Why I Bought Them: Custom Aventurine-Dial And Blue Enamel-Dial Watches From Lundis Bleus
“Caution! The oven is very hot, watch out.”
The “oven” here is actually a kiln and “very hot” is 830° Celsius.
Squinting at a safe distance through the small inspection hole in the door of a small kiln, I decided it was as hot as hell inside, and even from where I stood it felt like it too.
The hottest temperature I happily work at is 220° Celsius once a year when I succeed in making a cake. Bastien Vuilliomenet, however, is able to create beautiful watch dials at about 830° Celsius as if it were nothing special. His work immediately caught my attention: rare traditional craftsmanship combined with mechanical watchmaking. That is a combination hard to resist.
So I went to Neuchâtel to discover enameling, the artistic craft and territory of Bastien Vuilliomenet, owner and proprietor of Lundis Bleus.
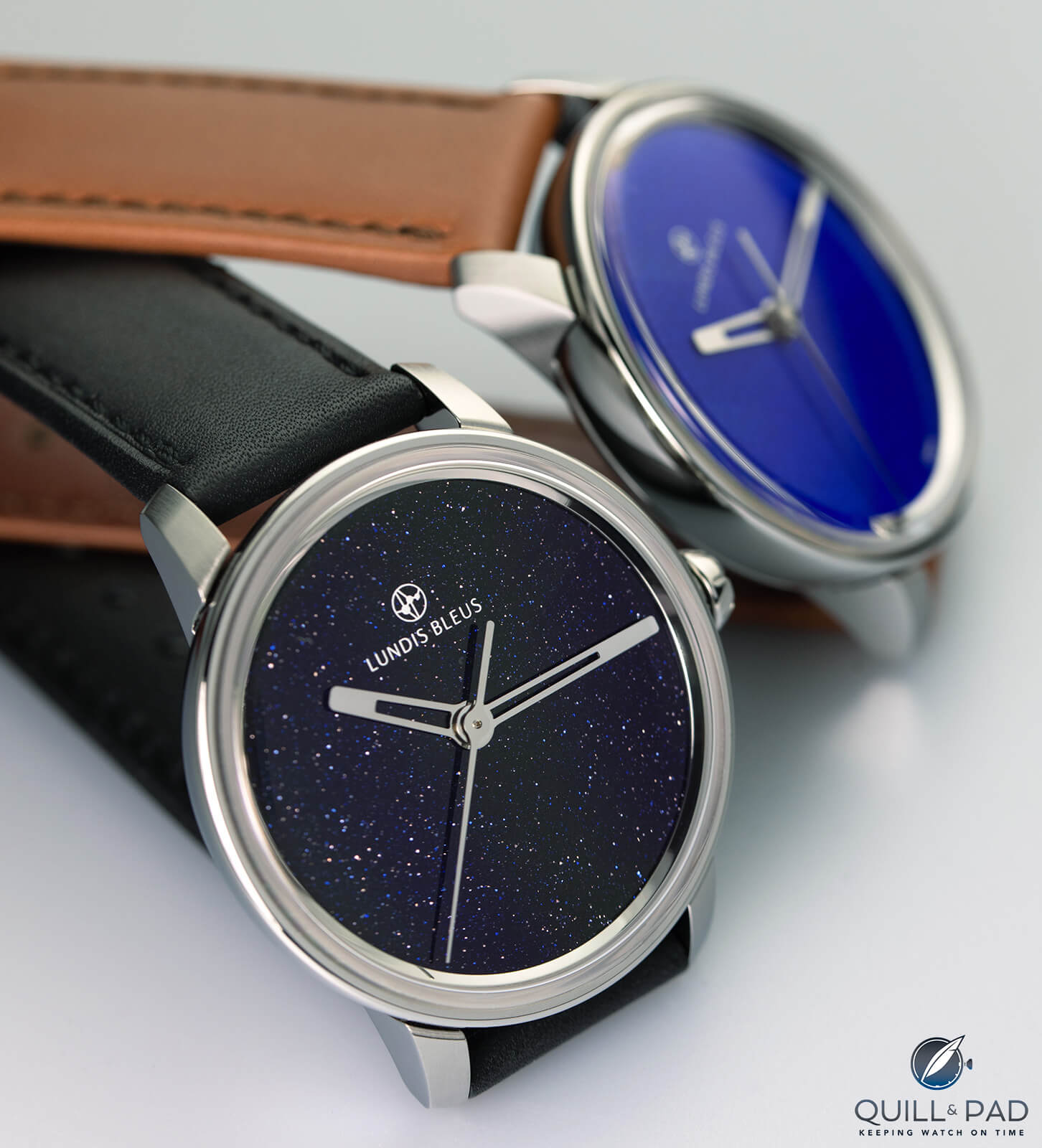
The author’s custom Lundis Bleus aventurine and blue enamel watches (photo courtesy Lundis Bleus)
And I discovered that the air in his workshop is filled with “meet the maker, buy the watch,” as GaryG would probably say.
The Lundis Bleus arts and crafts are a very special aspect of watchmaking. It is not so much about the mechanical side – escapements, micro rotors, gearwheels, and gold chatons – but more the artistic and aesthetic (dial) side of independent watchmaking. We all usually look at our watches from the dial side first, so it stands to reason.
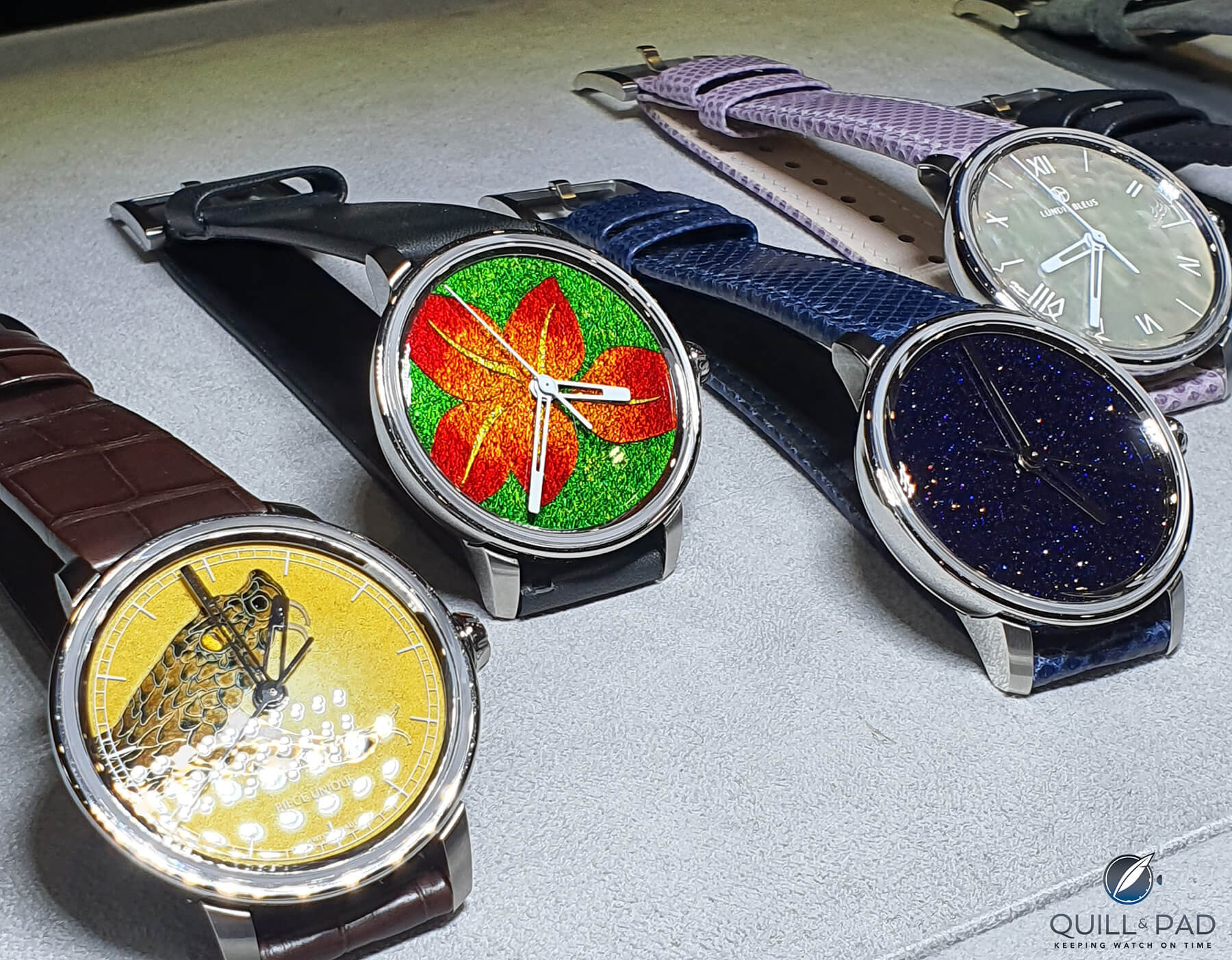
Lundis Bleus watches (photo courtesy Thomas Brechtel)
Lundis Bleus must have at least 100 psychedelic dials with the most beautiful patterns, materials, and colors to die for. The latest collection shown this year in Geneva at Time To Watches 2022 – which ran alongside Watches and Wonders in Geneva – is the microbrand’s Color Spectrum Collection, automatic Sellita 300-1-powered watches with the unique Lundis Bleus-designed stainless steel case and dials that come in seven different colors.
The dials are crafted in high-fire enamel in red, orange, yellow, green, cyan, blue, and violet over silver leaf. To decide on a dial color from this collection would be impossible for me: what can I recommend is all or nothing!
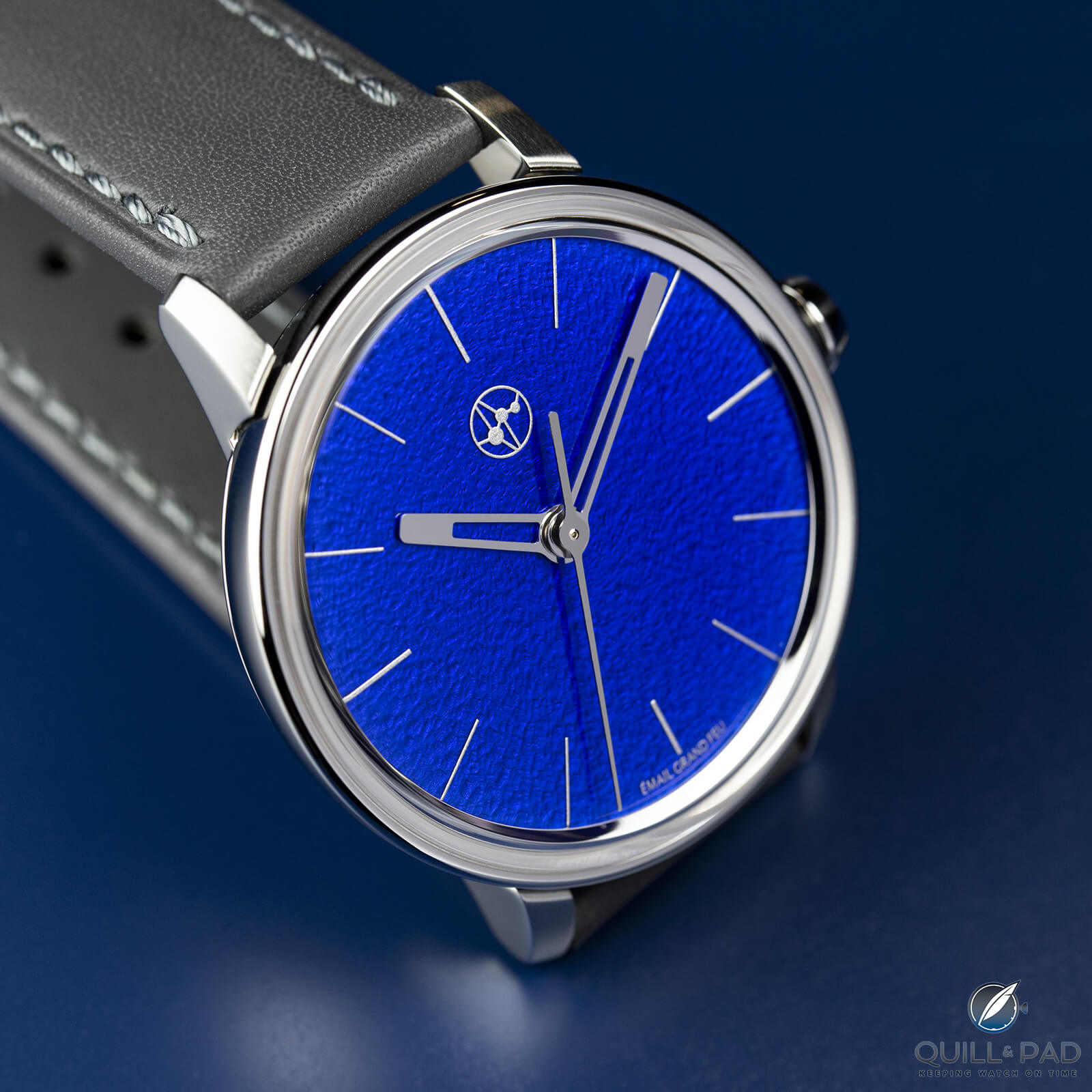
Lundis Bleus Royal Blue enamel watch
Melting glass and slicing and dicing stones
The work of Lundis Bleus lies mainly in the field of grand feu enameling, cloisonné, and working with rare materials and stones like onyx, aventurine, tiger eye, malachite, and meteorite. But it is especially aventurine that has had huge appeal to me ever since I saw it there.
Aventurine glass, sometimes called goldstone (probably translated from the German Goldfluss), is mainly made in Murano using glass, copper, and cobalt. (For more on aventurine please see Aventurine: Sparkling, Glittering, Mysterious, And Placing A Galaxy Of Stars On Your Wrist.) These days, aventurine comes with sad side news: its production might end sooner or later due to the harmful substances used to manufacture it.
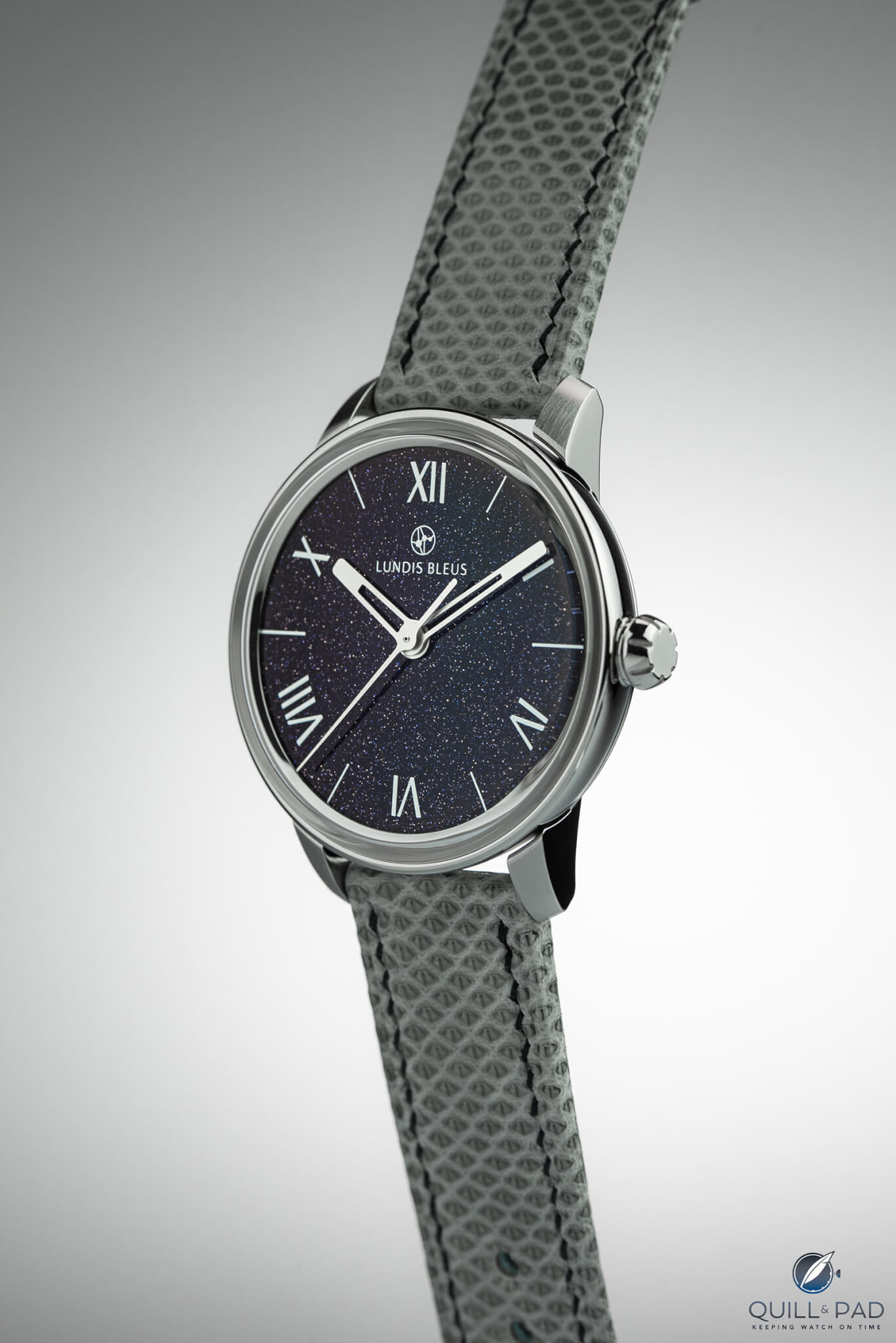
Lundis Bleus Blue Aventurine watch
Kiln-fired enamel
Enameling is more than 3,000 years old. The fine art of enameling nowadays is sometimes hidden like a professional secret – like the expert knowledge of many traditional arts and crafts. Artists do not want their competitors to know about or copy their skills and methods. But this means that enameling is in great danger of not being passed on to younger generations, threatening to become a bygone art.
It is so important that the old masters begin to document their knowledge and pass it on for the future. Many horological techniques should be documented. Incidentally, this is one of many tasks that the founders of HORO.PEDIA have set themselves as an objective for the future of their work as announced during Geneva Watch Days 2022. I heard Philippe Dufour saying at the launch of HORO.PEDIA, “The cemeteries are full of professional secrets.” Today, the art of enameling is present not only in Switzerland, but also in Japan, the United States of America, and Scotland.
The right temperature is a key element in enameling. A perfect result requires a high temperature of 800 to 830° Celsius and a short firing time. During firing and cooling in the kiln, the enamel changes color, which can make for a good or a bad surprise. Usually gold, silver, or a copper-silver alloy is used as the base material for the dials, with Lundis Bleus also using gold and/or silver leaf.
For the watches of the Color Spectrum Collection and also for his cloisonné dials, Vuilliomenet has chosen to use transparent vitreous enamel over gold leaf. According to the artist, the Lundis Bleus dials “go through the firing process an average of six times but can go up to 15 times.”
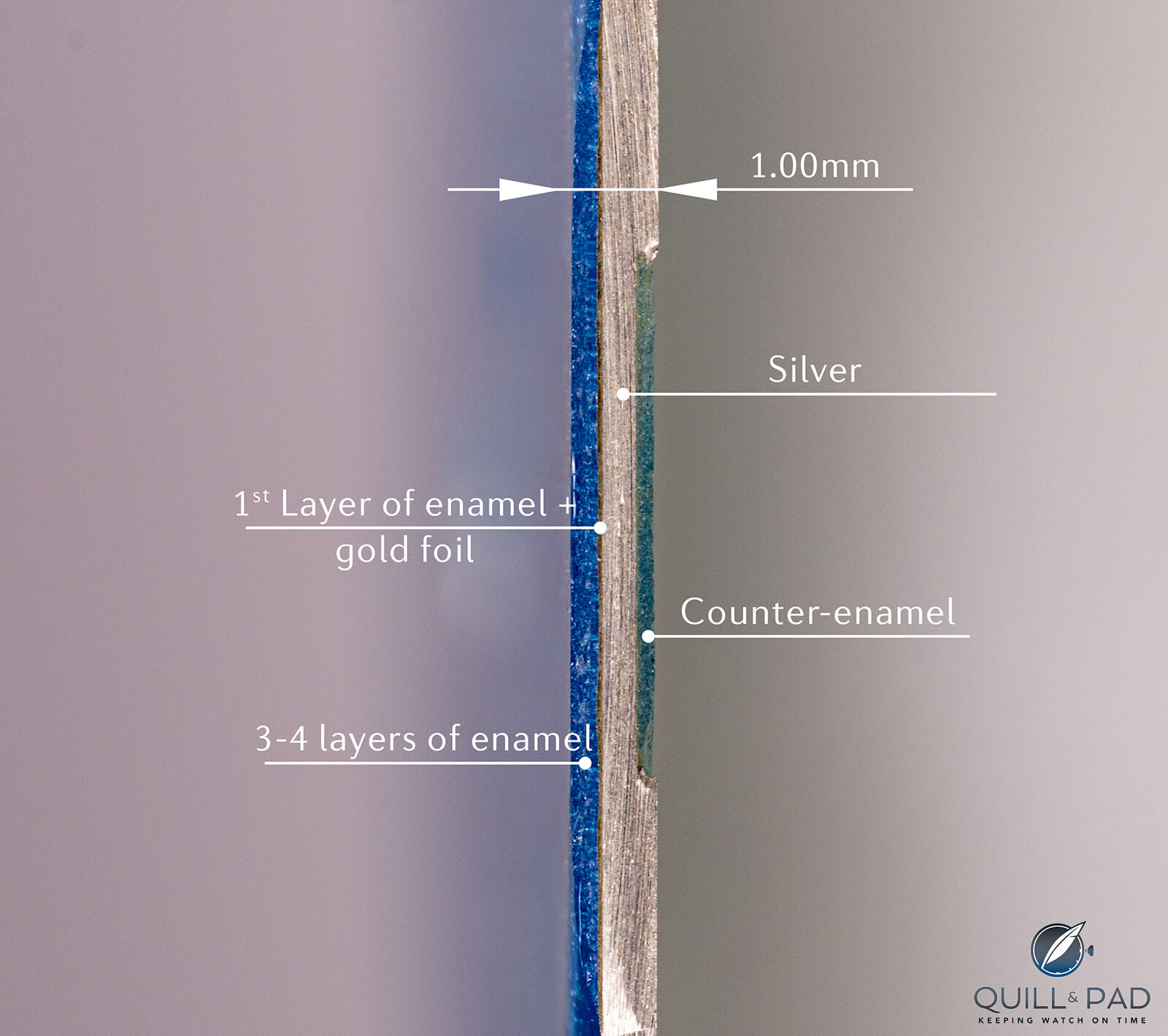
Cross section of an enamel dial according to Lundis Bleus (top of dial at left)
A basic fact I learned from Vuilliomenet right from the beginning is, “Every enamel needs contre–émail (counter enamel).” Enamel is a glass mixture that melts. The raw material comes in the size of hard candies, which has to be ground by hand to fine powder in as regular-sized grains as possible for a perfect result. The grains have to have the same size in order to prevent bubbles or imperfections while in the kiln.
To avoid distortion or cracks in the metal dial blank, counter enamel is needed. The enamel layer on the front is more brittle than the metal underneath, which means that it can crack or burst. Therefore, the enameler has to match the properties of the enamel exactly to the material of the dial and the purpose.
At this point, many unusable results occur – rejects – especially if the enameler is less experienced. If the color pigments do not melt properly, it may be that the kiln temperature is even slightly too high (enamel has a lower melting point than the dial blank). If the pigments burn, the resulting dial is almost always unusable.
The most exciting, but also the most difficult, moment in enameling begins when the object goes into the kiln for firing at about 830° Celsius. “Once the door is closed, there is nothing you can do,” Vuilliomenet explained to me. “It’s inhumanly hot. You can’t use your hand again to correct anything. If you think of anything you might want to correct, you can only do it anew from the beginning.”
Cloisonné on the wrist
Cloisons are individual cells created one by one from fine gold threads forming the many borders of the whole motif. The resulting areas are filled with enamel. This creates motifs that look like small, shiny, glossy paintings.
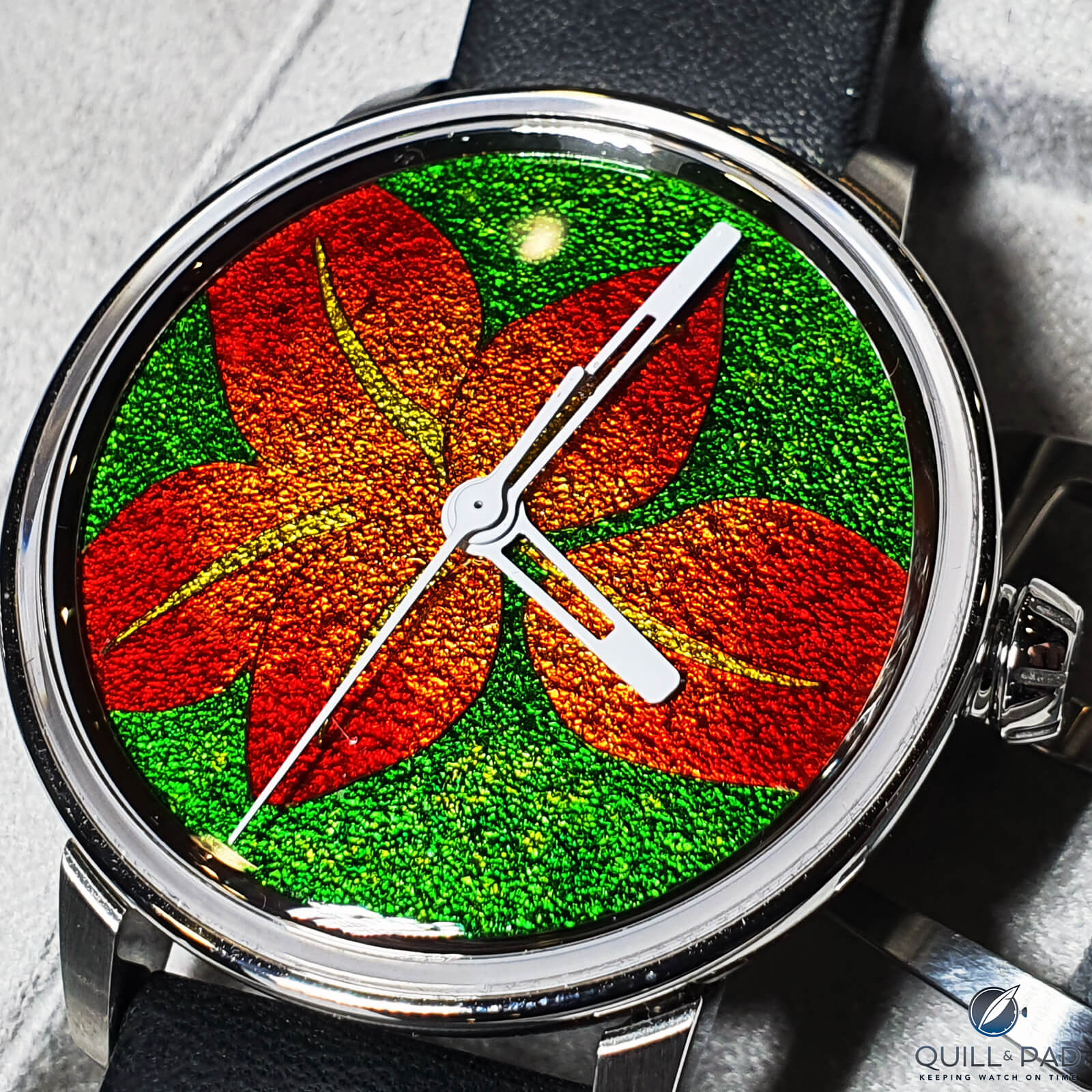
Lundis Bleus cloisonné enamel flower dial watch (photo courtesy Thomas Brechtel)
Lundis Bleus’ snake (seen in the second photo from the top) is such a dial painting. It was a unique piece made for a customer and took at least four long weeks to manufacture. During the creation process if something were to go wrong or Vuilliomenet was not satisfied with the result, everything would have to start all over again.
The Lundis Bleus unique pieces are usually special wishes or individual ideas from a customer who brings in the basic image for their unique dial. The realization of the dial and of the complete watch is then done together with the customer. Beauty comes at a cost: prices can be as high as five digits.
“A share of 30 percent of all dials will not find the way to a watch because of imperfections in the stone or the enamel,” Vuilliomenet says. Those who like old pendulum clocks and pocket watches or appreciate rare wristwatches with enamel dials (perhaps by Jaquet Droz, anOrdain, or Patek Philippe) know that enamel can last for centuries. Enamel dials are among the most long-lasting dials compared to varnished or lacquered surfaces.
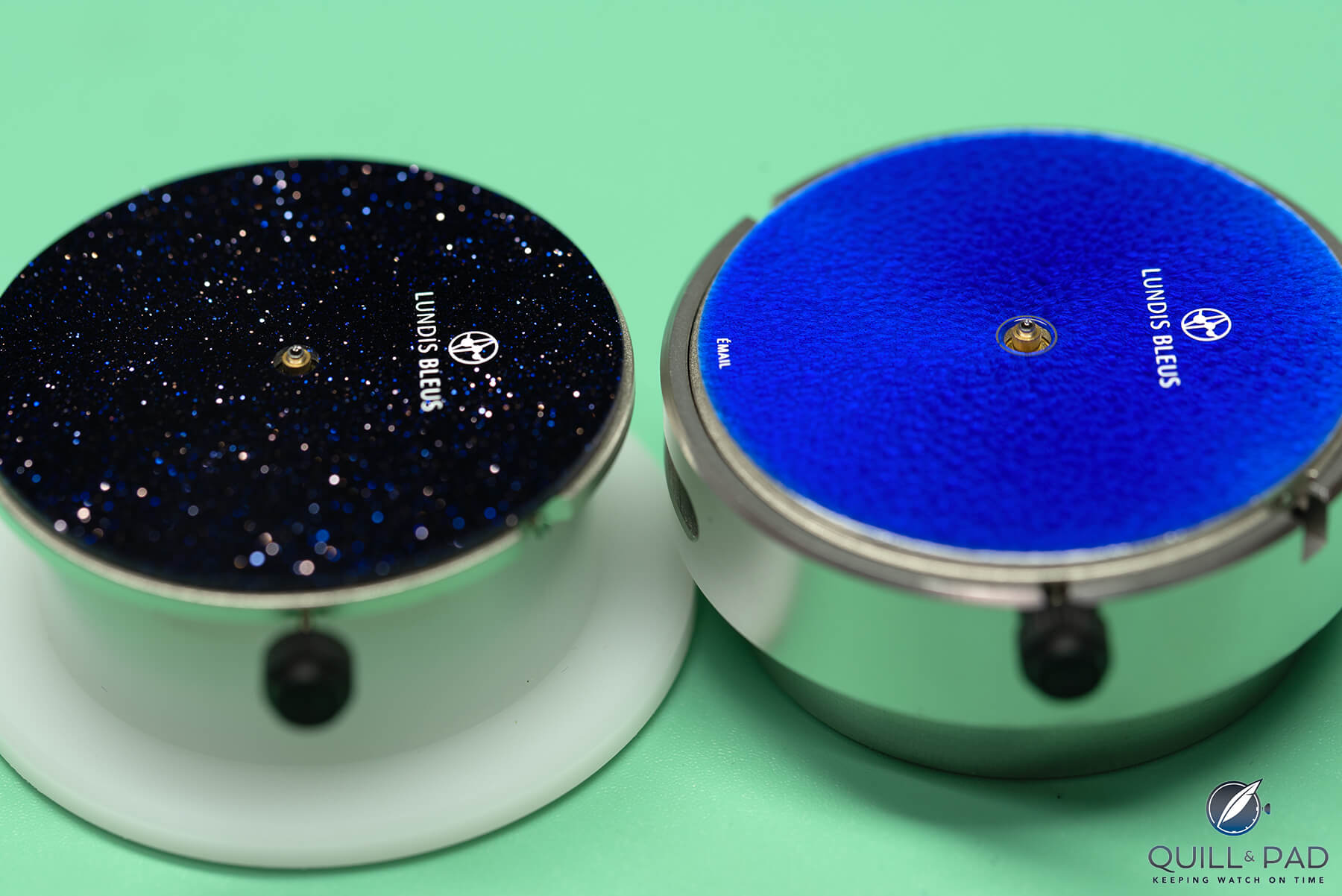
The author’s custom Lundis Bleus aventurine and blue enamel dials (photo courtesy Lundis Bleus)
“Nothing is more beautiful than a flawless enamel dial, but nothing could be worse if this dial is cracked or has chips,” Vuilliomenet added. I remember that it took years for A. Lange & Söhne to produce all the enamel dials for the Sax-o-Mat platinum Anniversary Langematik that came out in 2007. The process is very long and delicate.
There are easier ways to make a dial, but some makers like Vuilliomenet are dedicated to this old craft. As a result, the dial production is very limited, but always worth the effort.
Pad printing the Lundis Bleus dials
Almost all watches and dials made by Vuilliomenet for his Lundis Bleus brand today have a uniform core design. Vuilliomenet does the artistic pad printing of the dials himself in his workshop: these show the Lundis Bleu logo, the brand name, occasionally a reference to the dial material (“Email,” “Email Grand Feu”), and simple markers for the hours or a mixture of Roman numerals and markers if any.
A range of colors is available for the printing. Vuilliomenet thus counteracts too much inconsistency in his brand’s corporate image, which can come from too much individualization and even sometimes the desired imitation of other well-known designs, which can quickly lead to the core of a brand not being able to develop.
A too high degree of customization may lead to a confusing variety of special series. A brand needs to be recognizable, and disregarding this is not positive or helpful for the development of brand identity. This may disappoint some people, but it helps immensely to form the brand’s identity.
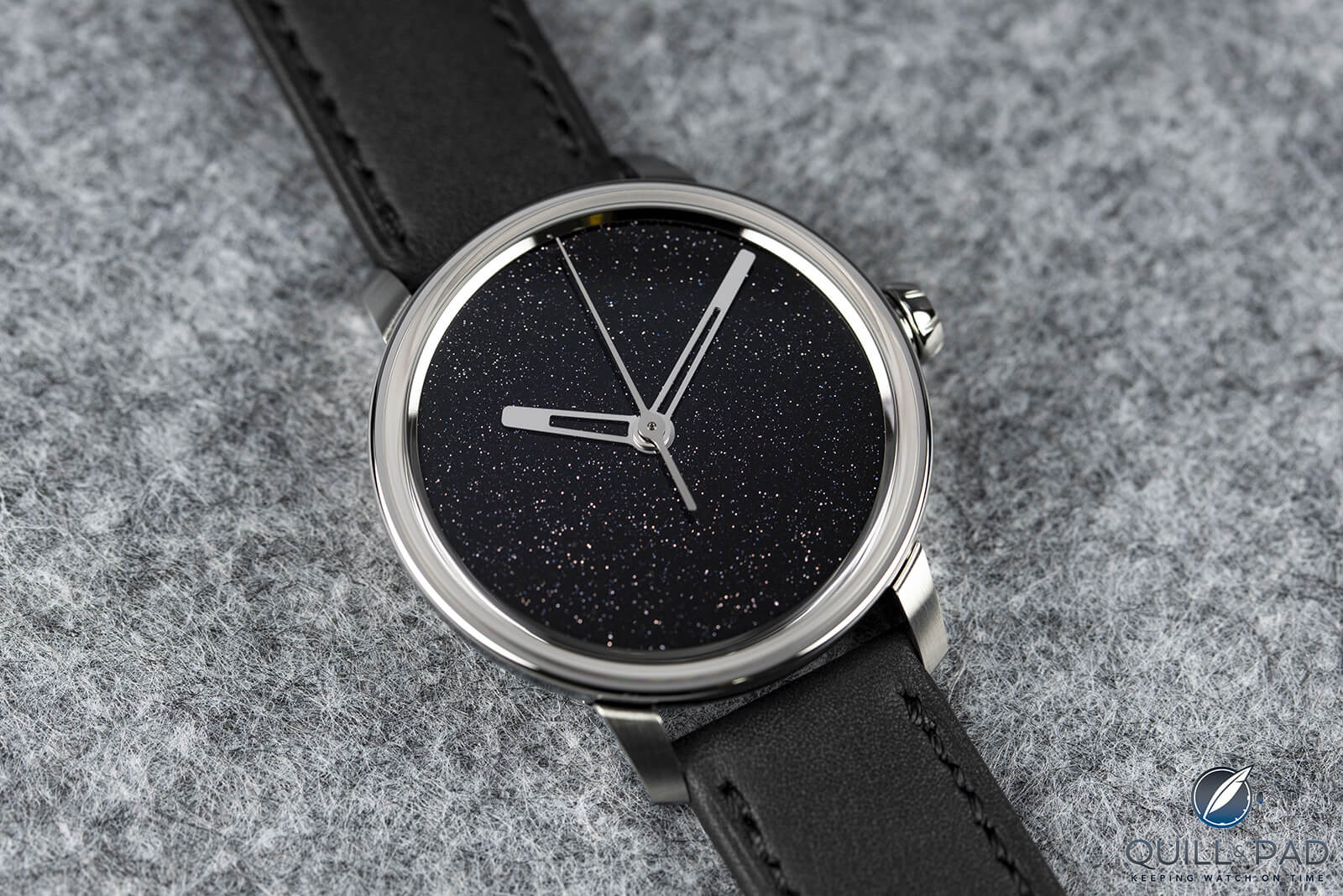
Lundis Bleus aventurine-dial watch
Who is Bastien Vuilliomenet and Lundis Bleus?
Lundis Bleus (French for “Monday Blues”) was founded by Johan Storni and Bastien Vuilliomenet in La Chaux-de-Fonds. Since August 2021 Vuilliomenet has run Lundis Bleus alone. The workshop is located in a beautiful Neuchâtel city house.
Vuilliomenet started his career as a watchmaker, and until 2010 he worked as an industrial/watch designer (e.g., for Corum from 2008 through 2013). After working as a product manager for private label company Roventa-Henex, he has become an experienced enameler working on the trust of his own intuition now for more than ten years.
Vuilliomenet and Lundis Bleus are known by a few enthusiasts and watch lovers mostly because of the stunning artistic enamel dials. One of the most fascinating pieces for me is the aforementioned Viper, a unique cloisonné artwork showing the head of a snake on a sand-colored dial.
Everything together makes a watch from Lundis Bleus
What turns a Vuilliomenet dial into a wristwatch? Lundis Bleus works with about 15 partners who supply the movements, cases, gaskets, sapphire crystals, hands, crowns, bracelets, buckles, and other parts. All Lundis Bleus watches now have automatic Swiss made movements by Sellita (Caliber 300-1, premium quality).
The polished stainless steel 316L case with brushed lugs is a Lundis Bleus design. The lugs of the 40 mm case do not touch the case itself, but are part of the case back in a very special construction.
A large stamped Lundis Bleus logo shaped like an alcohol molecule acts as the case back. Looking at the watch from the back one notices that the movement is not the focus of attention. But that should be clear anyway: the fascinating art of Lundis Bleus takes place on the dial side.
It is important to note that Lundis Bleus watches do not have a date window. I am very happy about it, but people who prefer a watch with high everyday usability might not be.
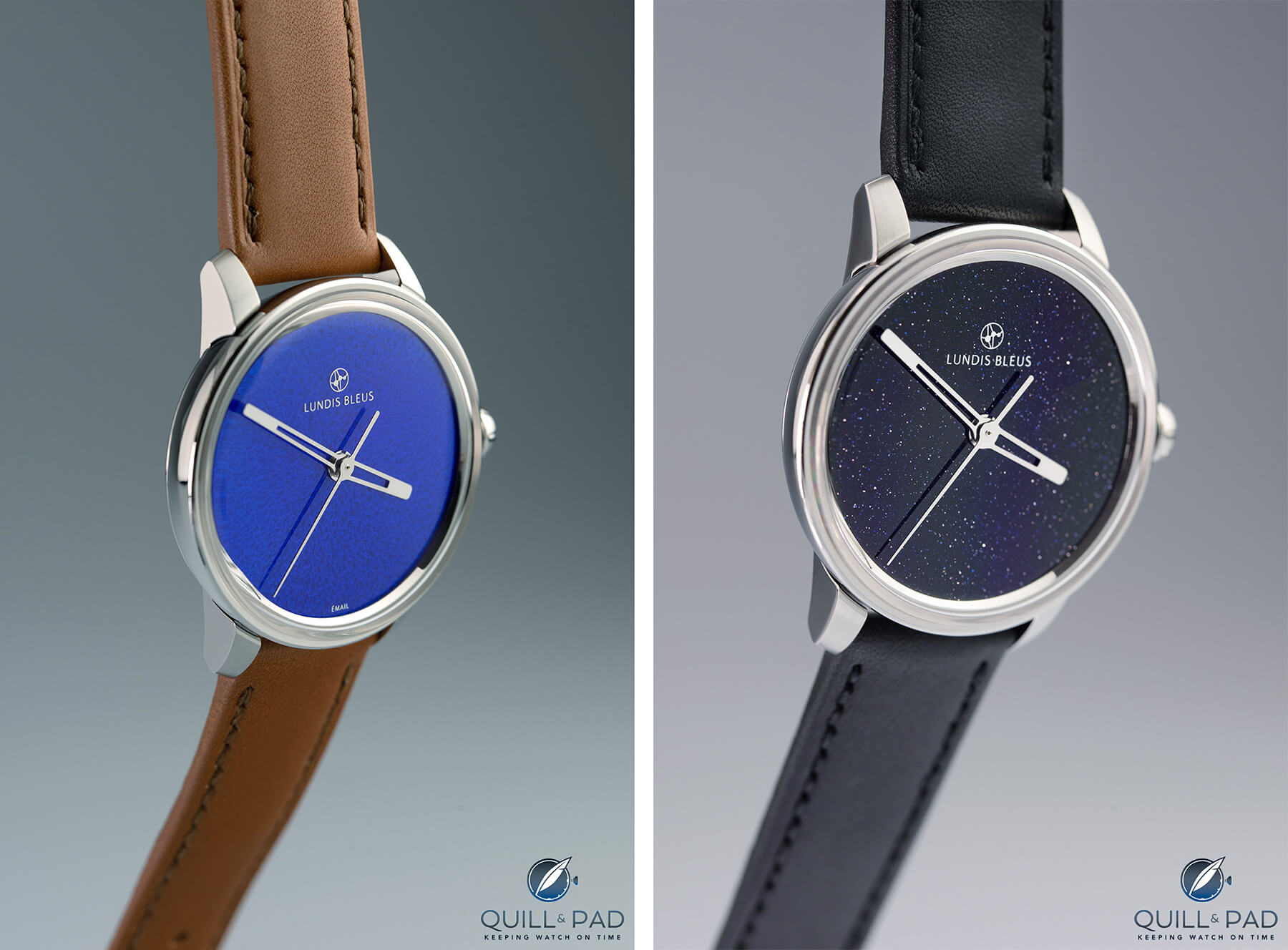
The author’s custom Lundis Bleus aventurine and blue enamel watches (photo courtesy Lundis Bleus)
Why I chose an aventurine dial
By now, some of you might be asking, “Why would anyone ever buy an aventurine-only dial?” Can there really be reasons to do that? People probably make most of their decisions emotionally – and if societal conditions make it necessary, they try to justify it rationally.
This sounds strange, but that’s the way it is. From an emotional point of view, an aventurine dial is too beautiful to let go. That could be the whole answer for me.
But for anyone who needs more reasons to make such a decision, I can still offer a few:
You are nuts.
You have much admiration for the craft.
You know that it is a rare (diminishing or vanishing) material in watchmaking.
You cannot afford a cloisonné dial.
You want to support the maker.
You cannot decide on one single color of the Color Spectrum Collection.
Lundis Bleus’ prices start at about CHF 3,900 (for a black or blue aventurine dial watch), but can go up to CHF 5,200 for a meteorite-dial watch and end at five-digit numbers for unique pieces (before tax).
For more information on Lundis Bleus, please visit lundis-bleus.com.
You may also enjoy:
Lundis Bleus: Relatively Affordable Swiss Independent With Eye-Catching Enamel And Engraved Dials
Watch Customization: Give People The Watch They Want
Aventurine: Sparkling, Glittering, Mysterious, And Placing A Galaxy Of Stars On Your Wrist
Oris Aquis Sun Wukong Artist Edition: Creating An Uproar (In Heaven)
Leave a Reply
Want to join the discussion?Feel free to contribute!
I almost thought it was my adventurine dial LB that was used for the article until I noticed my name wasn’t at the bottom of the dial! The adventurine dial was actually made by the renknowned dial maker Daniel Haas, who also makes dials for many of the premium watch brands.
Thank you Mark for mentioning Daniel Haas (Haas Cadrans; Pieterlen near Biel, CH). A craft and a company that also needs attention – similar to Bastien Vuilliomenet – when we appreciate rare material and craft in and for horology. You have a very good taste. My initial interest was caught by Bastien Vuilliomenet’s craft of enameling. As a ‘side-effect’ I came along Aventurine in his workshop, which he also uses for the Lundis Bleus watches. The sparkling effect of this material is fascinating.
Many thanks for the compliment. Actually I upgraded my first generation LB Ref 1105 to the aventurine! I have a special connection to LB as I was the first person to buy a watch from their then newly launched webshop, and the brands connection to alcohol was why I bought it to celebrate my first anniversary of having gone dry! I love what Bastien is doing with enamelling and I sometimes think maybe I should have got an enamelled dial, but there’s something about really good quality Aventurine that makes it so special, and especially with Daniel adding his exceptional skill. I also own a Jaquet Droz with a black onyx dial that was also made by Daniel. You can find them on my IG @watchcrazyham
I absolutely agree with you Mark. There are incredibly beautiful types, materials and artists who make and design dials – and we usually look at watches exactly from that side, from the dial side. That would really be worth an article: what kinds of handcrafted special dials are there, who makes them, who uses them … that would be a really big task. HOROPEDIA (https://horopedia.org/) comes directly to mind : )