Donzé Cadrans creates enamel dials as if they were 300 years old.
This sounds like a very odd statement for a company that was only founded by Francis Donzé in 1972, but the magic of enamel is that the dials still look like new after many hundreds of years.
Ten years after the founding, Donzé’s daughter Francine and her husband Michel Vermot joined the family-run company, which had managed to weather the decade of the quartz crisis as one of the very few specialists in labor- and cost-intensive enamel.
By the time Donzé retired in 1987, Vermot had already begun the company’s collaboration with Ulysse Nardin, which had been bought and resurrected in 1983 by Rolf Schnyder and a few friends.
The first timepiece Donzé and Ulysse Nardin worked on together was the complicated jacquemart-outfitted Hourstriker San Marco with its vibrant blue, which was certainly the first enamel dial of the modern incarnation of Ulysse Nardin, and likely one of the first of the Mechanical Renaissance, which was starting to bloom after the quartz crisis.
Ulysse Nardin and Donzé Cadrans became inseparable, and enamel dials became a signature element for the Le Locle-based brand’s haute horlogerie creations.
In 2012, as Vermot was in the process of retiring, Ulysse Nardin acquired Donzé Cadrans, thereby preserving this unique artisanal craft and securing its supply for the future. Donzé Cadrans also continues to supply other brands with dials.
Note: “cadran” is the French word for “dial.”
Grand feu
Donzé Cadrans only works in grand feu enamel, which means fired in a hot oven or kiln and represents the generic term for all genuine enamel that is fired at temperatures higher than 600°C. This is the point where enamel powders – which are basically crushed glass – melt and fuse with the base and/or other layers of enamel. The precise firing temperatures depend upon the specific the types of enamel powders used.
Donzé Cadrans’ standard enamel watch dial production comes straight from the past.
Using copper as the base – a metal element known as a “blank” – reproduces not only the look, but the whole general vibe, of a vintage or antique timepiece. The metal is soft, so it can bend to be absolutely flat or domed.
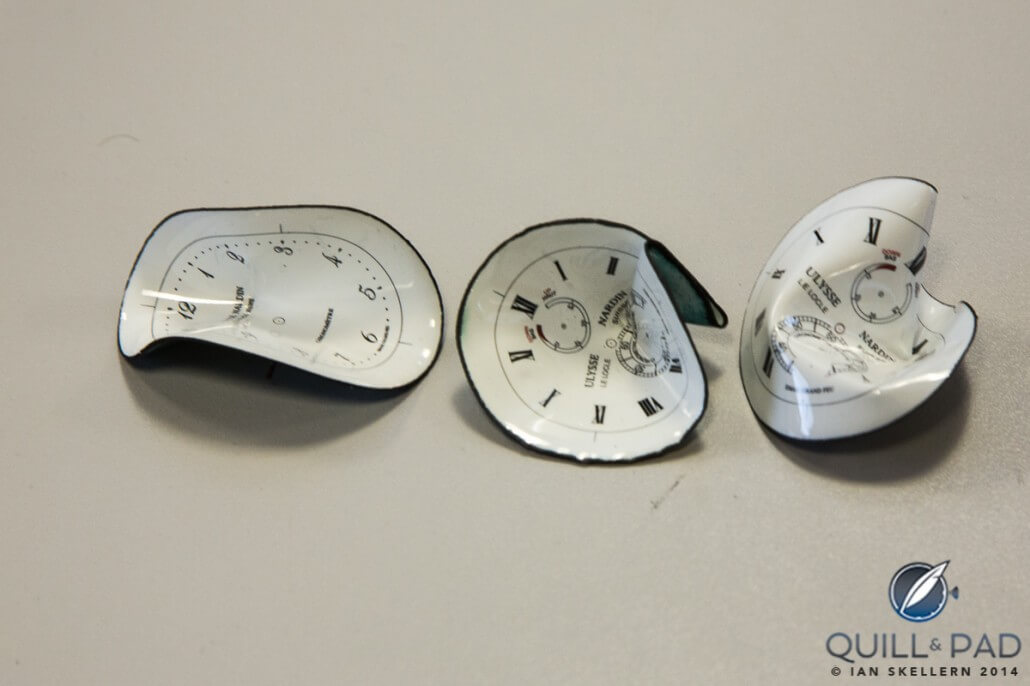
When heated to the right temperature, enamel dials can be bent without cracking the enamel, but ascertaining the correct temperature is not so easy (these are crushed rejects)
Additionally, it is easier to apply the champlevé technique to the soft copper, which calls for a comparatively thick metal base that has been engraved to leave cavities in the desired shape.
The enamel is put into these prepared grooves, which form shapes and thus allow for concrete forms. Then it is fired and sanded once it leaves the kiln; after cooling, excess material is removed to give it an extra shine.
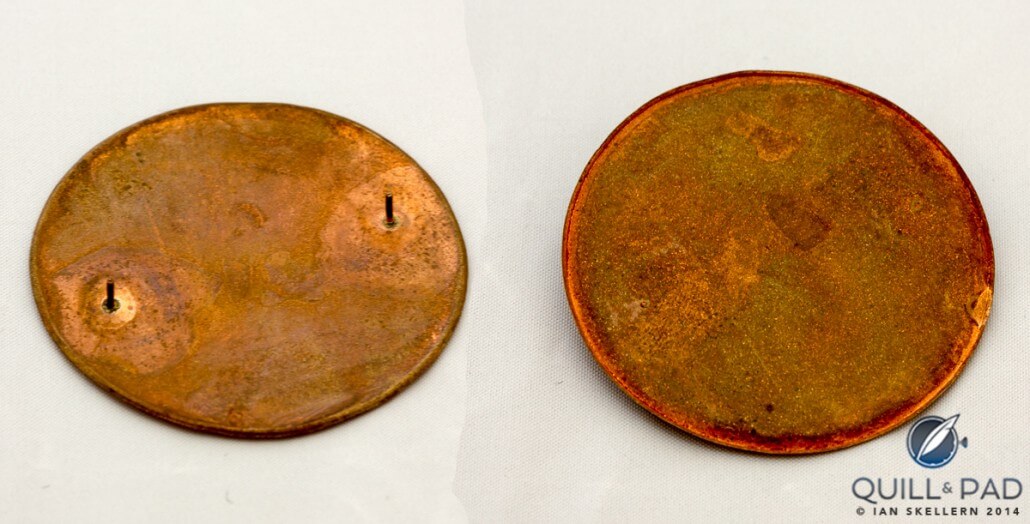
Top and bottom of copper dial blanks; you can see the positioning pins (“feet”) on the blank on the left
Using copper also makes it easier to solder the feet to the bottom of the dial. These are necessary for the dial’s production processes and for final watch assembly.
The process
Making an enamel dial according to the original traditional recipe takes precision, patience, experience and talent.
The copper blank first gets one layer of enamel on the front and back to equilibrate the dial before heading to the oven for the first round of firing. Putting enamel on the back of the blank is called contre-émail. If enamel is not first applied to both sides, the copper blank will warp when fired.
Then many more layers of enamel are added, and after each one the blank is fired in the hot oven. This creates enamel’s very specific sense of depth.
As the dials always have very small inclusions, the goal is to obtain the best possible surface. When it’s deemed done, the dial thickness is checked very carefully and then the enamel is polished and filed.
“Anything handmade is never perfect,” Claude-Eric Jan, today production head of Donzé Cadrans, reminds us.
The numerals, markers and any other markings such as the logo and brand name are printed on the dial in enamel using the transfer process.
At this stage in the production process, there will be a clear 60 to 70 percent reject quota. “Enamel is for life,” Jan says again, so the dials chosen for use in Ulysse Nardin’s timepieces must be as close to perfect as possible.
Following the enamel “printing,” the dial blank is fired for 5 to 7 seconds at about 800°C, after which it is flattened by an artisan using a piece of carbon. “This is a very delicate step,” admonishes Jan. Even more rejects can be created right here. The ones that survive are then trimmed to the right size.
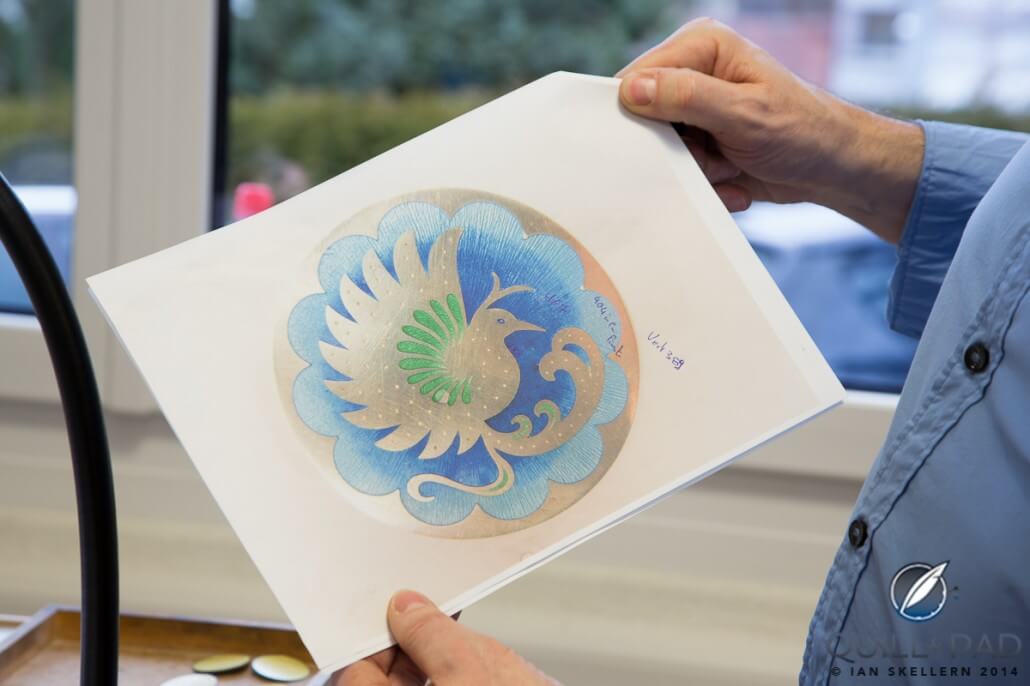
An intricately detailed pattern of a hummingbird is first drawn on paper before being miniaturized and “transferred” to the dial
Cloisonné and flinqué
There are many ways to work with enamel, but one of the most preferred manners for both Ulysse Nardin and Donzé Cadrans is the difficult cloisonné technique. This involves separating the colored fields with miniscule gold threads, some smaller in diameter than a single human hair, thereby practically tracing the outlines of a scene’s figures.
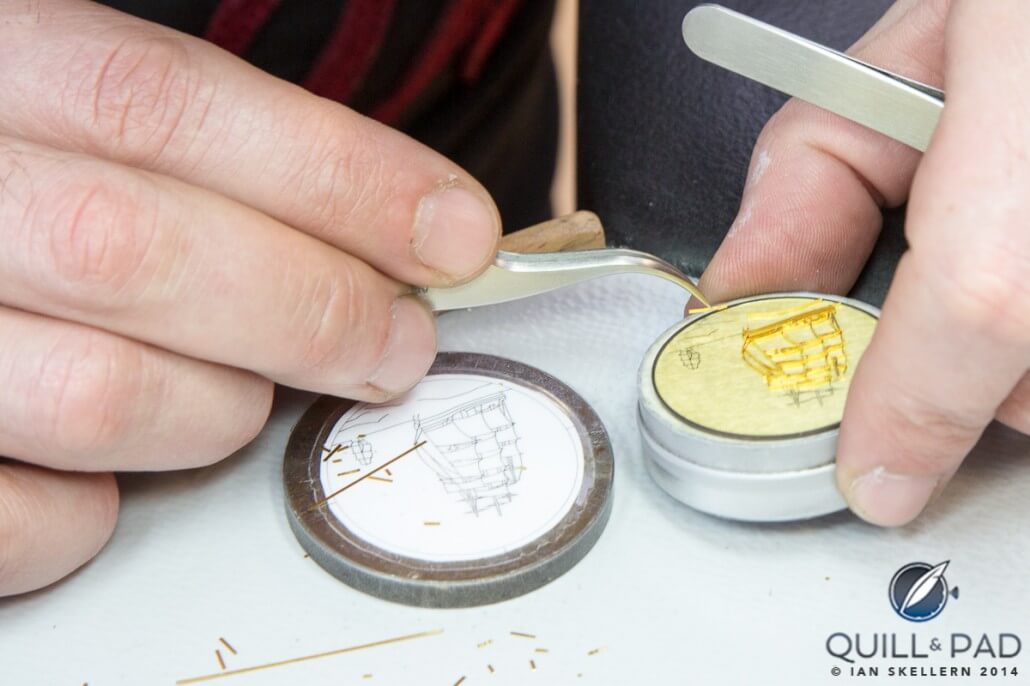
To achieve cloisonné enamel, tiny gold wires are first cut and shaped against a template (left) before being carefully positioned on the dial (right)
Cloisonné is one of the most painstaking examples of enamel. Bending and placing the infinitesimally small gold wire for one dial alone takes up to 15 hours. And there can be no shortcuts.
All in all, more than 50 steps are needed to complete a cloisonné dial, including up to 12 trips to the kiln, where each firing could conceivably mean that the dial becomes a reject.
The flinqué technique comprises enamel over guilloché. Thanks to enamel’s high reject rate, flinqué dials tend to be relatively rare.
Museum pieces
Donzé Cadrans is usually the go-to for Swiss watch museums if an antique dial needs repairing.
One big reason is, as Claude-Eric Jan explains, because the value of the watch does not decrease exponentially if Donzé replaces a broken dial on an antique timepiece. He explains that because the process is the same one used when the timepiece was originally created, the value would not decline much if at all.
Thus, when a museum timepiece has a broken dial, it is always made new rather than be repaired. Some dial makers repair broken dials of museum pieces with acrylic, but Jan says that this is not a good thing to do as the acrylic will yellow with time. Enamel, of course, won’t. It is made to last for lifetimes.
Donzé, at home on Rue de l’Avenir (“road of the future”) in Le Locle, has chosen the location of its domicile well: looking to the past for quality techniques has evidently also secured its future.
For more information, please visit www.donzecadranssa.ch and www.ulysse-nardin.com/en/swiss_watch_manufacturer/Portrait/Company_Background.html.
Trackbacks & Pingbacks
-
[…] For more on how Donzé Cadrans, a Ulysse Nardin-owned company, creates such masterpieces see Why Do Ulysse Nardin’s Dials Look So Good? Because Donzé Cadrans Authentically Fires Enamel. […]
-
[…] Aside from technical excellence, Ulysse Nardin’s expert knowledge also includes some of the most refined and time-consuming traditional handicrafts such as grand feu enamel and hand-painted miniature enamel dials that are true and long-lasting pieces of miniature art (see Why Do Ulysse Nardin’s Dials Look So Good? Because Donzé Cadrans Authentically Fires Enamel). […]
-
[…] oven-fired white enamel dial was supplied by Donzé Cadrans (owned by Ulysse Nardin), and unless physically damaged will look just as good after hundreds of […]
-
[…] The sublime enamel dial was crafted by Donzé Cadrans, a traditional enamel dial manufacture that Ulysse Nardin acquired in 2012. Donzé Cadrans and Ulysse Nardin have been inseparable since the company’s rebirth in 1983 (see Why Do Ulysse Nardin’s Dials Look So Good? Because Donzé Cadrans Authentically Fires Enamel). […]
-
[…] For fascinating information on how Donzé Cadrans, which was taken over by Ulysse Nardin in 2012, creates its enamel dials, please see Why Do Ulysse Nardin’s Dials Look So Good? Because Donzé Cadrans Authentically Fires Enamel. […]
-
[…] For more on Ulysse Nardin’s mastery of enamel see Why Do Ulysse Nardin’s Dials Look So Good? Because Donzé Cadrans Authentically Fires Enamel. […]
-
[…] For more on how Donzé Cadrans, a Ulysse Nardin-owned company, creates such masterpieces see Why Do Ulysse Nardin’s Dials Look So Good? Because Donzé Cadrans Authentically Fires Enamel. […]
-
[…] Crafting enamel dials at Donzé Cadrans on @QuillAndPad http://t.co/BpsmOzyYAr […]
-
[…] for design; Les Artisans Boîtiers for case manufacturing; Donzé Cadrans for enamel dials (see Why Do Ulysse Nardin’s Dials Look So Good? Because Donzé Cadrans Authentically Fires Enamel); Metallique & Convergence Composite for the composite carbon dials; H M Waeber for the […]
-
[…] Cadrans creates its grand feu enamel dials in just the same way they were made in the 1800s. (See Why Do Ulysse Nardin’s Dials Look So Good? Because Donzé Cadrans Authentically Fires Enamel for much more information on this […]
Leave a Reply
Want to join the discussion?Feel free to contribute!
Interesting read, thanks. These dials are really delightful. Isn’t the one in the second pic lapis lazulli though?
Thanks, Dale! If you are referring to the Hourstriker, no, it’s enamel, though it may have some paillons in it. This watch is described in the Ulysse Nardin book, ‘Making of a Masterpiece,’ and while we were at Donzé Mr. Jan specifically talked about this watch. I can assure you it’s enamel!
Guilloche enamel on a silver backing. Beautiful.
Guten Tag
Ich Brauche eine Zifferblatt von Ulysee Nardin für ETA Kaliber 2892 Farb ist egal
wo und wie bekomme ich MfG
Mancini
Am besten kontaktieren Sie Ulysse Nardin direkt: https://www.ulysse-nardin.com/row_euro_en/contact-us/