by Ian Skellern
This is part 2 of a three-part series about Derek Pratt’s reconstruction of John Harrison’s Longitude Prize winning H4, which was the world’s first precision marine chronometer. This article was first published in the The Horological Journal (HJ) in March 2015, who we thank for graciously granting permission to republish on Quill & Pad.
To learn more about Derek Pratt please see The Life And Times Of Legendary Independent Watchmaker Derek Pratt. For part 1 in this series click Derek Pratt’s Reconstruction Of John Harrison‘s H4, The World’s First Precision Marine Chronometer (Part 1 of 3) and for part 3 click Making The Escapement, Remontoir, And Timing For Derek Pratt’s Reconstruction Of John Harrison‘s H4, The World’s First Precision Marine Chronometer (Part 3 of 3).
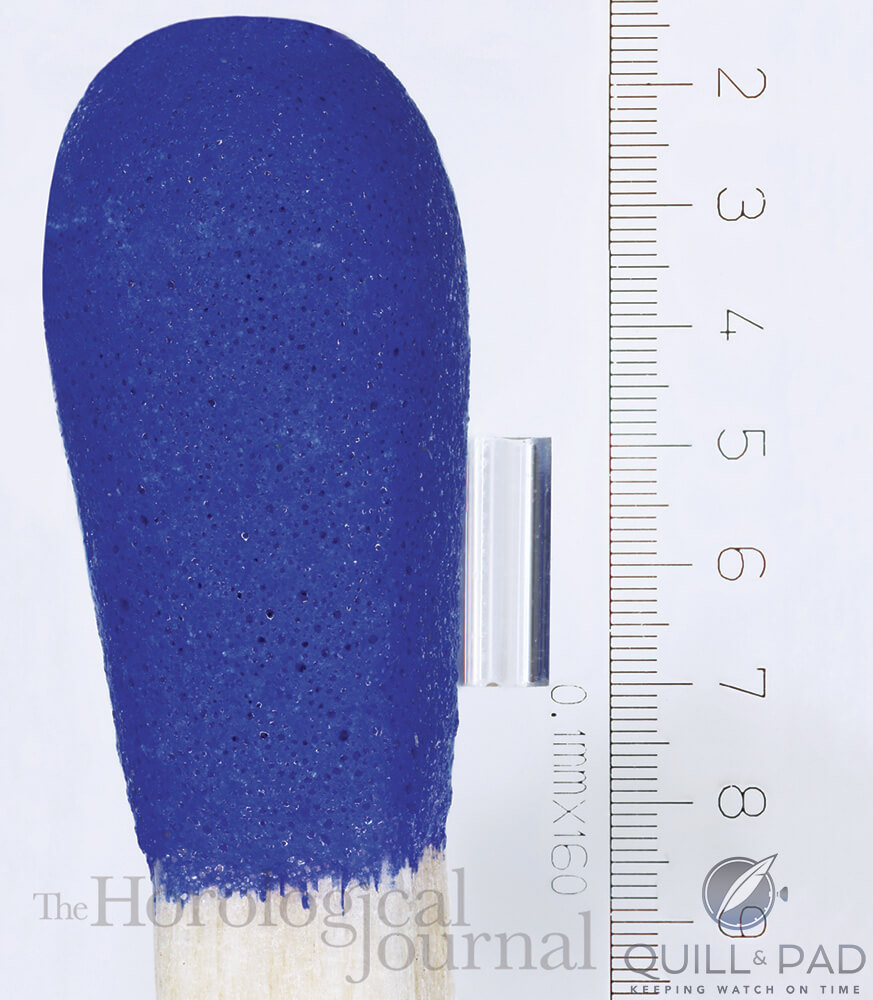
A completed diamond pallet for Derek Pratt’s John Harrison H4 reconstruction next to a match head (photo courtesy British Horological Journal)
Making Diamond Pallets for the Derek Pratt Reconstruction of John Harrison‘s H4
by Carl Murray
My colleague Roger Stevenson mentioned in the previous article that there would be four areas in the watch that would present challenges: the pair case, dial, engraving, and the diamond pallets.
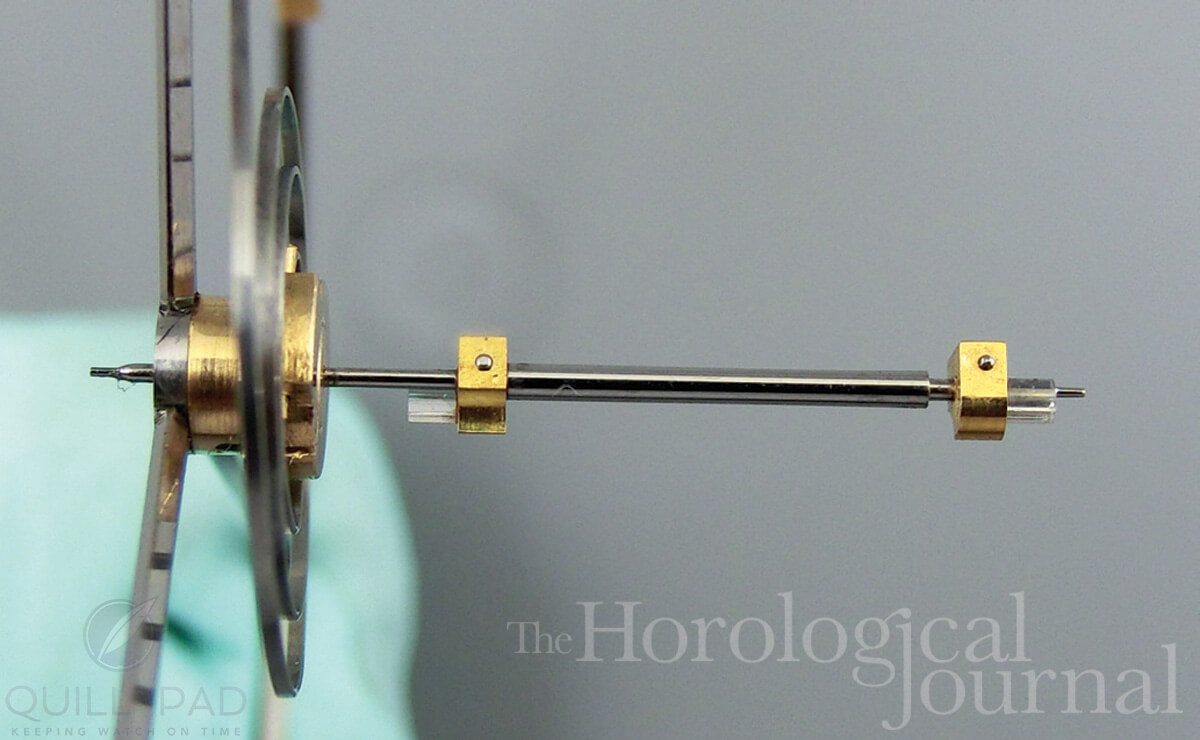
The diamond pallets in their holders on the staff for Derek Pratt’s John Harrison H4 reconstruction (photo courtesy British Horological Journal)
Derek had already found skilled craftsmen to carry out the first three tasks, but had decided to take on the pallets himself. By the time Derek had handed the project over to Frodshams, he’d already done a huge amount of research into the subject and had produced two diamond pallets, the first of which he thought wasn’t good enough to put in the watch and would need to be remade as it was a little undersized.
After close inspection, the second pallet was found to be exceptional, both dimensionally and in finish. Although it is difficult to compare Derek’s pallet with the original without having them side by side, we do have a reference point in the excellent paper by Jonathan Hird, “The Diamond Pallets of John Harrison’s Fourth Longitude Timekeeper H4.” I would say after studying the photographs and description in that article that the quality of finish on Derek’s pallet exceeds that of the original.
Derek made his pallets out of diamond cylinders, which had six facets ground around the edge. They measured 2 mm high and 1 mm in diameter. The method he used was a 200 mm cast iron lap (skaife), which had been charged with 8-16 micron diamond paste for grinding to shape and 4–8 micron diamond paste for polishing. This was spun on his Schaublin 102 lathe.
One of the first problems that Derek encountered was how to fix the diamond cylinder to a holder in order to grind and polish the various surfaces. At first he used dopping wax in order to stick the diamond cylinder to the holder, but found that because of the high pressures involved and the fact that diamond is such a good conductor of heat, they regularly came unstuck.
He got around this problem by making four different holders (one for each of the four surfaces to be ground), with each holder having an accurately “EDM’d” slot in it to receive the diamond, which was held in place with two endpieces.
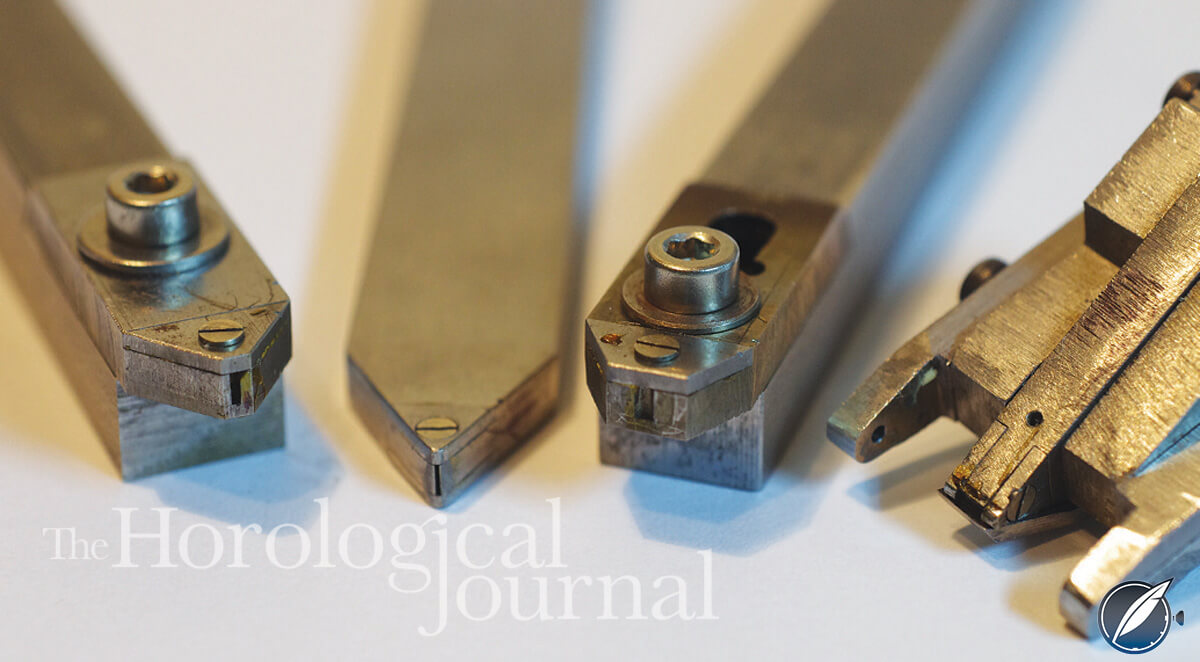
The four pallet holders made by Derek Pratt are used to make the diamond pallets for his John Harrison H4 reconstruction (photo courtesy British Horological Journal)
EDM stands for Electrical Discharge Machining, and Pratt was a pioneer in using this process for micro mechanics and watchmaking.
The small flat (heel) and large flat (impulse face) surfaces were ground and polished, I think, with the holder held in the cross slide. The curved back, on the other hand, looks to have been created by hand with the holder resting on a table and the diamond offered into a suitably shaped groove, which had been cut into the face of the lap. There seems to have been a certain amount of trial and error here as you can imagine and, although we had regular contact with Derek while he was making his pallets, we never got the chance to discuss the details with him before he passed away.
So what to do about the remaining pallet? After much discussion we decided to have a go ourselves (people willing to grind curved surfaces on diamonds are rather thin on the ground). Although we have plenty of experience in making watch jewels from synthetic sapphire and ruby we had no experience in working with diamond. After all, how hard could it be? Answer: very hard . . . literally.
Of course, one of the nice things about working on a project like this is that you get to think about how the original watch was constructed by Harrison all those years ago. This goes for the pallets too, and after reading Jonathan Hird’s paper it was clear that the direction of grinding and polishing lay across the width of the pallet and not along the length, which is preferable, as any polishing marks go in the same direction as the action of the escape wheel teeth, therefore reducing wear to the teeth tips. This is easy to achieve on the flat surfaces simply by orienting the holder in the desired direction on the cross slide. However, it is not so easy to achieve on the curved back of the pallet.
Although Derek had produced the curved back of his pallet by grinding and polishing along the length of the pallet, it was clear that because of the quality of finish this would not be of any consequence in the running watch. Still, as we had one pallet to make it would be nice from a historical perspective to have a go at forming the curved back by grinding and polishing across the width as per the original.
Luckily we were able to use Derek’s stock of diamond cylinders and holders, which gave us a good start. At this point, while Roger and Daniela were working on the rest of the watch, I started to look into ways of producing the second pallet.
As diamond has hard and soft planes, the first thing to do is to identify the soft planes and align these with the flat surfaces to be ground. Obviously, this is not possible with the curved back as this will contain both hard and soft planes due to the nature of its shape. There are two ways to do this, one is to use x-ray diffraction and the other method is trial and error, as presumably Harrison did (only because his x-ray diffraction equipment was broken at the time). So I opted for trial and error.
First, I used shellac to hold the diamond cylinder in a brass tube, which in turn was held in a square-headed pin vice. This allowed me to turn the diamond 90 degrees at a time and touch it against a fine diamond wheel spun in the watchmaker’s lathe. It soon became apparent where the softer planes lay, determined by sound and feel, as much as by the amount of material being removed.
With that done it was time to start grinding for real. I decided to grind the curved back, the impulse face, and heel in that order, finally rounding the sharp edge between the impulse face and the curved back.
A smaller (140 mm diameter) high-quality cast-iron plate was ordered. This was mounted on a Schaublin 70 face plate by my colleague Sean Martin, and a recess turned in the center 10 mm deep, leaving an outer band on the face of the skaife 8 mm wide.
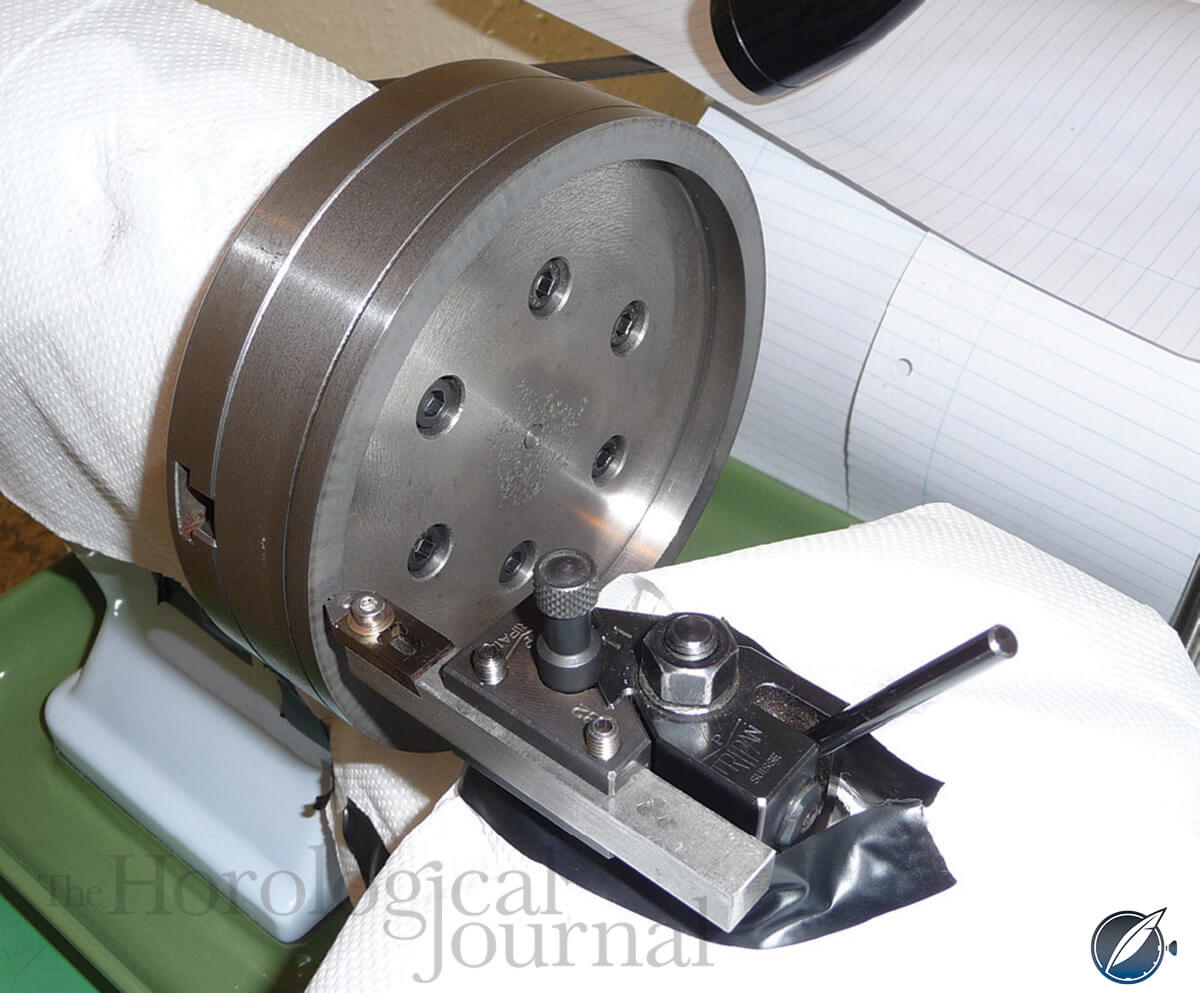
Cast iron skaife used for making the diamond pallets for Derek Pratt’s H4 reconstruction (photo courtesy British Horological Journal)
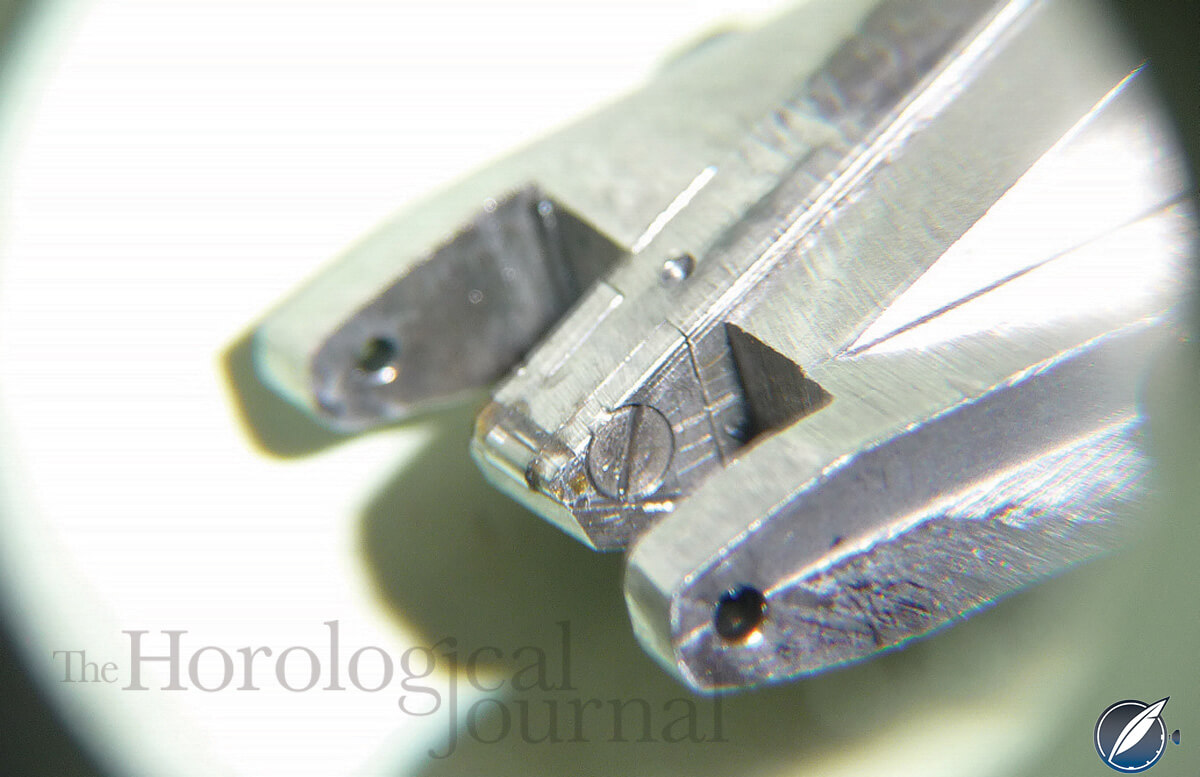
Pallet holder showing adjustable female pivot points used for making the diamond pallets for Derek Pratt’s H4 reconstruction (photo courtesy British Horological Journal)
I adapted Derek’s holder so it had an adjustable female pivot point on each side, allowing the diamond to pivot around any given radius. An attachment was made for the vertical slide, which had two male centers (arranged so there is a center on each side of the skaife’s 8 mm band).
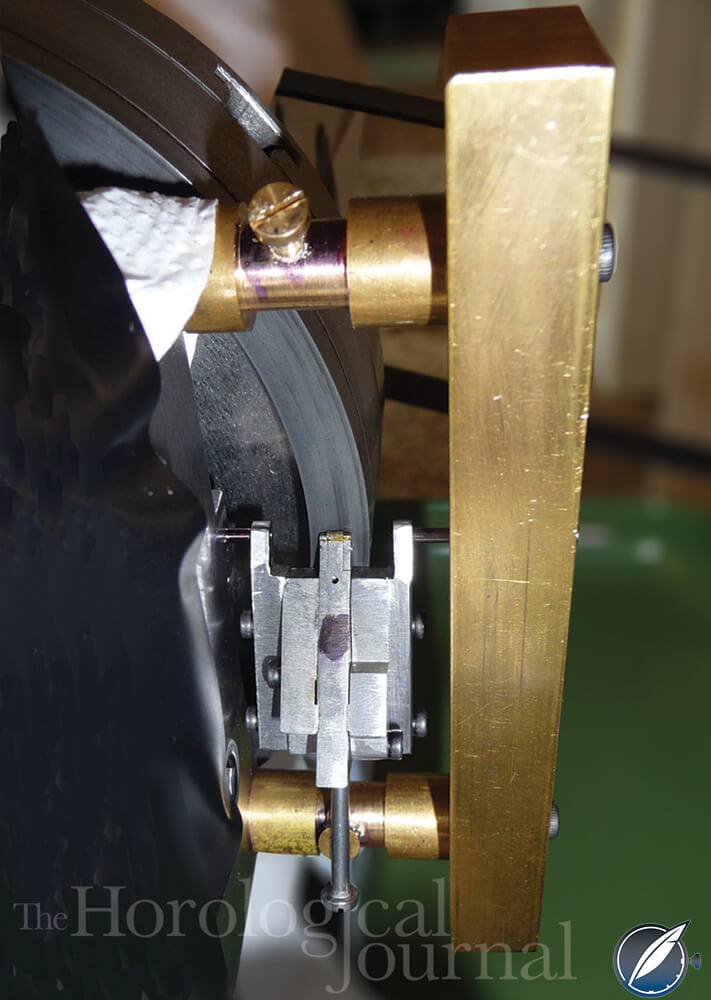
Pivoted pallet holder and lap mounted on the lathe to make the diamond pallets for Derek Pratt’s H4 reconstruction (photo courtesy British Horological Journal)
This allowed the diamond cylinder to be pivoted around its radius whilst contacting the outer band of the cast-iron skaife. Due to the small diameter of the radius to be ground on the diamond (0.6 mm radius), the holder’s female pivot points were set up in the Hauser jig borer using the microscope.
I initially charged the skaife with 8-micron diamond paste, but found this cut too slowly, so I tried a 14-micron variation. This sped things up a little and although the surface finish is quite rough at first, it improves as time goes on. I put this down to the diamond particles getting embedded in the surface of the skaife and breaking down in size.
Things progressed steadily for a while, only winding the cross slide in two or three microns at a time, although at this point I was only cutting the center of the curve and this, I think, was a soft plane. As I progressed round the edges of the curved back I truly found out the meaning of the word hard as I encountered the hard planes on either side of the center. It is difficult to believe that such a small area can resist the comparatively massive cast-iron skaife.
This really slowed things down and as the grinding and polishing continued I noticed a haziness forming around the hard planes. This was difficult to get rid of as one area was polished out another area of haziness would appear. I concluded this must be micro fracture, which Jonathan Hird mentions in his article and is present on the original pallets made by Harrison.
It is caused by trying to polish the hard planes. Eventually, as the curved back approached the correct shape and size, I reduced the micron grade of the paste, first down to 8 then 3 and finally 1 micron in an attempt to get a better polish. In truth, this doesn’t seem to improve the polish, it just speeds things up a little as the diamond particles don’t have as far to break down.
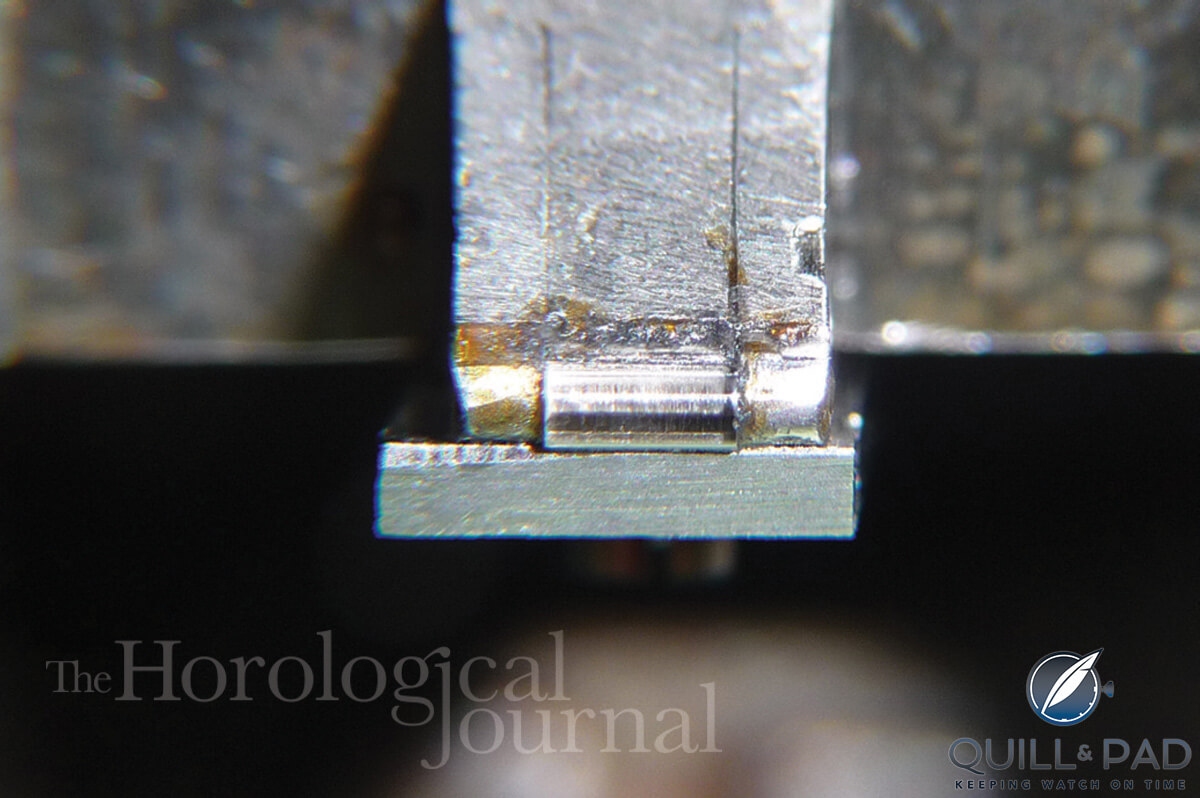
The diamond for the pallets for Derek Pratt’s H4 reconstruction clamped in the holder (photo courtesy British Horological Journal)
With the curved back as good as I could get it at this first attempt I moved on to the flat impulse face and the heel.
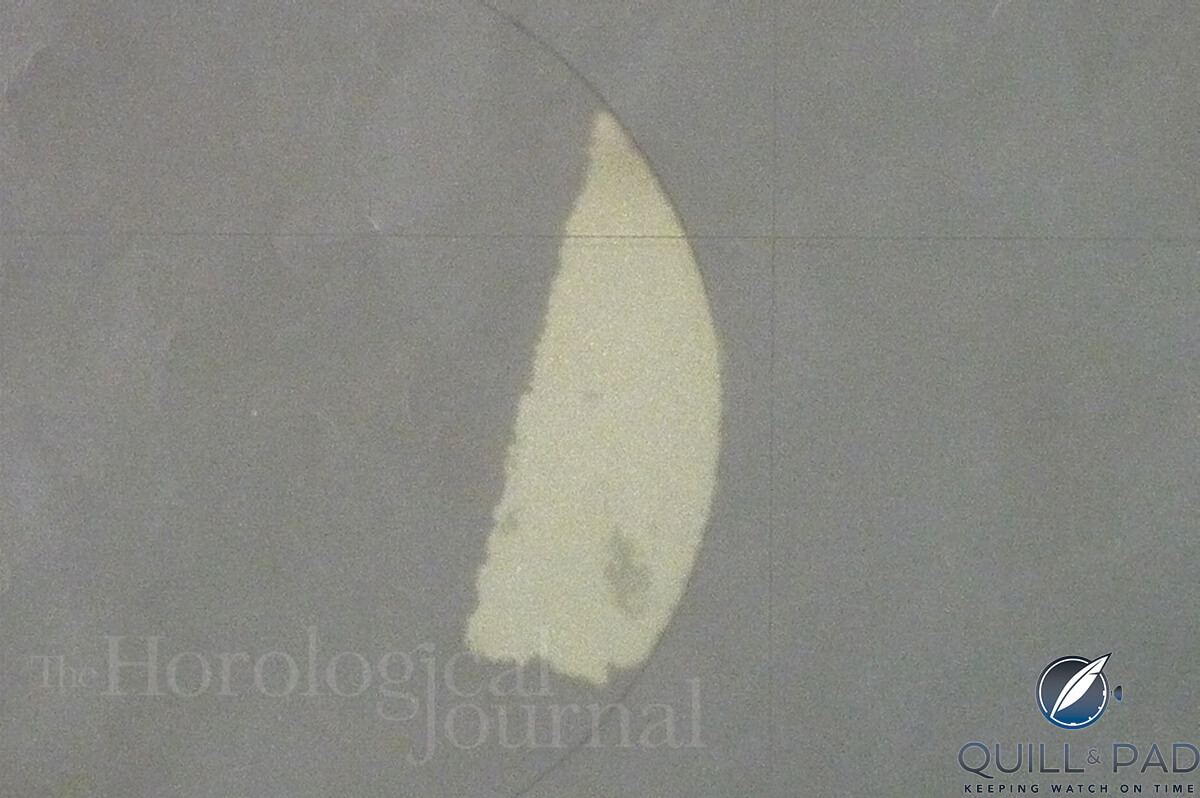
Checking the curve of a diamond pallet for Derek Pratt’s H4 reconstruction on the profile projector (photo courtesy British Horological Journal)
These surfaces were ground and polished quite quickly in comparison, using 8-micron diamond paste, by at first cutting along the length of the diamond (it seemed far more secure in its holder this way) before finally polishing across the width of the surface.
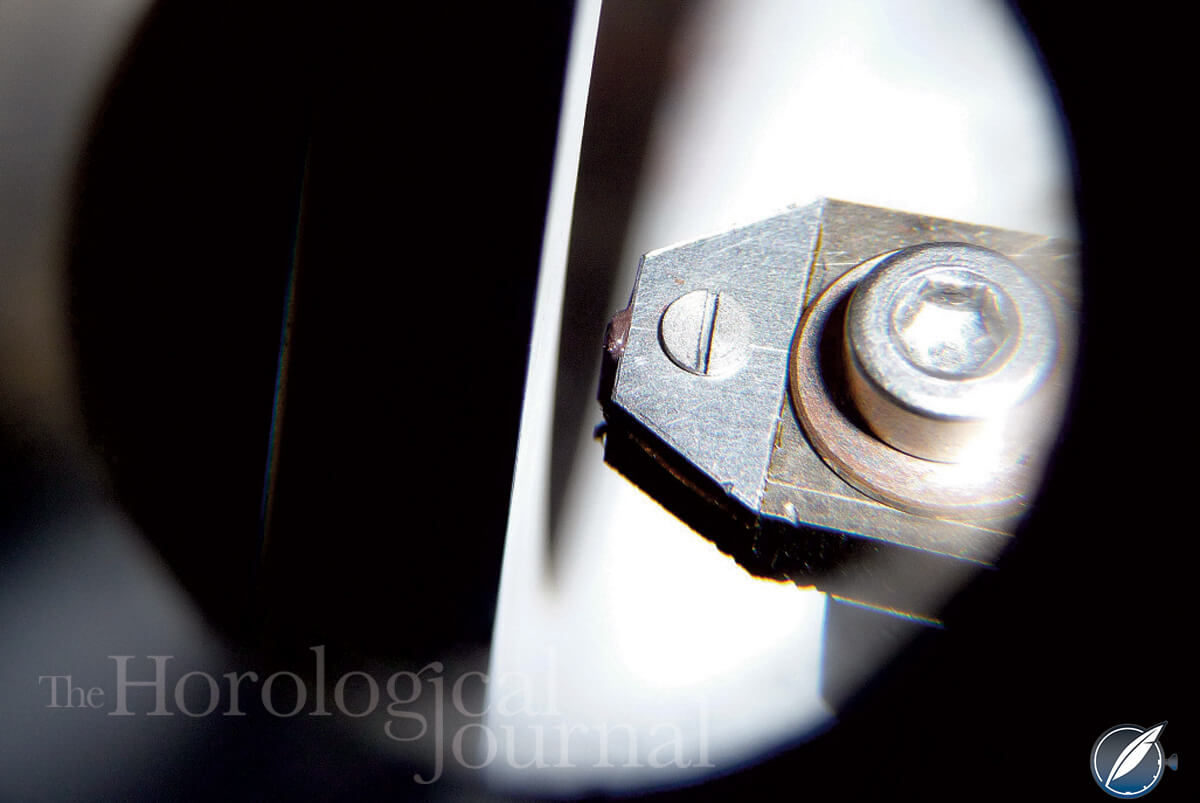
Grinding the impulse face of a diamond pallet for Derek Pratt’s H4 reconstruction (photo courtesy British Horological Journal)
All that was needed now was to round the edge between the impulse flat and the curved back. This is an easy task with sapphire, as all that is needed is a copper polisher rocked by hand and some diamond paste. Unfortunately this won’t touch diamond, so with great care I offered the almost finished pallet and its holder up to the slowly spinning skaife and gently rocked it back and forth. This gradually rounded the edge and, although I was constantly in fear of the edge chipping, it held up. It seems that, as well as being harder than sapphire, diamond is also tougher as I am convinced that sapphire would have chipped under such conditions.
Conclusion
The pallet was now finished.
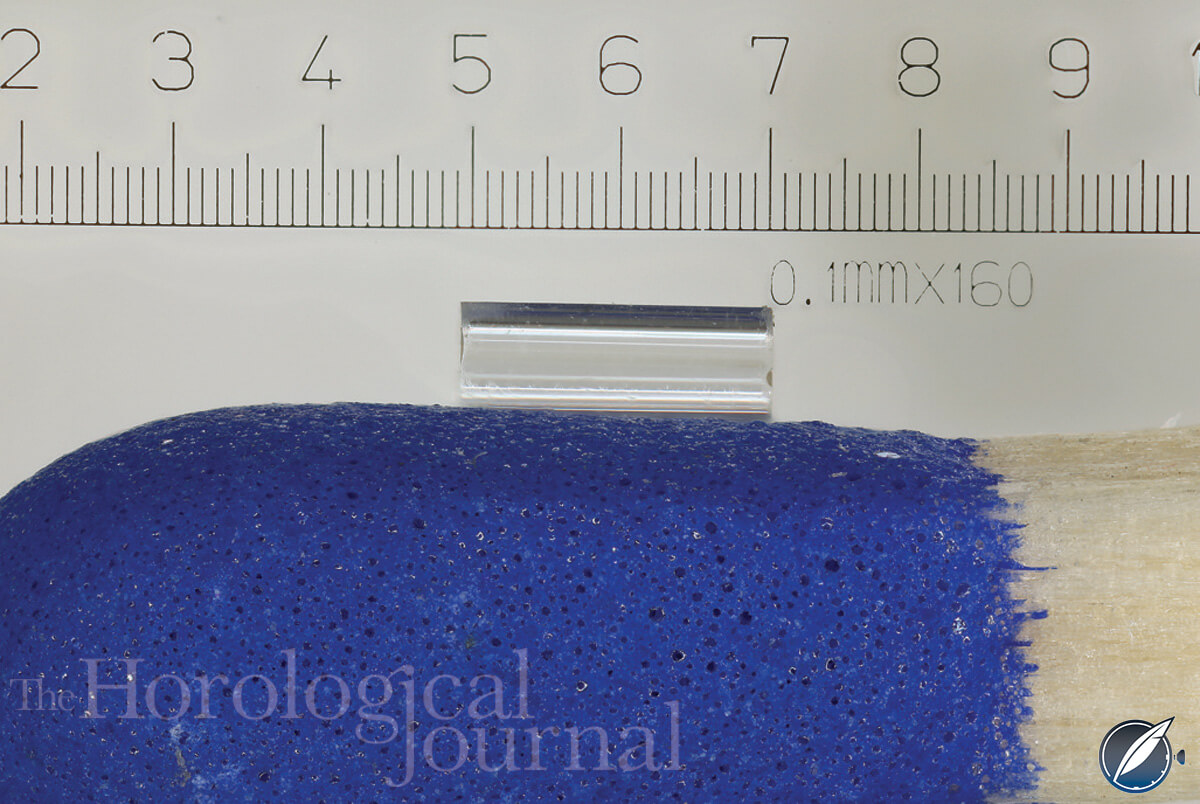
A finished diamond pallet for Derek Pratt’s John Harrison H4 reconstruction next to a match head (photo courtesy British Horological Journal)
Dimensionally, it was close to the drawing (the curved back coming out slightly larger than planned at 0.63 mm radius against the proposed 0.6 mm radius), and I was happy with the finish on the flat impulse face and the heel as it compared well with Derek’s pallet. I was less pleased with the finish on the curved back although it had been achieved in a manner that must have borne some resemblance to the way Harrison produced the originals; it exhibited the same sort of haziness towards the extremity of the curve.
This does not compare well with the finish that Derek achieved on the curved back of his pallet. I am still not entirely sure why it was harder to achieve a good finish across the width of the curved back. It may be that polishing in that direction around a curve requires a setup with more rigidity than mine. Having said that, after inspection by the Frodsham team, the consensus was that the pallet was of similar quality to the original, and so the pallet was paired with Derek’s and mounted in the replica, where they have performed well.
All in all, a very interesting exercise.
You can buy a DVD of the film about Derek Pratt’s H4 reconstruction at http://www.bdvideos.co.uk/site/shop/horology/a-detailed-study-of-h4 (all profits go to the charity Prostrate Cancer UK).
For more information, please visit www.frodsham.com/harrison-h4 and you may enjoy www.amazon.com/Longitude-Genius-Greatest-Scientific-Problem.
For part 1 in this series please see Derek Pratt’s Reconstruction Of John Harrison‘s H4, The World’s First Precision Marine Chronometer (Part 1 of 3).
For part 3 click Making The Escapement, Remontoir, And Timing For Derek Pratt’s Reconstruction Of John Harrison‘s H4, The World’s First Precision Marine Chronometer (Part 3 of 3).
We thank The Horological Journal for permission to republish this article.
Trackbacks & Pingbacks
[…] You may also enjoy Derek Pratt’s Reconstruction Of John Harrison‘s H4, The World’s First Precision Marine Chronometer (Part 1 of 3) and Making The Diamond Pallets For Derek Pratt’s Reconstruction Of John Harrison‘s H4, The World’s… […]
[…] may also enjoy reading the second part in this 3-part series, Making The Diamond Pallets For Derek Pratt’s Reconstruction Of John Harrison‘s H4, The World’s… and The Life And Times Of Legendary Independent Watchmaker Derek […]
Leave a Reply
Want to join the discussion?Feel free to contribute!