In Focus On Technology: 3D Printing, What Is It Really?, I introduced a topic that has become a bit of a buzzword in manufacturing: 3D printing. We began to establish that it is not yet necessarily widespread in the world of watchmaking, but that it is slowly creeping into our modern lives and culture as a whole.
We already covered a number of 3D printing processes. The last process I will focus on is called Selective Laser Sintering (SLS), which utilizes a high-powered laser to heat a powdered material and sinter it into a solid structure. This is the process most likely to change the watchmaking industry, as it is able to print with materials actually regularly utilized: metals and ceramics.
Just to clarify, sintering is the process by which heat and/or pressure is applied to a granular material to form a solid mass without melting said material. The atoms of the particles diffuse across their boundaries thanks to the heat and pressure causing the particles to fuse and bind together creating a solid material.
This traditional process is actually already used for sintering ceramic cases and other ceramic parts from brands like Rado and Omega.
SLS, SLM, DMLS. What?
The SLS process starts out very similarly to the Z-Corp process I covered in Part 1 as it has a bed upon which a powdered material (including polymers, metals, ceramics, and composites) is spread in a very thin layer.
A set of mirrors then direct a laser to pass over the powder and focus on the points where the material will be sintered into a solid.
Layer by layer, an object is built up until a final shape is created in the bin of powdered material. The layer thickness for this process depends largely upon material and machine quality, but will range from .15 mm down to .01 mm, which allows for a very accurate build.
Included under the umbrella of SLS are other processes that are technically different but in general terms function similarly. Direct Metal Laser Sintering (DMLS) focuses on sintering metals and can sinter, or in some cases fully melt, the powdered metal to create a homogeneous material. It also works with harder metals including Inconel and Titanium.
Selective Laser Melting (SLM) is very similar to SLS except that the material is completely melted, creating a solid and void-free material. It does this in a controlled atmosphere of inert gas, usually argon or nitrogen, to control the crystallization properties of the metals.
Both SLM and DMLS utilize a more powerful Ytterbium fiber laser, thus differing from SLS, which usually uses a CO2 laser.
Selective Heat Sintering (SHS) and Electron Beam Melting (EBM) are two processes that are less frequently used and not technically similar to these processes except in loose terms of melting and sintering particles.
So how are they used?
Now that you are familiar with the machines and processes, where does that bring us? It brings us to how they are used.
A 3D printer, no matter how advanced and computer controlled, is a tool. And as a tool, it is designed to perform a specific task.
Some machines like the Polyjet can perform multiple tasks very well, but it still cannot mimic a CNC lathe or a table saw. What they can do, however, is make complicated parts in a reasonable amount of time for assessment and testing, with generally less human involvement than many processes.
A majority of objects created by 3D printers are prototypes, i.e., test versions of products, components, designs, or concepts that will later be made in other ways. Trying to make something as complex as an organically shaped door handle with a rubber pad inserted into the surface would be very time-consuming using traditional machining, molding, and casting processes.
With 3D printing it can be done quickly and in a couple of steps as opposed to as many as a dozen steps using traditional processes. It may even feel similar to the end product when it is finally manufactured.
Technical impossibilities, static costs
Where 3D printing truly shines though is in its ability to produce geometries that are technically impossible to create using any other process. In these cases, 3D printing is the only tool in the toolbox.
Building parts that have shapes or cavities inside of a solid body cannot be done unless you build that object particle by particle, i.e. this can only be done at present by 3D printing.
And while this undeniably makes the 3D printer crucial for pushing the boundaries of design and engineering, it is not without its drawbacks.
Printing is fast, but not that fast. As people see a model printed in hours where before it might have taken days to produce the same thing, the idea begins to form that just printing something will be ever so much faster than any other way of making things. This is just wrong.
It is absolutely fantastic at producing one, two, or twenty of something very quickly with a very low tooling cost.
This is even truer if it is a unique and never-before-seen component.
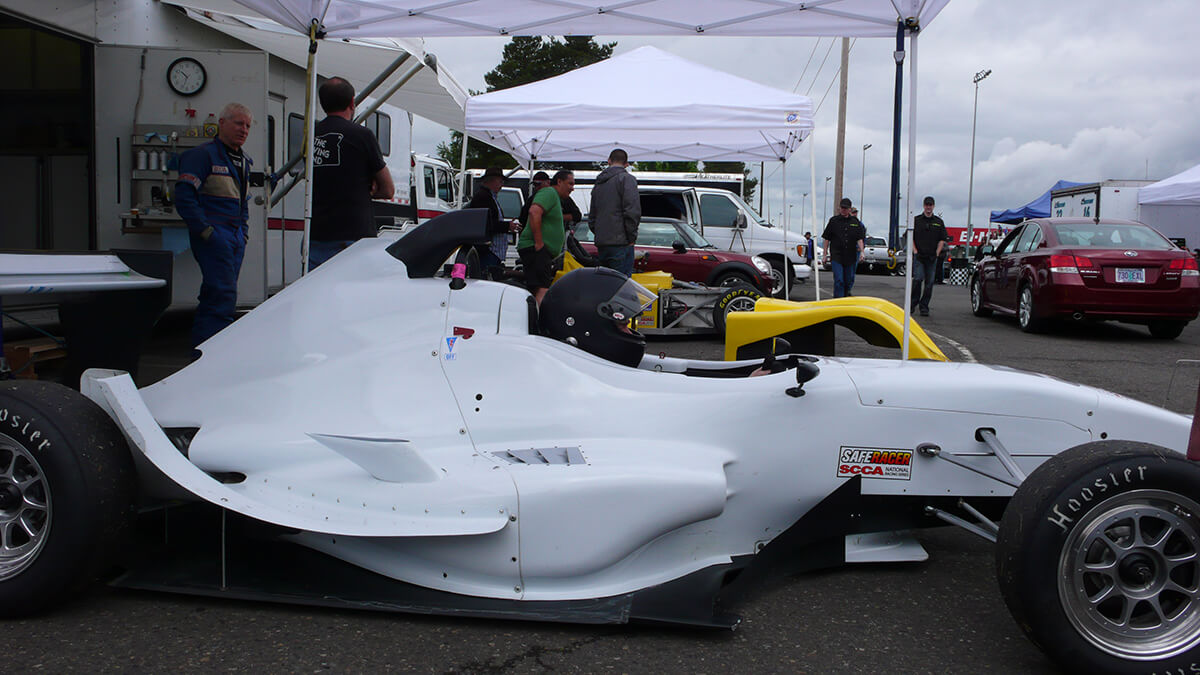
Many of the parts for this race car were manufactured using SLS 3D printing (photo courtesy NW Rapid)
Tooling cost, by the way, is the total cost of all machinery, equipment, and setup time associated with developing a part for manufacturing. This is not to be confused with CAD development, which is normally undertaken by a designer or engineer before being sent to a print specialist or service bureau. Sometimes companies approach the service bureau looking for CAD development, or complete CAD creation from an idea or a sketch, and this will dramatically add to cost, but for different reasons.
But if you need to order a thousand, or even a million, parts (which is extremely common in almost every industry), the 3D printer begins to lose its advantage.
With 3D printing, the cost per part is pretty much identical whether you want to print two, twenty, or 20,000. This is a major benefit to companies looking to make small quantities of a part because using traditional methods tend to make the price per part very high.
But the economies of scale don’t factor in much to 3D printing because you can’t just print it faster or make five thousand per hour with a larger machine.
You can with other forms of manufacturing, and as such, the cost per part comes down dramatically and the volume per hour increases. Not so with a 3D printer.
Also to take into consideration are the actual properties and finish of the parts produced by 3D printers. Depending on type of machine and material, the mechanical properties of the parts vary widely and for good reason.
The faster and cheaper the machine and material, the less like a finished component the part is. With Z-Corp printing, the part actually resembles something made out of compressed sand particles and is about as brittle even after curing and post-processing with an infiltrant (like a hardener).
With FDM, the individual layers are more than visible and create a stair-stepped appearance, which means the surface is not smooth and usually would require filling and sanding if a nice surface finish was desired.
But as you go into SLA, SLS, and Polyjet technologies, the parts can become very nicely finished with smooth surfaces and strong structures. There are exceptions as well, mostly due to geometries and material choices, but overall these are your higher-end processes. Finishing processes are still required, but the extent is much more reasonable.
Regardless of that, however, comes another downfall of 3D printing: asymmetrical dimensional properties. This translates into where things are accurate and where they are not.
Geometric squish
When you have three different directions that a part, support table, and printing head move in space, one of those directions is liable to move differently than the other two. This is true with 3D printers and becomes apparent in the Z-axis.
3D programming-nerd side-note: Each direction is given an axis name, with side-to-side and front-to-back labeled X and Y, while the vertical axis is the Z-axis.
For reasons including inaccurate axis movement, settling of the material under the force of gravity, and artifacts from layer slicing, things printed in the Z-axis have a tendency to squish slightly. This creates flatter shapes, out-of-round circles, and poorly aligned features.
This is most noticeable with circles as they become, in some extreme cases, egg- or oval-shaped. The problem is usually reduced or eliminated in the X and Y-axes as the movements of the print apparatus can translate the points much more accurately in a stable position. The main place where this holds less true, however, is in laser systems as the laser is bounced off a set of mirrors and obtuse angles can add in relatively small errors in the X and Y-axes as well.
System accuracy
The final main issue of 3D printing is the overall accuracy of the systems. Depending on materials, print head design, alignment motors, and layer thickness, the minimum accuracy of 3D printers varies as much as the choices for machines.
The FDM process uses a filament of extruded plastic, which means any detail smaller than that filament is impossible, and any detail less than four times the diameter of the filament will become more or less a useless blob on your model.
Grain size with Z-corp, SLS, and other granular- or powder-based systems limits minimum feature size, along with surface finish capabilities though they can still be rather small for some machines. SLA and Polyjet use photopolymers which tend to offer some of the smaller minimum feature sizes for increased accuracy.
But after all that pessimistic talk I will follow it up with the fact that over the past thirty years the technology has grown by leaps and bounds. Organizations like SpaceX and NASA are using high-end machines to make very low-run parts that are actually used on things sent into space. They aren’t manufacturing two million units a year, but for the three or four that they need, 3D printing is now a viable manufacturing method.
Nice (read: expensive) machines can create parts with very nice surface finishes, parts can be made very strong, or very flexible, or somewhere in between. People are experimenting with printing foods, living cells, and even printing houses on a grand scale. Things are changing for sure.
And for watches?
In regards to the world of watches, where does that leave us? Well, it leaves us in a very grey area. Watch companies have been using 3D printing for years, maybe even a couple decades, for prototyping cases and dials for quick mockups and line expansion concepts.
Surface finish and material properties aren’t really crucial for that, only size, shape, and maybe color matter. I have read about companies or watchmakers (like Nicholas Manousos) beginning to use 3D printing to help prototype mechanisms or simply ideate improvements to existing movements and escapements.
And as the technology advances and more companies start investing, some 3D-printed components may just find their way into watches for sale, just not likely in the cheaper models and probably no critical moving parts. This is because the tolerances required for movement components are still hard to achieve even with the best 3D printers.
The current production strategies for all of these companies, likewise with companies around the globe, rely on tried-and-true manufacturing processes, which can hold tight tolerances and make numerous components very quickly.
It is not easier for Rolex or Patek Philippe, for example, to produce dials, balance wheels, or other components with 3D printing. It isn’t even cost-effective yet. They have the infrastructure to produce their parts, to spec, with traditional machining and manufacturing processes.
Now, very small independents producing only ten to one hundred watches a year and wanting to try some very complicated things might find it extremely cost effective to have a DMLS part made to fit into their latest prototype movements.
Chances are they will need to do a decent amount of post-processing with hands-on finishing, making sure the part is accurate and true, but it may still speed up the prototyping process while dramatically reducing development costs. This is still where the technology shines, in the ideation process, allowing for complicated things to be made very quickly in extremely low volumes for testing an idea.
The entire world of 3D printing has a lot to offer, and in many industries it is making a very clear change to how things work. But most importantly, it is another amazing tool for people to use to create new and exciting objects that could never be created before.
It could surely help in creating watches, but when dealing with the exacting tolerances required and specific materials manufacturers tend to use, it still has a ways to go before being a fundamental tool used in the creation of fine timepieces. Though that is changing every day and I am very excited for whatever might come down the line.
I hope you enjoyed my rather wordy look into the topic of 3D printing and how it might relate to our shared interests in amazing timepieces. It is a fascinating tool that can help create amazing things, though it must be remembered that it is still a tool and may only be as good as the operator or designer.
Seeing the things that are coming out of the industry, I know there is more than one smooth operator just waiting to be let loose with a sketchbook and a brand new 3D printer.
Click here if you missed Part 1 of Focus On Technology: 3D Printing, What Is It Really?
* This article was first published June 8, 2014 at Focus On Technology: 3D Printing, What Is It Really? Part Deux.
You may also enjoy:
Focus On Technology: 3D Printing, What Is It Really?
Understanding Ceramics: Now Used For Watch Cases, Bezels, And Much More
Timekeeping In A 5G World: Coordinated Universal Time Blown Away By Ultra-Precision Time On Tap
Leave a Reply
Want to join the discussion?Feel free to contribute!
Great article on applications of 3D printing. Can 3D printing cater to art and jewelry market ? and what about the accuracy ?
Downloading the drivers necessary, Installing the drivers, Loading the cartilage and drum, loading print papers, and the actual printout procedure. The first 3 steps are explained earlier. Now let’s see the further steps.