Hairsprings: Origins, Progress, And (Dare I Say) Exciting Future
There ain’t no words for the beauty, the splendor, the wonder of my
Hair(spring), hair(spring), hair(spring), hair(spring).
Flow it, show it, long as the Swiss can grow it, my hair(spring)!
The Cowsills didn’t know back in 1969 that they weren’t just singing about the hair on their heads in their aptly named song “Hair,” but to my ear were also singing about the wonder of material science that is the watch’s hairspring!
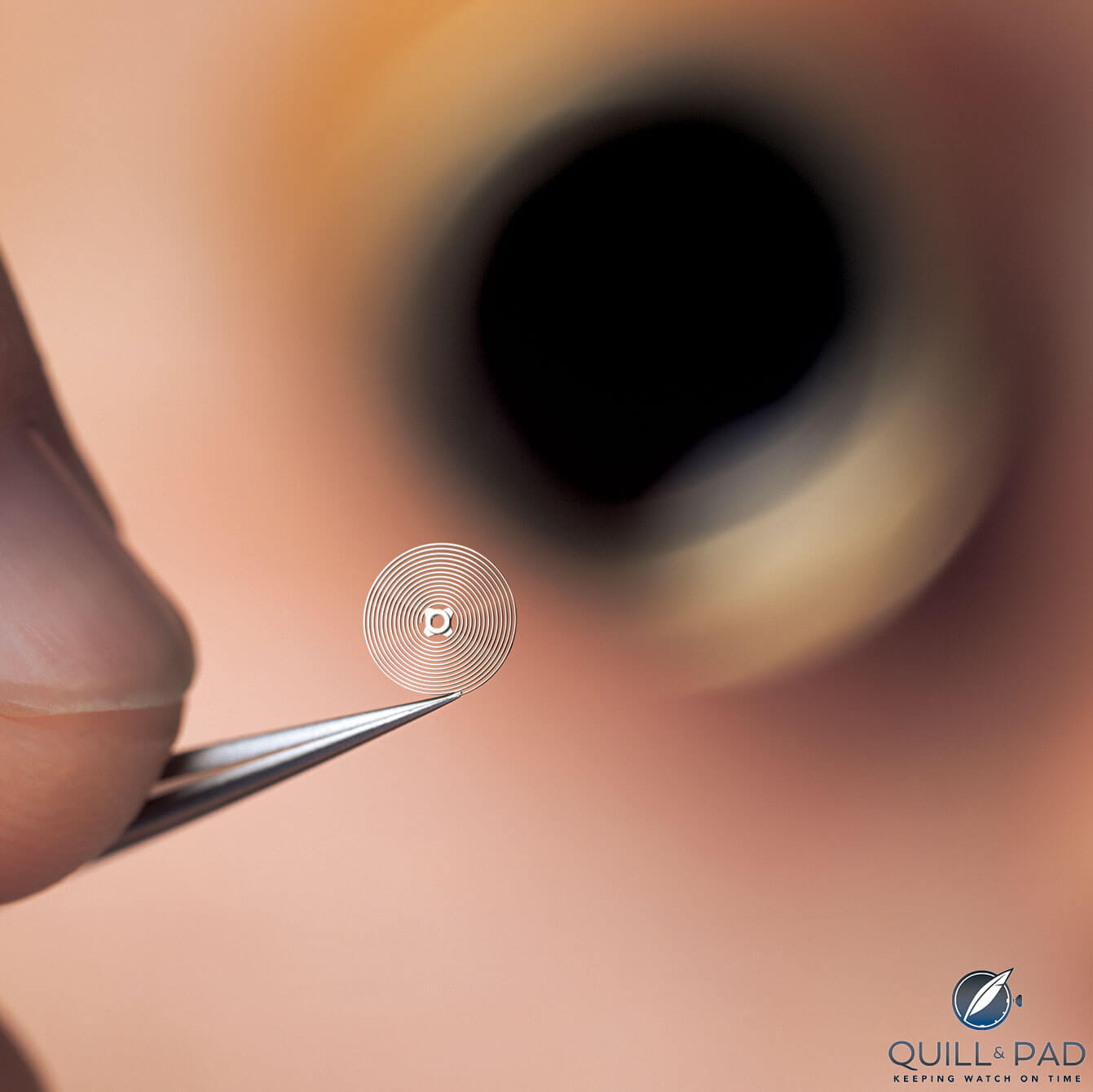
A hairspring at A. Lange & Söhne
The tiny, delicate, nearly impossible-to-create hairspring/balance spring is the one of the biggest advances for modern scientific technology there is, as the accurate measurement of time intervals greatly expanded research methodology in nearly every discipline of science to date.
The hairspring had been integral to one of two leading methods of measuring time (the other is the pendulum) for nearly 300 years until electric clocks had securely displaced balance springs and pendulums as the most accurate timing mechanism.
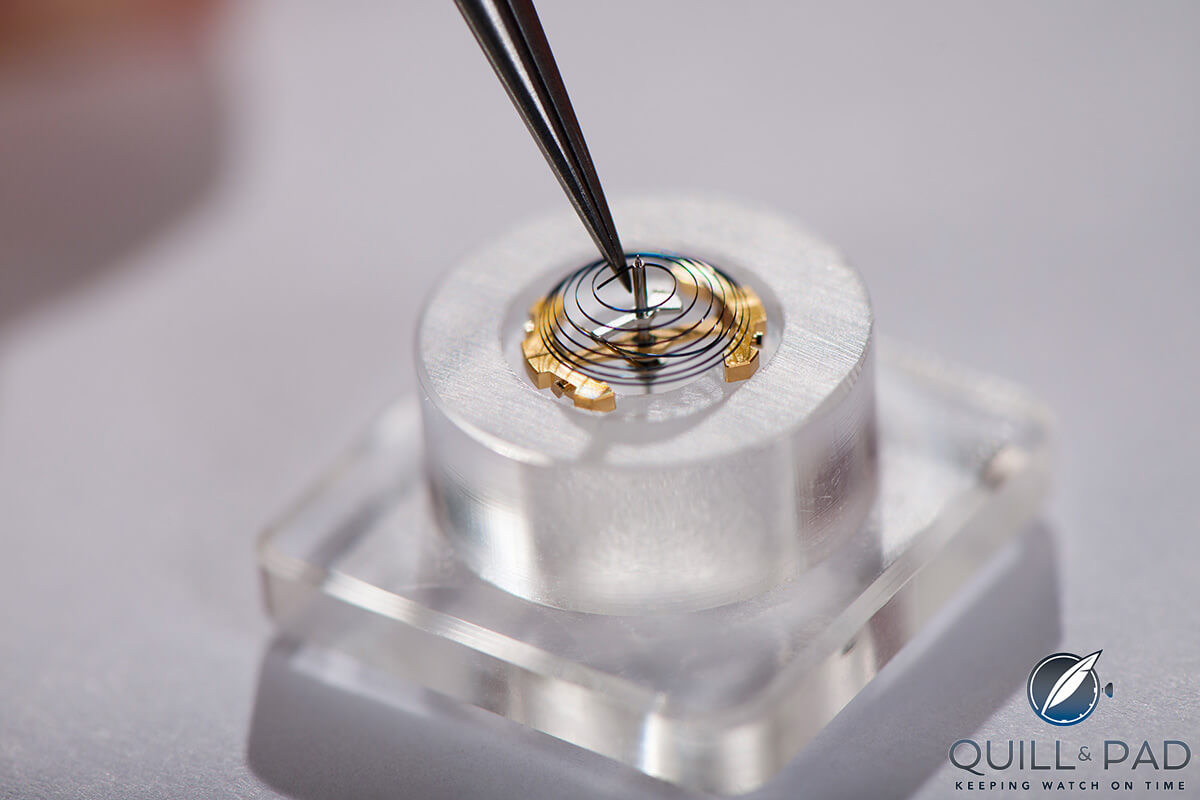
Semi-spherical hairspring in the Jaeger-LeCoultre Gyrotourbillon
Over that time, a great variety of advances were made in hairspring technology. But those advances have never really stopped, and there is still a vibrant effort to create ever more accurate and consistent hairsprings from a variety of materials. The research behind hairspring technology is probably still the most advanced research being done in the watch industry.
The delicate hairspring has such an important role in keeping a watch consistent and accurate that some companies invest millions in research and development, leading to a slew of developments in the last few decades.
Today I want to break down exactly what hairsprings have been historically and what they have become.
What is a hairspring?
Let’s kick this off with the basics: what is the hairspring?
The hairspring is conventionally a flat spiral of steel that is finer than a human hair. It attaches to the balance wheel and, after the balance wheel receives an impulse from the escape lever, it expands (or contracts), thereby limiting the balance wheel rotation’s before returning it to the beginning. The process then repeats in the opposite direction, often occurring between five and ten times a second.
Its precise size, shape, and mounting position leads directly to the balance wheel’s frequency, which, once combined with the appropriate gearing, determines a watch’s rate and accuracy.
When the hairspring was first invented, it consisted of a somewhat crude semi-spiral of steel wire that was attached to a balance wheel. The early hairspring didn’t have many spirals, making it inconsistent as it expanded and contracted during rotation due to uneven “breathing.”
These early hairsprings weren’t hardened or tempered, either, so the spring force varied greatly and tended to weaken over time, not to mention that corrosion was also an issue with the unstable steel. This is where the first foray into exotic materials began.
Some watchmakers, including John Arnold (1736-1799), experimented with gold-alloy hairsprings as it was a much better understood metal during that time and could be more easily shaped; on top of that it was completely corrosion-free.
But like most metals, it also suffered from fatigue over time, gradually weakening and introducing inconsistent rates. I also have seen a few examples of movements featuring palladium hairsprings, likely attempted for reasons similar to gold.
Eventually the art of hardening and tempering steel was introduced by John Harrison (1693-1776), greatly reducing the effects of metal fatigue as well as corrosion over time and making much more pliable and long-lasting hairsprings. This led to the development of much more consistent hairsprings as experimentation with the form factor was added to just trying to get a material that even functioned as a spring.
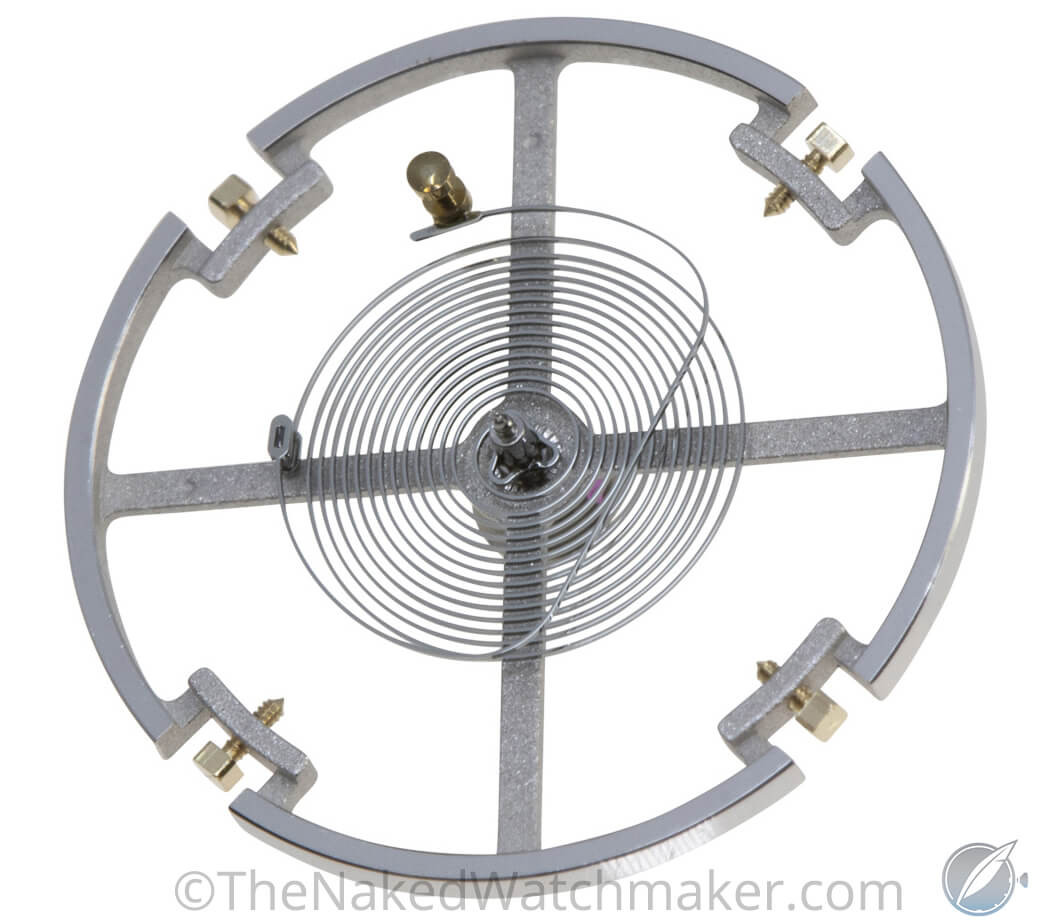
The balance spring of the Breguet Tradition Automatique Seconde Rétrograde 7097 contains a silicon balance spring with Breguet overcoil
This is when technicians began adding spirals and calculating the optimal terminal curves to allow for increased isochronism and consistent rates. But as these became better, other issues took center stage like the effects magnetism and temperature fluctuations would have on the now more accurate hairsprings. These effects had already been discovered and some attempts at remedying them had been undertaken, though none were successful.
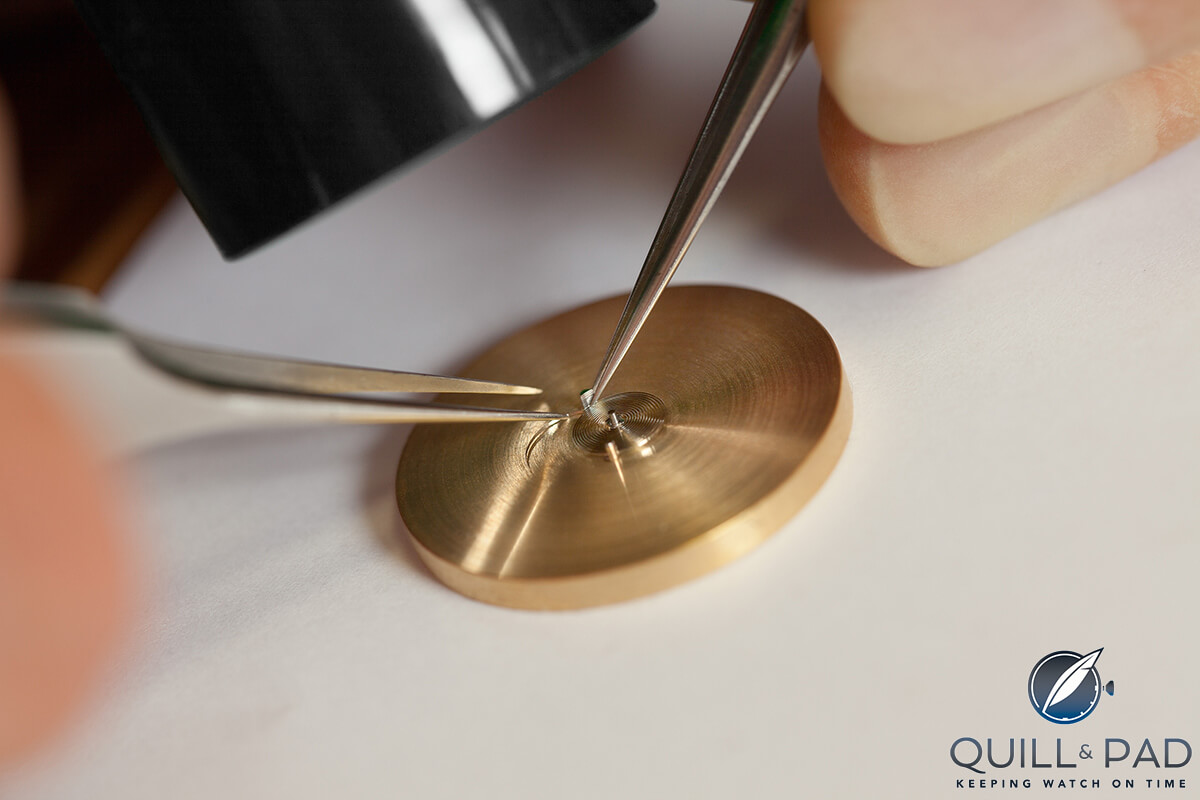
Bending the first dogleg of the hairspring of the Habring2 Felix
This led to more research and development. Many watchmakers, most notably Abraham-Louis Breguet (1747-1823) and the firm Arnold & Dent, experimented with glass hairsprings as the material provided a lot of positives over the aforementioned tempered steel.
In the plus column, it was non-magnetic, corrosion-free, much less susceptible to temperature changes, had increased purity (as the production process of glass was much cleaner than that of metal alloys), and it even had lower susceptibility to inertial issues (bumps and shocks) due to a lower density. The glass hairsprings were actually rather robust and seemed to be a viable alternative.
Alas, it was not meant to be as other negative issues also became apparent. First, glass is never truly a solid, which means it can move and change over time, basically leading to disintegration as a hairspring. It also was tricky to attach the ends to metal components, and it was practically impossible to adjust or modify the spring once formed.
But the nail in the coffin was the rate change over time. Like metals, glass can fatigue and weaken, leading to a change in rate. While steel hairsprings will have a rate that accelerates over time from these effects, that of glass is even worse.
This meant that especially for use during nautical navigation the calculations would change over time and sailors could end up way, way off course. Steel hairsprings proved less susceptible to this rate change and when combined with forms such as a helix spiral resulted in much more accurate timepieces over much longer periods of time.
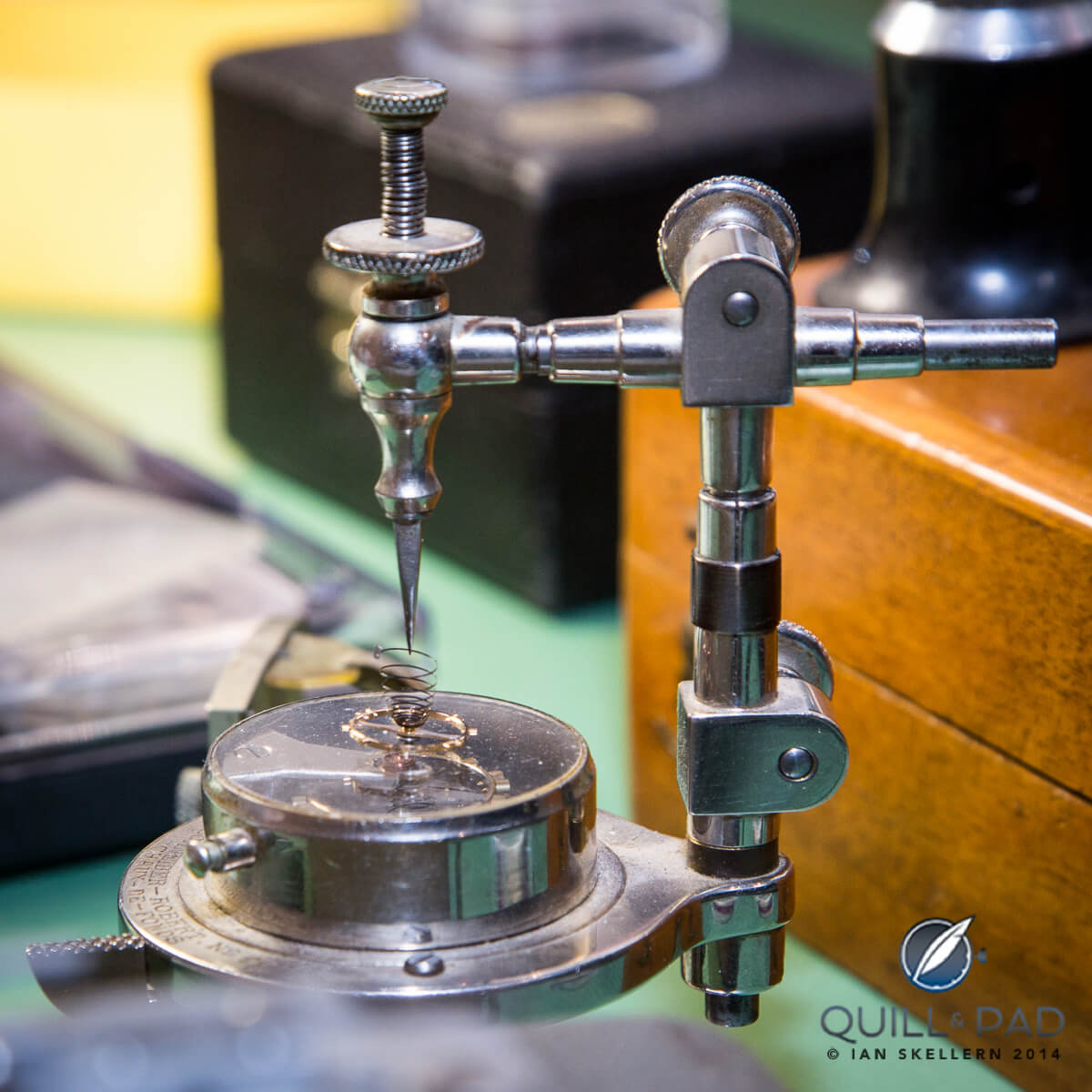
Vibrating a hairspring: the finish of the tweezers on the tool from which the hairspring is suspended is particularly important to get the precise vibrating point for the active length of the spring, which ensures good precision timing
Moving hairsprings toward the modern era: Invar, Elinvar, Nivarox
For many years, no dramatic changes developed due to the hairspring’s already impressive abilities aside from refinements in form and some improvement in material quality.
The balance spring had come a long way from the original by the turn of the twentieth century, and thanks to Swiss physicist Charles Édouard Guillaume (1861-1938) it was about to get better in a significant way.
Guillaume developed a nickel-iron alloy named Elinvar that was corrosion resistant, almost non-magnetic, but most importantly was nearly unaffected by temperature changes making it perfect for hairsprings as it was more stable than anything that had come before.
Elinvar – a contraction of the French words elasticité invariable (“invariable elasticity”) – was Guillaume’s follow-up to his 1896 invention of Invar, a similar alloy that had fairly comparable properties (and helped Guillaume win the 1920 Nobel Prize in Physics for his discoveries).
Elinvar was immediately put to use for various scientific apparatuses and watch and chronometer hairsprings. By the early 1930s an even better nickel-iron alloy was developed, this time by Dr. Reinhard Straumann in Waldenburg, Switzerland. The name of that alloy was Nivarox.
Nivarox– a contraction of the German words nicht variable oxydfest (“invariable non-oxidizing”) – is a fracture-resistant, self-compensating, corrosion-free, and antimagnetic alloy consisting of seven alloying elements.
Nivarox became the most widely used alloy for watch hairsprings from then on, used in approximately 90 percent of all mechanical watches by the year 2009. The company that Straumann founded went on to develop another alloy named Nivaflex, though this did not surpass the broad popularity of the original Nivarox.
But something happened between the 1930s and now that altered the future of watchmaking and hairspring research for the second half of the twentieth century: the quartz crisis.
This has nothing to do with electricity and the invention of the electric clock. Electronic clocks were first invented in 1840 and had slowly been developed over the ensuing century, while the first electric watches made their debuts in 1952, with the first commercially available watches sold in 1957.
These developments didn’t seem to change the progress of advanced mechanical watchmaking (probably because electric clocks and watches were still largely mechanical in nature), but when quartz watches appeared in 1969 with the debut of the Seiko Astron the whole world shifted.
The quartz movement was an order of magnitude more accurate and consistent than any mechanical or electro-mechanical movement that had preceded it.
What’s more, these became cheap as time went on, making them very appealing to the average consumer.
The mechanical watch industry was shattered. It took nearly 20 years for it to resemble even a shadow of its former self. But once the upswing came, a zeal for research and development returned, if at fewer companies, and mechanical progress began to march again.
Advanced hairsprings of the modern era: it gets really interesting here
At first during what is known as the mechanical renaissance, brands focused on complications and switching to a luxury business model, which is what the 1990s was all about.
But by the year 2000 the “traditional” complications were becoming much more common (as common as high complications in a once nearly-extinct industry can be), and brands started to actively look at making new things.
This required looking at every component of a watch movement and seeing where innovations had been lacking for a while. Attention turned to the hairspring once again, and here’s where it began to get really interesting.
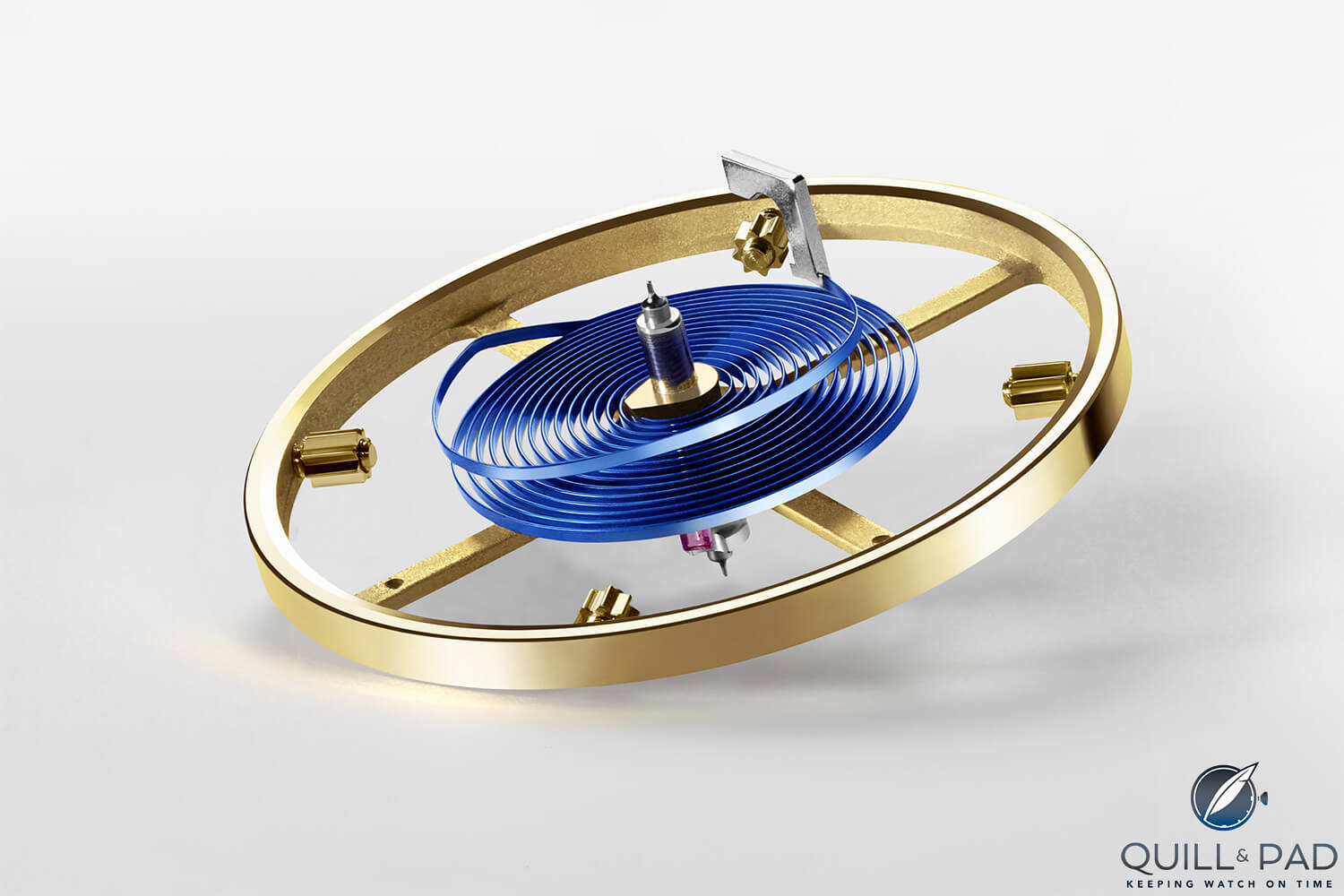
Rolex Parachrom hairspring
Rolex made the first big debut in the year 2000 with its now-famous Parachrom hairspring, which is an alloy of niobium, zirconium, and oxygen (for more see The Golden Age Of Rolex Movements Part II).
Formed in a similar way to Nivarox hairsprings, the Parachrom hairspring has even better anti-magnetic properties and a dramatic improvement in resistance to shocks.
According to Rolex, the Parachrom hairspring is ten times more accurate when experiencing shocks (I’m assuming this relates to deformation or rate consistency) over traditional hairsprings.
Also, due to its high-temperature thermal vacuum treatment after forming, the Parachrom hairspring is a striking blue hue, a color that became popular with the next big hairspring development: silicon.
Rolex, Patek Philippe, Ulysse Nardin, and the Swatch Group all formed a research consortium by partnering with CSEM (Swiss Center for Electronics and Microtechnology) along with its IMT (Institute of Microengineering) in Neuchâtel and the EPFL (Swiss Federal Institute of Technology) in Lausanne for the development of the silicon hairsprings, allowing development costs to be shared.
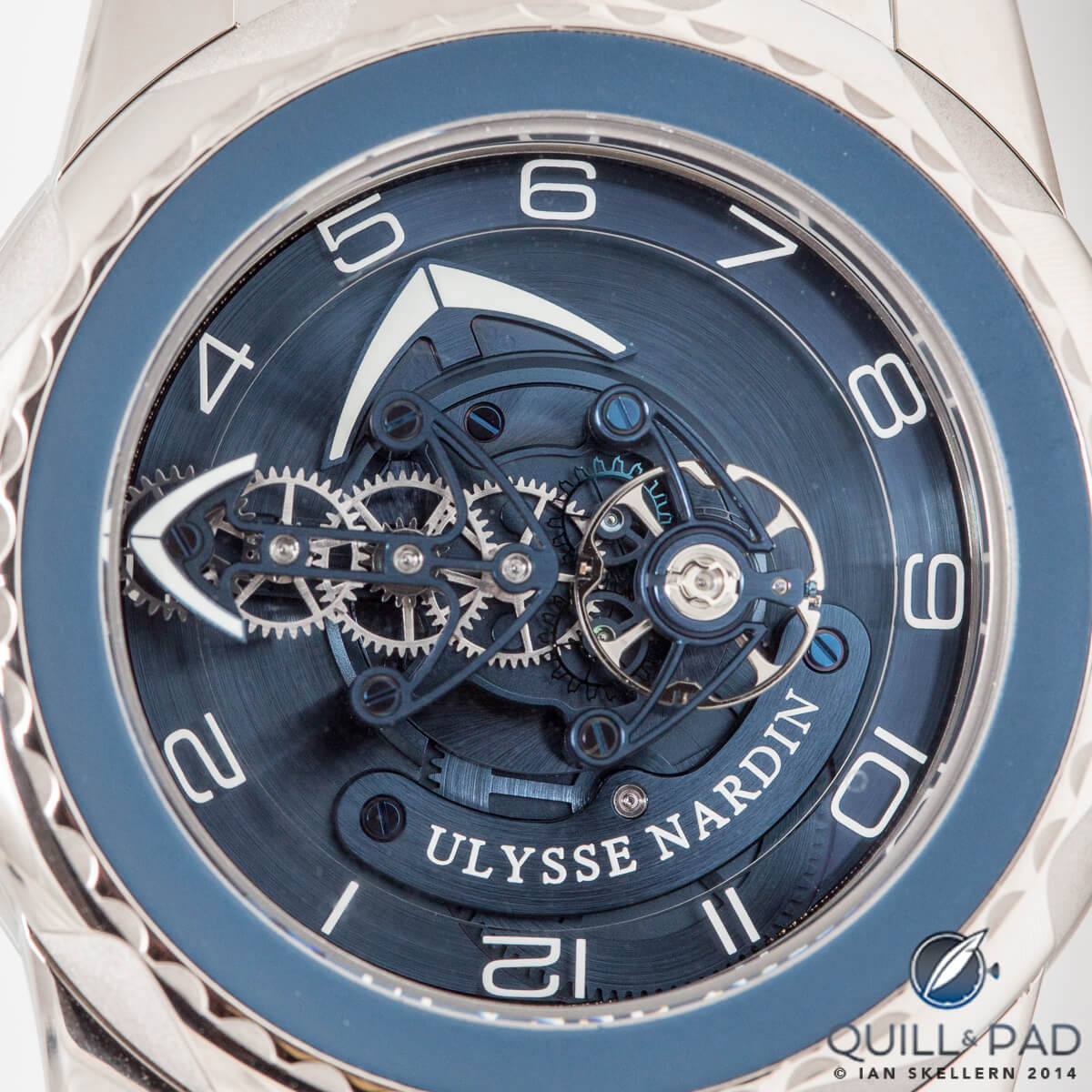
Ulysse Nardin Freak Blue Cruiser
Ulysse Nardin was the first on the scene with silicon components in watches, releasing a silicon hairspring in 2001 in the Freak. Over the next decade or so, most of the major players followed suit, with Patek Philippe introducing the Spiromax in 2005 (Reference 5250 Advanced Research), the Swatch Group via Breguet in 2006, the Rolex Syloxi appeared in 2014, and Richemont’s brands finally joined the party in 2017 with the Twinspir, which made its debut in the Baume & Mercier Clifton Manual 1830.
But why is silicon good for hairsprings? Like everything else, it comes down to how it acts within nature and how difficult it is to manufacture.
Silicon hairsprings are better in nearly every category over Nivarox hairsprings as they have better temperature stability, are completely non-magnetic, have low inertia, are perfectly homogeneous, and have better shock resistance. Silicon is more fragile, and it may shatter or break with hard enough shocks, but these hairsprings have already performed beautifully for years (and extreme shocks are still a problem for almost every watch).
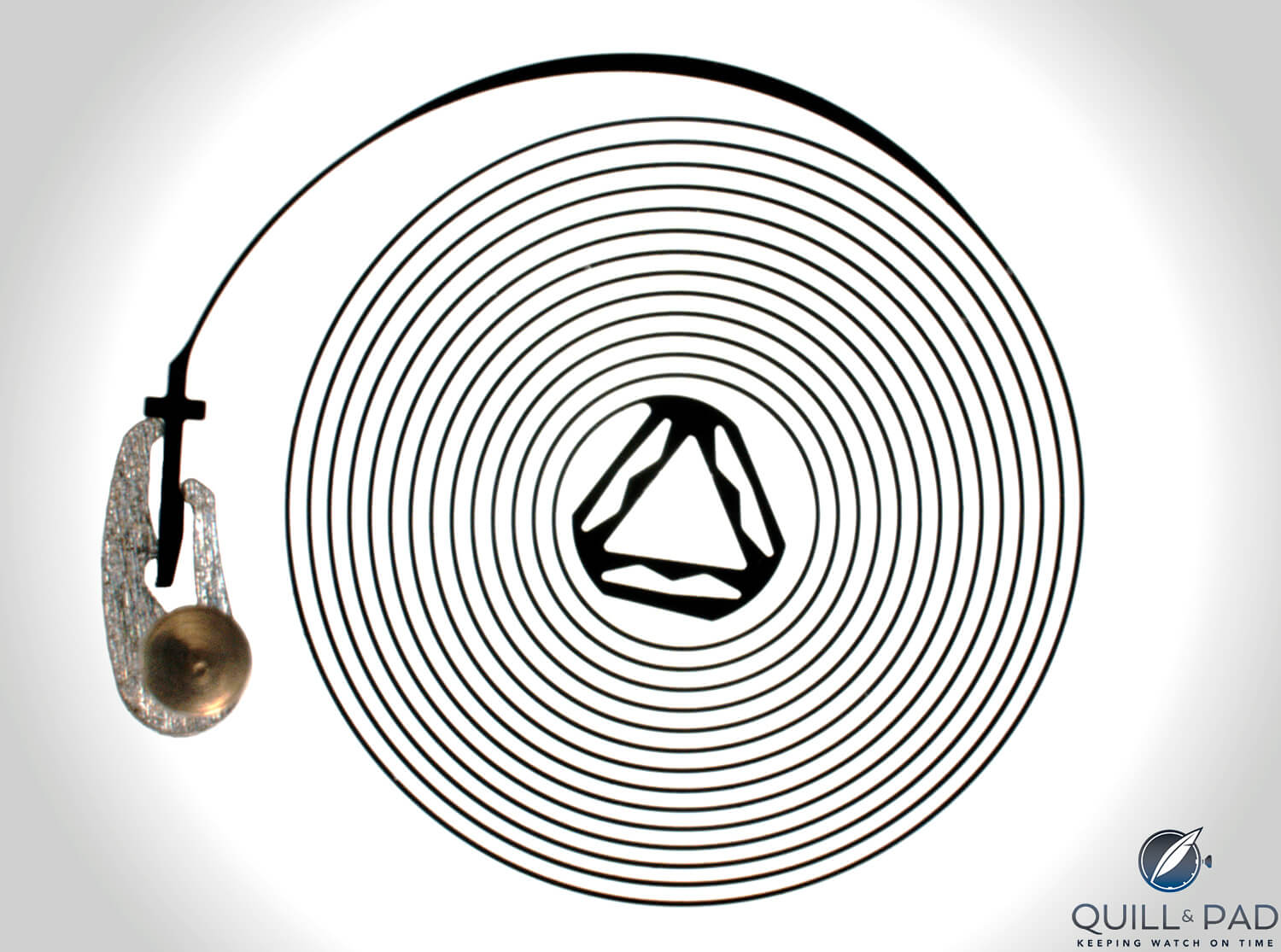
Patek Philippe Spiromax silicon balance spring
Some attempts to solve this have seen coatings added to the silicon structure, including diamond and silicon dioxide, which lead to more durable components.
Silicon components are made using a photolithographic Deep Reactive Ion Etching (DRIE) process that builds the silicon atom by atom (after using photolithography to create the shape for it to adhere to), meaning the material is fundamentally perfect and also can be shaped in any way desired.
That ability has allowed for an explosion of research into forms once again as every aspect of the spring can be tailored for conditions pertaining to movement, frequency, and intended use. Any desired feature can be built in, also reducing the need for additional components and creating hairsprings that are lightyears ahead of the very first steel hairsprings.
And now: yet even more hairspring advances
Given the quality and capabilities of silicon, one might imagine that brands might take it easy. But, when they have ideas, creative people don’t have the ability to sit still.
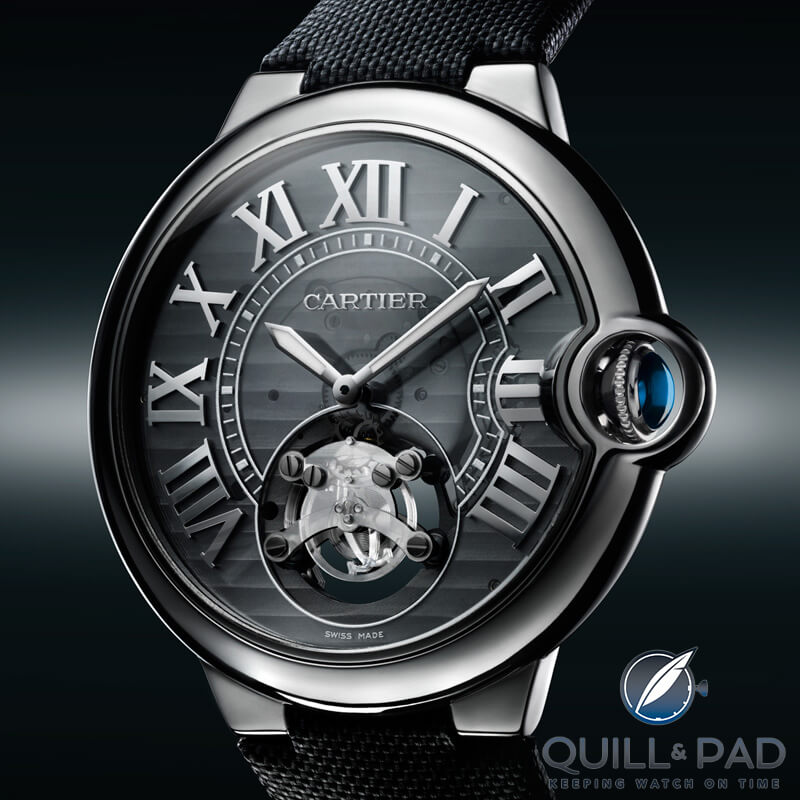
Cartier ID One concept watch
In 2009, Cartier introduced the ID One concept watch that was jam-packed with technology. One of its elements was another new hairspring material called Zerodur, a glass ceramic material of carbon crystal that is, like silicon, manufactured using the DRIE process.
This material, like silicon, is non-magnetic, homogeneous, shock resistant, and exhibits almost no thermal expansion. I have not seen a direct comparison of any figures, but I imagine they are pretty close in terms of capabilities.
Going a different route, in 2016 H. Moser & Cie & Precision Engineering AG introduced a metal hairspring akin to the Rolex Parachrom using a brand-new alloy, PE500. The material is an alloy of niobium, titanium, and oxygen that exhibits similar characteristics of being anti-magnetic, shock and temperature resistant, and formable – something still largely impossible with non-metallic hairsprings.
In 2017, Hong-Kong based Master Dynamic released its first patented hairspring made of silicon, but with an interesting new twist. I know I just mentioned that forming a non-metallic hairspring is largely impossible after it is created, but Master Dynamic has found at least one way, and it comes down to angles (and some heat).
If you didn’t know (I didn’t), silicon is anisotropic, meaning that based on the form of the cubic structure and the atoms that make up said structure, the physical properties differ depending on the orientation. And this can be used to advantage.
The difference leads to the ability to cut the silicon wafers (the base material used to produce the silicon components) at angles away from square, which Master Dynamic does at 45 degrees.
This produces a couple of benefits. The first is that bevels in the material can actually be formed using a second etching process, something not possible with the regular DRIE process. This helps direct stresses throughout the part and avoid sharp edges that become fracture points.
But even more interestingly, it allows the material to be manipulated, with the application of constant heat, to bend and kink the end of the silicon hairspring into a Breguet overcoil, making the Master Dynamic hairspring a combination of the best parts of both silicon and metallic hairsprings.
The end is folded over like a book to shape the overcoil, a key part of the patent for the hairspring. A truly impressive step in developing silicon fabrication techniques.
In 2018, the Swatch Group (owner of Nivarox) released another new metallic hairspring in collaboration with Audemars Piguet called Nivachron, which made its debut in the Swatch Flymagic early in 2019.
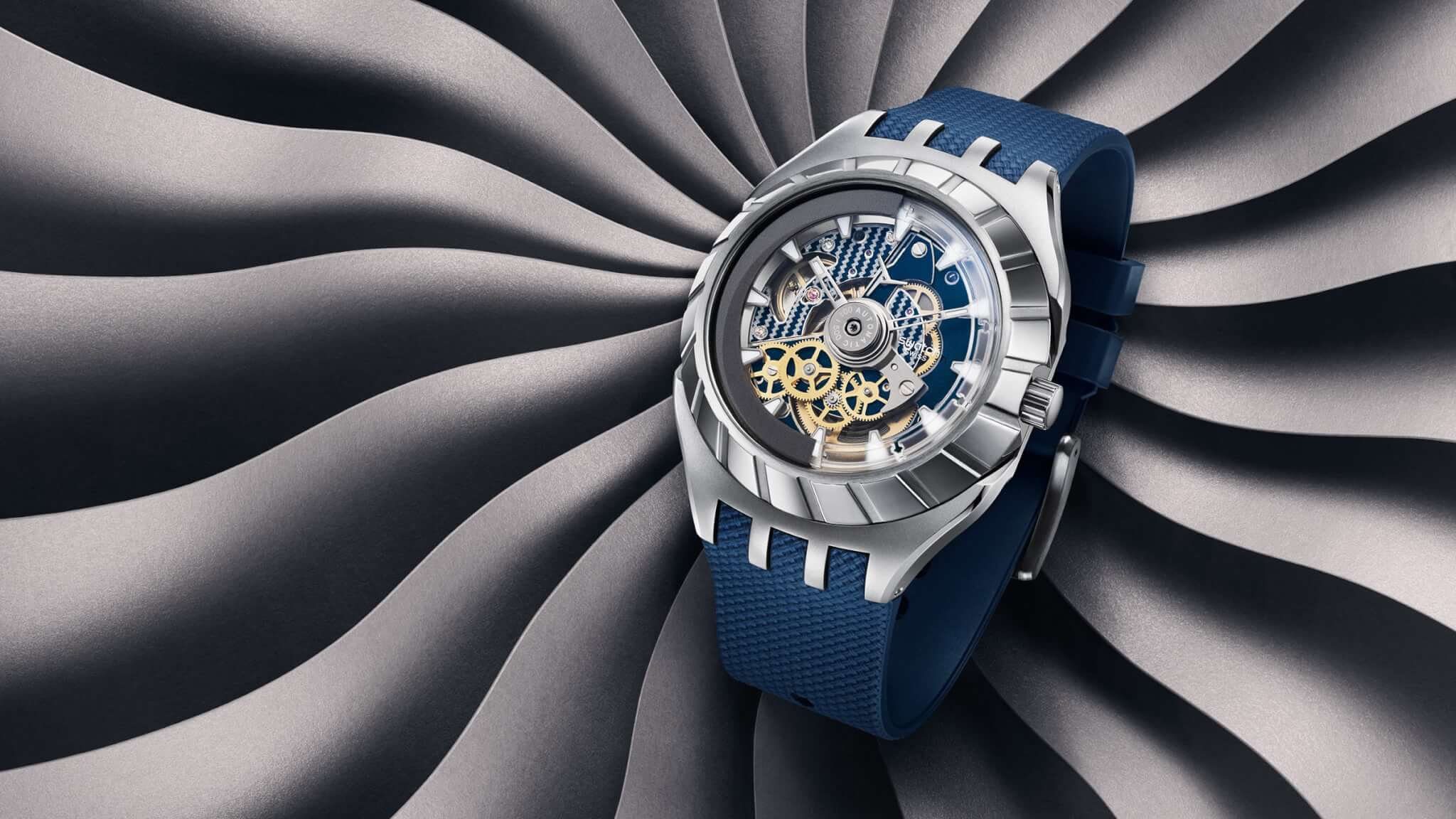
Swatch Flymagic
The reasoning behind going a bit more old school in terms of material is an attempt to ensure that future watchmakers will be able to repair watches with these hairsprings without access to original parts or high-tech DRIE equipment.
The Nivachron hairspring is titanium-based and extremely paramagnetic, which leads to much less susceptibility to be influenced by magnetic fields (supposedly a reduction by at least a factor of ten). Otherwise, the properties are likely similar to the Parachrom and PE500 materials.
Pushing the envelope hard: the TAG Heuer Isograph
But the innovation that has pushed the technology forward the most has to be the latest development from TAG Heuer, a carbon-composite hairspring called Isograph that is based on carbon nanotubes and their incredible structural stability and lightness.
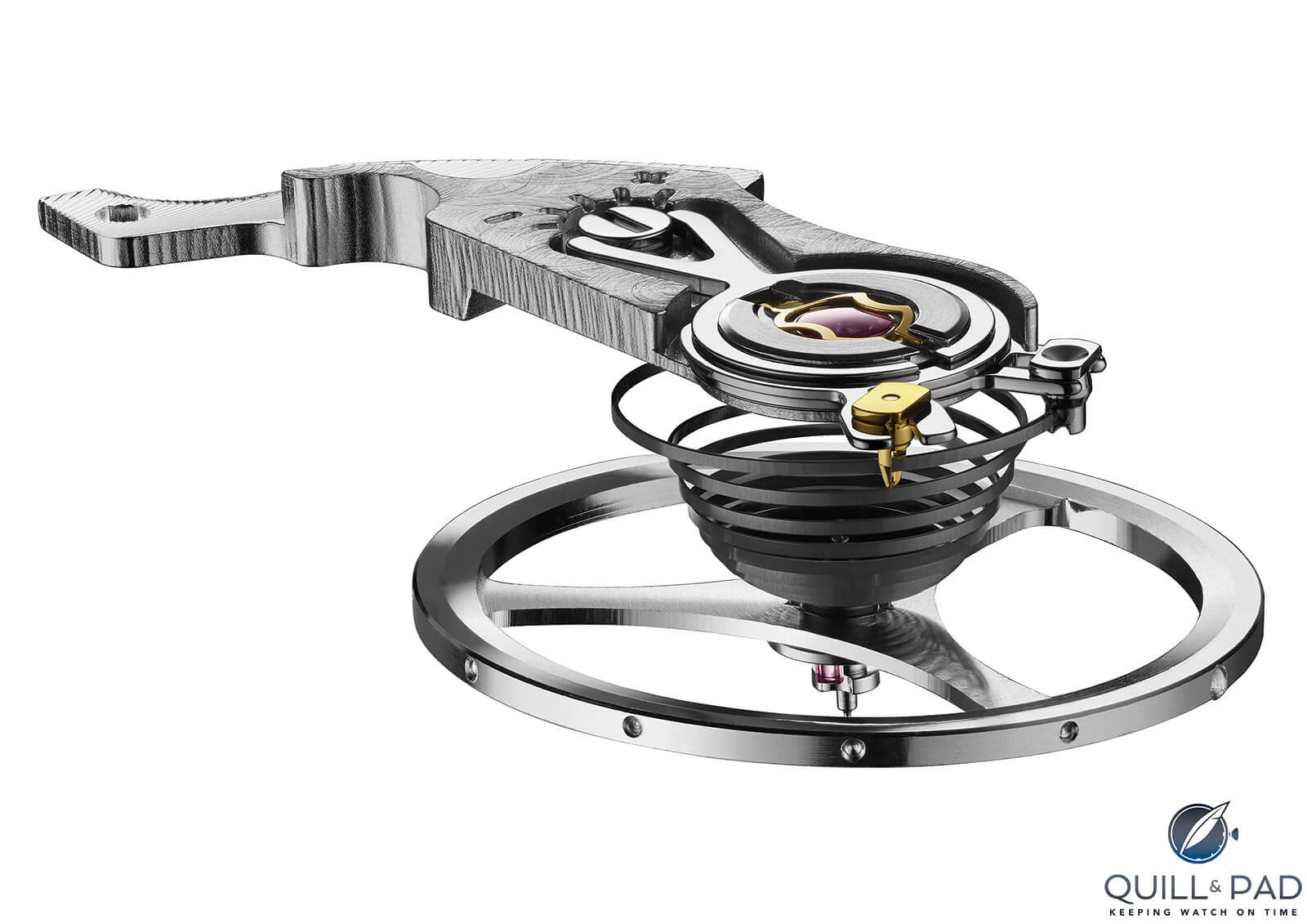
The Isograph, a carbon-composite hairspring, beats inside the TAG Heuer Autavia
This carbon composite material was one of the highlights of the 2019 fair season for me.
So how is it made and why is it good?
First, the shape of the hairspring spiral is created out of carbon nanotubes using a custom CVD process. Yet the nanotubes are empty and need to be combined with another material that supports and protects their structure, making it a composite.
Amorphous carbon is used to fill in the space inside and between the carbon nanotubes, and thanks to very stable covalent bonds it produces a functional material that behaves like a polymer composite (which is very flexible and resilient) but has physical properties of a crystalline structure (which is very strong).
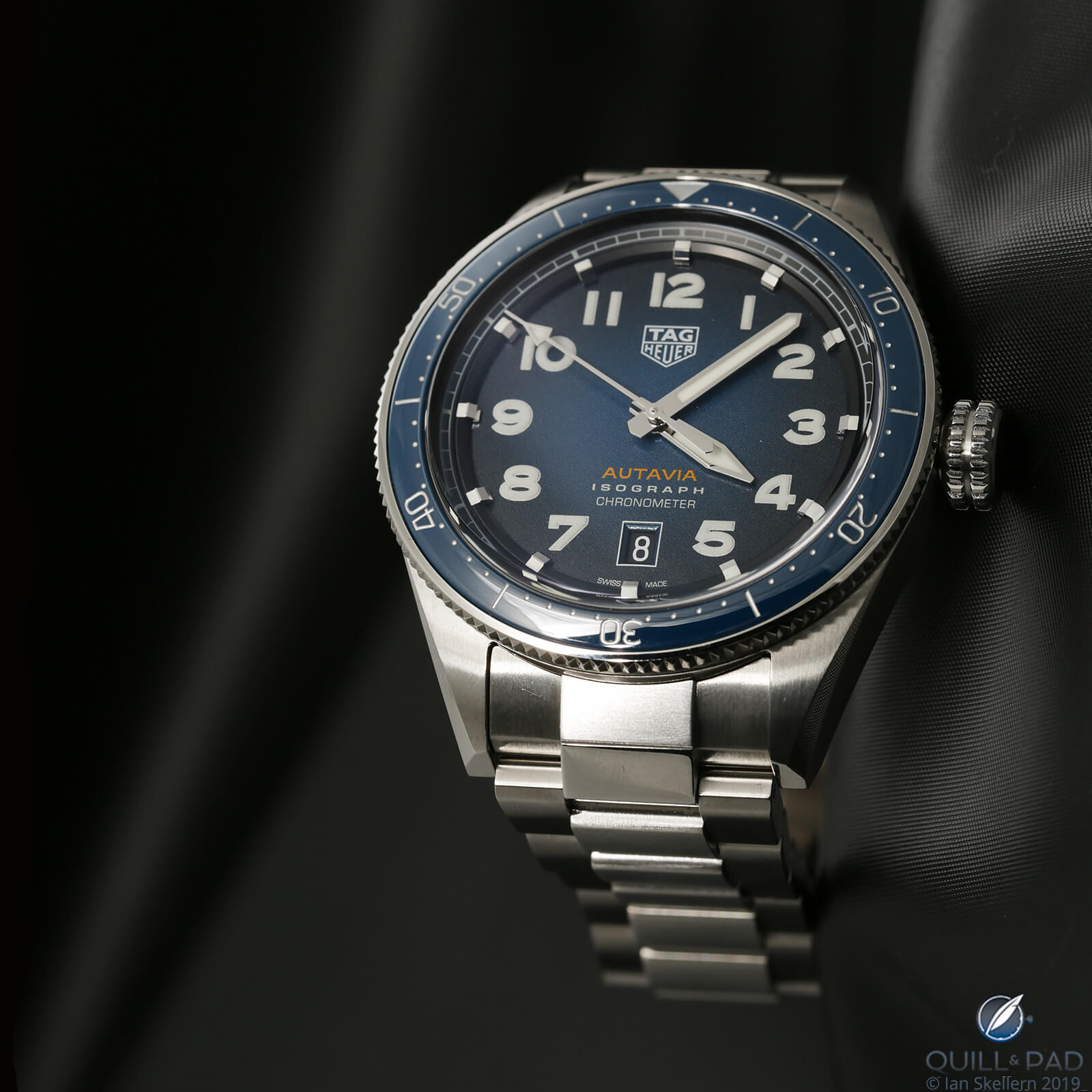
TAG Heuer Autavia Isograph
Basically, the carbon composite hairsprings are better in most ways over the silicon, which was already better in most ways over the metallic options: reduced density and sensitivity to shocks, non-magnetic, ultimately pure with complete control over the shape and therefore the dynamic properties. It is more thermally variable compared to silicon, but it comes combined with an aluminum balance wheel to offset that issue.
The carbon composite spring is incredible, demonstrating a level of research into new materials that has recently become the norm for high-end watchmaking. If you don’t believe me, check out what Zenith is also doing with its Inventor technology.
Every new hairspring that has come out in the last two decades as the modern era of watchmaking, research, and development has kicked into high gear is rather incredible when considering where the humble hairspring began.
Each research path is a different way to approach the same problem, and each one comes with positives and negatives, allowing for choices to be made for a variety of factors or constraints.
More importantly, the quartz crisis eventually led to a continuation of technical watchmaking as people eventually went on to develop new techniques, materials, and processes in an attempt to achieve the best mechanical watch possible.
Nobody really expects to beat quartz (or atomic) watches for accuracy, but that isn’t the point. The hairspring is a fundamental part of the scientific method throughout history and, with further developments and innovation, we remain part of that lineage.
Hairsprings are still utterly fundamental to mechanical watchmaking, and the additions over the last two decades are intensely impressive.
This rundown of history and developments scratches the surface of everything that goes into – and has gone into – the delicate hairspring.
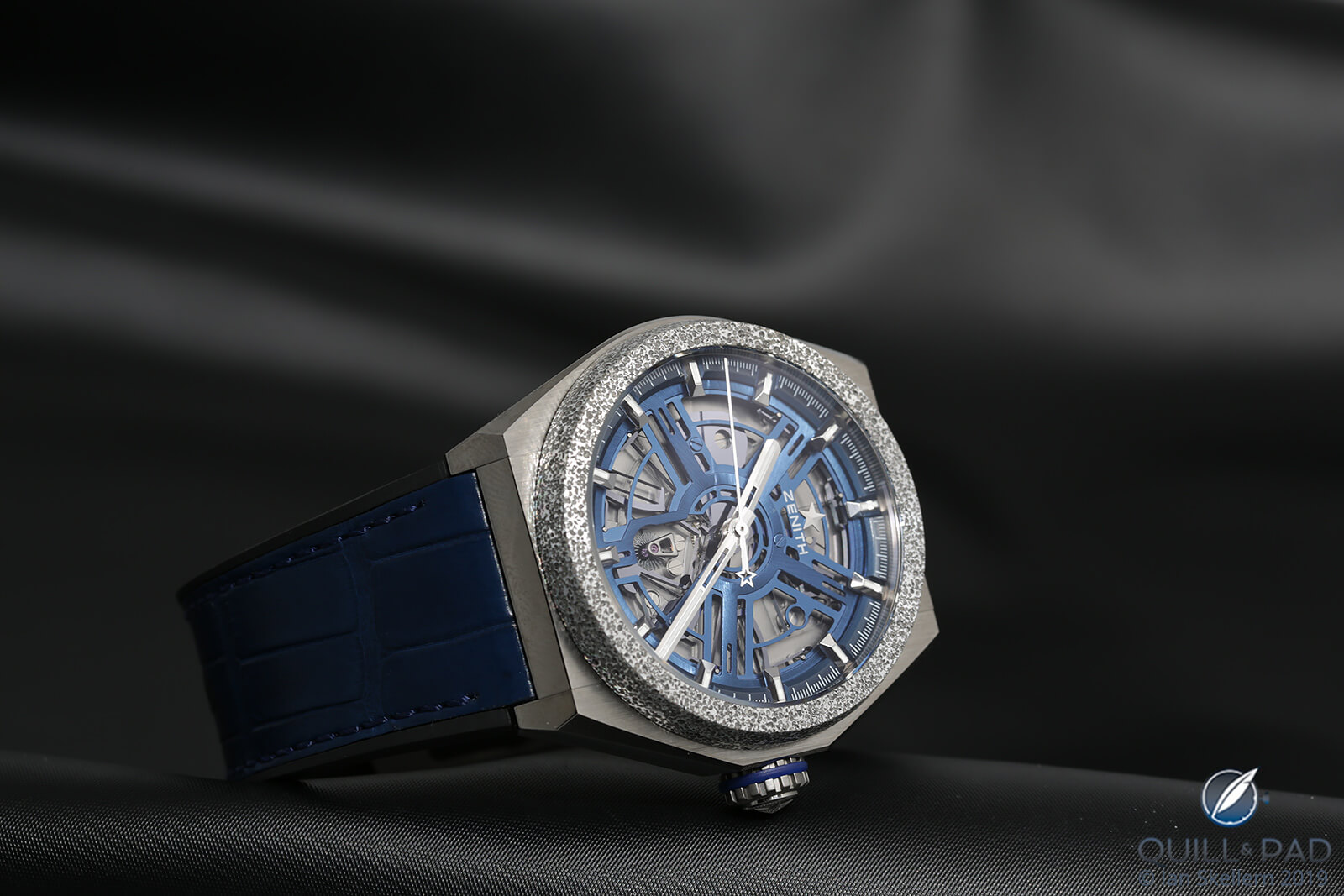
Zenith Defy Inventor
With the latest research and the developments into other entirely different types of oscillators – I’m looking at you again, Zenith – there is going to be a lot to keep an eye on over the next two decades.
Technology drives innovation, and as tools, materials, and designs improve the sky really does become the limit!
You may also enjoy:
Measuring The Time Between The Seconds: The Truth Behind High-Frequency Movements
TAG Heuer Autavia Isograph: Carbon-Composite High-Tech Hairspring For All
Is Silicon Here To Stay In (Rolex) Watch Movements?
Quartz: Past, Present, But No Future?
Silicon: A Closer Look At The Material That Unleashed A Refreshing Range Of Haute Horlogerie Ideas
Zenith Defy Inventor: Experimental Compliant Tech Goes Into Serial Watch Production
Leave a Reply
Want to join the discussion?Feel free to contribute!
A good read, very interesting. Does Richemont have the rights to use silicon hairsprings? I can’t remember where I read it, but I could swear there was something about them getting their wrist smacked by the consortium (Swatch/Rolex/Patek) and backing off.
Silicon hairsprings are not patented per se, what is patented is the fact to oxydize the right amount on the surface of the hairspring for thermal compensation. So maybe those outside the consortium use another technique for thermal compensation? Or they are just waiting for the patent to expire before releasing their hairsprings?
By the way, contrarily to what is said in the article, I don’t believe Ulysse Nardin was part of the consortium, they led their research on silicon independantly, with Mimotec and created the joit-venture Sigatec.
Hi Polerouter, UN brought out the first silicon components in the industry in its Freak of 2001 and the first diamond-coated components in 2002 in the Freak DiamonSil. Sigatec was founded in 2006 (jointly with UN). I am pretty sure they were part of the consortium at the beginning as any silicon at that time would have come from CSEM (who the consortium worked with).
I stand corrected indeed about Sigatec which appeared far later, and UN may have worked with CSEM independently from the consortium, but they were not part of the consortium about thermocompensated hairsprings. There was indeed a dispute between the consortium and UN/Sigatec about those hairsprings, which reached an undisclosed agreement in 2013. Here are french- and english-speaking sources. http://www.agefi.com/quotidien-agefi/une/detail/edition/2013-11-29/article/le-litige-opposant-swatch-group-rolex-patek-a-sigatec-ulysse-nardin-est-enfin-regle.html
https://monochrome-watches.com/technical-perspective-hairspring-technology-manufacturing-process-developments/
This is quite interesting stuff. I’ve tried to look for more details in my typical half-assed way and what I gleaned before I got distracted is that Swatch/Rolex/Patek were the ones to throw big money at the research with CSEM that UN had sown the seeds of, in order to enable a progression and perfection of the tech for mass manufacture; but since this big money understandably came with some strict demands, and because UN wasn’t also a big financial contributor (in fact, they seemed to be a recipient of the financial aid in a certain respect), they were not part of the ‘gang’, and eventually lost the right to sell the silicon parts they made to third parties, only being able to use them in their own products. I suppose that’s the gist of the undisclosed details of the litigation that took place.
So, the patent expires in 2021. A lot of industry bigwigs who had a diatribe ready at the drop of a silicon hat are going to be changing their tone, heh.
Which is a bit weird on reflection, as F.P. Journe has recently announced he’ll be using silicon hairsprings in a couple of his models (after previously slagging off silicon as an inferior, future-doomed material that he wouldn’t use because he wants his pieces to last), so I must be confabulating. Unless it’s because he’s getting them from America, and there’s a strangehold on Europe and Asia that needs to be circumvented.
I’m waffling.
You are absolutely right on all counts: the Baumatic needed to be altered for the reason you named and F.P. Journe did say that but seems to be backpedaling a bit. And, yes, the institution where he is said to be considering sourcing his silicon balance springs is located in the U.S.A. But I don’t know more than that yet, unfortunately. We’ll see how that ends up panning out in the end.
Thanks Elizabeth!
I believe Baume et Mercier is Richemont and they had to alter a new model’s escapement in response to threats of a lawsuit.It is called the Baumatic.
Ah, the Baumatic, that was it!
Thanks, another great technical resumé (which I would be proud to have written).
I was especially interested in the account of Dynamic’s use of the anisotropic properties of silicon, something I was never able to get the Swiss to comment on.
TAG’s work with carbon nanotubes is also fascinating. An individual, Gideon Livingston, discussed his work with carbon composite balance springs at BHI 150 Seminar in 2008. Kari Voutilainen used these springs in one of his chronometers but tremendous financial resources are needed to perfect such developments.
I just wish there was as much research being made in quartz technology. Citizen seem to be the only serious “purists” on this front. +/-1s per year is astounding accuracy from their Cal.0100 and nobody seems to care. This is a damning indictment of the so-called horological community.
Everyone else is either struggling to make good on their HAQ claims (my Bulova 262 WAS within spec until summer arrived) or opting for atomic/GPS resetting. If customers can be convinced to spend £1,000 on a phone they’ll dump in three years, I can see no reason for them not to spend £2-3,000 on a lifetime purchase. This is the huge advantage The Swiss mechanical makers have. No-one dreams of handing down their Citizen eco-drive to their son.
I am a fourth year mechanical student, wanting to research on hairsprings and improvements in the material used.
any suggestions on material combinations to look at that have not been done
That is quite the question, but there is always room for new innovations. We hopefully covered a lot of what has been tried here, different alloys, silicon, and unique materials, but if I were to venture a guess the answer is going to come from high-tech composites or exotic alloys that are not easily created, or a material that can only be created in a way similar to silicon.
The biggest considerations are always going to be flexibility, temperature sensitivity, reactions to magnetism, and cost effectiveness of producing the spring in the appropriate shape. From outside of the watch industry you may need to work with material scientists or researchers that develop new alloys and composites. As always, it will require a lot of testing and math, and trial and error I’m sure.