a lens on a specific point in space and pulsed, changing the properties of that specific point. This takes place millions of times to slowly remove all the material that is not required for the final part.
The region modified by the laser can be down to 600 nanometers in all directions, or about one micron square. This means that the effective resolution can be in the two-to-five micron range for an actual feature on a part, which is the same as the level of tolerance on some of the more precise components in the watch industry.
The fused quartz block is then placed into an acid etching solution and the laser-affected region etched away, leaving the solid fused quartz component perfectly formed.
The surface is very fine, and can even be less than 100 nanometers for a mirror-smooth surface.
The FEMTOPrint process allows the creation of nearly any geometry that can be imagined at sizes hitherto unimaginable in traditional watchmaking. This has allowed Ulysse Nardin to look at ideas that may have been impossible in the past.
There are three innovations that Ulysse Nardin has developed that utilize FEMTOPrint technology to create standout components taking the InnoVision 2 well into the future of watchmaking.
Three-dimensional glass minute hand
The largest component made using the FEMTOPrint process is the very obvious minute hand made from a solid block of fused quartz.
The hand is sort of shaped like a fuselage that surrounds the going train and the previously mentioned silicon bridge. The large minute hand is supported by a metal plate to protect it from shocks with text blocks built right into the sides.
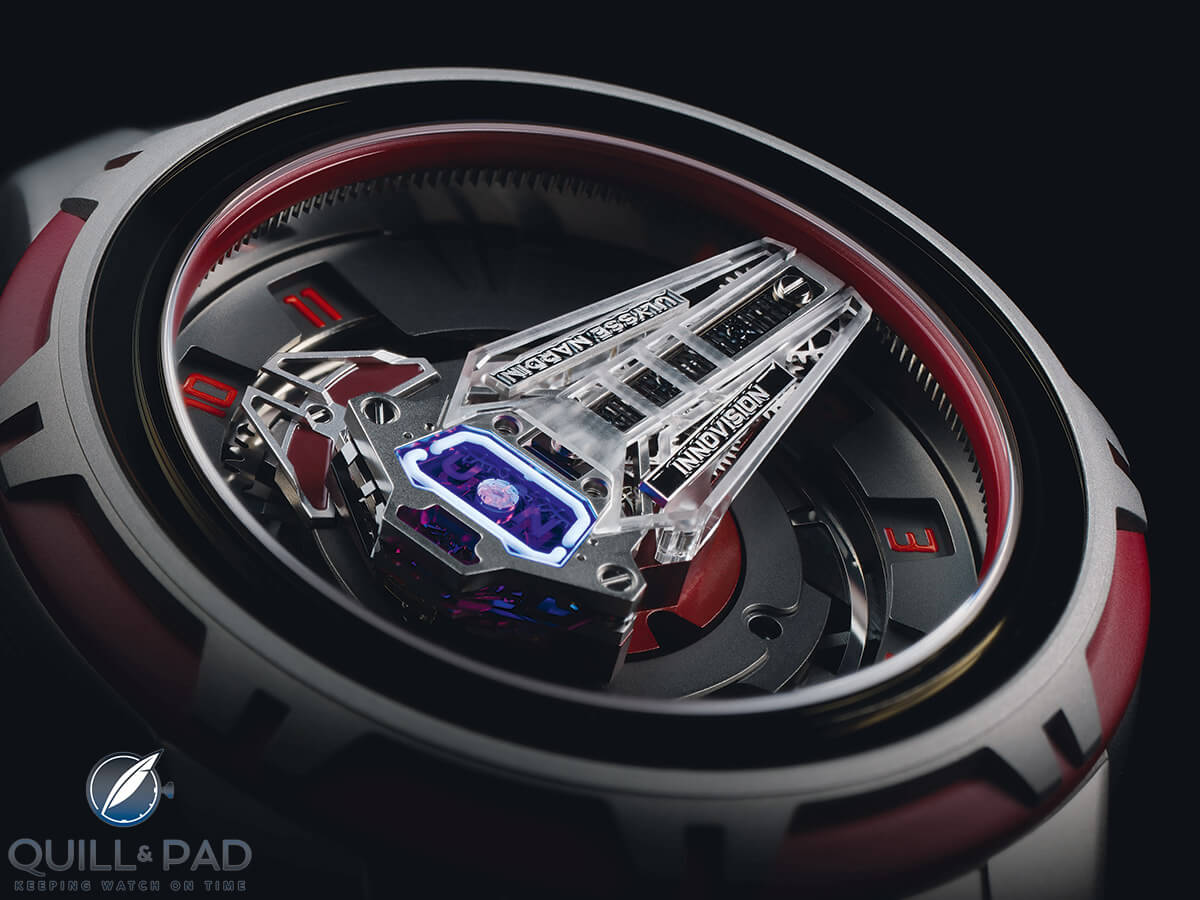
Minute hand of the Ulysse Nardin InnoVision 2
It is definitely the most technologically advanced minute hand ever made, displaying a variety of capabilities for the FEMTOPrint process. But it isn’t even the most impressive example of the watch’s technology.
That honor belongs to the . . .
Glass balance bridge with integrated shock protection & internal channels filled with Super-LumiNova
While this component looks pretty straightforward, for me it is in contention with the Dual Constant Escapement for the prize of coolest culmination after years of research and development.
The balance bridge of the InnoVision 2 is a direct descendant of one of the innovations presented in the InnoVision 1: a silicon shock-absorbing system.
Originally designed to reduce the complexity and inaccuracies of shock-absorbing systems and utilize the elasticity of silicon, the idea has found a new iteration with a new process.
Glass is usually considered to be extremely hard and brittle (as the majority of its uses show), so for some it is a surprise to hear that, under the right circumstances, glass can be very elastic.
When taken to very small thicknesses, glass becomes elastic and will return to position if bent or flexed. The same properties are found in silicon, which is why the material has been used for hairsprings for years.
Ulysse Nardin has been at the forefront of flexible silicon since the beginning, so it follows that experiments with other rigid materials would have been a next step.
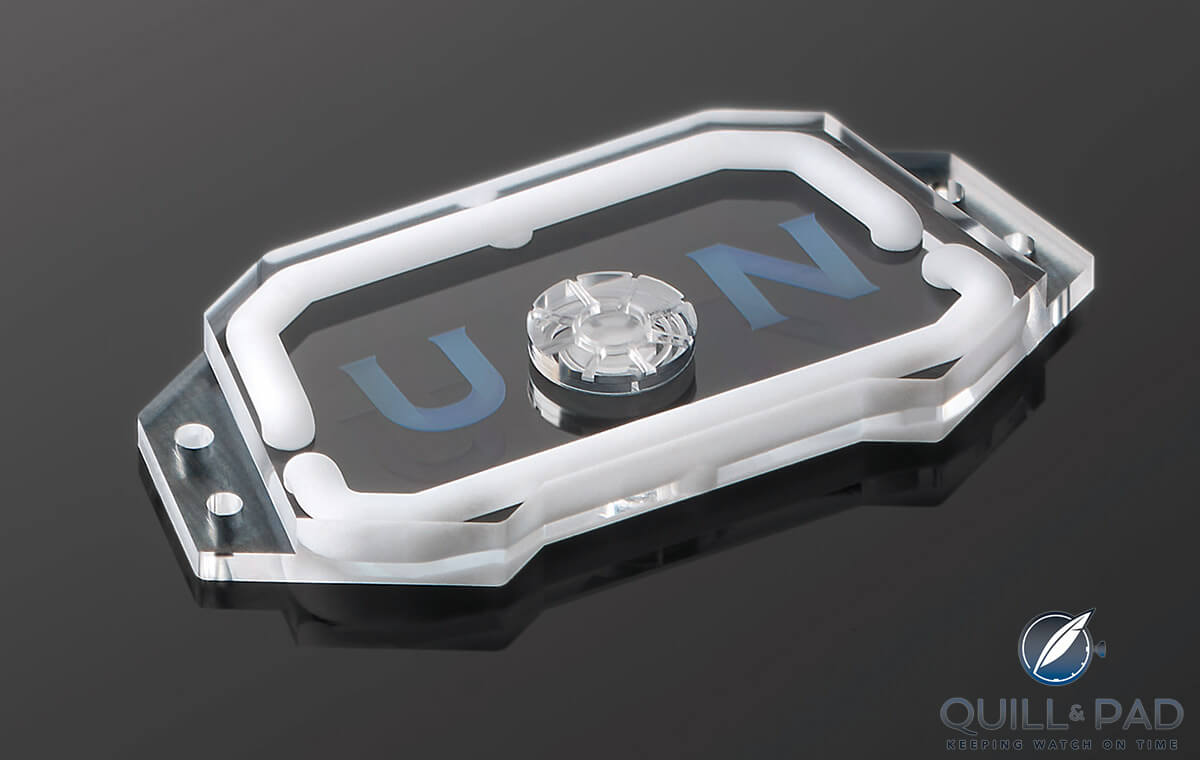
Glass bridge of the Ulysse Nardin InnoVision 2
The new glass balance bridge features a spiral shock absorber and jewel combination that is made entirely out of the single piece of fused quartz thanks to the very precise FEMTOPrint process.
Instead of adding half a dozen components that all have tolerances (which can result in tolerance stack-up, where things are looser than desired) and fail to function properly under certain circumstances, the integrated shock-absorbing system maintains perfect concentricity with the pivot as it is constructed in one piece.
This is an example of extreme optimization that could see part counts on complex watches begin to decrease instead of becoming ever more numerous. Soon engineering like this could make high part counts a sign of inferior production methods.
Obviously, there would be a lot of debate over that idea, but it could follow that multitasking components could become the new norm.
The second innovation in this part is thanks to another awesome aspect of the FEMTOPrint process: integrated channels filled with Super-LumiNova. The FEMTOPrint technology is very precise (if that wasn’t apparent already), and due to the very small resolution possible micro channels can be created inside the blocks of glass.
The smallest channels possible with this technology are only 2 x 2 x 8 microns! That is pretty much invisible to the naked eye and clearly much smaller than the channels in the glass balance bridge.
No, those channels are much bigger. And they are created in the same way that any feature is created using the femtosecond laser: the entirety of the channels are exposed and then etched away, leaving smooth channels just waiting to be filled with Super-LumiNova.
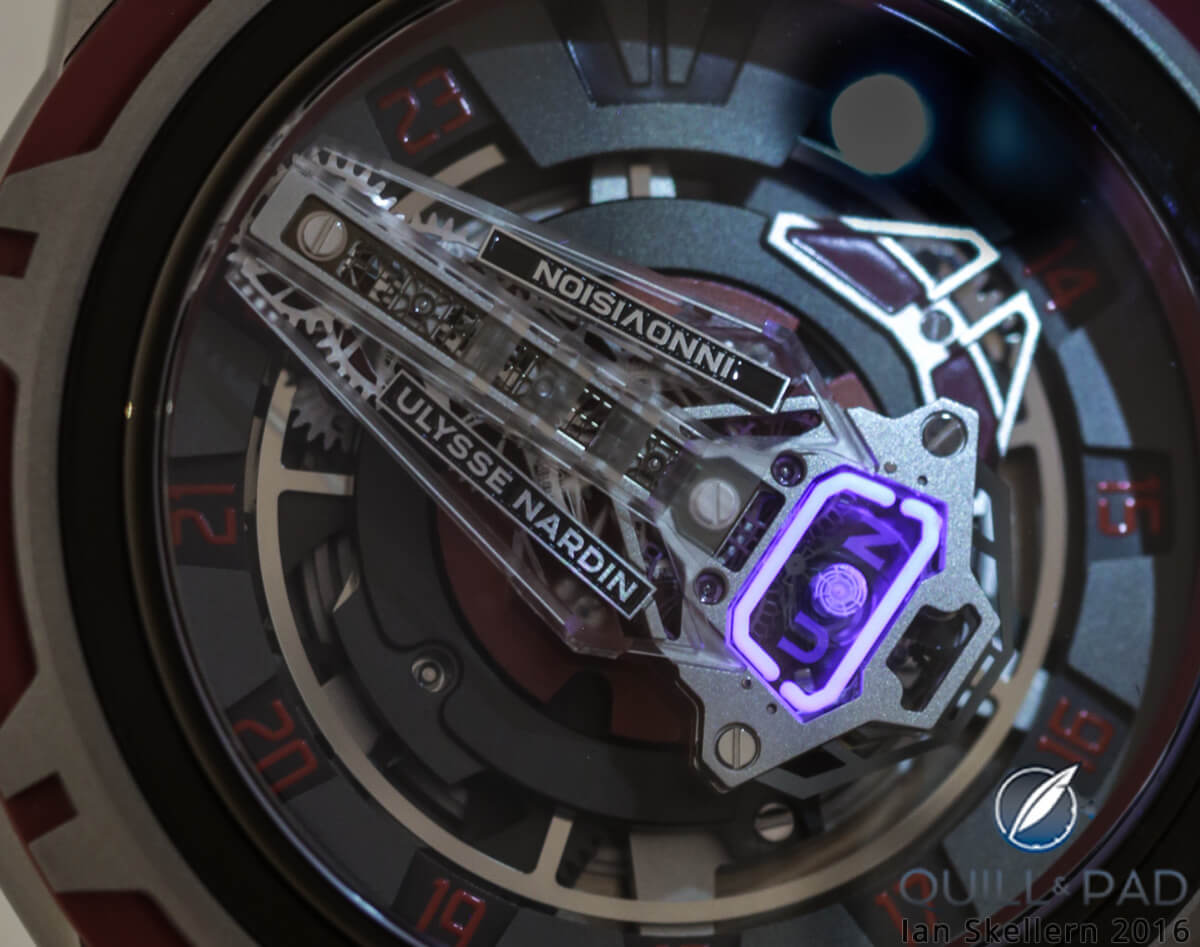
Super-LumiNova glowing in the glass bridge of the Ulysse Nardin InnoVision 2
When the luminous material glows inside the glass structure, it creates a bit of a halo inside the bridge, around the balance wheel. This also helps the extensive silicon components shine like they deserve. I’m excited to see integrated channels in more parts in the future, as it seems like this might be one of the better ways to create interesting movements and dials that are legibly visible at night.
Innovations outside of silicon and glass
Following on from the extensive innovations from the first InnoVision as well as the silicon and glass innovations for InnoVision 2, the final three take a variety of turns.
Let’s start with the time display for the hours.
24-hour time display
The choice for the InnoVision 2 to display all 24 hours created an interesting problem: how to show all the hours while still having the hour pointer rotate twice around the dial every day. The solution sounds easy, but the implementation is complicated enough to warrant a patent.
It begins with a set of windows with the numbers 1 through 11 displayed in the AM and 12 o’clock left solid.
As the hour hand reaches midday, the numerals in the windows change over to display 13 through 23.
The change, driven directly off the large spring barrel, takes 15 minutes to complete.
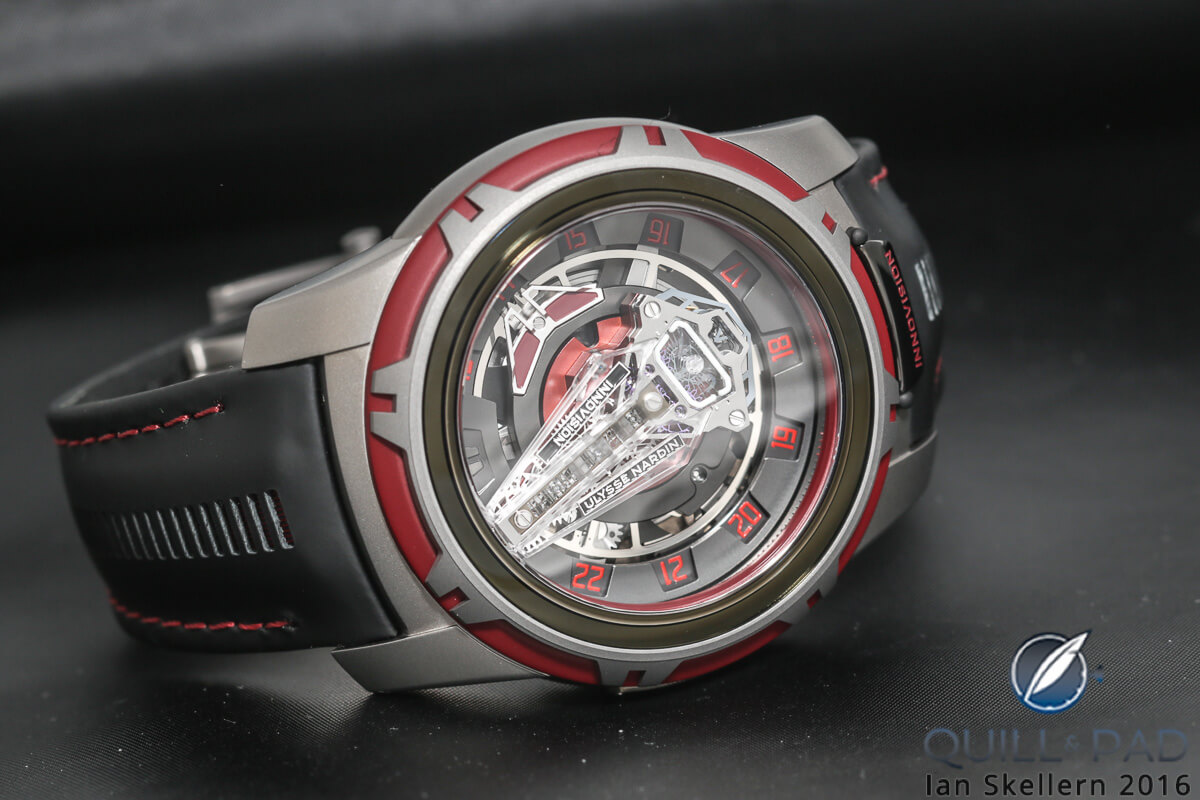
Ulysse Nardin InnoVision 2
Since the change is not instantaneous, this answers the question as to why the 12 o’clock position was removed from the process. As the numbers change, the hour hand is nowhere near to pointing at them, making sure no confusion can be had about whether it is noon or midnight (let’s assume you work a very long shift in a basement).
If this was just a continuous process to rotate a numeral ring, it wouldn’t be much to celebrate (though that would still be a cool mechanism).
The thing about this mechanism is that it rotates one position forward and then rotates one position backward. This forward-reverse dance is what makes the display special, which also explains why further details of the mechanism’s design are still sparse (patent pending).
24-karat hard gold wheels
Gold has always been a pretty amazing metal with unique properties that have made it perpetually coveted.
Here, gold is used because of its tribological (relating to friction, wear, and lubrication) properties, which means it has lower friction when meshing with steel pinions.
The hard gold wheels comprise the going train, which is mounted in the glass minute hand underneath the sapphire-coated silicon bridge.
The wheels themselves are manufactured using the LIGA process (photolithography) at Mimotec (for a full explanation of LIGA and Mimotec see Looking Back On 10 Years Of Ulysse Nardin’s Pioneering InnoVision Technology).
Again, the name is a bit of a misnomer as the wheels are not fully 24-karat (pure) gold, but slightly less after having been alloyed with other metals to obtain the desired hardening properties.
This is called micro alloying, and it allows the gold to be technically 24-karat but still be alloyed for improved mechanical abilities. Still, the nearly pure gold is significantly harder than regular 24-karat gold that normally tests at 70 on the Vickers scale for hardness.
The hard gold measures in at about 220 Vickers hardness, a significant increase with only a small amount of additives. The wheels are also rhodium-plated for the aesthetics of the area inside the glass minute hand.
Grinder self-winding mechanism
I’ve saved one of the best for last, and the one I think is most likely to find its way into production watches first: the new Grinder self-winding mechanism, which is a new way to capture power from the motion of the wrist, though this one can be fully wound using half as much movement from the wearer.
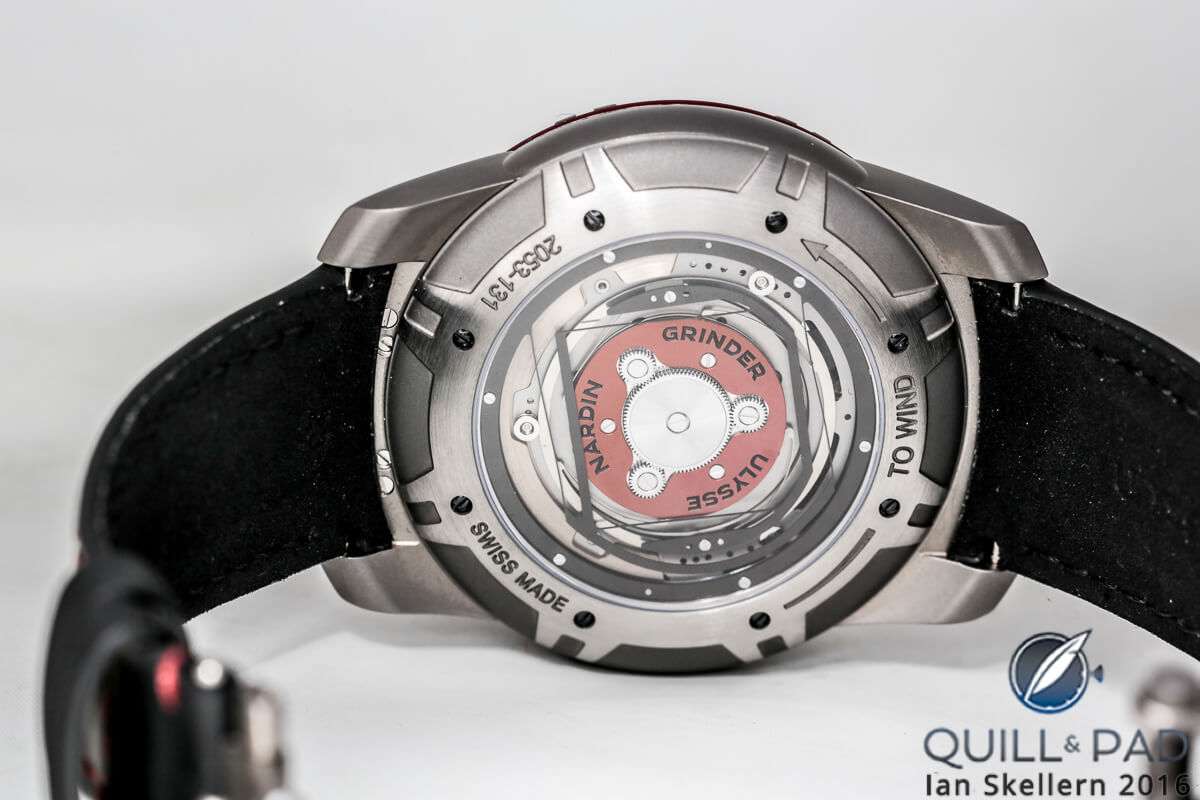
The Grinder winding mechanism visible through the display back of the Ulysse Nardin InnoVision 2
The mechanism is a little bit inspired by a grasshopper escapement in reverse, though it has twice as many catches. Or at least that is what I see when I look at the mechanism.
The system begins with a centrally mounted ball bearing rotor (technically speaking, not that different) followed by three smaller ball bearings attached to a couple sets of springs. These springs have four long ratchet hooks with very small catches on the end. The ratchets catch a center wheel with nearly indistinguishable teeth on it.
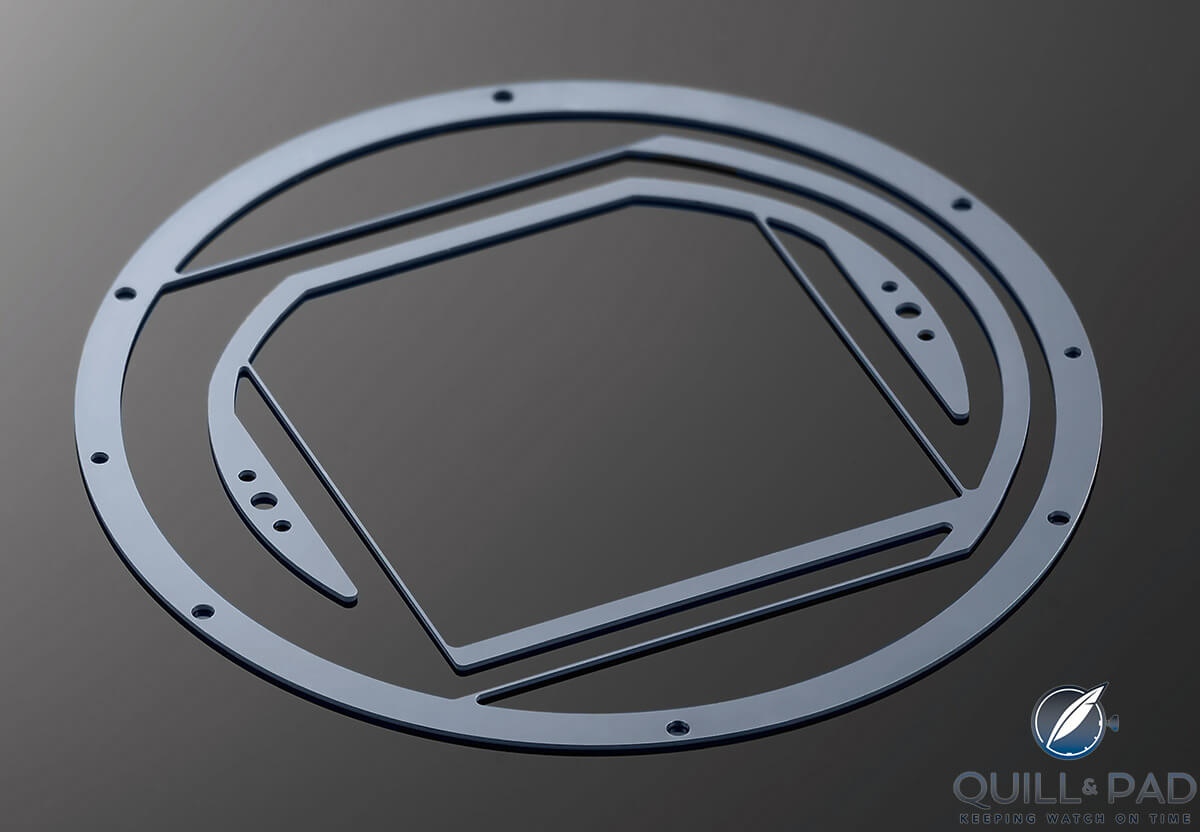
Flexible frame for the Grinder mechanism of the Ulysse Nardin InnoVision 2
The small size of these teeth allow for the sprung ratchet hooks to only need to move a very small amount to grab the next teeth and move the wheel forward. The four springs work independently yet together to create a very small rotational force from the slightest motion.
The angle of rotation needed to gain one position on the ratchet wheel is half that of a conventional winding system. Better yet, the mechanism is twice as efficient at winding compared to standard mechanisms.
This is accomplished by the two-stage planetary gear system in the center, which allows the micro-sized movements of the ratchet hooks and wheel to be translated into a larger winding force.
This has the potential of being more efficient for more sedentary watch enthusiasts that sometimes have trouble moving enough in a day to keep their watches wound. I have even heard of people who work in an office doing hours of computer work and not moving enough to maintain an appropriate amount of power reserve.
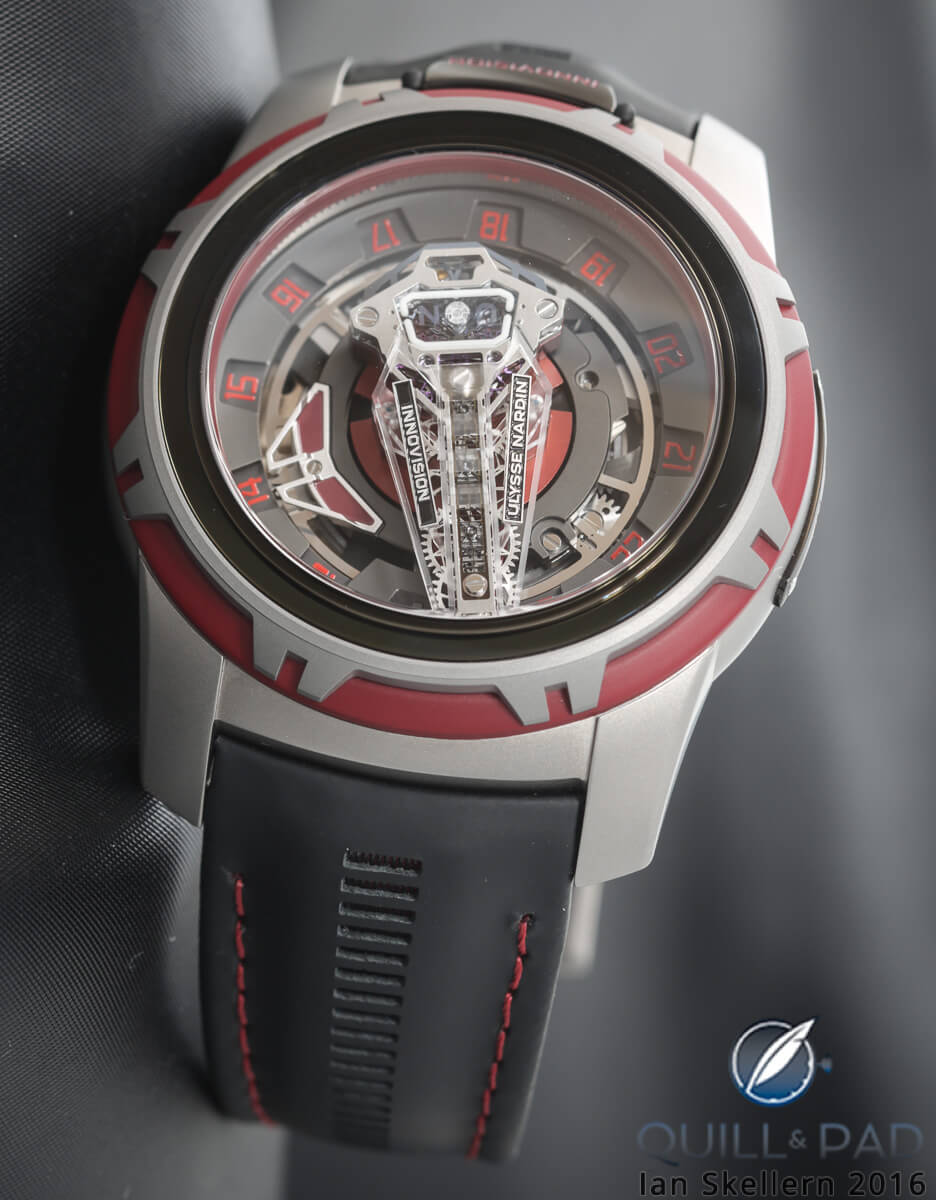
Ulysse Nardin InnoVision 2
The system might also find a home in mobile electronics, since the addition of regular bi-directional winding systems have found their way into self-charging gadgets already and are even being experimented with for pacemakers.
I can imagine that a more efficient mechanical system could find potential markets everywhere; it’s only a matter of time.
Out of all the innovations presented in the InnoVision 2, the Grinder system seems the most useful and inexpensive to incorporate into production models. The other innovations are complicated and much more difficult to produce, so I wouldn’t be surprised if it takes longer for them to find homes in new serial models.
That being said, seven out of the ten innovations from the original InnoVision found their way into production watches, so the odds are good that we will see a majority of these innovations available for sale in the coming years.
For me, that might be the worst thing about the InnoVision 2: it is “just” a concept watch – a showcase for ideas – and so will never be available for sale.
Of course, it would be out of my price range but I would absolutely love to have an assembly of these innovations on my wrist – and for longer than the few minutes we are lucky to get at a meeting.
Still, I am glad that Ulysse Nardin continues to forge ahead with engineering challenges that push the boundaries of watchmaking technology.
The brand has been one of the foremost leaders in watchmaking research over the last two decades, and the InnoVision 2 proves again that Ulysse Nardin is not afraid to make a bold statement.
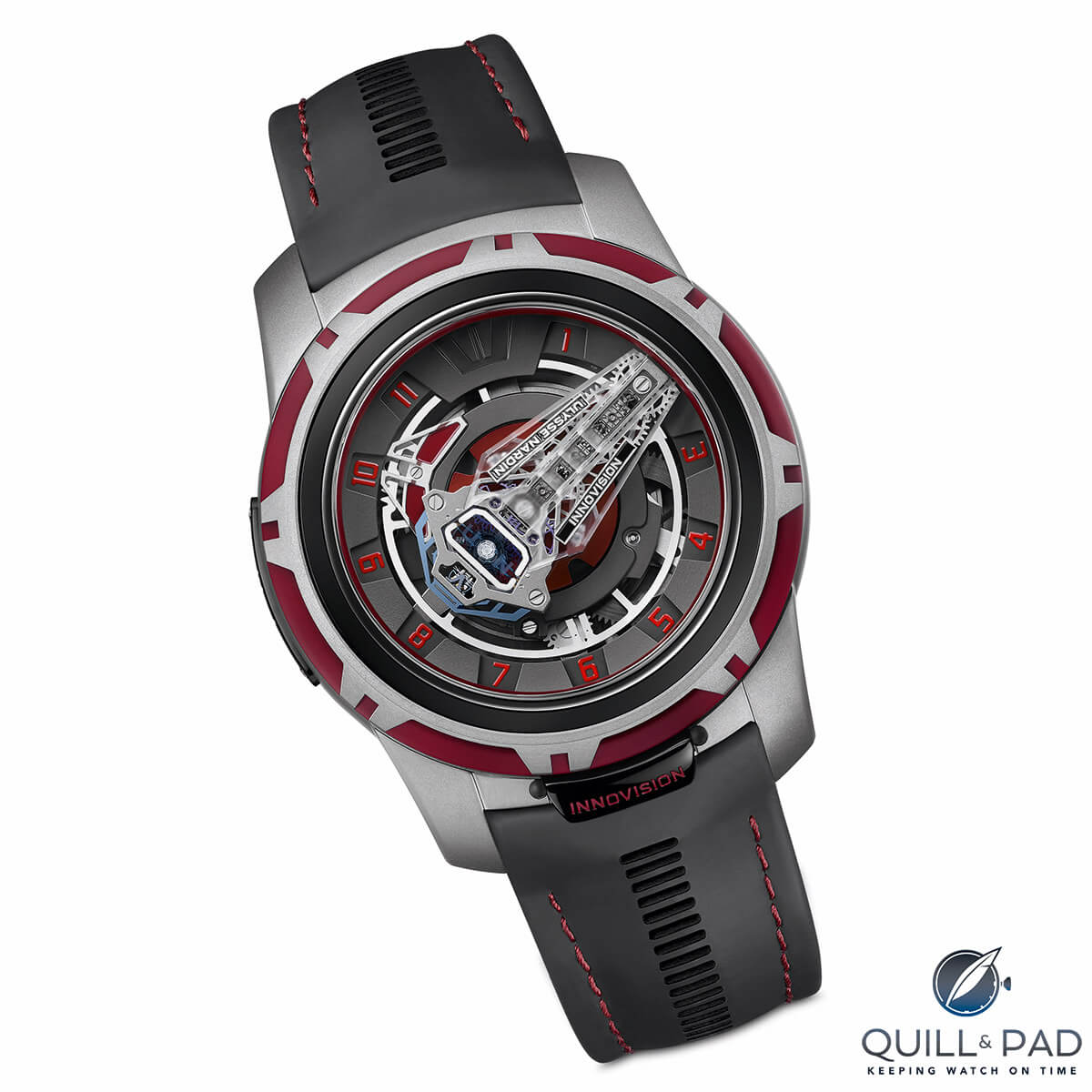
Ulysse Nardin InnoVision 2
Kudos to everyone involved in research and development at Ulysse Nardin and its partner companies: your work speaks volumes.
For more information, please visit www.ulysse-nardin.com/news/innovision-2.
Trackbacks & Pingbacks
-
[…] of the ten innovations in the InnoVision had found their way into production pieces, and a new InnoVision 2 was released with ten more impressive, new […]
-
[…] I doubt that, and Ulysse Nardin’s Innovision 2 from SIHH 2017 is a perfect example (see Diving Deep Into The Technology Of The Ulysse Nardin InnoVision 2). […]
-
[…] that Ulysse Nardin made a big impression at its first showing at SIHH with products such as the InnoVision 2 concept watch, the Marine Regatta, the Hourstriker Pin-Up, and the very competitively priced Marine […]
Leave a Reply
Want to join the discussion?Feel free to contribute!
Awesome stuff! Great read – thanks for that Joshua.