When you look back, 2008 was a strange year. Most of the great events in that year were overshadowed by the subprime mortgage and financial crises sparking the biggest global recession of the decade. Yet while the world reeled and economies took a tumble, there were also bright spots to be celebrated.
For one, the Olympic athletes in Beijing captured the world’s attention to the tune of 5 billion viewers. Venus and Serena Williams battled for the Wimbledon title – a truly historic moment in tennis – and the New England Patriots lost the Superbowl. A pretty good year for U.S. sports fans.
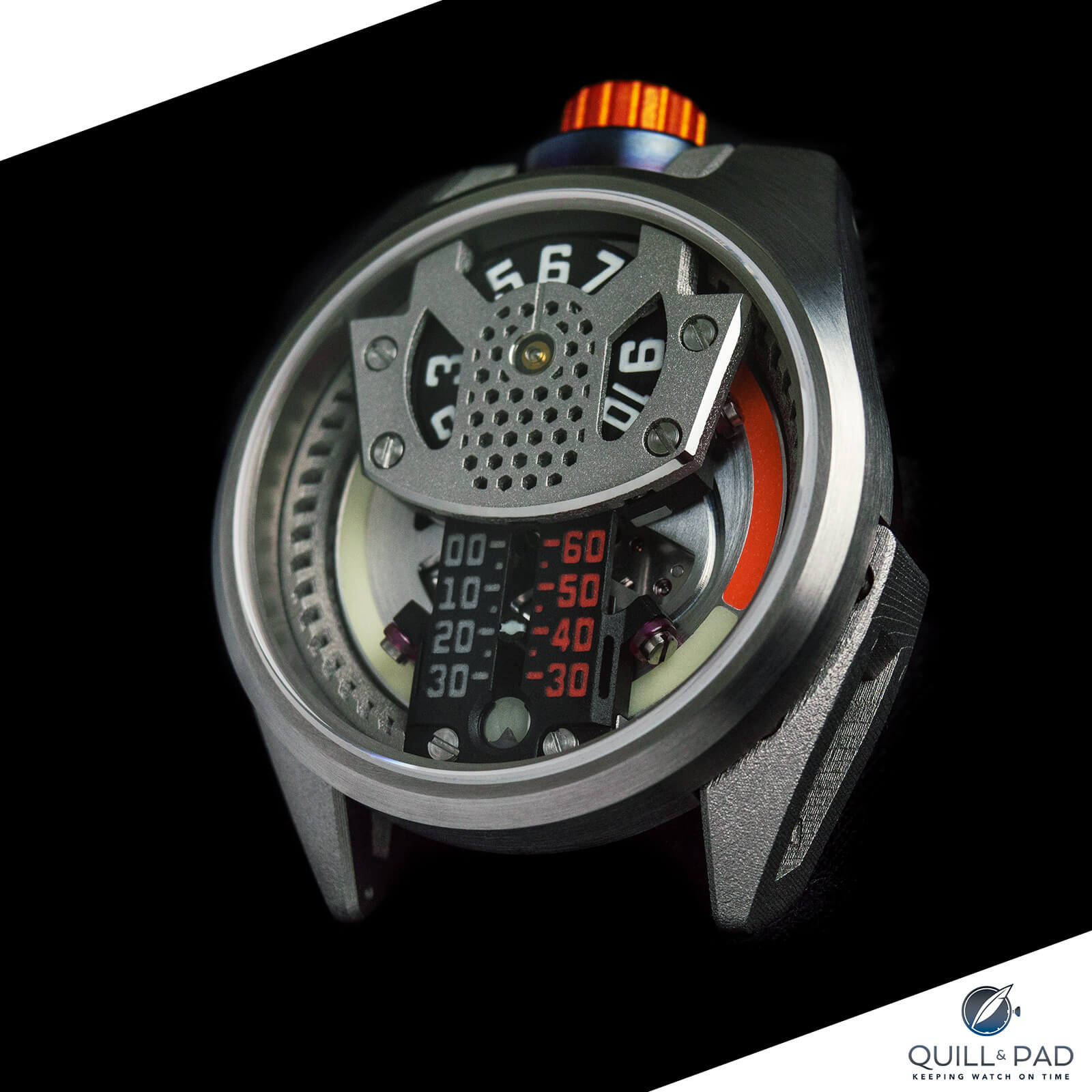
Barrelhand P1
Bhutan officially became a democracy and same-sex marriage became legal in a few more U.S. states (even though four countries, including Canada, had already made it fully legal nationwide). In November 2008, Barack Obama was elected as the first biracial President of the United States, and only a month later Bernie Madoff was arrested and charged with securities fraud in $50 billion Ponzi scheme. Not a bad month.
Science shone brightly in 2008 as the Large Hadron Collider at CERN was powered up for the first time in Geneva, Switzerland. In space news China launched the Shenzhou 7 spacecraft and performed the first Chinese EVA (spacewalk). India launched its first unmanned lunar mission, Chandrayaan-1. And as a harbinger of what was to come, SpaceX launched the first private spacecraft, Falcon 1, into orbit.
But most importantly for today’s article, the band Fall Out Boy was at the height of its fame as a pop punk band, riding the success of its 2007 album Infinity On High.
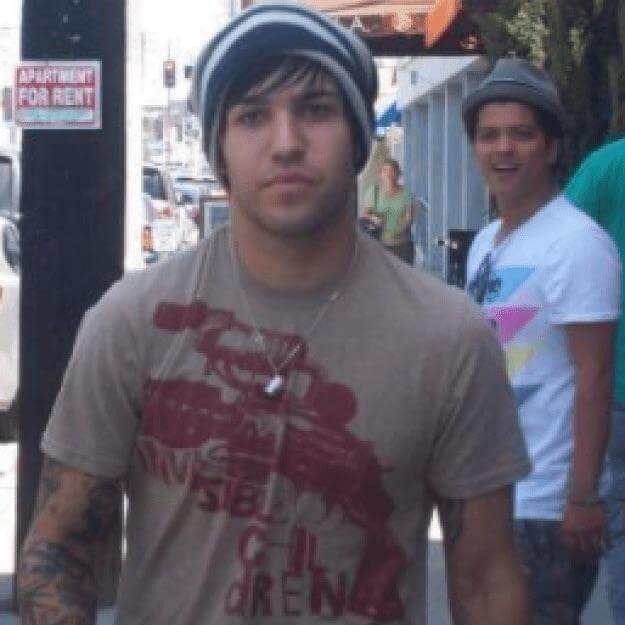
Fall Out Boy bassist Pete Wentz with Bruno Mars in the background
Then, on April 29, 2008, paparazzi captured an image of Fall Out Boy bassist Pete Wentz on the streets of Los Angeles with a man in the background looking shocked. The man in question was future superstar Bruno Mars before his meteoric rise. This photo has gone on to be an internet favorite, spawning the Bruno Mars starstruck folklore before he ultimately became a star himself.
While Mars debunked this specific account (he said he was actually shocked that the photographer had aggressively pushed him and his friend out of the way seeking a clearer shot of Wentz), the photo is now inadvertently famous as an example of how people can be fans before their own success.
And that brings me to the Barrelhand P1 and its creator, Karel Bachand.
History first
Bachand was a brand-new mechanical engineering student at San Jose State University in 2012 when he stumbled upon the Urwerk UR-202 and decided that even though he was a college student on a tight budget, he needed that watch.
So he did what any ambitious engineering student would do: he made his own working replica. It took about two years and a lot of hard work, but in 2014 he revealed to the world what he had created. The replica was so good (and made on such a relatively small budget while studying to be an engineer) that it gained him recognition – and an invitation from Urwerk to visit during SIHH.
That opportunity lit the fires of passion inside Bachand, and his own ideas of a brand-new watch started to take shape. Now, six years and after lots of hard work and tireless dedication later, plus the usual setbacks when developing a brand-new watch, his first timepiece, the Barrelhand P1, is finally ready.
Obviously inspired by Urwerk, but unique and distinctive in its own right, the P1 extensively utilizes metal 3D printing – even for one functional movement component – and sets the stage for some awesome aesthetics for fans of wild watches.
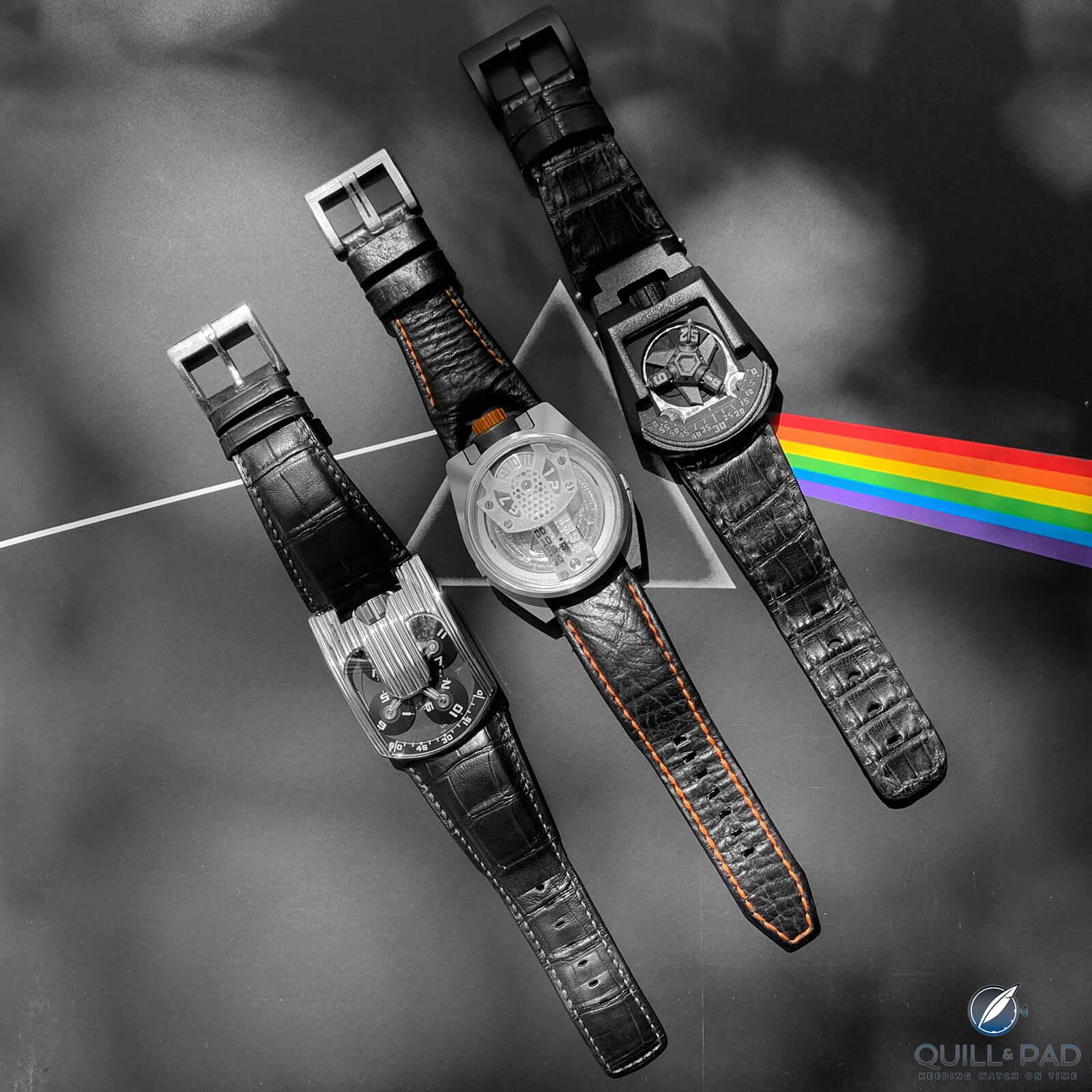
Left to right: Urwerk UR-103, Barrelhand P1 prototype, and Bachand’s homage to the Urwerk UR-202
Barrelhand P1
The Barrelhand P1 takes a lot of the lessons learned from developing the replica of the UR-202. It features linear minutes and a Geneva-wheel hour mechanism that shares a lot of mechanical direction from Urwerk, including how that company’s satellite hour mechanism works.
The P1 has a central minutes column with a sliding indicator pointing to two columns of digits: 0 through 30 on the left in white Super-LumiNova and 30 through 60 on the right in orange Super-LumiNova. The column to read the time is indicated by a matching color seen through a little round window at 6 o’clock.
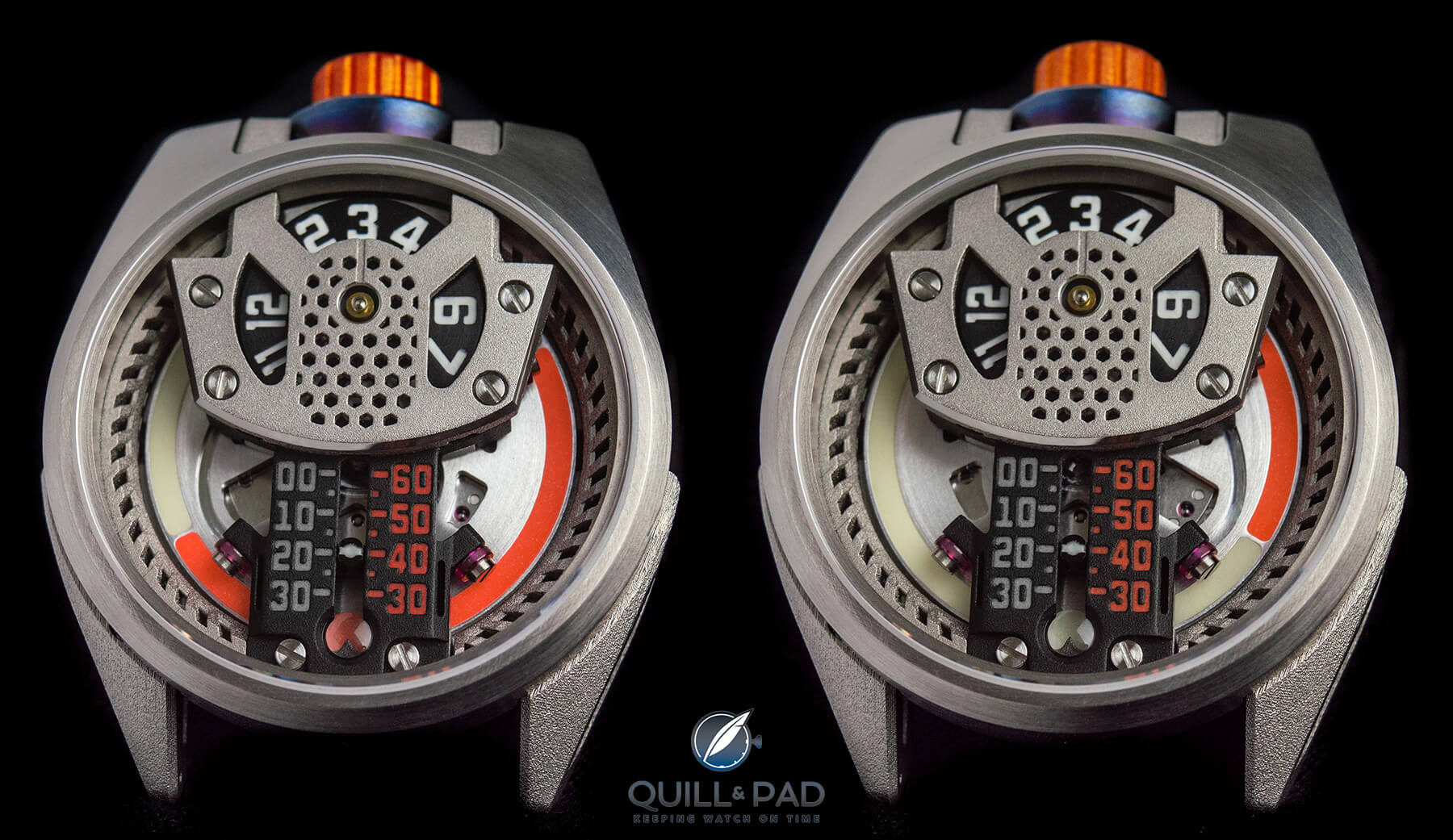
Barrelhand P1 indications
The hours, read via a disk at 12 o’clock, are viewed through a window in the upper movement plate. The hour digits are filled with the more traditional green Super-LumiNova to match the minute hand pointer below and tie the time indications together.
The crown is at the top of the case, like Urwerk’s crowns, and the design of the mechanism allows forward and reverse time setting and manual winding. The time-setting mode is activated by a small lever on the rear of the case that pops the crown out from winding mode where it is nestled in a titanium “exhaust tip.” It’s playing off the “spaceships for your wrist” theme that Bachand says is the driving inspiration behind the brand.
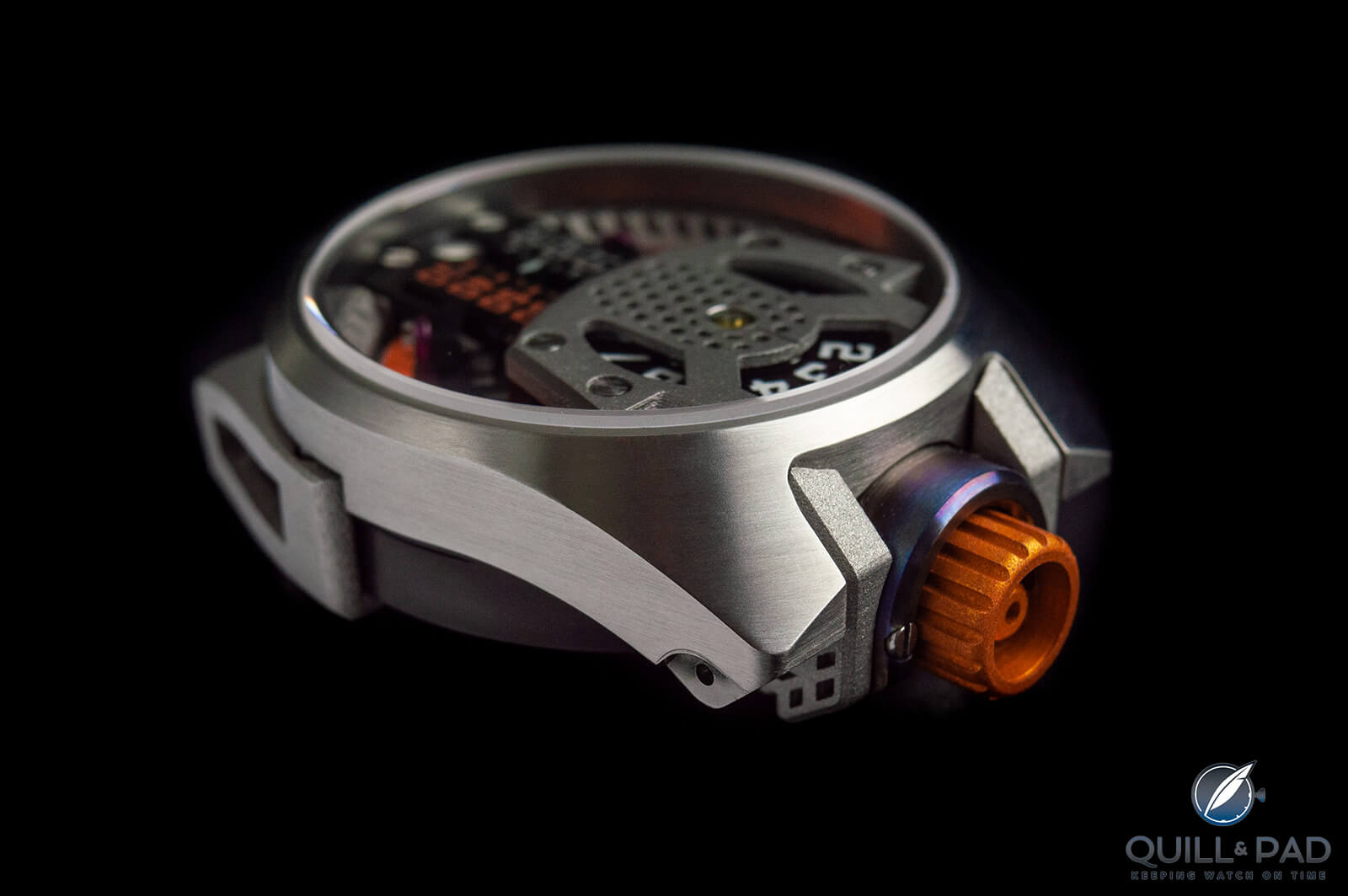
Barrelhand P1 crown
With the asymmetrical case and crown at the top, the P1 takes on a general bullhead design that is likely to be popular with many collectors. The design is helped by separate lugs on both ends of the case that create a visual distinction between the case and the metal binder jet components, which to me are reminiscent of “old” sci-fi spaceships that have salvaged additions to the original ship (nothing goes to waste in space).
The case is in machined titanium, while the lugs are made from binder jet-printed steel (I’ll dive into that more in a bit) that is only minimally finished to maintain the rugged look of the printing process.
Aside from the base Swiss movement and a couple of DMLS (Direct Metal Laser Sintering) steel components, everything is manufactured in the USA, giving the P1 a strong American watchmaking presence.
This is most impressive when you consider how unusual it is – not the typical wristwatch that the likes of RGM or other small producers are making. But let’s dig a bit deeper into the details that demonstrate all the cool features of the Barrelhand P1.
Mechanism design
The time display mechanisms are basically a complete module atop a Swiss base. The minute pinion drives the whole thing via a large cam plate dial underlying the entire mechanism, inspired by the function of a record player needle. The cam plate is a flat plate with an inset groove to produce variable motion, a similar function to the more standard lobed cam or spiral cam.
The bottom cam plate dial uses a channel machined into the surface to act as a cam path for the minute indicator. As the underlying dial rotates once per hour, the cam path traces a rounded heart shape that translates into linear motion.
The indicator rides in the channel and is constrained by small rails underneath the linear minutes to keep it limited to the simple back and forth movement over 60 minutes. The minute indicator carriage glides along two precision rails to prevent any racking and provide smooth operation.
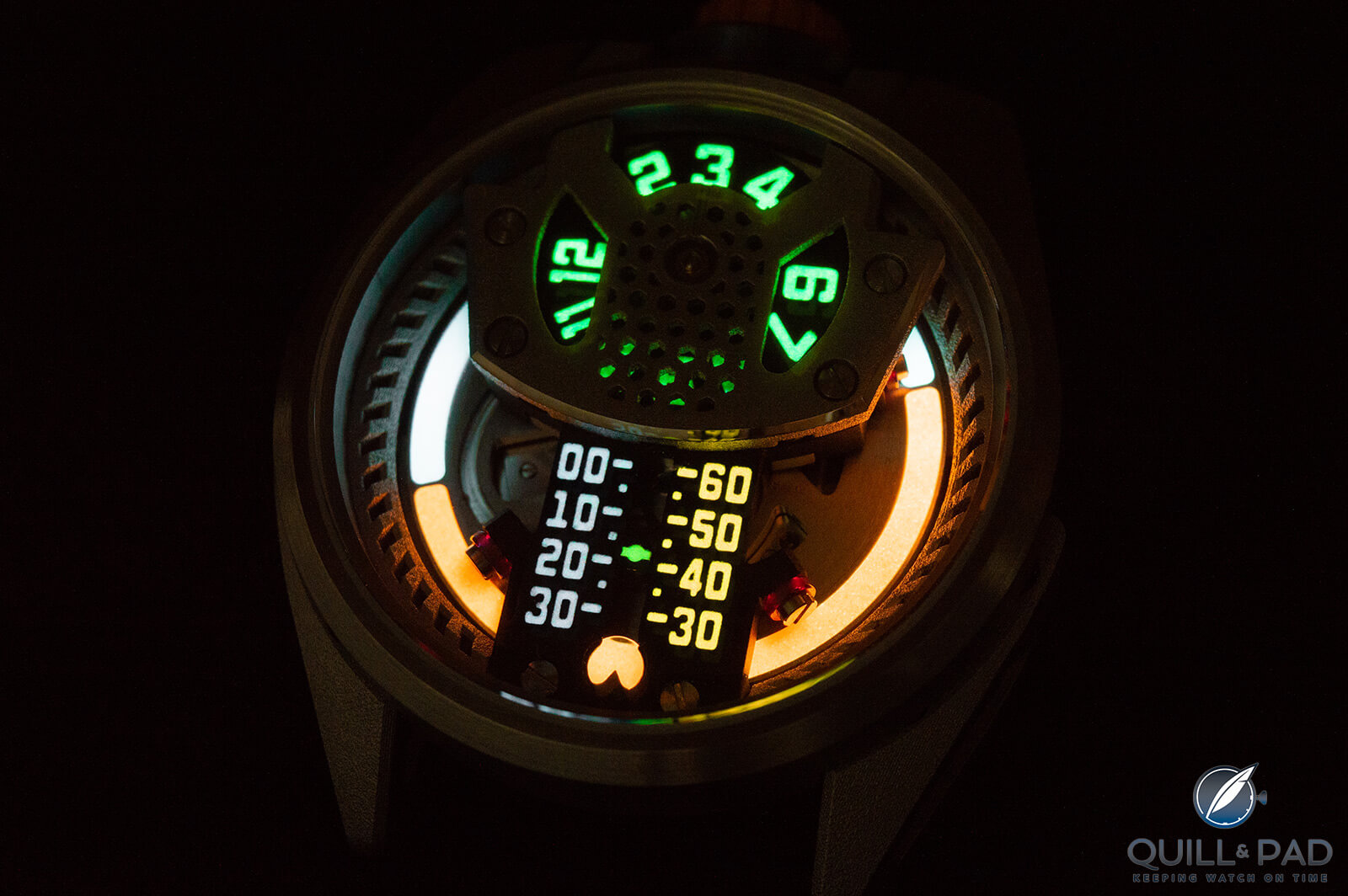
Barrelhand P1 lume shot
The underlying dial also has a set of luminous inserts around the perimeter that act as the delineator between the first half of the hour and the second half. The lume material looks similar to something by Black Badger, a plastic made from luminous pigment and resin machined to shape for a solid block of light emitting material. The material has been dubbed ForgeGlow by Mike Mishler, who developed the material, as a direct analog to the Black Badger. It isn’t available commercially, but Bachand worked with Mishler to make the necessary components for the P1.
At the midpoint of the two inserts there is a very small gap to mark the top of the hour and the midway point. These small breaks can be seen when they align in the color indicator window with a pointer for a more precise ability to set the time.
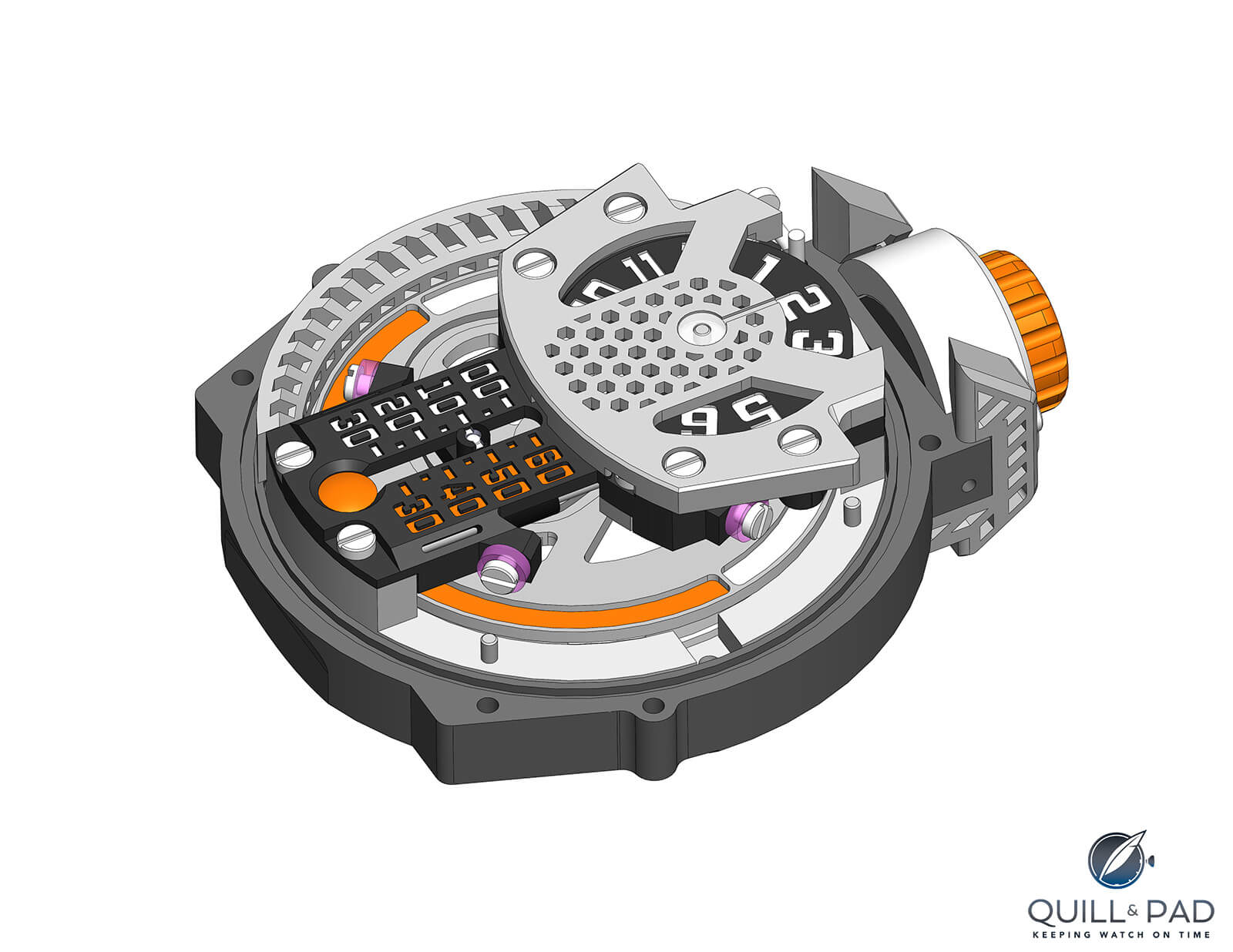
Barrelhand P1 movement details
The cam plate dial also incorporates the driver for the hours, which utilizes a Geneva wheel mechanism. A lobe with a pin extending upward from the cam plate meshes with small channels of a 12-position Geneva wheel affixed to the bottom of the hour dial. As this pin engages with the slots, it slowly (over about 15 minutes) rotates the dial to the next position for the top of the hour. Once the pin disengages, the cam plate also has a semicircular lobe that blocks the hour dial from moving until the next hour arrives.
This is a very tried-and-true mechanism, and the implementation is a very smooth way to create intermittent motion from simple rotating wheels. Urwerk was basically built on the mechanism and it is no surprise that Bachand gravitated toward that solution.
In fact, the cam channel for the linear minutes is also derived from the UR-202, which has a retractable pointer that follows a similar style of path for its own motion.
This is probably the most successful aspect of the P1: utilizing proven techniques to create something brand new. The P1 is very unique yet builds on a foundation developed both by Urwerk and watchmakers in general for generations. But it doesn’t end there.
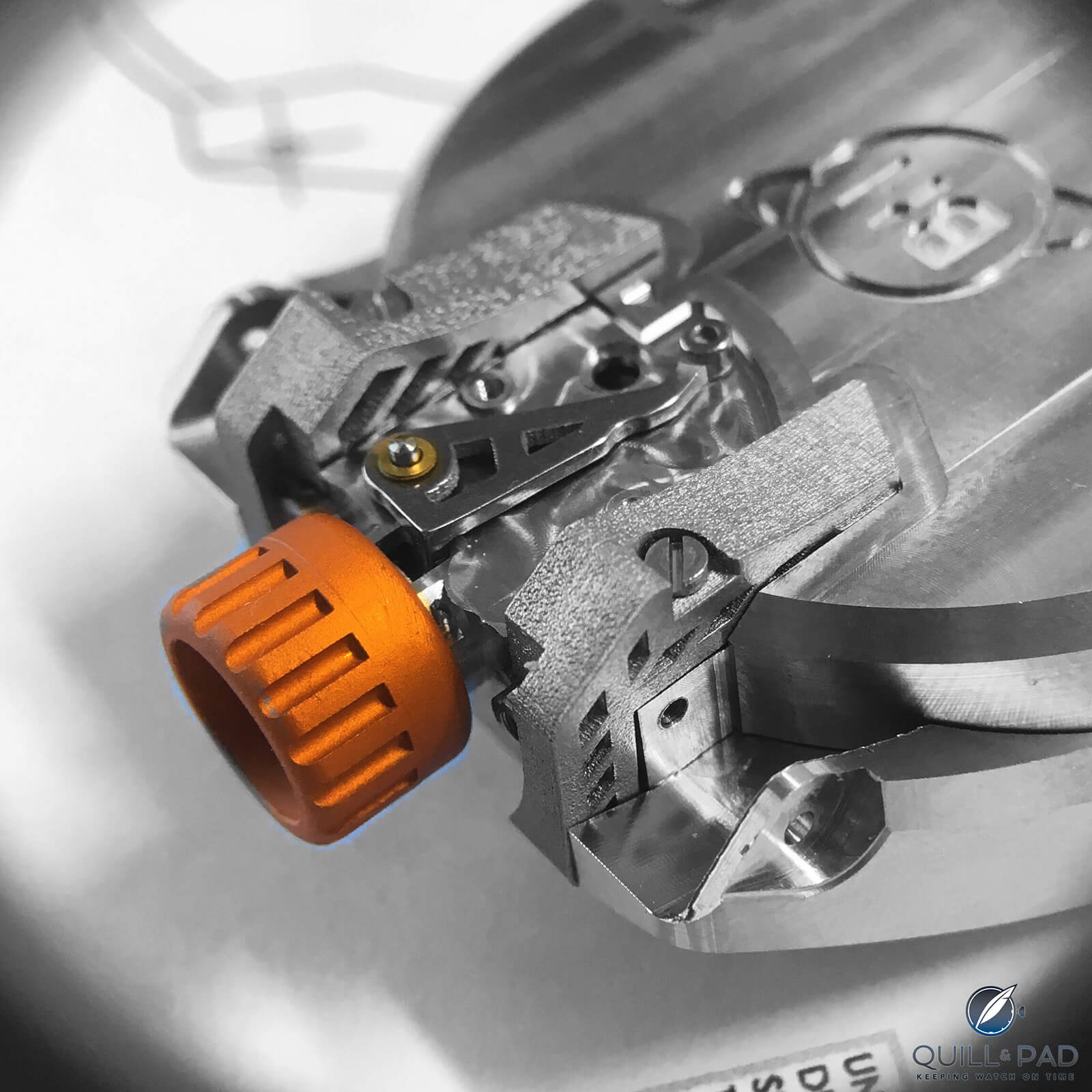
Barrelhand P1 crown release mechanism
Clever solutions and material innovations, including 3D printing
The underlying cam plate dial is also a rather large component that could be prone to shocks so it rides along a set of four jewel bearings (the cam plate leveling system) to provide a very precise, low-friction way to keep the dial where it needs to be.
I’ve seen this strategy implemented in other watches but not many. It was most recently seen in the Bovet Récital 26 Brainstorm Chapter Two, once again putting the P1 in great company.
If that was there the story ended this would be a fantastic watch, but Bachand also has a passion for innovation and materials thanks to his background with 3D printing technologies. For the Barrelhand P1 he chose to incorporate as many additively manufactured components as possible, which is still a relatively rare thing across the watchmaking industry.
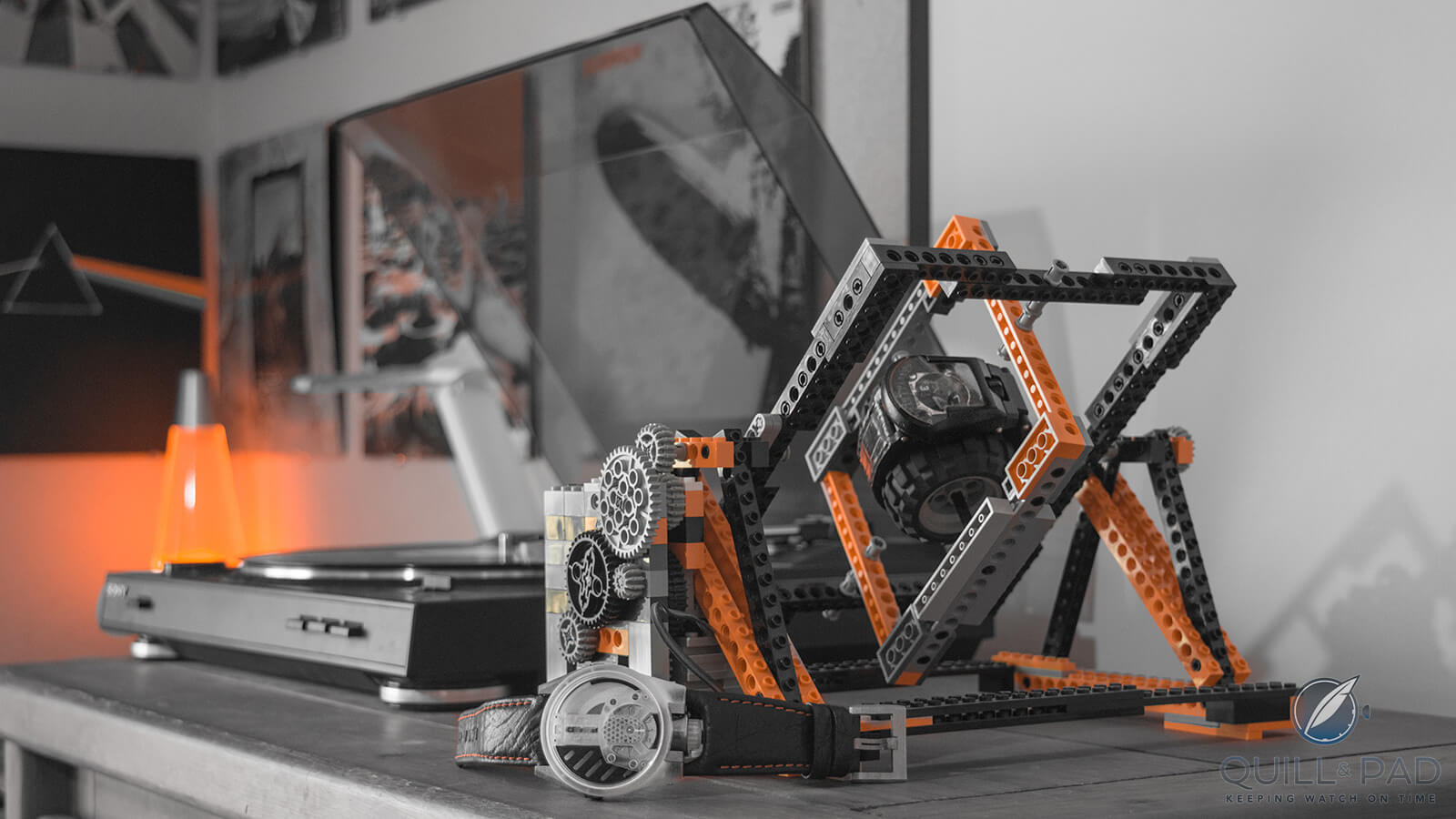
Barrelhand Lego testing rig
The project was founded upon pushing what this technology could do for watchmaking in general. It took six years and 36 prototypes to land on the final design and discover what was currently capable of being produced with additive manufacturing. In the end, there are 11 components made using a process called metal binder jetting, which is a fairly accessible way to “print” accurate metal parts that can be fairly similar to machined counterparts.
The process begins with a layer of metal powder approximately 25 microns thick (0.025 mm), which has a binding agent, similar to a liquid ink, applied by a print head in the exact location where the very thin slice of the geometry is required. Then another 25-micron layer of metal powder is quickly drawn over the top and the process repeats.
The metal part grows by layers and is fully supported by powder on all sides, making for a fast and well-supported print similar to the more familiar DMLS (Direct Metal Laser Sintering) but a fair amount more accurate.
The part is then cured in the machine up to 200 degrees Celsius and then taken out of the powder for a follow-up round of sintering at 100 degrees Celsius for up to 36 hours to burn off any remaining binder agent. This results in a rather strong and only slightly porous component that can be further strengthened with bronze infiltration, though it isn’t necessary in all cases.
The components in the P1 made by this process include the steel lugs, the crown release system, the lattice dial inserts, and the buckle. And more importantly the hour wheel top bridge, which is a functional movement component.
The part comes off the machine ready to use, and with the installation of a jewel bearing to support the hour wheel it can be installed as a fully functional component. This is likely the first functional 3D printed movement component in the industry to find its way into a production watch, with maybe only Panerai nipping at Barrelhand’s heels. I still have not seen any movement components from that brand however, only non-movement components with no functional use.
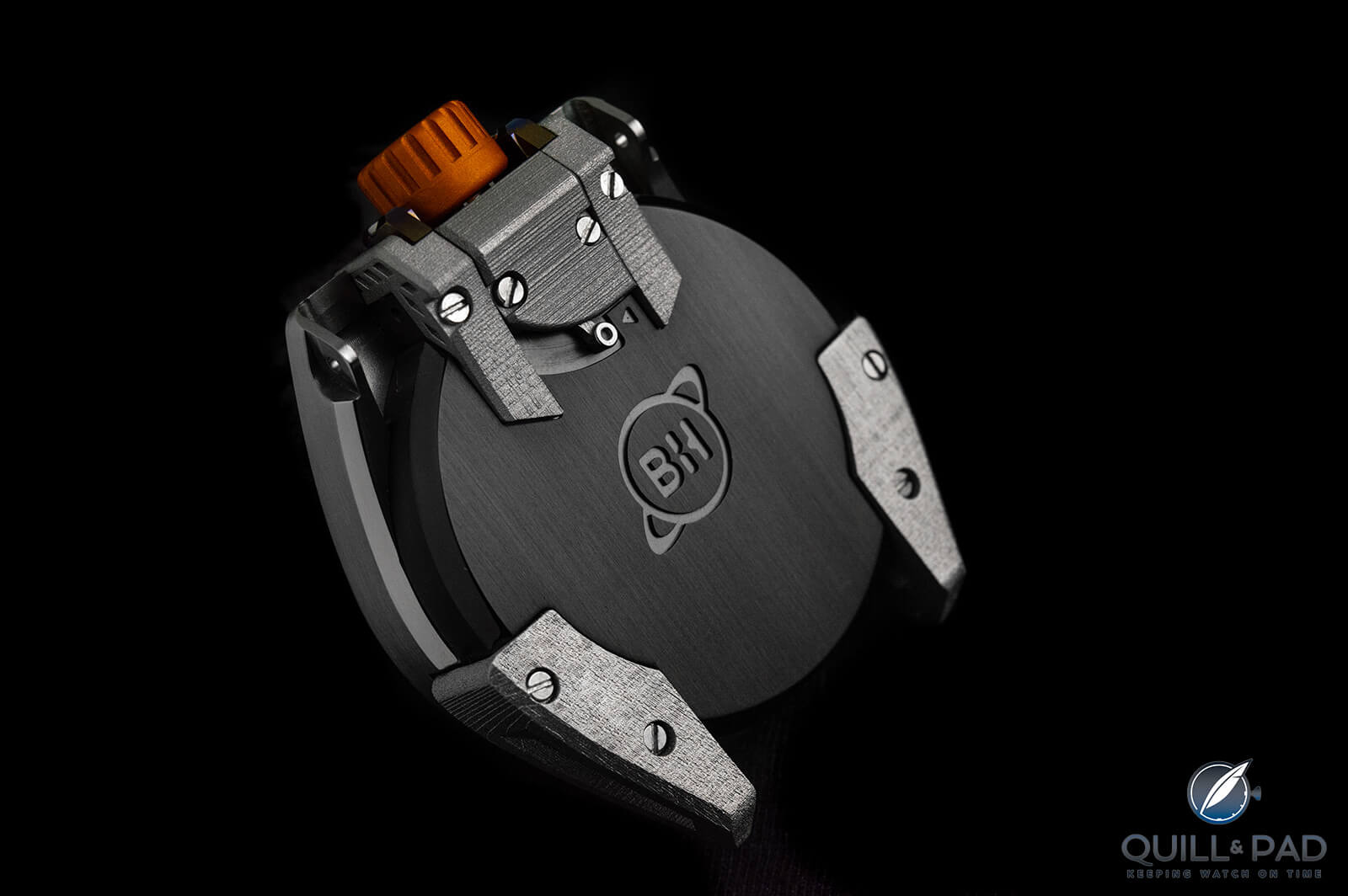
Barrelhand P1 case back
Finishing touches
Most of the components also feature a latticework structure that does double duty by showing off the capabilities of the process but also helping to ensure dimensional stability during the curing and sintering process. Since the material can shrink in sometimes irregular ways, avoiding large solid masses can keep parts more stable for a better end result.
This strategy also led to the lugs being skeletonized and allowed for the serial number to be printed within the structure where it would be incredibly difficult to machine or engrave using standard machining processes.
While this is entirely unnecessary, it shows the type of thinking that went into the development of the components and how additive manufacturing was always a driver for the design. It’s also obvious with the “unfinished” nature of those components, which allows the micro grain and print layers to remain visible, giving the P1 a strong industrial aesthetic.
The titanium case is nicely finished with some very cool combinations of brushed and polished surfaces. But overall the aesthetic is not trying to be haute horlogerie with delicate finishes suitable for a black-tie affair.
This watch is designed to highlight the mechanisms and the technology and does that very well. From the visible cam plate mechanism to the metal binder jet components, it’s obvious that this is no dainty watch, even if the proportions keep it within the standards of the large avant-garde watches like Urwerk and MB&F.
I’ve been watching the progress of this project for nearly its entire existence, first finding Karel Bachand after he released his homage replica of the Urwerk UR-202 in 2014. The development of the Barrelhand P1 has clearly been a labor of love and it’s fantastic to see it come to completion. I am excited to see the broader reception of the piece and look forward to what he will create next as he continues to push additive manufacturing in the watchmaking industry.
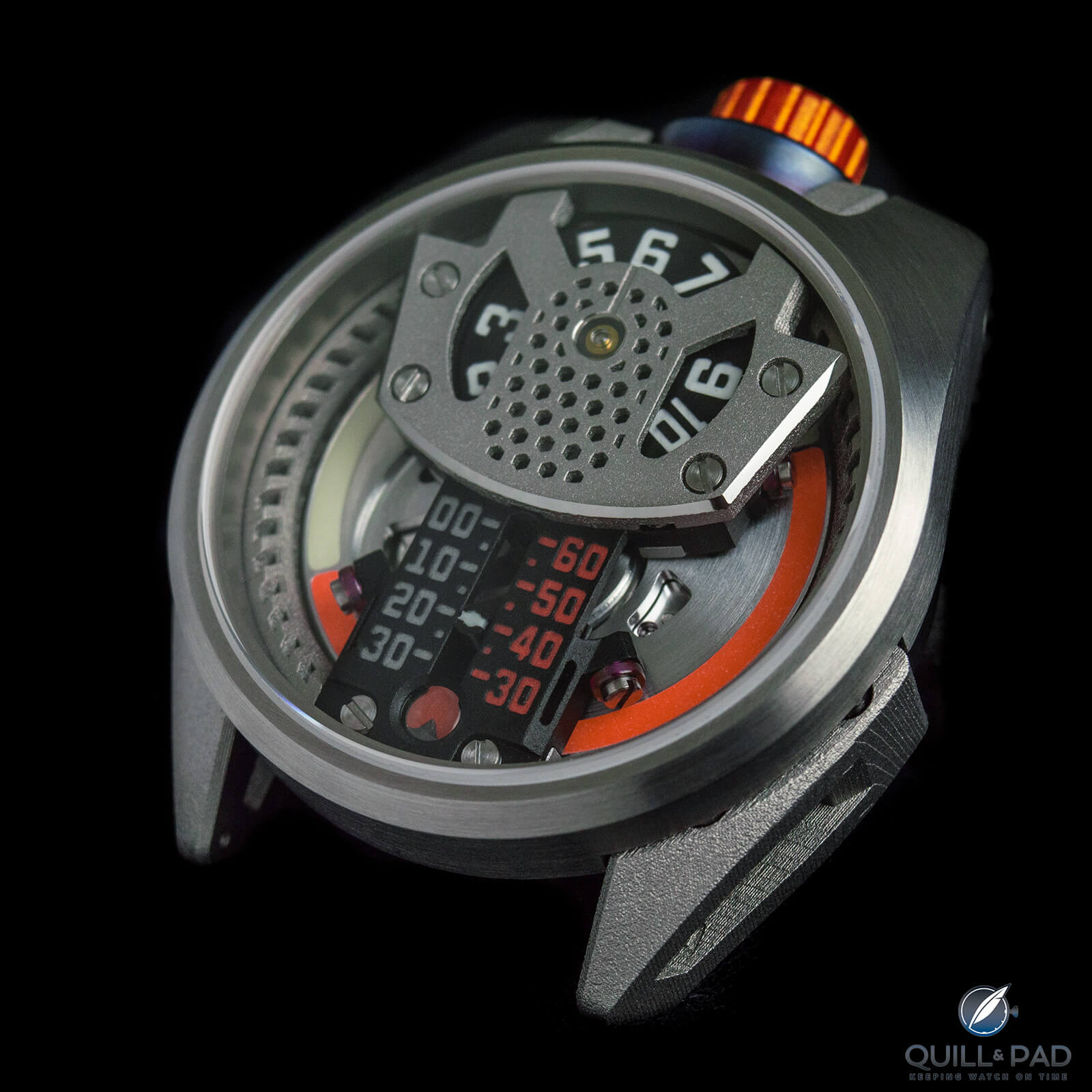
Barrelhand P1
The style may not be for everyone, though, and the price definitely is a bit hard to swallow considering the lack of high-end finishing. I’m assuming that the cost of development and the fact that it is manufactured almost exclusively in the USA in very small quantities also adds to the cost, but collectors may balk at the value proposition.
Since almost everything I love is out of my price range anyway, cost isn’t a factor in my personal enjoyment of this watch. But I could see it being a sticking point for potential clients for this piece.
The reception so far has seemed strong so perhaps a future might include a higher level of finishing (while still keeping the raw aesthetic of the metal binder jet steel parts) at a more economical cost to appeal to a wider range of potential clients. The inspiration is definitely there, and the development of a brand-new module is very impressive considering development in the U.S. A. As always, time will tell.
I urge you to check out Bachand’s work and dig deeper into the development of the P1, which is documented via the Barrelhand Instagram account. This is a great example of the future of small independent watchmaking: passionate individuals taking on a serious goal of making something incredible.
Now that I’ve built it up, let’s break it down!
- Wowza Factor * 9.4 It’s not every day that a new brand pops up that hasn’t just outsourced some fairly standard components in a unique color but actually developed its own module and avant-garde case!
- Late Night Lust Appeal * 94» 921.825m/s2 Serious late-night lust for this piece; after watching for six years it’s not only finally here but awesome to boot!
- M.G.R. * 62 Solid base movement powering a brand-new American made module developed right over in Silicon Valley!
- Added-Functionitis * N/A The effort was clearly placed on unique time displays (a common theme in watches I love) so no need for Gotta-HAVE-That cream even though the function is increditastic as it is!
- Ouch Outline * 10.4 The crick in your neck that moves to your back after sleeping wrong! I’m no spring chicken anymore, it seems, and some mornings the old bag of bones wants to remind me that I’m still not in charge, and it hurts something fierce. Though I’d gladly wake up like that for a month if it meant getting this watch on my wrist!
- Mermaid Moment * It’s finally here (AKA six years)! When you watch something slowly being birthed over a long period of time, you fall in love the whole way through, so it could be said to be instantaneous affection but it was, in fact, the entire process!
- Awesome Total * 906 Take the number of pieces in the limited edition (20) and multiply by the case diameter (44), then add the number of jewels (26) for an inspiringly new awesome total!
For more information, please visit www.barrelhand.com.
Quick Facts Barrelhand P1
Case: 44 x 15 mm, titanium and binder jet-printed steel
Movement: modified manual winding Eterna Caliber 3901M with American made linear minutes and Geneva wheel-driven hour module, 28,800 vph/4 Hz frequency
Functions: hours, linear minutes
Limitation: 20 pieces
Price: $30,000
You may also enjoy:
Bovet Récital 26 Brainstorm Chapter Two: It’s Mind Blowing! (Live Photos)
Focus On Technology: 3D Printing, What Is It Really?
Focus On Technology: 3D Printing, What Is It Really? Part Deux
The Panerai Lab-ID Luminor 1950 Carbotech 3 Days With 50-Year Guarantee!
Leave a Reply
Want to join the discussion?Feel free to contribute!
Interesting article! Amazing how 3D printing is getting so precise that movement parts are beginning to be 3D printed as well. Another brand that is pushing the 3D printing boundaries and using the tech to play with case shapes is Holthinrichs Watches, I hope you guys can do a bit of coverage on them here on Quill and Pad, and also perhaps a follow up on the detailed “3D Printing, What is it Really?” articles that you guys did several years ago to see the progress the technology has made since then!
comprar Um