by Ian Skellern
On a recent visit to the Valbray manufacture, which is around 45 minutes’ drive north of Geneva, I surreptitiously took a look at the electrics in back of a CNC machine (as one does). Seeing my interest, Côme de Valbray, who co-founded the brand with his wife Olga, casually mentioned that the racks of electronics contained the processing power of 350 powerful computers and that the machine drew up to 90,000 watts of power in operation: that’s the equivalent to the power needed by around ten homes.
CNC machines have revolutionized the production of relatively small quantities of complex-shaped components, and it almost goes without saying that they have had a dramatic impact on the watch industry.
Most of us have seen at least photos and perhaps even videos of these ubiquitous machines with their bits and cutters spinning and whirling under high-pressure jets of lubricating oil and robotic tool changes.
Precision is everything in the manufacture of watch components, and every time the bar or plate of metal being machined is manually turned or rotated on the plate of the CNC machine, there is a risk of slight misalignment.
And in watch components, every micron counts.
The weakest link is . . . us
To minimize potentially precision-upsetting human intervention, CNC machines have steadily become more sophisticated, particularly in the number of axes the worked metal and tools rotate in.
Imagine a two-axis CNC machine: it would only be able to cut a single face to a single predefined depth. The milled plate would have to be manually rotated for each face to be machined.
Three-axis CNC machines can cut along three axes simultaneously: the x-axis, the y-axis, and the z-axis. The x-axis moves the cutting tool from front to back, the y-axis moves it from left to right, and the z-axis moves it up and down. Three-axis machines are used primarily for cutting flat, two-dimensional parts.
Five-axis CNC machines cut along two additional axes. These routers have the ability to cut on five sides (four sides and top) of a piece of material simultaneously for increased speed and flexibility. Five-axis machines are usually used to mill large three-dimensional components.
With five and more axes, the CNC machine can rotate both the piece being machined and the tool doing the machining through virtually any angle in three-dimensional shape. This has two related benefits compared to three-axis machines:
* The object does not have to be removed from the mount, rotated, and re-fixed so often (if at all), which minimizes positional errors.
* Reducing human intervention saves time. These are very expensive machines, so the more time they spend actually milling rather than being stopped to manually prepare for the next step both increases efficiency and lowers costs.
Until the last decade or so, milling curved surfaces on a CNC machine involved cutting a series of steps rather than a continual curved line because in terms of processing power straight lines are easy, even when there are millions of straight lines. Calculating even simple curves is much more complex, and compound multi-radius curves are even more difficult.
As the prices of computing power decreased, CNC machines became capable of milling continuous complex curves, which made for much higher precision components. To increase the speed of the milling process even more, the machines had to become even smarter.
Gentlemen, start your engines
The fastest car around a track isn’t always the fastest car or the most powerful car. A driver who knows the track well can slow down to an optimal speed ahead of corners so as to go around it faster, and a smarter driver can anticipate and avoid problems rather than react to them.
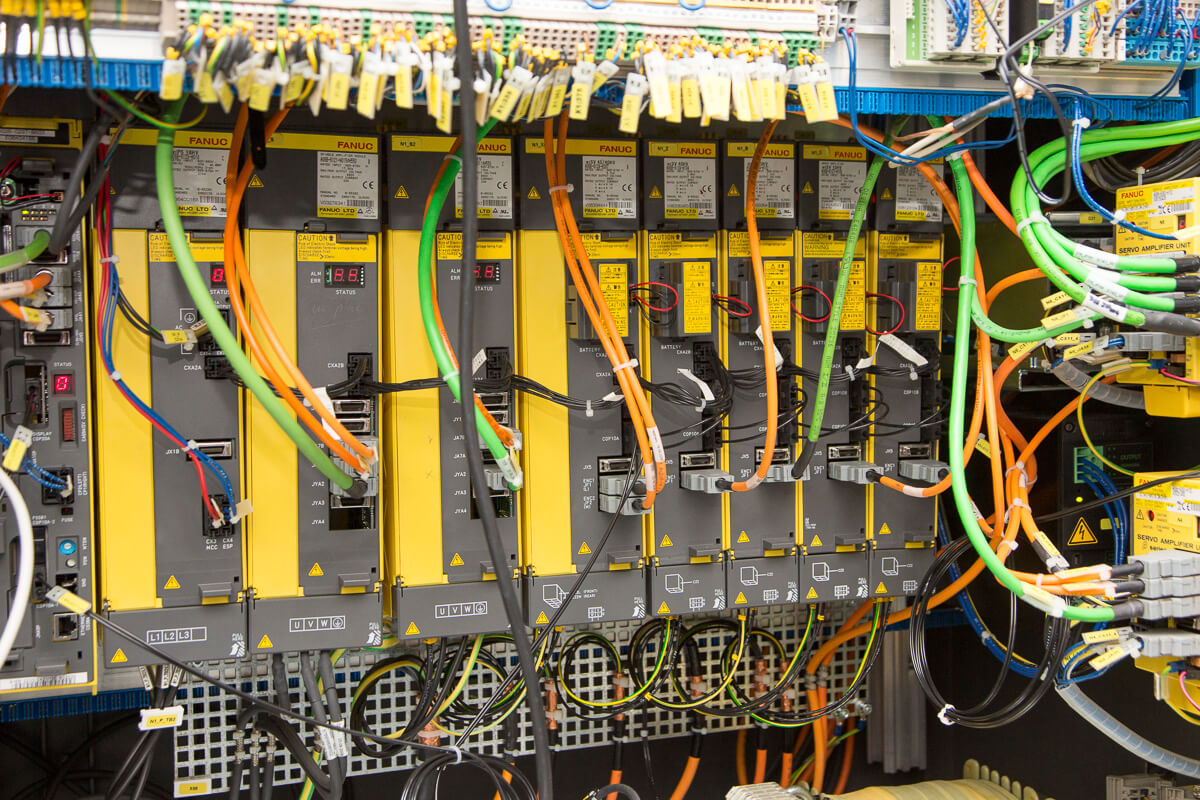
These represent the equivalent to 350 high-performance computer processors and they control the operation of a Valbray five-axis CNC machine
Likewise, a smarter CNC machine or, to be more precise, a smarter program can prepare for complex curves and changes of cutting tool so that the overall process is smoother and quicker.
What I hadn’t appreciated as I looked in at those high-speed, oil-drenched components being milled before is just how much processing power was required. And 350 high-powered processors running one machine really drove that point home.
If milling a curved line is difficult, imagine doing the same thing at very high speed with the radius and shape of the curves continually changing, also at very high speed, with both the piece being machined and the piece (and there may be more than one) holding the cutting tool also moving.
The video above is a different five-axis CNC machine from that used by Valbray, however it demonstrates the flexibility and complexity of what these machines are able to do.
And there is one more number that I thought interesting: one megabyte. The Valbray machine required an impressive 350 processors, but just one MB of memory. The compressed jpeg photos in this article are likely to add up to be larger than that!
If you found this interesting, you may also like Focus On Technology: 3D Printing, What Is It Really? and Focus On Technology: 3D Printing, What Is It Really? Part Deux.
Trackbacks & Pingbacks
-
[…] Ian Skellern, Quill & Pad readers have been given a quick primer to CNC machining in 350 Processors And 90,000 Watts Of Power Just To Mill A Curved Line? This article expands upon the subject, focusing on the technical details that I love to ramble on […]
-
[…] key machines that is employed in precision manufacturing today, the 5 axis CNC milling machine. Check out the article for more information on these […]
Leave a Reply
Want to join the discussion?Feel free to contribute!
Thank you for your information. It’s very useful.