There is absolutely no doubt that rare arts have become an important subject in today’s luxury watchmaking world. Not only do they add decorative beauty to a timepiece, but they also add value to it because the artwork can only be accomplished by hand-making each piece.
In 2014, Jaeger-LeCoultre created the rare and unique 12-piece Hybris Artistica series featuring incredibly technical and creative movements already in existence as a base to which rare and costly artisanal arts were added. Naturally, these timepieces are both unique and exquisite. For more see When Art Ticks: Why Jaeger-LeCoultre Is A Master Of Art And Mechanics.
With a flawless technical reputation, why did a major brand like Jaeger-LeCoultre feel the need to go to the trouble of developing such unique pieces? “It shows a bit of the future of what we can do,” marketing and product director Stéphane Belmont told me at the time.
“In the last ten years, in creating the Hybris Mechanica collection, it was more to demonstrate the watchmaking mastery of Jaeger-LeCoultre. In addition, we have many artisans and designers and people who are collaborating every day. The result of their work might not be as visible as what we have today in watchmaking.”
It all started with enamel
Belmont was certainly referring, among others, to Jaeger-LeCoultre’s talented in-house enameller Miklos Merczel and his team of artisans. “We wanted to also make people aware of the design, which is to us actually a part of the success,” he continued.
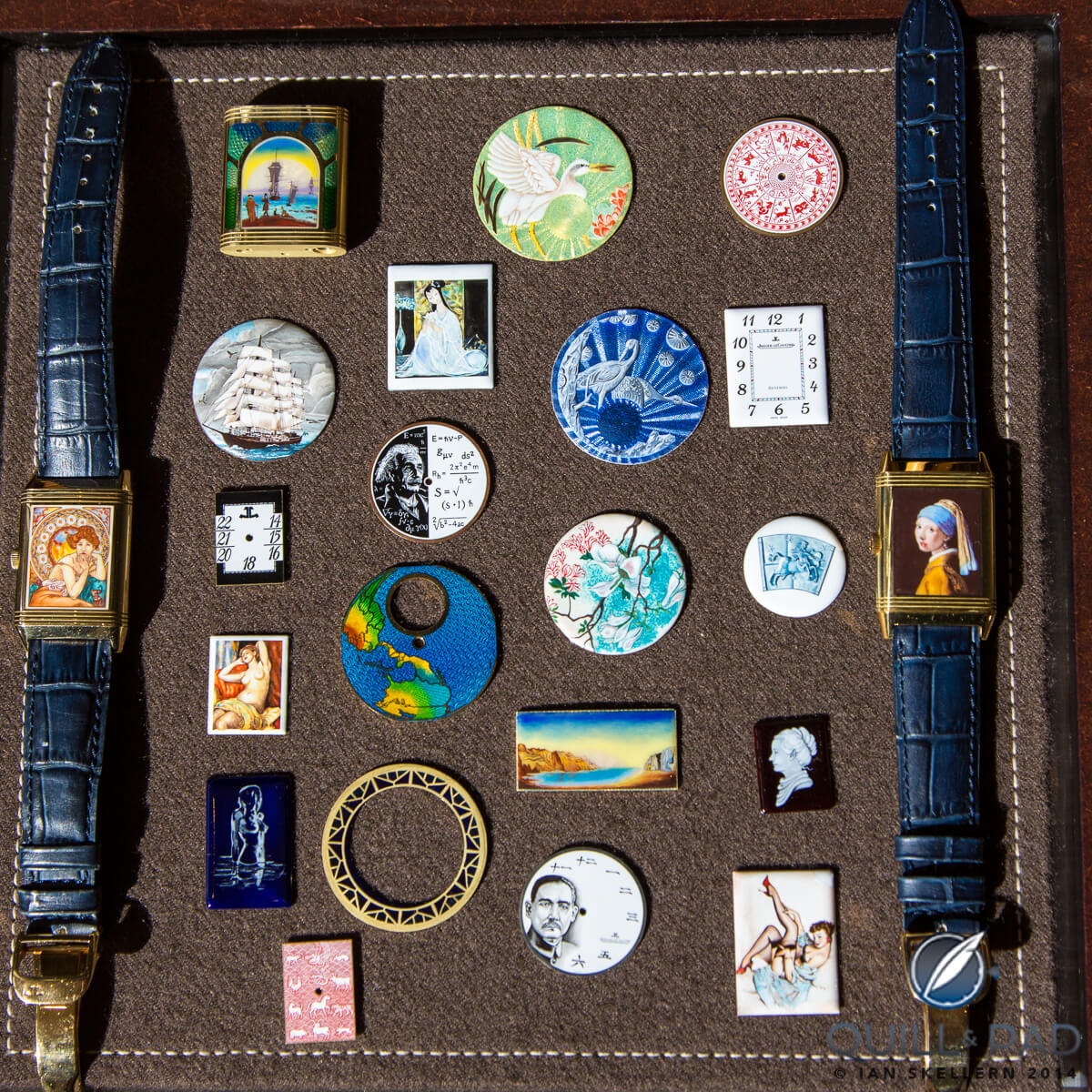
Just a small selection of different styles of enamel on offer at Jaeger-LeCoultre: as you can see any type of personalization is possible
“The Hybris Artistica is more to show that we can also make pieces that are from an aesthetic point of view also very surprising or beautiful to look at: combining different skills and not being just one enamel piece, or one gem-set piece, but combining all this to create a watch that is beautiful to look at in addition to the complications.”
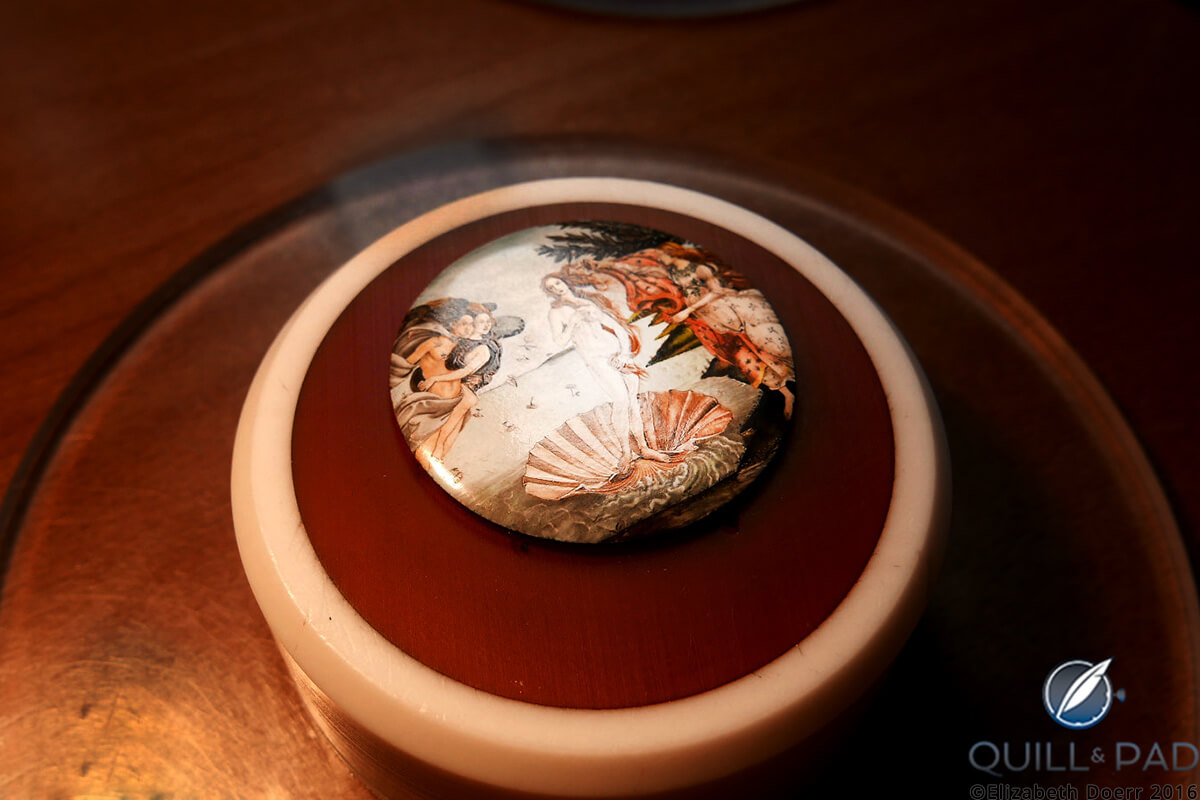
An enamel of Boticelli’s Venus in progress as a practice piece (!) at Jaeger-LeCoultre’s dedicated new métiers d’art workshop
While all of this might seem to form a sort of trend that luxury watchmakers could be following to add more value to complicated watches, indeed I believe it is more an extension of the way high-end brands look to differentiate themselves as markets and consumers mature by tapping into quasi-lost art forms.
And at Jaeger-LeCoultre, it is actually part of a natural progression: Miklos Merczel, originally a watchmaker, organically founded the enameling department in Le Sentier in 1992 thanks to a personal passion for the subject. Learn more about Merczel and enameling at JLC in Jaeger-LeCoultre’s Art Of In-House Enameling.
One of Merczel’s longest-standing colleagues in the enamel department is Sophie Quenaon, who began learning the art form from him in 2000 after already having worked in Jaeger-LeCoultre’s engraving workshop for five years. “I learned engraving and enameling from artisans here at Jaeger-LeCoultre,” Quenaon explained in reply to where she had learned the crafts.
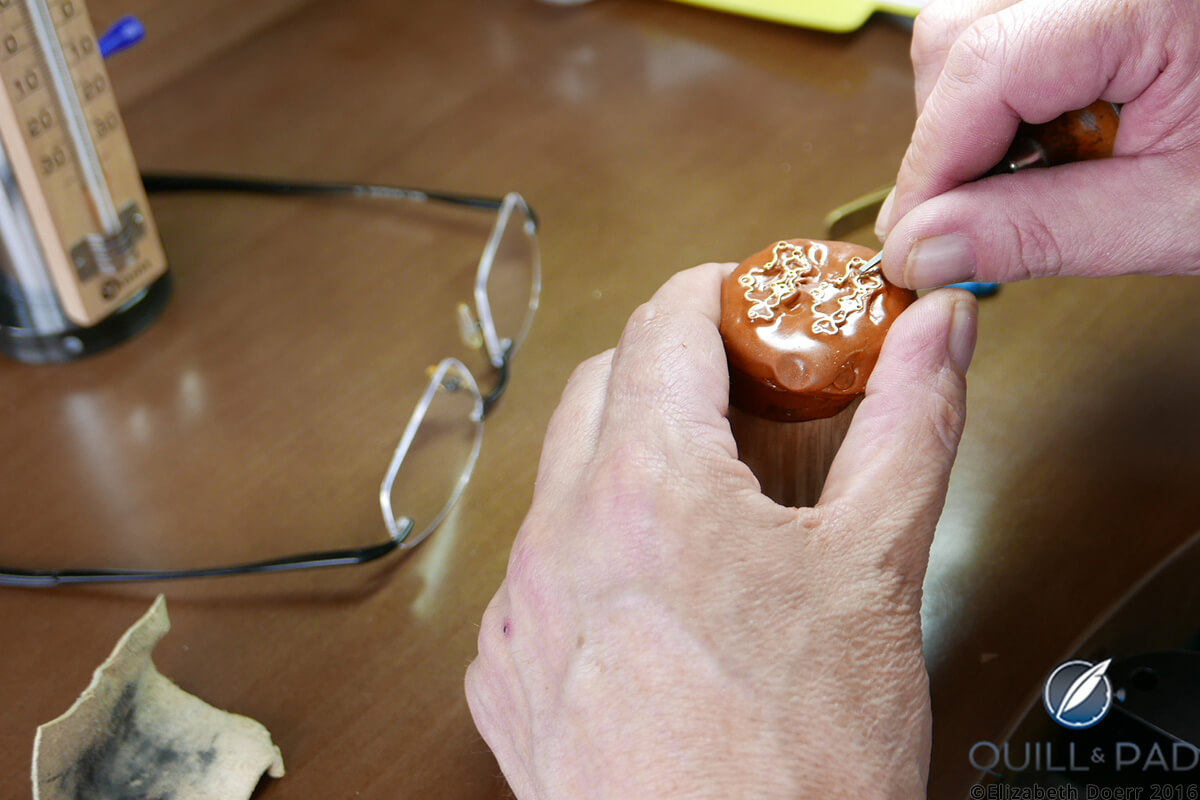
A beautiful movement component being engraved at Jaeger-LeCoultre’s dedicated new métiers d’art workshop
“I devoted five years to engraving, and then one day Miklos Merczel, who contributed to the revival of the enameling art at the manufacture, invited me to join him. The idea of working with colors and the alchemy of enamel seemed amazing,” she explained.
“It’s all done completely by hand,” Quenaon continued. “No computers, projectors or other machines . . . we work in the same manner as was done many centuries before . . . and our work involves many delicate stages that have to be mastered with equal care.”
Artisans now gathered in one department
But if you were to think that Jaeger-LeCoultre’s only artisanal talent was enameling, you’d be wrong. Merczel, Quenaon, and their colleagues in enameling now join artisans proficient in other métiers in one department, which opened at the beginning of 2016.
As revealed in 85 Years Of The Jaeger-LeCoultre Reverso, in the mid 2000s Jaeger-LeCoultre began producing more and more exceptional pieces for women set with exquisite gemstones. New settings engineered by the brand included snow setting (random setting with various-sized stones) and rock setting (a type of invisible setting).
In addition to gem setters, Jaeger-LeCoultre also employs engravers – mainly to personalize the reverse sides of Reverso models.
Jaeger-LeCoultre’s new department to house all of these artisans together allows them the freedom to create both in partnership with other artisans or alone.
And finally Jaeger-LeCoultre has also brought guilloche into this mix. Not only does a guillocheur work in this department, but the brand has also found and acquired four vintage machines: three rose engines and one pantograph. You can see components worked by this new artisanal technique in the new Reverso Tribute Gyrotourbillon introduced at SIHH 2016 (see The New Jaeger-LeCoultre Reverso Tribute Gyrotourbillon: Now More Comfortable To Wear Through Even Slimmer Fit).
All in all, about 30 artisans work in this new department. And I look forward to the next beautiful designs to emerge from it!
For more on the latest news from Jaeger-LeCoultre, please visit www.jaeger-lecoultre.com/news.
Trackbacks & Pingbacks
[…] A few weeks ago, I visited the Jaeger-LeCoultre factory as I talked about in Jaeger-LeCoultre’s Specialized Department For Artistic Crafts: Enamel, Gem Setting, Engraving, And… […]
Leave a Reply
Want to join the discussion?Feel free to contribute!