The Horological Elegance of Skeleton Watches
Not just time-telling devices but miniature works of art, skeleton watches blend mechanical complexity with architectural elegance.
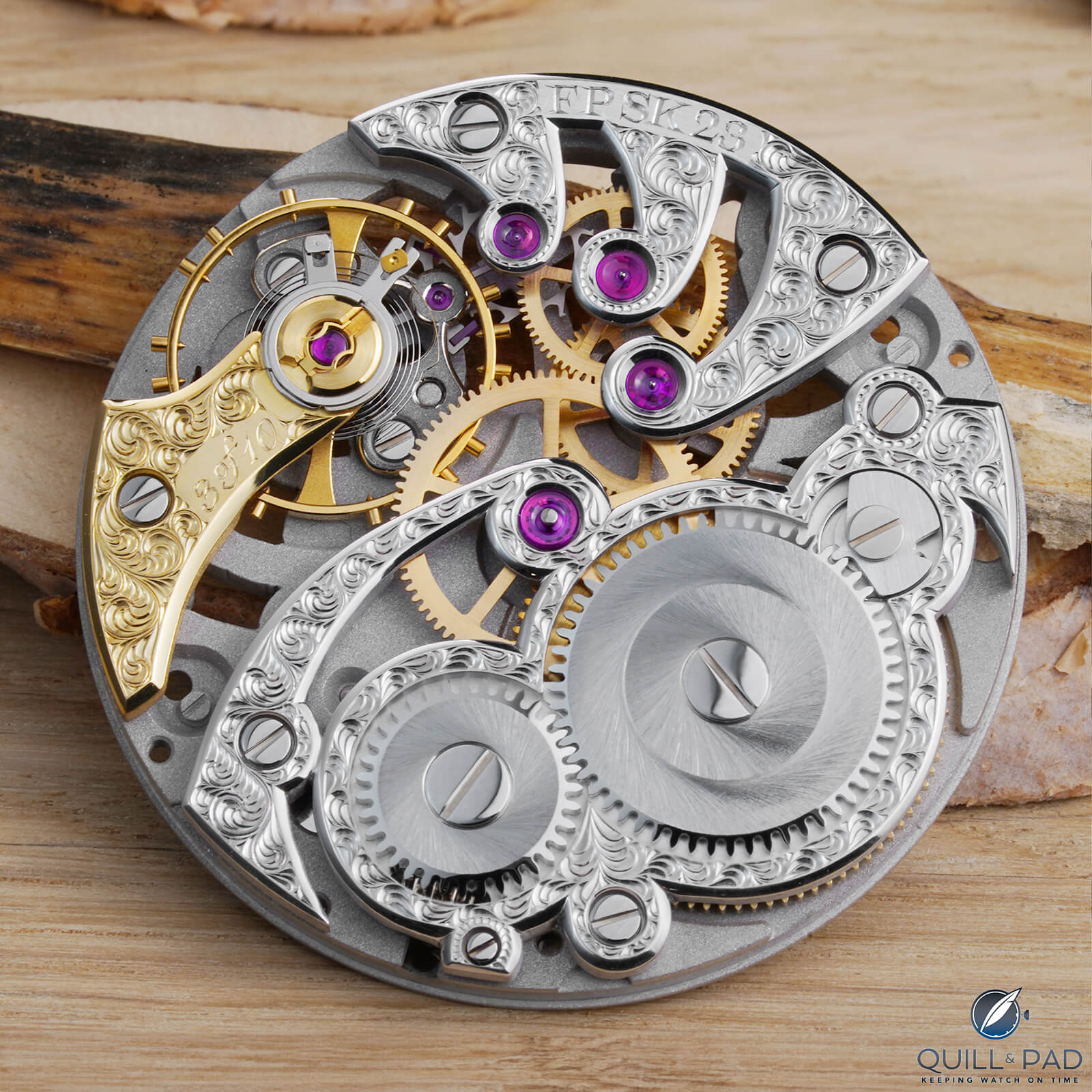
Felipe Pikullik caliber FPSQ23
André-Charles Caron created the first skeleton watch in the 1760s. Born in 1698, Caron was a master clockmaker who worked at the court of King Louis XV of France. He was the son of a watchmaker and later became the father-in-law of another famous French clockmaker, Jean-Antoine Lepine, whose contribution to horology, which preceded Caron’s invention by a few years, was the simplification and considerable slimming of pocket watch movements.
This contribution opened the way to further miniaturization and the development of the modern watch.
Due to the influence of humanistic trends such as Illuminism, Caron had the idea of rendering the inner mechanics of pocket watches visible by removing the dial and skeletonizing the movement. This was the birth of skeleton watches, the ultimate form of minimalism and craftsmanship in watchmaking.
Skeletonized vs open-worked watches
In skeleton watches, the watchmaker removes any non-essential metal from the movement, leaving behind a skeleton of its components (e.g. bridges, mainplate, wheel train, etc.).
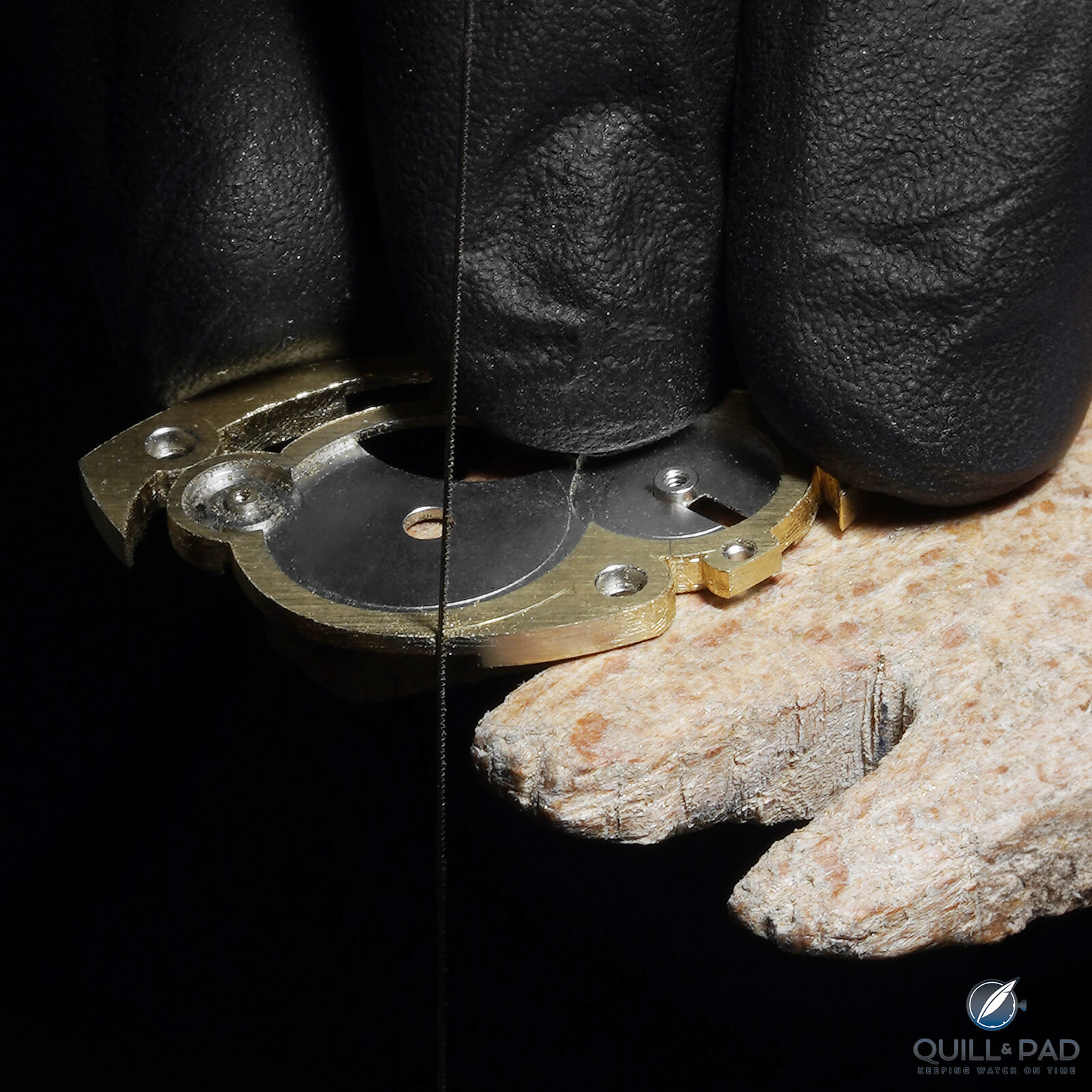
Hand skeletonizing a Felipe Pikullik movement plate
Skeletonization requires several long hours of patient and painstaking chiseling and metal trimming by the watchmaker. This process continues until only the most essential parts of the movement are left, while ensuring that the resulting minimalism of the mechanics in the movement does not affect the structural integrity and reliability.
Luxury skeleton watches are meticulously hand-decorated with various motifs using techniques and special tools that are centuries old in tradition, such as engraving, embellishing, and polishing.
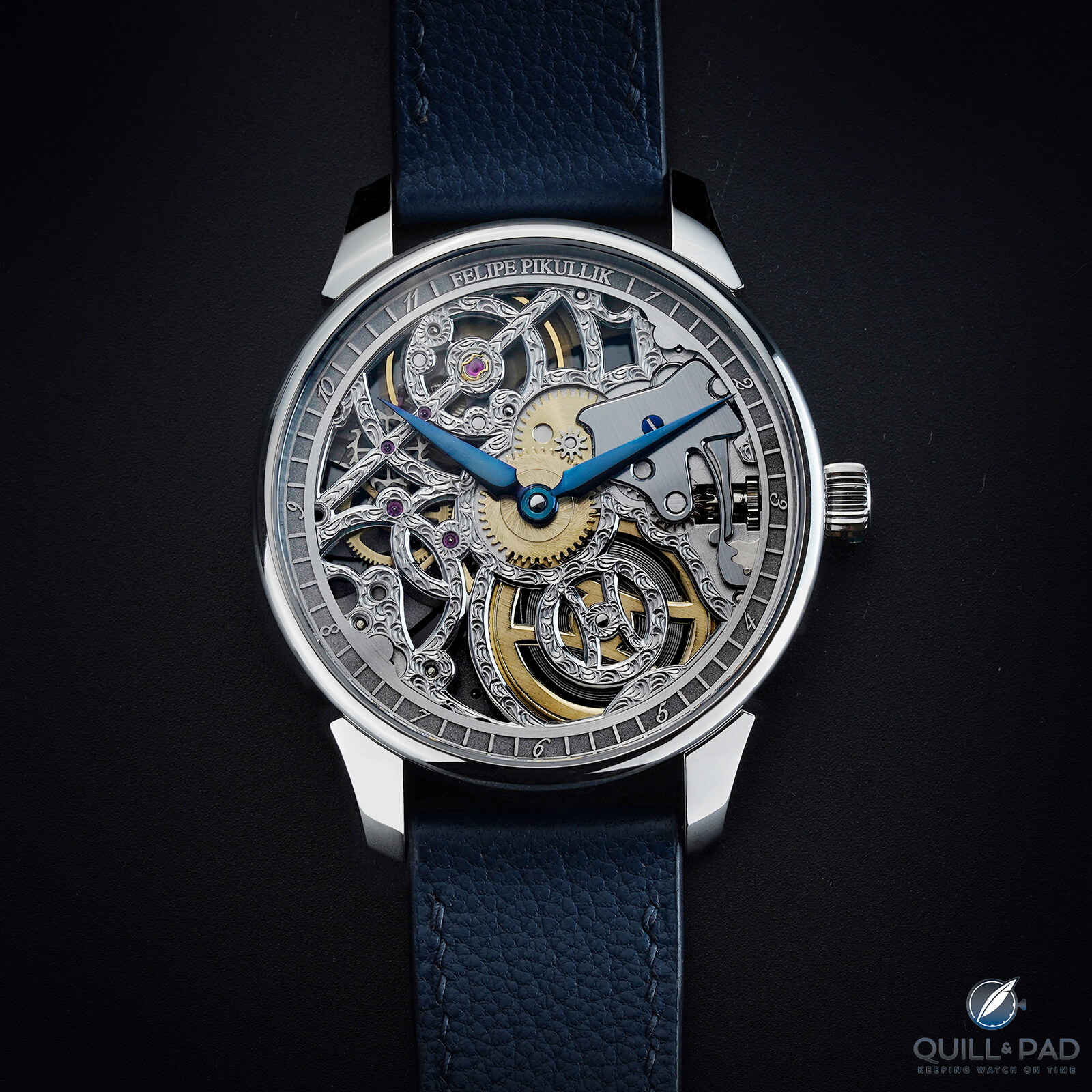
Ornately engraved Felipe Pikullik FPSK23
The purpose of skeletonization is to showcase exceptional craftsmanship and to reveal the fascinating elements of a movement such as the balance wheel, the mainspring, the escapement, and how they all interact together.
————————————————————————————————
————————————————————————————————
Openworked dials are the window to skeletonized movements. The skeleton of the movement becomes visible through the face of the watch as the dial, or sections of it, is removed.
Often, a transparent case back provides a view of the second face of the skeleton movement.
The revival of the skeleton watch
Following Caron’s time, skeleton watches lost popularity and became forgotten.
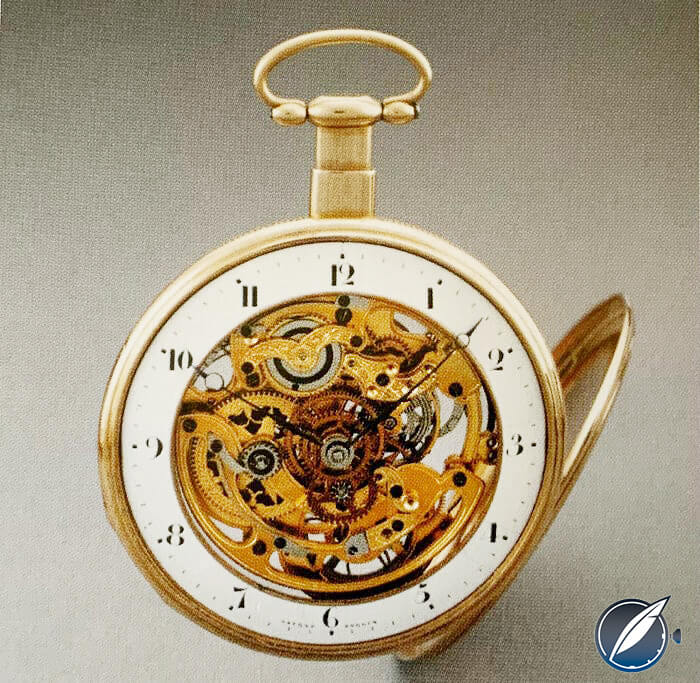
Samuel Frederic Ravené, Quarter-Repeating Pocket Watch (photo courtesy Musée International d’Horlogerie)
They were revived in the early 19th century when Samuel Frederic Ravené, watchmaker to the court of King Friedrich Wilhelm III of Prussia, created a quarter-repeating pocket watch with a skeletonized engraved movement visible through the transparent center of a white enamel dial.
In the 1860s, Patek Philippe produced a small series of skeleton pocket watches for exhibition purposes to showcase the brand’s horological savoir faire. These pocket watches were eventually commercialized starting in the late 1970s.
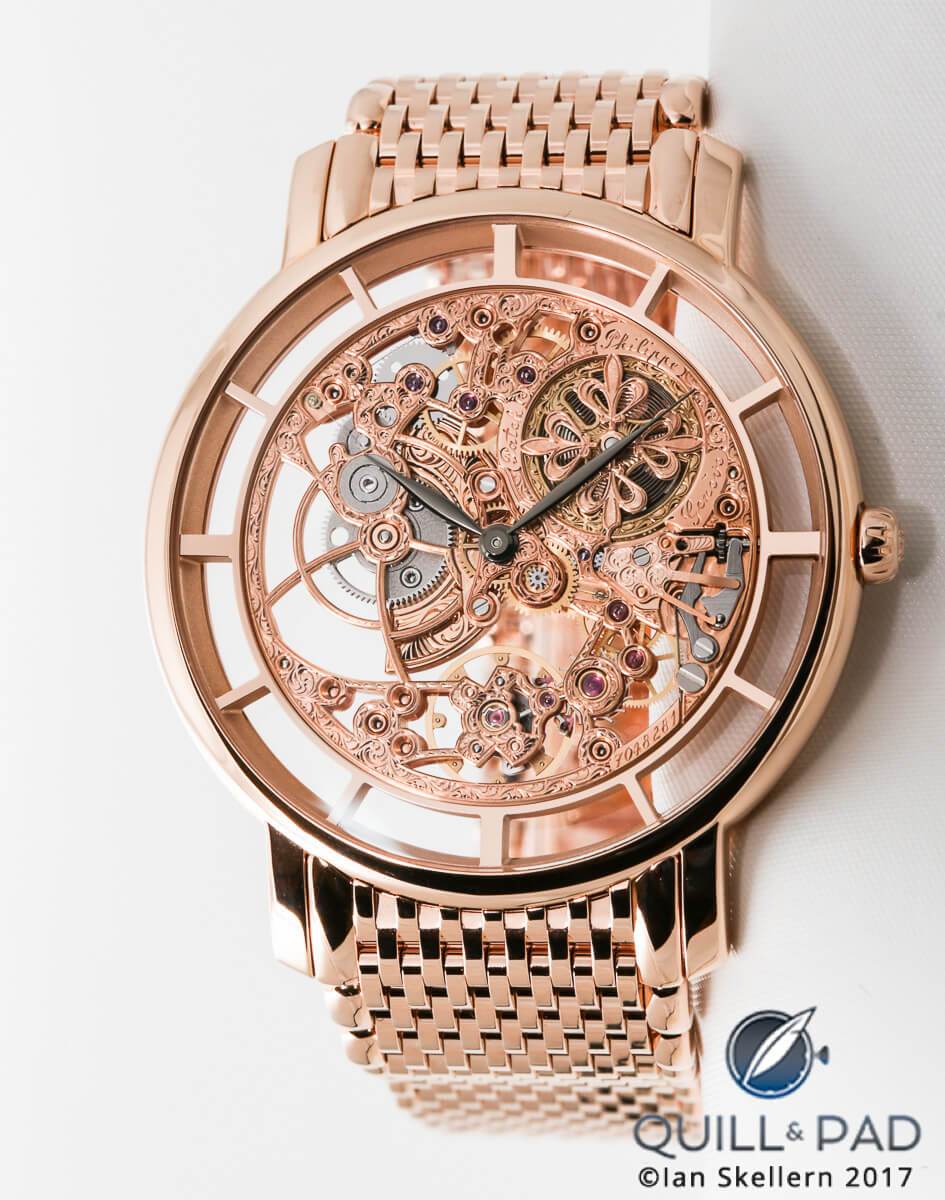
Patek Philippe Calatrava Squelette Reference 5180/1R-001
There aren’t many skeleton watches that pre-date the quartz crisis, which began in 1969 with the launch by Seiko of the Astron 35SQ. The quartz revolution drove several Swiss brands to reposition themselves to the higher end of the market shifting their focus from precision to technical creativity and luxury.
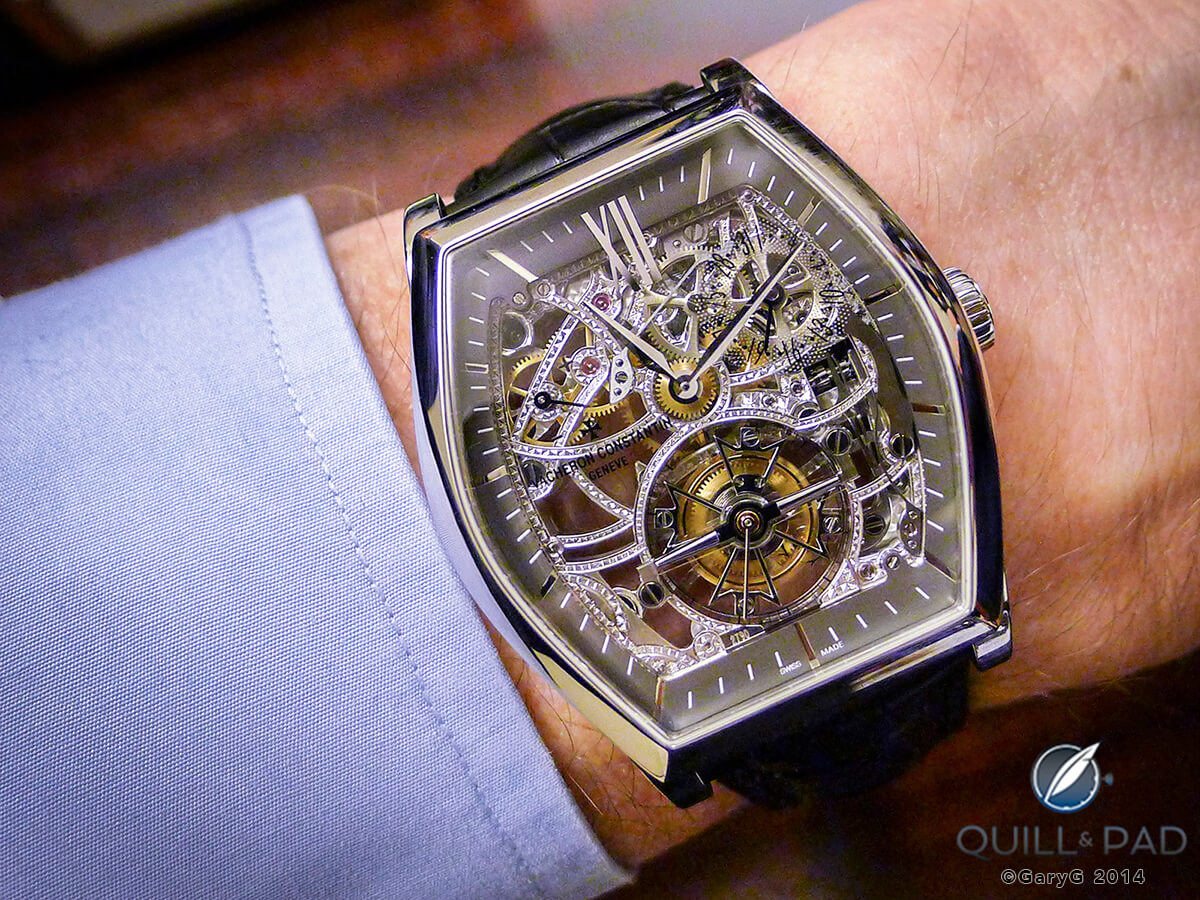
Vacheron Constantine skeletonized tourbillon
Since then, brands like Vacheron Constantin, Audemars Piguet, Patek Philippe, and Jaeger LeCoultre have become renowned for their ability to create skeletonized movements with intricate decorative motifs and elegant architecture.
Two approaches to creating a skeleton watch
The hand skeletonization of a movement is a rare craft and the result of a long and laborious process by a highly skilled and experienced watchmaker. The artisan-watchmaker starts with an existing movement and chisels material away to achieve the desired new layout.
The objective is to enhance the transparency and the aesthetic appeal of the inner workings of the watch without jeopardizing its functionality and reliability.
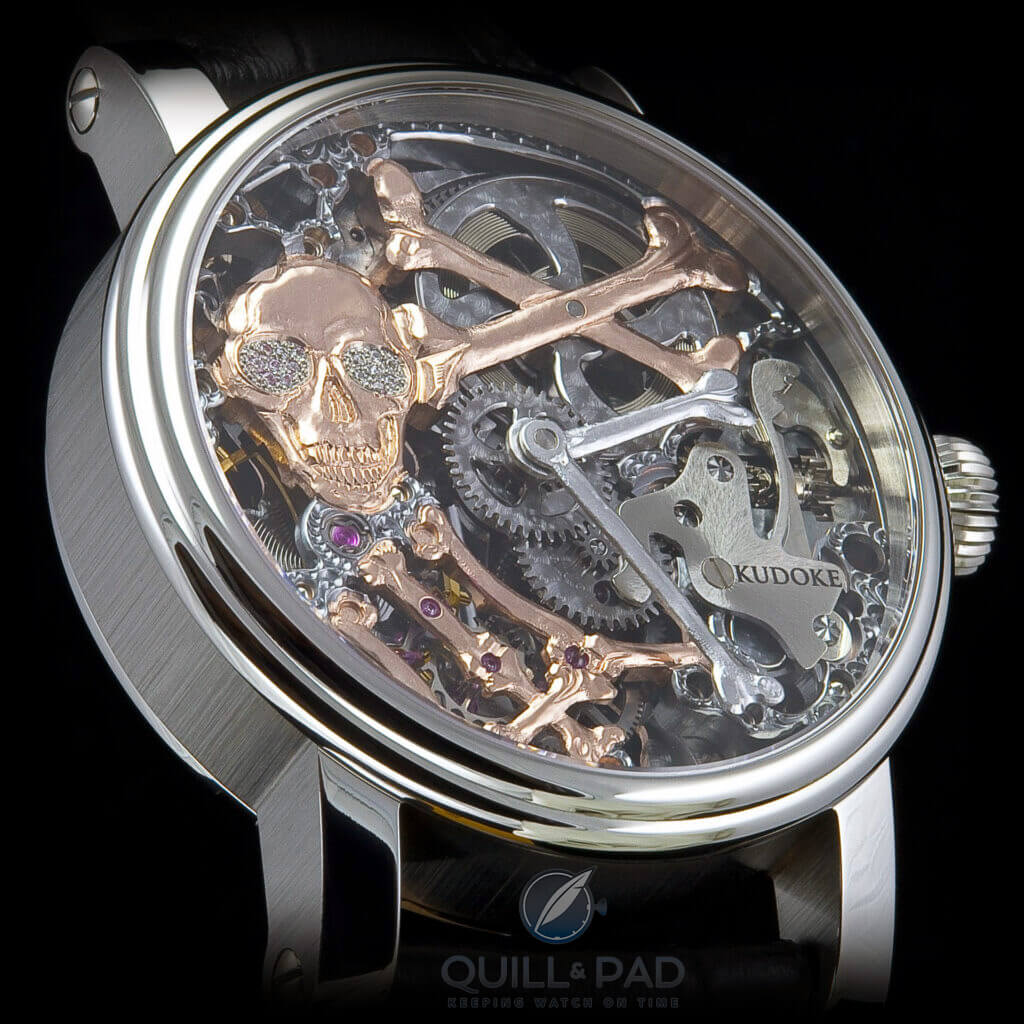
Kudoke Real Skeleton
Refinements such as decorations and finishing are often meticulously applied to the skeletonized movement. These will include intricate motif engravings, guilloché patterns (precise intricate and repetitive engraved patterns), Cotes de Geneve (straight line engravings), perlage (patterns of small overlapping circles), Rhodium plating, beveling and polishing.
————————————————————————————————
————————————————————————————————-
The engravings alone of the skeletonized Patek Philippe Calatrava required about 130 hours of artisanal work, as described by the brand on its website. The absence of a dial and the presence of a sapphire crystal caseback in the Calatrava Skeleton make it an exciting visual experience.
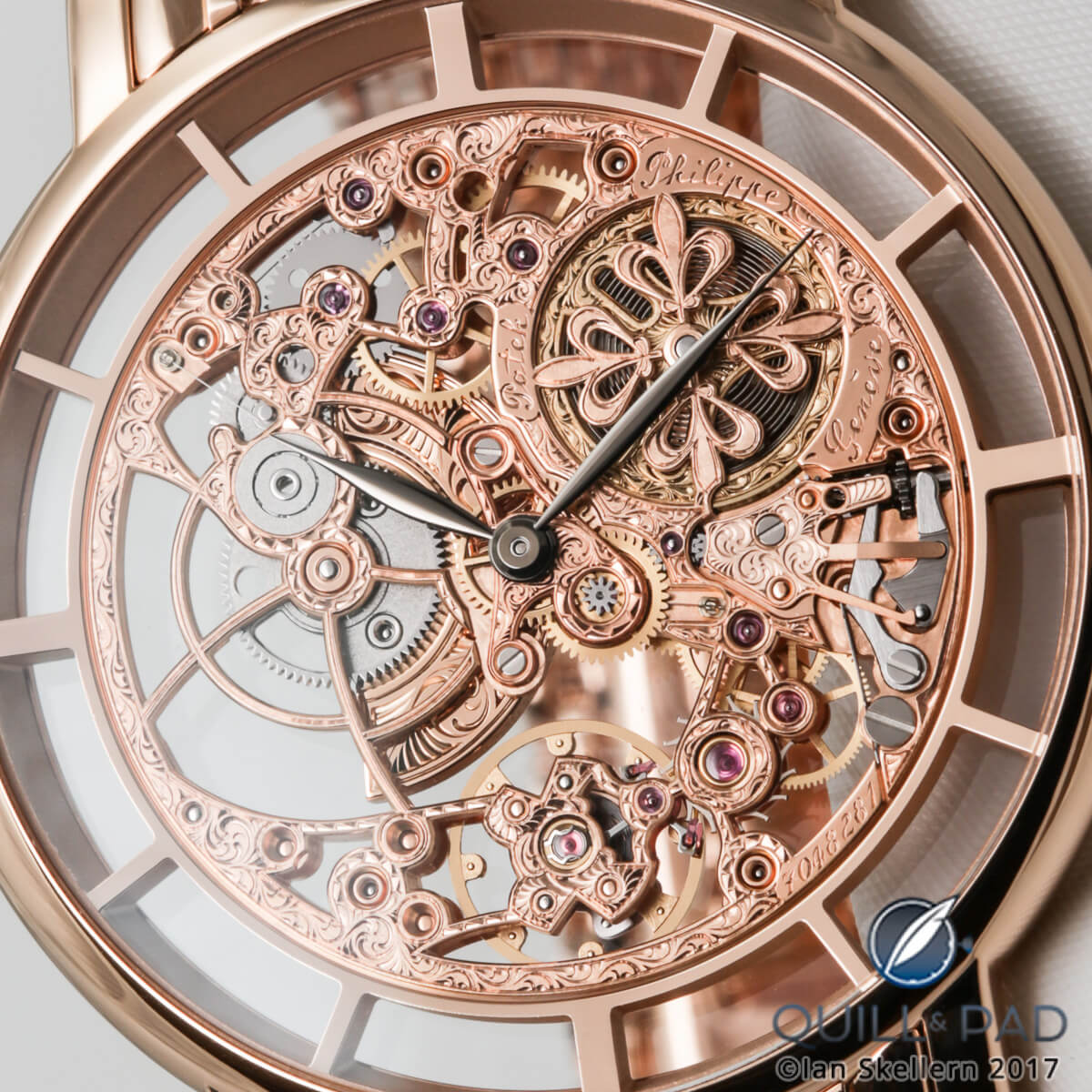
Patek Philippe Calatrava Squelette Reference 5180/1R-001
The watch’s movement is only 2.53mm thick. It is a statement of the delicate balancing act that skeletonization plays between aesthetic appeal and mechanical integrity. Anything more removed from the movement would make it too fragile and its chronometry would be compromised.
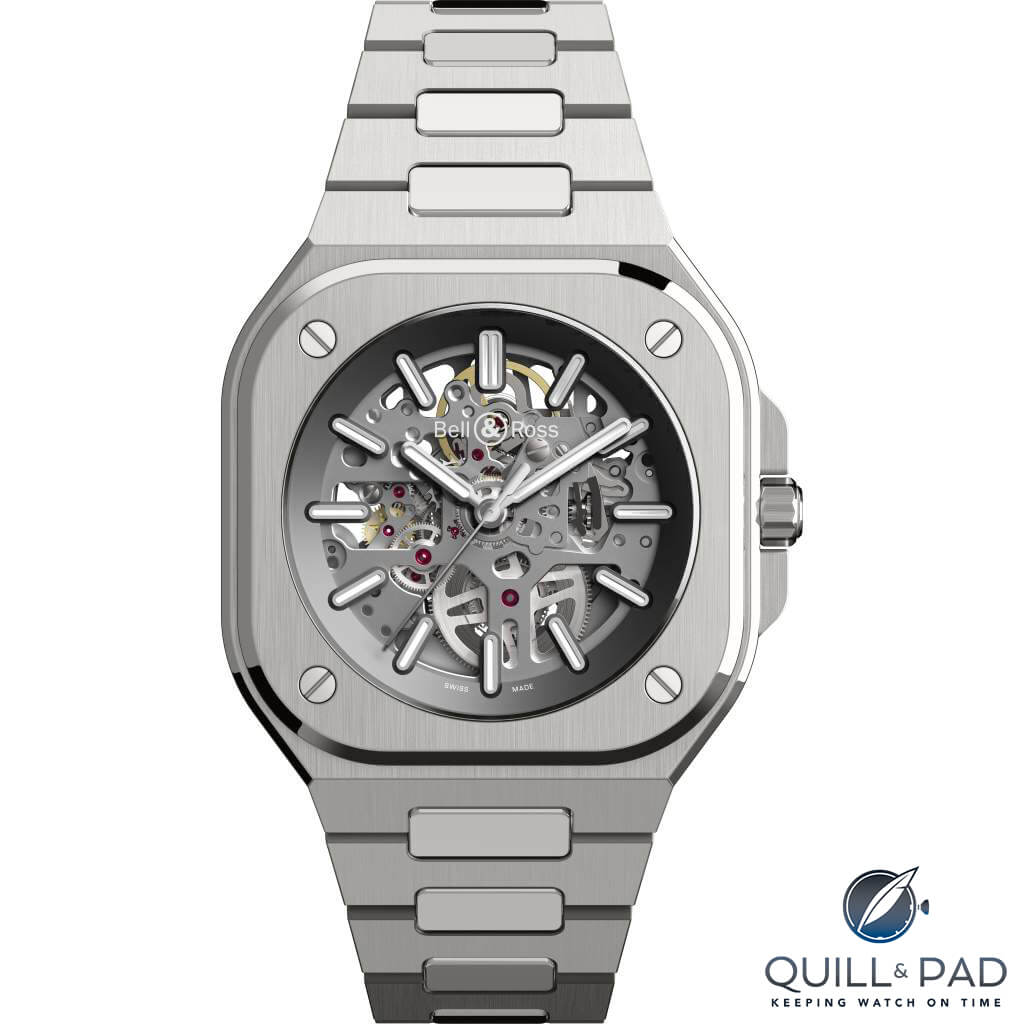
Bell & Ross BR 05 Skeleton
During the last 20 years, advances in computer-aided design and manufacturing (CAD-CAM) have made the production of skeletonized movements more accessible to more brands. Using modern technology, watchmakers can pre-engineer a skeleton movement, to deliver maximum visual impact with designs that are impossible to replicate by hand.
Calculations can be made to evaluate the torsional limits of the materials used in the movement and the exact amount required, which reduces waste. Modern lighter and stronger materials such as titanium and forged carbon introduced from the aerospace and F1 racing industries have further enhanced the structural resistance of skeleton movements.
Like or hate it
Not all watch enthusiasts agree with the idea of skeletonization: legibility and fragility are often the undesired outcomes of skeletonization. Openworked watches with fully skeletonized movement do not facilitate the reading of time, as the hour and minute hands are lost in the intricate architecture of the movement.
When the number of components increases because of a complication, the architecture of the movement becomes complex, without a discernible design or logic, and may lack the three-dimensional perspective that is usually expected in skeleton watches.
Today, the use of coloration has helped simplify the reading of time. Coloring techniques like Physical Vapour Deposition (PVD) are frequently used in high-end watches to color bridges, main plates, and the wheel train.
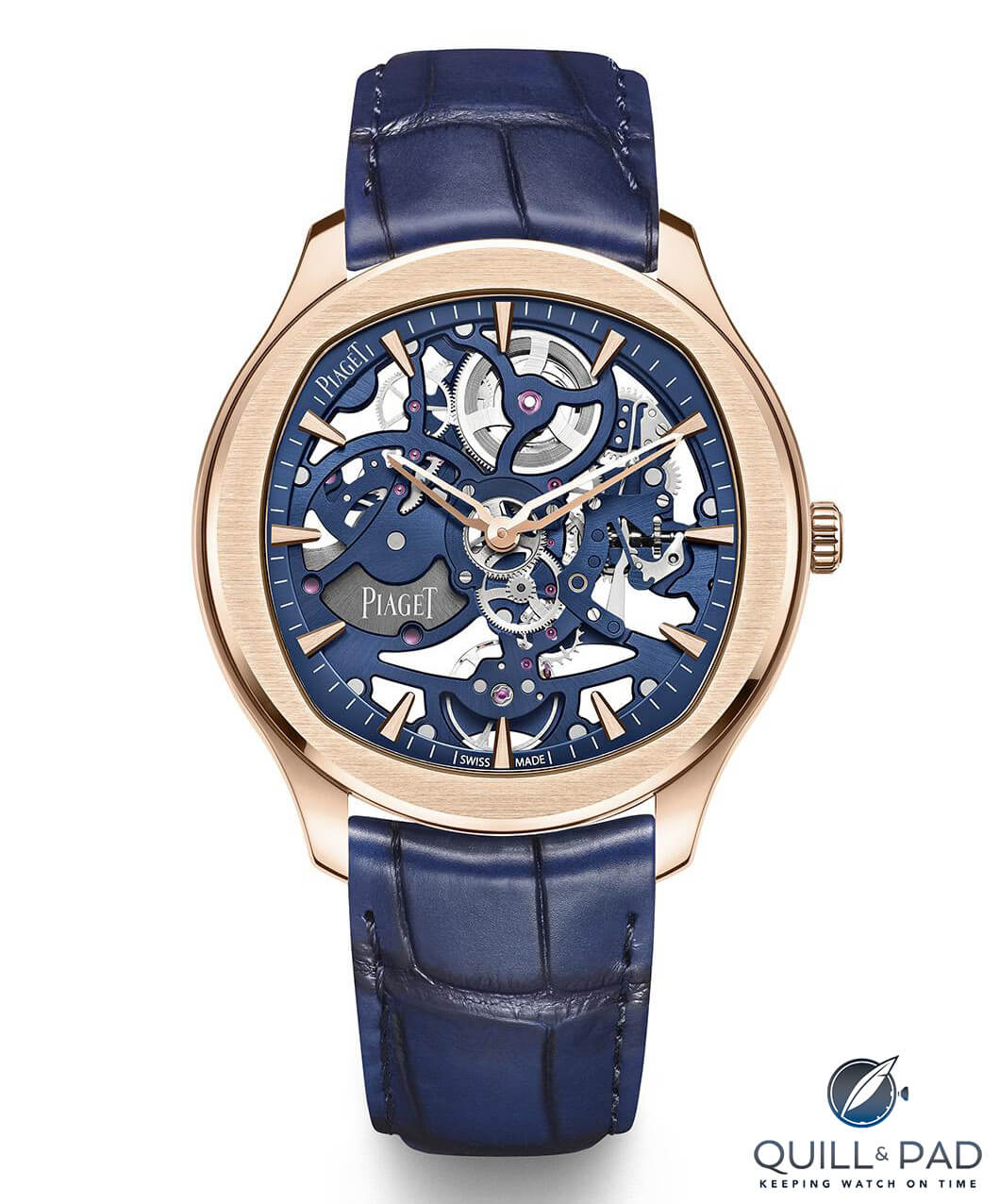
Piaget Polo Skeleton
In the Piaget Polo Skeleton, a blue PVD coating is applied to parts of the movement to create a useful degree of contrast and a three-dimensional perspective that enhances legibility.
There is a growing interest from today’s consumers for skeleton watches and several brands from the mid to high end of the market are offering skeleton watches in their product lines. For these consumers, a skeleton watch is not primarily to tell time but to show off craftsmanship and represent a work of art. It is meant to deliver a unique experience as there are no two skeleton watches that are exactly alike.
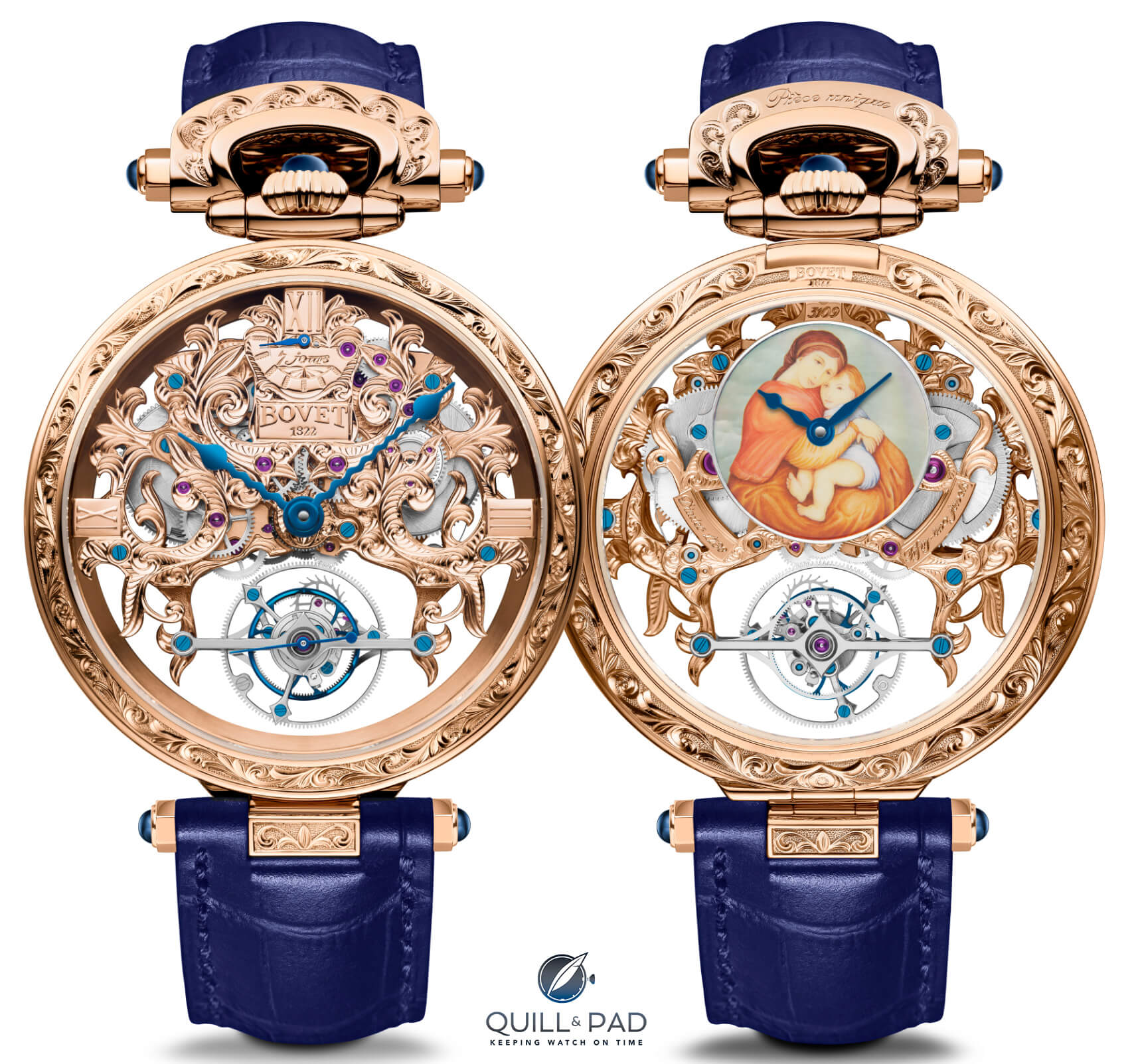
Bovet Amadeo Amadeo Skeleton Tourbillon front and back
For these watch collectors and enthusiasts, gazing at the inner workings of the movement, at the rhythm with which they interact with each other, at their craftsmanship and decorations, will deliver a powerful emotion.
* This article was first published in La Rivista magazine in September 2023.
You might also enjoy:
Vacheron Constantin Overseas Perpetual Calendar Ultra-Thin Skeleton (Video)
Bell & Ross BR 05 Skeleton Gold: There’s Visual Value In Precious Metal
Kudoke Real Skeleton Stars In ‘Last Looks’ Feature Film Alongside Charlie Hunnam And Mel Gibson
H. Moser & Cie Pioneer Cylindrical Tourbillon Skeleton: Having a Funky Good Time on Your Own Terms
Piaget Polo Skeleton in Pink Gold: The Power of a Sublime Blue-Gold Contrast
Leave a Reply
Want to join the discussion?Feel free to contribute!